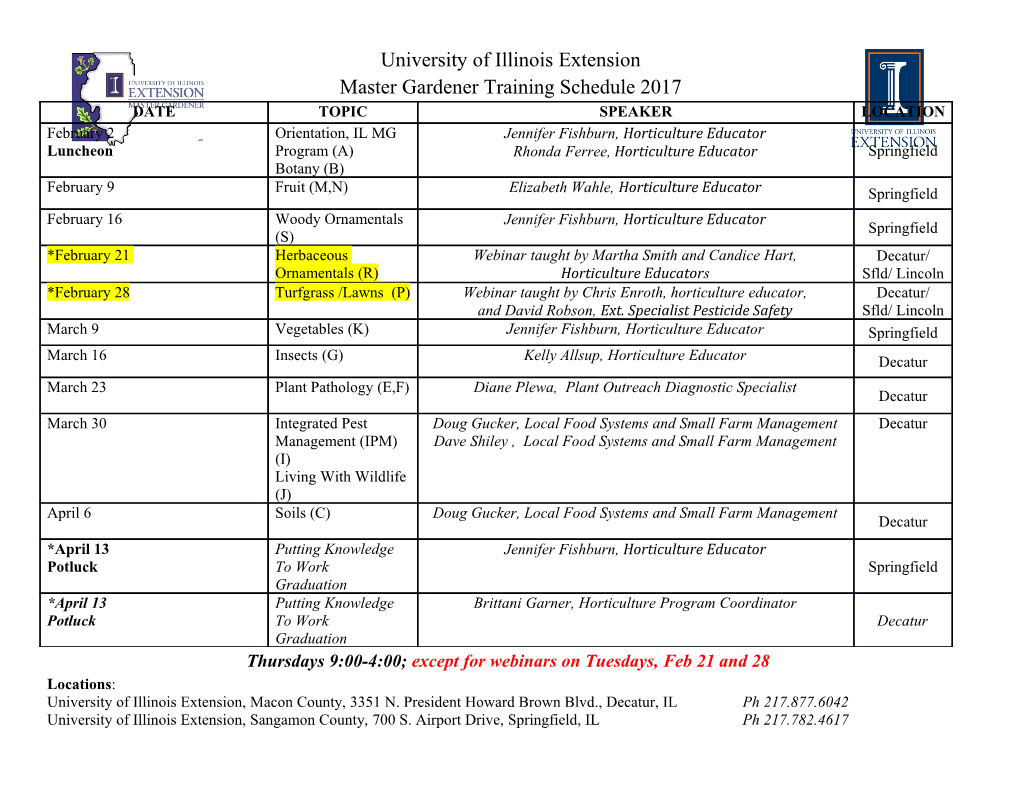
<p> Faculty of chemical and food technology STU in Bratislava</p><p>Institute of chemical and environmental engineering</p><p>Steam system</p><p>Milan Škultéty Study Group 36 Acad. year 2016/2017</p><p>Table of Contents</p><p>Sources...... 3 Abstracts from sources...... 4 1. A Heuristic Approach for Petrochemical Plant Layout Considering Steam Pipeline Length...... 4 2. Determination of annual heat losses from heat and steam pipeline networks and economic analysis of their thermomodernisation...... 4 3. Data-driven based model for flow prediction of steam system in steel industry...... 4 4. Optimal retrofit design and operation of the steam-supply system of a chemical complex...... 4 5. Online hydraulic calculation and operation optimization of industrial steam heating networks considering heat dissipation in pipes...... 4 Abstract...... 4 Project – Steam system...... 4 Introduction...... 4 Problem formulation...... 4 Optimization of the steam pipeline network...... 4 Conclusion...... 4 Supplementary literature...... 4 Sources</p><p>[1] Wu Y., Wang Y., Feng X.: A Heuristic Approach for Petrochemical Plant Layout Considering Steam Pipeline Length, 2016, doi: 10.1016/j.cjche.2016.04.043</p><p>[2] Kruczek T.: Determination of annual heat losses from heat and steam pipeline networks and economic analysis of their thermomodernisation, Energy 62 (2013), pg.120-131</p><p>[3] Liu Y., Liu Q., Wang W., Zhao J., Leung H.: Data-driven based model for flow prediction of steam system in steel industry, Information Sciences 193 (2012), pg. 104-114</p><p>[4] Halasz L., Nagy A.B., Ivicz T., Friedler F., Fan L.T.: Optimal retrofit design and operation of the steam-supply system of a chemical complex, Applied Thermal Engineering 22 (2002), pg. 939-947</p><p>[5] Zhong W. et al.: Online hydraulic calculation and operation optimization of industrial steam heating networks considering heat dissipation in pipes, Energy 87 (2015), pg. 566-577</p><p>[6] The Causes and Effects of Water Hammer – Armstrong International, available online: 16.01.2016 https://www.youtube.com/watch?v=5WTVQtvavmY Abstracts from sources</p><p>1. A Heuristic Approach for Petrochemical Plant Layout Considering Steam Pipeline Length</p><p>Plant layout design affects both investment and performance of a factory. To maximize the economic benefits of a petrochemical factory, a large number of factors must be considered simultaneously, such as material flow, heat flow and safety. However, conventional principles for plant layout design and optimization do not involve the heat flow, resulting in higher construction investment. To solve this problem, a new heuristic approach is proposed in this paper based on the current layout design principles. Both material flow (pipelines for process streams) and heat flow (pipelines for steam) are considered. Three optimization methods with different objective functions are used to optimize the layout. The application of proposed approach is illustrated with a case study. The optimal scheme and pipeline networks can be obtained, and the pipeline length is reduced significantly. </p><p>Keywords petrochemical plant layout; heuristic; steam system; pipeline length; optimization</p><p>2. Determination of annual heat losses from heat and steam pipeline networks and economic analysis of their thermomodernisation</p><p>The paper presents a method of evaluation and selective thermomodernisation of overhead thermal pipeline networks. The expression “thermomodernisation” is used for determination of all those activities that deal with improvement of heat insulation features of the pipelines under consideration. The method is particularly useful for extensive and complex heat or steam pipelines. A novel method for the determination of annual heat losses from overhead pipelines into the environment has been developed in the work. The heat losses from the pipelines are generated during the whole year. The proposed method is based on the concept of one-off examination of the pipeline under consideration by means of a thermovision camera, performed in existing weather conditions. An example of an analysis has been carried out and results are presented for an existing industrial