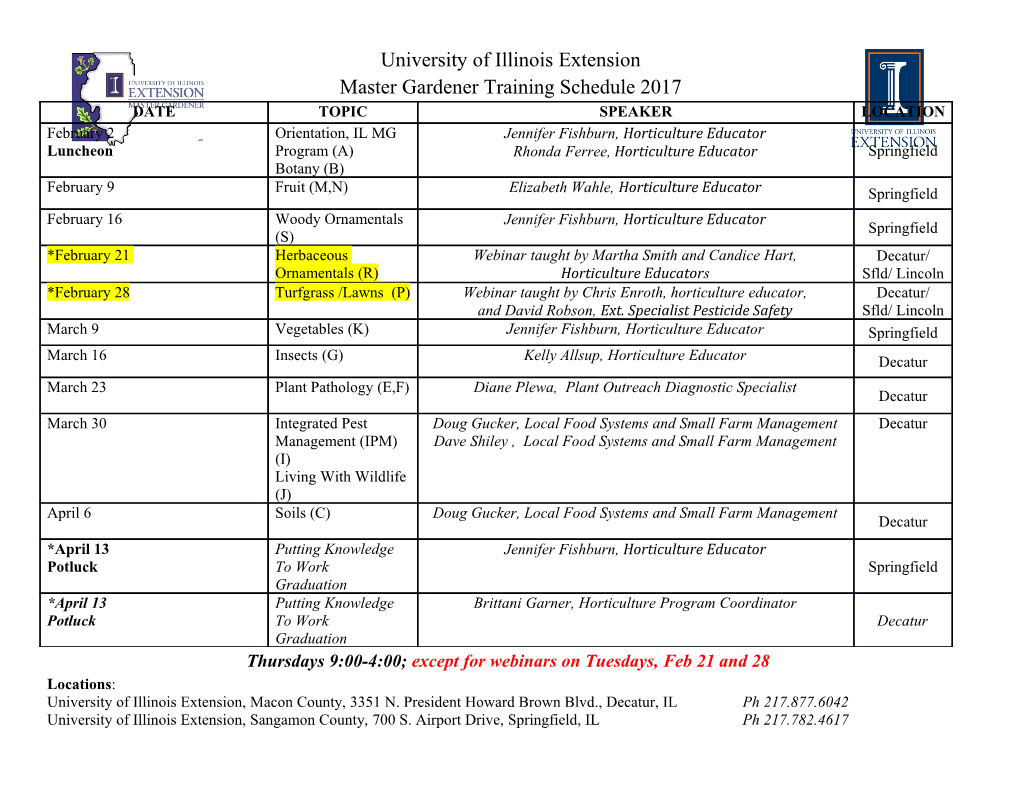
Active electromagnetic suspension system for improved vehicle dynamics Citation for published version (APA): Gysen, B. L. J., Paulides, J. J. H., Janssen, J. L. G., & Lomonova, E. A. (2008). Active electromagnetic suspension system for improved vehicle dynamics. In IEEE Vehicle Power and Propulsion Conference, 2008 : VPPC '08 ; 3 - 5 Sept. 2008, Harbin, China (pp. 1-6). Institute of Electrical and Electronics Engineers. https://doi.org/10.1109/VPPC.2008.4677555 DOI: 10.1109/VPPC.2008.4677555 Document status and date: Published: 01/01/2008 Document Version: Publisher’s PDF, also known as Version of Record (includes final page, issue and volume numbers) Please check the document version of this publication: • A submitted manuscript is the version of the article upon submission and before peer-review. There can be important differences between the submitted version and the official published version of record. People interested in the research are advised to contact the author for the final version of the publication, or visit the DOI to the publisher's website. • The final author version and the galley proof are versions of the publication after peer review. • The final published version features the final layout of the paper including the volume, issue and page numbers. Link to publication General rights Copyright and moral rights for the publications made accessible in the public portal are retained by the authors and/or other copyright owners and it is a condition of accessing publications that users recognise and abide by the legal requirements associated with these rights. • Users may download and print one copy of any publication from the public portal for the purpose of private study or research. • You may not further distribute the material or use it for any profit-making activity or commercial gain • You may freely distribute the URL identifying the publication in the public portal. If the publication is distributed under the terms of Article 25fa of the Dutch Copyright Act, indicated by the “Taverne” license above, please follow below link for the End User Agreement: www.tue.nl/taverne Take down policy If you believe that this document breaches copyright please contact us at: [email protected] providing details and we will investigate your claim. Download date: 26. Sep. 2021 IEEE Vehicle Power and Propulsion Conference (VPPC), September 3-5, 2008, Harbin, China Active Electromagnetic Suspension System for Improved Vehicle Dynamics Bart L.J. Gysen, Johannes J.H. Paulides, Jeroen L.G. Janssen, and Elena A. Lomonova Eindhoven University of Technology, The Netherlands. Email: [email protected] Abstract—This paper offers motivations for an active suspension system which provides for both additional stability and maneuverability by performing active roll and pitch control during cornering and braking as well as eliminating road irregularities, hence increasing both vehicle and passenger safety and drive comfort. Various technologies are compared to the proposed electromagnetic suspension system which uses a tubular permanent magnet (PM) actuator together with a passive spring. Based upon on-road measurements and results from the literature, several specifications for the design of an electromagnetic suspension system are derived. The measured on-road movement of the passive suspension system is reproduced by electromagnetic actuation on a quarter car setup proving the dynamic capabilities of an electromagnetic suspension system. Figure 1. (a) Conventional passive suspension system, Keywords—Active Suspension; Permanent Magnet; Tubular (b) electromagnetic suspension system Actuator greater suspension articulation when driving under low- I. INTRODUCTION yaw circumstances (driving relatively straight) to absorb Advanced electro-mechanical and electronic systems road irregularities and have a much more rigid response are increasingly installed to influence the dynamic when the car is driven through turns which improves performance of the vehicle, for example antilock braking vehicle dynamics. systems (ABS), electronic break force distribution (EBD), In order to facilitate the ideal suspension with regard electronic stability program (ESP), etc. These systems are to comfort, handling and safety, various commercial installed to improve vehicle handling and passenger technologies are used to improve or replace the safety, since this becomes an ever increasing demand for conventional passive suspension system shown in the automotive industry especially when cars tend to Fig. 1(a). This paper discusses an active electromagnetic become smaller (SMART), incorporate a higher center of suspension system incorporating a brushless tubular gravity (SUV) and reduced footprint. For instance, the permanent magnet actuator in parallel with a mechanical transportation research