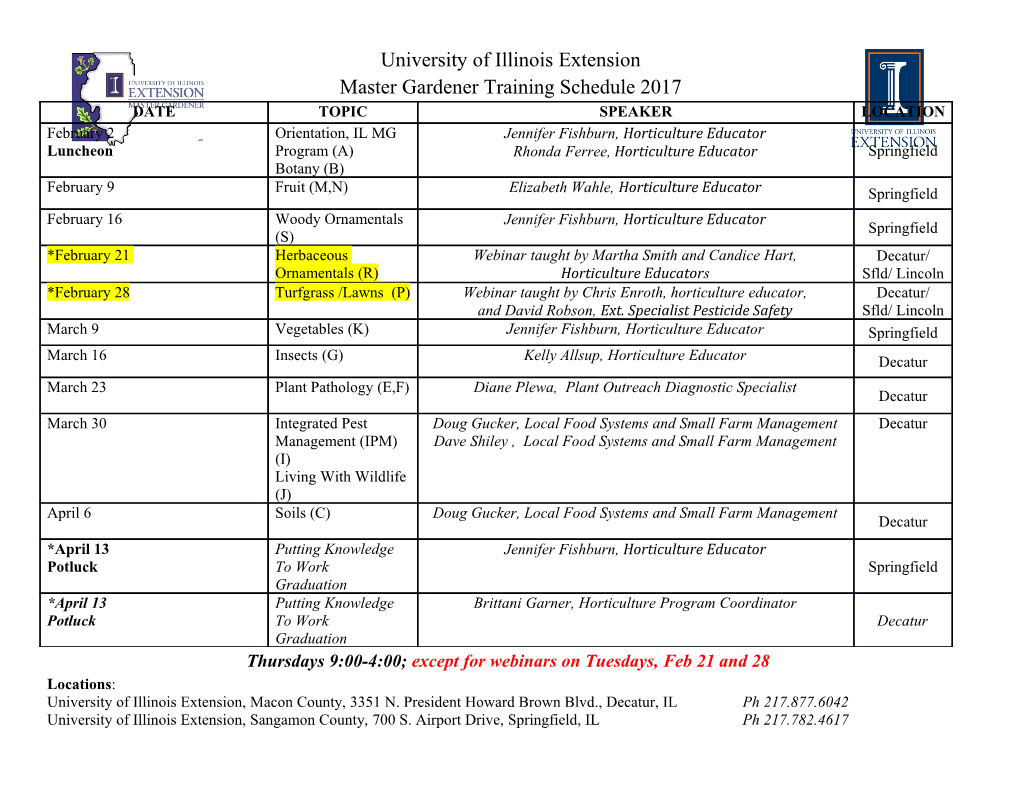
409 CORRELATION OF VISUAL AND INSTRUMENTAL COLOR MEASUREMENTS TO ESTABLISH COLOR TOLERANCE USING REGRESSION ANALYSIS by MALATHY JAWAHAR,* SWARNA V. KANTH, R. VENBA AND NARASIMHAN KANNAN CHANDRA BABU Council of Scientific and Industrial Research-Central Leather Research Institute, Adyar, Chennai 600 020, India ABSTRACT perceptible changes in the leathers need to be characterized and the batch can be assorted into acceptable and unacceptable Color is one of the important parameter considered in the groups to enable corrective measures. The color variations are determination of quality for fashion materials like leather. The due to inconsistency in raw material homogeneity and leather color variation in each piece of leather sample in a batch processing technology adopted that result in variations in dye should be within the acceptable range. Visual assessment is diffusion and uptake. Even though hides and skins are currently used in leather industry for quality control and color processed and finished with organolleptic properties needed sorting. The current method used is subjective and often leads for end-use applications; the resultant leathers may be rejected, to disagreement between buyer and seller. Color measurement if the color does not match the buyer’s sample/swatch (beyond using reflectance spectrophotometer evaluates color 5% tolerance limit). Assortment of color into groups of almost consistently and is an objective assessment system. However, similar shades is also done during the manufacture of leather there is always an apprehension that the instrumental color products. The panels of leather product should be of same assortment may not agree with the human perception of color color as more than one piece of leather is used. Leather difference. Hence, in the present investigation, an attempt was manufacturers and leather goods/garment/footwear producers made to screen four color difference formulae, viz., consider shade-sorting as a challenge to bring in color CIELAB76, CMC (2:1), CIE94 and CIE2000 for their consistency using visual assessment. suitability in obtaining pass/fail decisions, which would be in conformity with that of the average human observer. Visual evaluation of color tolerance is not consistent when Regression analysis was performed to find a correlation establishing the fine line between acceptable color differences between visual and instrumental color assessments and the (maximum color difference between the standard and sample) results indicate that CMC(2:1) formula may be the most suited and perceptible color differences (minimum color difference for the purpose. A detailed analysis of visual and instrumental between the standard and sample). Such a highly subjective 1 color values revealed visual non-uniformity towards sensitivity visual color assessment system generally results in dispute to hue, chroma and lightness. This difference in sensitivity between the buyer and the seller of the leathers. Large errors was also taken into consideration in instrumental color sorting in judgment are common due to lack of experience and color and pass/fail tolerance was established that led to closer vision defects of the evaluators. But error occurs even among conformity between visual and instrumental methods. the experienced evaluators due to ageing and fatigue. There is a growing need to shade-sort leather samples