pipeline network. In this analysis the whole pipeline network was divided into segments characterised by identical technical features. To determine the annual heat loss, the operation of the considered pipeline during the whole year in different meteorological conditions was simulated numerically. Next, economic factors were calculated for each pipeline segment. Generally, the selection of line segments recommended for thermomodernisation was done on the basis of heat losses and SPBT (simple pay-back time) calculations. </p><p>Keywords: Pipelines, Thermal insulation, Heat losses, Infrared camera, Thermomodernisation</p><p>3. Data-driven based model for flow prediction of steam system in steel industry</p><p>The steam system is one of the main energy systems in steel industry, and its operational scheduling plays a crucial role for energy utility and resources saving. For a reasonable resources operation, the accurate prediction of steam flow is required. Considering the large amount of production data in energy system, a data-driven based model is proposed to perform a time series prediction for steam flow, in which a Bayesian echo state network (ESN) is established. This method combines Bayesian theory with ESN to obtain optimal output weight via maximizing the posterior probability density of the weights to avoid over-fitting in the training process of sample data. To pursue optimized hyper-parameters in the proposed Bayesian ESN, the evidence framework based on sample data is further adopted in this work. Experimental results using the real production data from Shanghai Baosteel show the validity and practicality of the proposed data-driven based model in providing scientific decision guidance for the steam system.</p><p>Keywords: Steam system, Data-driven, Time series prediction, Bayesian ESN</p><p>4. Optimal retrofit design and operation of the steam-supply system of a chemical complex</p><p>It is inordinately difficult to optimise the steam-supply system of a chemical complex under the condition that the production capacities of a multitude of products vary temporarily. Any of the available general purpose methods for optimal design and operation hardly suffices for this purpose; therefore, a specific purpose method has been developed in the current work. The efficacy of the resultant method is illustrated by optimising the steam-supply system of an existing chemical complex. The complex consists of one power-plant; one boiler station; four production plants operated in batch; one production plant operated continuously; and one pipeline network.</p><p>Keywords: Heat integration; Steam-supply system; Process synthesis</p><p>5. Online hydraulic calculation and operation optimization of industrial steam heating networks considering heat dissipation in pipes</p><p>Constructing industrial parks with DH (district heating) systems has become a main way to develop modern industry, which requires strict security and reliability of heating networks. Industrial steam heating networks are usually ring-shaped with multiple heating sources, and the working conditions would be changeable due to the high frequency and a wide range of load variation of heating consumers. Under a specific working condition, low steam velocity for a long time (namely “steam stagnation”) in certain pipes will result in CIWH (condensation- induced water hammer) which will threaten the security of the whole DH system. In this paper, a hydraulic calculation model is built to study the steam flow regime considering heat dissipation and condensation in pipes, an operation optimization method is proposed to help eliminate steam stagnation through optimizing the heat load distribution of each heating source, a general software system entitled “HEATNET” is presented to realize online hydraulic calculation and operation optimization for arbitrary structured heating networks. The practical application of HEATNET in Shanghai chemical industry zone shows that heat dissipation and condensation in pipes would influence the overall hydraulic calculation of steam heating networks and it can prevent CIWH and improve the security and reliability of steam heating networks.