board [1], reported that 51 % of the spring [5], as illustrated in Fig. 1(b). This topology has serious car accidents are caused by rollover. been chosen since the tubular structure exhibits a high Another trend in the automotive industry is the ‘more efficiency and excellent servo characteristics. electric car’, for example the Toyota Prius. These hybrid Furthermore, the mechanical spring supports the sprung vehicles combine the efficiency of an electric motor mass; hence no continuous power is needed. The main together with an internal combustion engine. Due to the advantage of this system is that it simultaneously allows global increase in oil prices and the importance of for both the elimination of the road disturbances and environmental sustainability, the ‘full electric car’ is also active roll and pitch control. gaining attention. Recently, a Dutch energy company, In section II, the ideal suspension regarding passenger Essent [2], launched a commercial electric car together comfort is discussed. Section III gives an overview of with Electric Car Europe. These cars have a totally different technologies for active suspension which are different weight distribution since the combustion engine compared to the proposed electromagnetic suspension is replaced by an electric motor together with a battery system. Based upon the quarter car model, the influence of pack of around 400 kg. As such, the optimal electrical changing the sprung and unsprung mass is shown in drivetrain efficiency is reached when completely Section IV. Various on-road and off-road measurements incorporated in the wheel [3, 4]. However, as a result, the are performed on the current passive suspension system unsprung mass of the vehicle increases which is a and specifications regarding force, power and stroke are disadvantage regarding passenger comfort and handling. derived for the active suspension system in Section V. These trends clearly show the need of active suspension to Electromagnetic actuation is performed on a quarter car be incorporated into vehicles. These systems allow for test setup which mimics the on-road measurements and conclusions are drawn in Section VI. 978-1-4244-1849-7/08/$25.00○C 2008 IEEE Authorized licensed use limited to: Eindhoven University of Technology. Downloaded on April 8, 2009 at 08:22 from IEEE Xplore. Restrictions apply. IEEE Vehicle Power and Propulsion Conference (VPPC), September 3-5, 2008, Harbin, China II. THE IDEAL SUSPENSION The ideal automotive suspension would, independently, absorb road shocks rapidly and would return to its normal position slowly while maintaining optimal tire to road contact. However, this is difficult to achieve passively, where a soft spring allows for too much movement and a hard spring causes passenger discomfort due to road irregularities. Passenger comfort (combined with handling and safety) is an ever increasing demand, where everybody expects ever improving comfort and handling from the automotive industry. Albeit that a dearth of Figure 2. Illustration of the active roll control (ARC) system of publications exists regarding passenger comfort, it was BMW using a hydraulic rotary actuator [14] assumed that general comfort is improved when two conditions are minimized: situation of roll during cornering and the condition where the right wheel experiences a different bump then the left • Motion sickness, ~1 Hz [6], and wheel. Therefore, different sensor inputs, e.g. position, • head toss, ~2-8 Hz [7]. speed, acceleration, force and roll angle are preferred where, based upon these measurements, the exact state of A. Motion sickness the vehicle can be estimated in order to control the active Motion sickness, especially when reading, is a suspension system. common by-product of exposure to optical depictions of inertial motion [8]. This phenomenon, called visually III. ACTIVE SUSPENSIONS induced motion sickness (VIMS), has been reported in a A. Hydraulic systems variety of virtual environments, such as fixed-base flight and automobile simulators [9, 10, 11]. Further Gahlinger Due to the high force density, ease of design, maturity [12] discussed that motion sickness occurs most of technology and commercial availability of the various commonly with acceleration in a direction perpendicular parts, hydraulic systems are used in body control systems. to the longitudinal axis of the body, which is why head As an example, BMW recently developed an anti roll movements away from the direction of motion are so control (BMW-ARC) system by placing a hydraulic rotary provocative. He further mentioned that vertical oscillatory actuator in the center of the anti roll bar at the rear of the motion (appropriately called heave) at a frequency
Details
-
File Typepdf
-
Upload Time-
-
Content LanguagesEnglish
-
Upload UserAnonymous/Not logged-in
-
File Pages7 Page
-
File Size-