consistently with the increasing stringent demands by quality conscious INTRODUCTION customers. Leather manufacturers produce large consignment of leathers Advancements in computer technology have made it possible in a particular shade/color with a reasonable degree of to replace the visual evaluation with instrumental objective accuracy to meet the requirement of a buyer. Color is a vital color measurements to obtain reproducible and reliable data factor used during quality inspection of finished leathers for that give consistent pass/fail decisions. Acceptable color limits different end products. Nevertheless, color variations within a are set as tolerances on color scales or indices such as L*a*b* batch of leathers are inevitable even though dyeing/finishing (ΔL value ‘+’ is lighter and ‘–’ for darker, Δa is ‘+’ for redder is carried out with best process control systems due to and ‘–’ for greener and Δb value is ‘+’ for yellower and ‘–’ for heterogeneity of the substrate. Color variations with bluer) and LCH (ΔL value ‘+’ is lighter and ‘–’ for darker, ΔC value represents the difference in chroma ‘+’ for brighter / * Corresponding author e-mail: [email protected] Manuscript received March 15, 2015. Accepted for publication August 17, 2015. JALCA, VOL. 110, 2015 VISUAL AND INSTRUMENTAL COLOR ANALYSIS 410 more saturated and ‘–’ for duller / less saturated and ΔH value represents chroma or intensity or ‘saturation’ ranging from represents shift in hue angle ‘+’ for increase in hue angle 0-100. For unsaturated colors such as grey, black or white C*= and ‘–’ for decrease in hue angle). There are several color 0. For very high chroma (saturation) or intense colors or pure space options available for implementing pass/fail tolerance colors C*=100. The h* axis represents hue and is represented program. Determining instrumental tolerance limit for leather in degrees. ho is ranging from 0° (red) through 90° (yellow), is a difficult process due to variations in shade from/within 180° (green), 270° (blue) and back to 0°. customer to customer and product to product with stringent acceptance levels. Hence, it is necessary to select instrumental CIE 1994 (Equation 2) employs simple linear functions of method that gives the best correlation with the visual color chroma and hue to obtain SC, SH and unity to SL. It also 14 perception. Four color difference formulae, viz., CIE1976, includes parametric assessing functions KL, KC and KH to CIE94, CIE 2000 and CMC(2:1) were selected for the present provide better correlation to visual difference.15,16 In the study and their suitability for color assortment for an present study, parametric functions assumes KL=2, KC =1 and achromatic color like grayish black was investigated. The KH = 1. characteristic feature of the four color formulae are summarized as follows. (2) * CIE1976 (ΔE ab) CIE1976 is the first color difference formula recommended by Where SL = 1, SC = 1 + 0.045C* and SH = 1+0.015C* CIE (Commission de lÉclairage) for surface color evaluation 2 * and used in many color industries that include leather. CIE2000 (ΔE 00) CIE1976 color formula is based on the CIE LAB3 color space. An attempt was made to improve upon CIE 1994 equation by In CIE LAB color notation, L* axis represents lightness value, adding more assessing factors depending on the hue angle of ranging from 0 (black) to 100 (white). a* axis value is ‘+’ for the color which resulted