</p><p>Keywords: Steam heating network, CIWH (condensation-induced water hammer), Flow regime, Heat dissipation, Online hydraulic calculation, Operation optimization Abstract</p><p>This project’s key role is to present various methods of steam flow prediction. The steam flow in pipelines varies depending on the heat demand of the industrial process. This variation makes the whole optimization of the steam pipeline network more complicated. In the present, hardly any of the available general purpose methods for optimal design and operation of steam networks suffices for this purpose. The goal of the optimization of the steam pipeline network is to achieve further economy benefits. To maximize the economy benefits or minimize heat dissipation of the steam pipeline network, a large number of factors must be considered simultaneously, such as operational features of the pipelines – pipeline diameter, insulation thickness, pipeline length and positioning, etc. </p><p>Keywords: Pipelines, Steam system, Operation optimization Project – Steam system</p><p>Introduction</p><p>Steam is one of the important resources in industry, which provides energy in the production process. For instance, steam can be generated by burning gas, and the produced steam may be further utilized by internal electricity power plant. Therefore, steam and hot water pipeline networks play a key role in energy transfer in industrial plants as well as in district heating systems. Generally, steam is supplied by two sources, the boiler station and the power plant. The distance between any of these sources and the destination of the steam can exceed a mile; thus, the capital and operating costs of the steam supply system strongly depends on the geometrical and operating parameters (diameter of the pipe, thickness of insulation, pressure drop, etc.). In the chemical industry the involvement of batch operation and the varying levels of production of multiple products can give rise to a significant variation in the energy or heat-power demand of a chemical complex. Such a variation, results in immense difficulties in optimising the steam- supply system of the complex; the system must be capable of supplying the maximum demand of the given chemical complex. [4]. Therefore, the biggest challenge in steam resource utility is the scientific steam flow prediction. Once the variation tendency of steam flow can be accurately predicted, an effective scheduling can then be implemented. For example, when the amount of steam generated is more than the consumed amount at time, boilers or power generators can be used to reduce the steam supply. In such way, the steam diffusion can be largely avoided. On the other hand, when the steam flow is insufficient, boilers and power generators can produce steam in time so as to complement the demand for production. Thereby, online prediction for steam generation and consumption flow is an effective way for energy utility and beneficial to economy profit in the industry. [3] Problem formulation</p><p>The above mentioned papers are focused generally on the application of various methods which help in the prediction of the steam flow. For industrial heating systems, operators can hardly get the real time steam flow regime in each pipe for the lack of related measuring devices to record the flow rate, temperature and pressure of steam. Nowadays, with the development of computational technology, it is possible to calculate the steam flow theoretically and thus realize operation optimization for heating networks. Fluid flowing in pipelines must satisfy the Kirchhoff’s law – the flow rate conservation law of nodes and energy conservation law of circuits, where nodes are representing the points where mass flows in and out. The laws are based on the law of mass and energy conservation. The flow rate conservation law of nodes can be described as: the algebraic sum of flow rate going into and out of any node is zero and the energy conservation law of circuits is: the algebraic sum of all pressure drops around a closed path, or mesh, in the network must be also zero. There are several factors, which noticeably effect steam flow in the pipeline network. Heat dissipation from the steam, typically linked with water condensation at the inner surface of the pipeline, is one