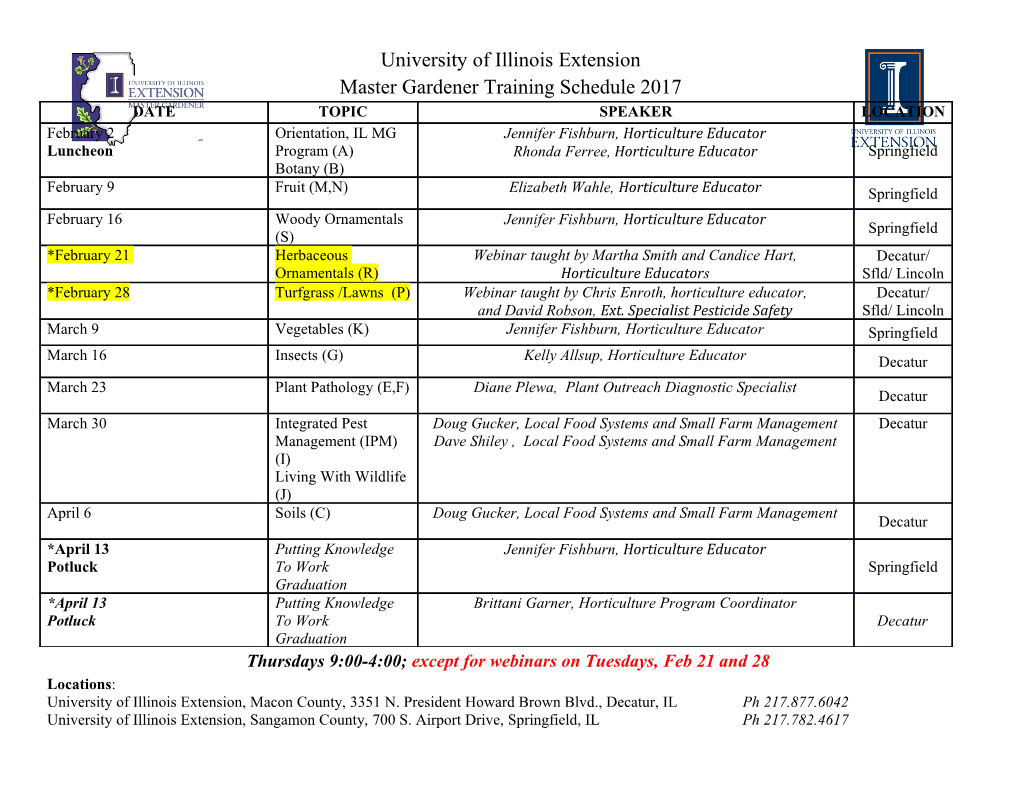
<p> CHECK FIGURES, 14th ed.</p><p>CHAPTER 1</p><p>Problem 1-1. Total variance-February…………………………………………………… $ 200 U</p><p>1-2. 1. Cost of goods sold...... $116,000 2. Cost of goods sold...... $281,000</p><p>1-3. 2. Gross profit on sales...... $ 26,850 Net income...... $ 11,650 3. Total assets...... $442,100</p><p>1-4. 3. Cost of goods manufactured...... $ 91,000 Net income...... $145,850</p><p>1-5. 8. Dr. to Work in Process (Factory Overhead). . $73,900 </p><p>1-6. 1. Cost of goods manufactured...... $348,000 2. Prime cost...... $264,000 3. Conversion cost...... $240,000</p><p>1-7. Cost of goods manufactured…………………………………………. $970,000</p><p>1-8. 1. Cost of Job 1066...... $6,100</p><p>1-9. 2. (a) Gross profit on sales...... $36,250 (b) Gross profit per Job 230...... $17,000 (c) Gross profit per unit, Job 230...... $1.70</p><p>1-10. 2. Cost of Job 90BZ...... $94,000 4. Cost of goods manufactured...... $343,000</p><p>CHAPTER 2</p><p>Problem 2-1. 3. 3,000 average units in inventory.</p><p>2-2. 1. (b) LIFO costing, ending inventory balance. $112,500</p><p>2-3. 2. FIFO cost of ending inventory……………………………. $120,500</p><p>2-4. 3. Moving average, ending inventory balance. . . $4,508</p><p>2-5. 3. (b) Materials on hand...... $43,100</p><p>2-6. 3. Inventory of materials...... $10,000</p><p>41 42 CHECK FIGURES</p><p>2-7. 2. (a) Material inventory balance...... $9,950</p><p>2-8. 3. 1 days</p><p>2-9. (a) Raw and in-process inventory...... $150,000</p><p>2-10 (a) Adjustment of materials account...... $546</p><p>2-11. 1. (b) Inventory value of spoiled goods...... $300</p><p>2-12. 1. Spoiled goods inventory...... $1,125</p><p>RP. 4. Cost of goods manufactured...... $98,290 6. Total assets...... $282895</p><p>Mini-Case 1 Net advantage of JIT…………………………………………………………..$80,000</p><p>CHAPTER 3</p><p>Problem 3-1. 1. Hourly bonus rate...... $.5486</p><p>3-2. 2. Job 2525……………………………………………………………………………………………. $ 480</p><p>3-3. 1. Net earnings for the week...... $2,564.10</p><p>3-4. Total payroll taxes imposed on employer.... $16,627</p><p>3-5. 2. (c) Employer's share of payroll taxes (total)...... $146.61</p><p>3-6. 3. Earnings – Jan. 1 to Jan. 15...... $19,375</p><p>3-7. 1. Net earnings for the week...... $6,022.22</p><p>3-8. 2. Overtime premium payment...... $3,190,000</p><p>3-9. 3. Labor Cost Summary Total Payroll (credit). . $14,928</p><p>3-10. 1. Total payroll taxes...... $49,010</p><p>3-11. Factory Overhead (vacation pay)...... $8,000</p><p>Mini-Case 1 Bonus liability…………………………………………………………………….. $4,563</p><p>CHAPTER 4</p><p>Problem 4-1. (f) C</p><p>4-2. 1. Variable cost (per unit)...... $1.00</p><p>4-3. 2. Fixed costs...... $2,100 CHECK FIGURES 43</p><p>4-4. Total expense at 4,000 units…………………………………….. $160,000</p><p>4-5. 