in CIE2000.17,18,19 CIE2000 (Equation redder and ‘a’ value is ‘–’ for greener; similarly b* axis value 3) color difference equation is complicated but does not tend is ‘+’ for yellower and ‘b’ value is ‘–’ for bluer. There are no to show improvement in correlation with visual differences. maximum and minimum values for a* and b*, however in practice they are numbered as -128 to + 127 (256 levels). (3) Difference between two color samples is often expressed as Delta E, also called ΔE. ΔE values show how far the two * samples are visually apart in the color sphere and is defined as Color Measurement Committee (ΔE cmc) an Euclidean distance in a uniform space, which include CMC equation (Equation 4) was created by the Color difference in lightness L*, red-green difference in terms of a* Measurement Committee of the Society of Dyers and 20 and yellow-blue difference in terms of b*. The mathematical Colourists of Great Britain. It is a British standard and 21 20,22 equation to compute overall the color difference is given in drafted as an ISO standard and used in many industries. 23,24 Equation 1. It was reported by Mc Donald that L*a*b* color CMC and CIE94 DE calculation defines a tolerance 15 notation is not visually uniform4 and several experimental ellipsoid corresponding to hue, chroma and lightness and is investigations have proved that DE CIELAB 76 does not distinct from the rectangular co-ordinates of CIELAB color ab 17 agree well with visual perception.5-11 space. In CMC (2:1) (Equation 4) DE is similar to the CIE94 DE (Equation 2) in terms of assessing on the lightness, chroma, and hue of the colors. CMC(2:1) equation employs hyperbolic regression analysis model to compute ellipsoidal (1) semi-axes (lSL, cSC, SH) (Equation 5, 6 and 7); l and c refers to constants 1,1 or 2,1 depending on the tolerance given to * lightness and chroma co-ordinates. The size and the shape of CIE1994 (ΔE 94) Considerable work was also done in the area of developing the CMC tolerance ellipsoid vary for each color and hence color difference equations, which describe perceived color ellipsoidal volume of acceptance varies. difference for practical use in coloration industry. An attempt was made by CIE in 1994 to correct the visual non-uniformity (4) of L*a*b* by assessing lightness, chroma and hue in different proportions.11-12 The CIE1994 color difference equation was developed based on CIE LCH color notation with two sets of coefficients (KL, KC, KH and SL, SC, SH) that account for effects influencing color difference judgment and CIELab’s lack of (5) visual uniformity.13 In CIE LCH notation, L* axis represents lightness ranging from 0-100. C* axis JALCA, VOL. 110, 2015 411 VISUAL AND INSTRUMENTAL COLOR ANALYSIS The average of the visual difference for all 20 experts was computed and listed in Table I. Instrumental Color Analysis (6) Reflectance measurements were carried out using Premier Colorscan reflectance spectrophotometer interfaced with a computer. Before commencing color measurement, the (7) instrument was calibrated against white MgO tile. D65 illuminant with 10-degree standard observer including UV component and excluding specular component with Do8 Performance of the above color difference formulae (Equation geometry were set for measurement of reflectance.
Details
-
File Typepdf
-
Upload Time-
-
Content LanguagesEnglish
-
Upload UserAnonymous/Not logged-in
-
File Pages11 Page
-
File Size-