to be considered. The heat transfer process from steam to the ambient consists of:</p><p>1. Heat convection from flowing steam to the inner wall of the pipe;</p><p>2. Heat conduction in the pipe and insulation layer;</p><p>3. Heat convection and radiation from the insulation layer to the ambient [5] Figure 1 Cross section of a steam pipe. The condensation water in pipes, induced by heat dissipation, would flow along with the steam and drain out through a steam trap. When optimizing steam pipeline networks, more attention should be paid to the drainage of all steam traps, since it can reach 3-10% of the total heat supply. [5] Other factors are the radiative temperature of the environment, consisting of thermal radiation of the ground surface and sky radiation, also the wind speed can have slight effect on the steam flow in pipelines and condensation drainage as mentioned in papers by Kruczek and Zhong et al. </p><p>Optimization of the steam pipeline network</p><p>The paper [1] focuses on the effect of a petrochemical plant layout on both investment and performance of a factory. Factors, leading to maximization of economic benefits of a petrochemical plant layout, are related to the material flow, heat flow and moreover safety. Conventional principles for plant layout design and optimization do not involve the heat flow. The plant layout of petrochemical factory is a branch of facility layout problem, which main goal is to determine the most effective department arrangement in a facility and to minimize material handling costs. </p><p>To solve this problem, three optimization methods have been proposed: [1] </p><p> minimization of the length of material flow pipeline</p><p> minimization of the length of steam pipeline network, considering 3 levels of steam (high, medium and low pressure steam)</p><p> optimization of the length of material and steam flows simultaneously</p><p>The goal of the paper is to show that optimizing only one type of pipeline leads the incomprehensive results. Optimization of both material and steam pipelines to reduce the overall pipeline cost is required – where high pressure steam pipelines are the shortest.</p><p>The rest of the studies are focused on optimizing an already existing pipeline, but each of them have a unique approach to the problem mentioned. The main role in the paper [2] is the thermomodernisation – the determination of all activities leading to the improvement of heat insulation features of the pipeline. Four different thermos-economic techniques are presented. They are based on the optimization of the pipe diameter and insulation thickness based on maximization of exergy energy, also maximizing economic benefits. The study was executed in sequences – selection of pipeline segments to be measured by IR camera, thermovision measurements, calculation of heat losses and calculation of economic indicators of the thermomodernisation. In general, the calculation results correspond relatively well to the annual measured heat losses determined by means of the balance method. However, the observed heat losses for the considered pipeline network pieces were higher by 30-40% than the calculated losses. The discrepancy between the calculated and observed results can be accounted with:</p><p> penetration of thermal insulation by snow- or rain-water in the case of a leaky outer pipeline shell;</p><p> intensive cooling of pipelines during rain periods and the inability to quantify the effects;</p><p>In the papers Liu et al. and Halasz et al. the experiments were held at a steel industry company and at a chemical complex. They led the optimization applying various methods. In the paper Liu et al. is proposed a data-driven based model to perform time series prediction of the steam flow. This data-driven based model uses neural network approach – the echo state network ESN. The steel enterprise has accumulated a large set of real-time data, which reflect the dynamic characteristics of the system, during the production process. Two types of ESN were mentioned. Due to the complexity and steam flow fluctuations of the production process the steam data collected are usually noisy. If the generic ESN is used directly for modeling, the prediction performance can be