1. Bldg. Maint.distribution, per square foot. . $0.256</p><p>4-6. 2. Completed cost of Job 18AX...... $1,500</p><p>4-7. 1. Total cost of Job G35...... $2,926</p><p>4-8. 2. Cost of Job 2008...... $65,250</p><p>4-9. (m) Debit Factory Overhead...... $2,600</p><p>4-10. 1. (c) Machine hour rate...... $3.00</p><p>4-11. 1. (c) Department rates: Bronzing...... $5.00 Casting...... $2.00 Finishing...... $8.00</p><p>4-12. Assembly (overapplied)...... $(6,000)</p><p>4-13. 1. Total Cost, Job 2527...... $36,400</p><p>4-14. 2. Cost of Goods Sold...... $6,800</p><p>RP. 6. (b) Cost of goods manufactured ...... $78,700</p><p>Mini-Case 3. Deluxe, per unit cost……………………………………………………..$347.50 44 CHECK FIGURES</p><p>CHAPTER 5</p><p>Problem 5-1. Cost of goods finished and transferred to finished goods...... $84,000</p><p>5-2. Cost of goods finished and transferred to finished goods...... $27,300</p><p>5-3. Cost of goods finished and transferred to Shaping Dept...... $54,000 Cost of goods finished and transferred to Finishing Dept...... $55,000 Cost of goods finished and transferred to finished goods...... $66,000</p><p>5-4. Cost of goods manufactured……………………………………………… $66,000</p><p>5-5. 4. Total cost of units finished...... $70,191</p><p>5-6. Cost of goods finished and transferred to Grinding...... $105,000</p><p>5-7. Total equivalent production...... 9,000 Cost of goods finished and transferred to Finishing...... $50,000</p><p>5-8. Debit Work in Process---Finishing...... $50,000</p><p>5-9. 1. Cost of goods finished and transferred to Blending...... $26,650 Cost of goods finished and transferred to Bottling...... $34,000 Cost of goods finished and transferred to Finished goods...... $57,310</p><p>CHAPTER 6</p><p>Problem 6-1. 1. Cost of goods finished and transferred to Blending Dept. for January...... $43,200 Cost of goods finished and transferred to Blending Dept. for February...... $67,200</p><p>6-2. f. Cost of finished goods transferred from work in process...... $201,700</p><p>6-3. 1. Cost of goods finished and transferred to Dept. 2...... $34,000 Cost of goods finished and on hand in Dept. 2...... $11,450 Cost of goods finished and transferred to finished goods...... $103,320</p><p>6-4. 1. Cost of completed production for Nov...... $139,650 CHECK FIGURES 45</p><p>6-5. Cost of goods finished and transferred to finished goods...... $57,000</p><p>6-6. Cost of goods finished and transferred to Dept. B ...... $39,100 Cost of goods finished and transferred to finished goods...... $61,180</p><p>6-7. Total cost of goods finished and transferred to finished goods during month...... $82,500</p><p>6-8. Cost of ending work in process$19,872 </p><p>6-9. Cost of goods finished and transferred to Finishing Dept...... $447,900 Cost of goods finished and transferred to finished goods from units started and finished during month...... $584,160</p><p>6-10. Cost allocated to Product A...... $25,420 Cost allocated to Product B...... $3,390 Cost allocated to Product C...... $560</p><p>6-11. Allocation of joint costs for Product A.... $32,500 Total allocated joint cost...... $100,000</p><p>Mini Case 1. Joint cost allocation: Product A...... $32,500 Product B……………………………………………………………………………... $13,400 Product C……………………………………………………………………………….. $54,100</p><p>CHAPTER 7</p><p>Problem 7-1. c. Total direct labor---Forming...... $324,000</p><p>7-2. 3. Total direct materials purchases...... $4,835,000 4. Total direct labor cost...... $405,500 6. Cost of goods sold...... $5,824,068</p><p>7-3. 1. Total selling and administrative expense. . . $3,939,000 2. Net income...... $1,822,159</p><p>7-4. Operating income at 31,000 units...... $1,672,880</p><p>7-5. Total variable expense variance...... $3,935 U</p><p>7-6. 1. Total factory overhead cost: at 80% ...... $8,600 at 90% ...... $8,800 at 110% ...... $9,200 2. Total variable cost: 46 CHECK FIGURES</p><p> at 80% ...... $1,240 at 90% ...... $1,530 at 110% ...... $1,870</p><p>7-7. Total fixed factory overhead...... $4,800</p><p>Mini-Case 2. Total variable expense:</p><p>At 45,000 units....$540,000 At 50,000 units....$600,000 At 55,000 units....$660,000</p><p>CHAPTER 8</p><p>Problem 8-1. 1. Material quantity variance - unfavorable...... $12.50 2. Labor efficiency variance - unfavorable...... $360.00</p><p>8-2. 3. Net materials variance - favorable. . . $234.40 6. Net labor variance - unfavorable..... $6,176.00</p><p>8-3. 2. Materials purchase price variance for Stomp - favorable...... $60,000 4. Labor rate variance - unfavorable.... $6,480</p><p>8-4. 2. Materials purchase price variance – favorable...... $520 4. Labor rate variance - favorable...... $1,640</p><p>8-5. 3. Materials purchase price variance for Class – favorable...... $3,000 6. Labor rate variance - favorable...... $6,200</p><p>8-6. Materials purchase price variance for aluminum – unfavorable...... $144 Labor rate variance - unfavorable.... $1,620 </p><p>8-7. 2. Varnish price variance - ...... $-0- Labor efficiency variance – unfavorable...... $6,000</p><p>8-8. 2. Debit Work in Process...... $99,000</p><p>8-9. 3. Total amount of direct labor cost in finished goods inventory...... $132,750 4. Total cost of goods sold...... $1,687,850 </p><p>8-10. 3. Standard hours allowed………………………………………… 4,000 5. Actual direct labor rate………………………………$8.20</p><p>8-11. Factory overhead volume variance - favorable...... $3,800 CHECK FIGURES 47</p><p>8-12. 1. Credit Factory Overhead Volume Variance-- Mixing ...... $400 Credit Factory Overhead Controllable Variance--Blending ...... $100 3. Total costs accounted for...... $33,843</p><p>8-13. 