degraded, and over-fitting might occur. Therefore, a Bayesian ESN is proposed. After the comparison of the predicted results calculated using these state networks, it is possible to confirm that the Bayesian ESN can provide a higher robustness, when compared with the generic ESN. In the paper by [4] the optimization is led by applying mathematical models developed based on P-graph representation, the decision-mapping, combinatorial algorithms, and the accelerated branch-and-bound method. </p><p>In the last article [5] a method to calculate the steam flow regime in pipelines in Shanghai chemical industry park is presented. Also, the drainage of steam traps is taken into consideration, and an operation optimization method is proposed to help eliminate steam stagnation through optimizing the heat load distribution of each heating source. Based on the research, a general software system “HEATNET”. The significant variation in the steam demand in industrial processes may lead to complicated steam flow regime, hydraulic maladjustment or even steam stagnation in certain pipes. HEATNET can read operating data of a heating network from real- time database and display key information, such as the pressure of heating consumers and steam velocities in pipes. Moreover, it can locate steam stagnation pipes quickly and accurately with the established model and the real-time calculation results, providing an effective method to eliminate side effects, such as CIWH (Condensation-induced water hammer), which can result in instability and hydraulic shock, causing even serious damage to equipment and thus leading to a safety breach. CIWH happens in two-phase systems, when steam enters the condensate. Due to temperature difference the steam collapses, surrounding condensate is accelerated into the vaccum (steam has 100x volume compared to liquid state), filling the void, the water impacts at the center sending shockwaves in all directions. The phenomenon is better described at source video [6].</p><p>Conclusion</p><p>In the industry the steam flow in pipelines varies depending on the heat demand of the industrial process. This variation makes the whole optimization of the steam pipeline network more complicated. The key role of this project is to present various methods of scientific steam flow prediction as an effective way for energy management and including benefits to economy profit in the industry. Every method and software has its pros and cons and neither of them can absolutely calculate the steam flow in the pipelines. Many factors affect the transport of steam, as heat medium, such as weather conditions, which create immense difficulties in the simulation. Overall, the software HEATNET, described in the latest paper from 2015 [5], can predict the behavior of the heating system relatively well, and furthermore it can eliminate safety breaches by locating pipeline sections with complicated steam flow regime or occurring steam stagnation. Supplementary literature</p><p>1. Białecki R.A., Kruczek T.: Frictional, diathermal flow of steam in a pipeline, Chemical Engineering Science 51 (1996), pg. 4369-4378</p><p>2. Wu L., Liu Y., Liang X., Kang L.: Multi-objective optimization for design of a steam system with drivers option in process industries, Journal of Cleaner Production 136 part B (2016), pg. 89-98</p><p>3. Wang H., Haiying Wang H., Zhu T., Deng W.: A novel model for steam transportation considering drainage loss in pipeline networks, Applied Energy 188 (2017), pg. 178-189</p><p>4. Niu X., Gong J., , Jiang Y., Bao J.: Creep damage prediction of the steam pipelines with high temperature and high pressure, International Journal of Pressure Vessels and Piping 86 (2009), pg. 593-598</p><p>5. Urban C., Schlüter M.: Investigations on the stochastic nature of condensation induced water hammer, International Journal of Multiphase Flow 67 (2014), pg. 1-98</p><p>6. Vanaeia H.R., Eslamia A., Egbewandeb A.: A review on pipeline corrosion, in-line inspection (ILI), and corrosion growth rate models, International Journal of Pressure Vessels and Piping 149 (2017), pg. 43-54</p>
Details
-
File Typepdf
-
Upload Time-
-
Content LanguagesEnglish
-
Upload UserAnonymous/Not logged-in
-
File Pages13 Page
-
File Size-