4. Volume variance (unfavorable)...... $816</p><p>8-14. Net materials variance - favorable...... $613.66 Overhead volume variance - favorable...... $360.00</p><p>8-15. 1. Spending variance - favorable...... $3,040</p><p>8-16. 1. Labor rate variance -unfavorable...... $1,144.80 2. Factory overhead efficiency variance -unfavorable...... $324.00</p><p>8-17. Factory overhead--spending variance - unfavorable...... $758.00 Factory overhead--volume variance - favorable...... $1,001.00 Net labor variance - favorable...... $183.80</p><p>8-18. Capacity variance for Mixing - favorable $300 Capacity variance for Blending...... $0</p><p>8-19. Capacity variance - favorable...... $1,650 Overhead efficiency variance - unfavorable. $1,350</p><p>RP. 4. b. Capacity variance - favorable...... $6,000 c. Efficiency variance ...... $0</p><p>Mini-Case 4. Mixing, balance in work in process…………… $11,000 5. Total cost accounted for………………………………….. $150,345 6 (b) Gross margin at actual...... $62,155 48 CHECK FIGURES CHECK FIGURES 49</p><p>CHAPTER 9</p><p>Problem 9-1. Total engagement costs...... $20,465</p><p>9-2. 1. Total variance (favorable)...... $635</p><p>9-3. 2. Total labor...... $2,840,000</p><p>9-4. 3. Operating income...... $502,000</p><p>9-5. Litigation support rate...... $4/hour</p><p>9-6. 2. Sayers Markets, total job cost...... $2,346</p><p>9-7. Shank Prod., undercosted, simplified system $1,318</p><p>Mini-Case 2. Bid price, Endicott...... $19,688 Bid price, Vestal...... $12,031</p><p>CHAPTER 10</p><p>Problem 10-1. 1. Mar. 31, fixed fact. overhd. overapplied. $11,000 Apr. 30, fixed fact. overhd. underapplied. . $(1,000)</p><p>10-2. 1. Nov., absorption costing net income…………….. $3,500 2. Nov., variable costing net income……….. $17,000</p><p>10-3. 1. North segment margin...... $176,000</p><p>10-4. 1. Territorial margin--North...... $21,200 Total company net income...... $50,000 10-5. 1. Product margin--Executive...... $4,000 Total company net loss...... $(64,000)</p><p>10-6. 1. Selling price per unit...... $9.22 2. Net income...... $36,000 3. Break-even sales volume in dollars...... $132,000</p><p>10-7. 2. Break-even sales volume in units...... 3,200 4. Net income...... $78,750 5. Break-even (units)...... 2,769</p><p>10-8. 3. Weighted average contribution margin...... $3.143 5. Product units sold (cashews)...... 1,818</p><p>10-9. 1. Break-even units...... 30,372</p><p>10-10. 1. Pre-tax income...... $833,333 3. Target volume (units)...... 22,223</p><p>10-11. 2. Bug-Off should not pay more than $3.30 per unit</p><p>RP. 1. Break-even sales volume in dollars...... $2,448,000 2. Units that must be sold...... 142,400 50 CHECK FIGURES</p><p>Mini-Case 2. Alternative 2 will result in $40,000 more CM.</p>
Details
-
File Typepdf
-
Upload Time-
-
Content LanguagesEnglish
-
Upload UserAnonymous/Not logged-in
-
File Pages10 Page
-
File Size-