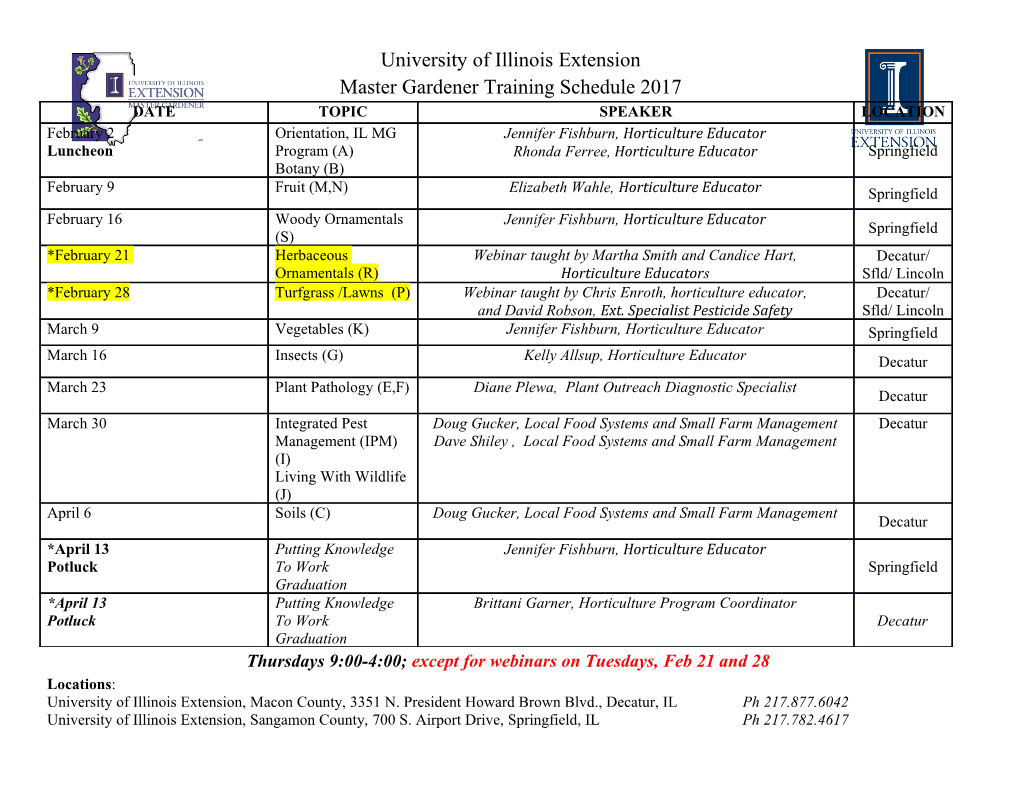
sensors Article Analysis of Temperature and Humidity Field in a New Bulk Tobacco Curing Barn Based on CFD Zhipeng Bai, Duoduo Guo, Shoucang Li and Yaohua Hu * College of Mechanical and Electronic Engineering, Northwest A&F University, Yangling 712100, China; [email protected] (Z.B.); [email protected] (D.G.); [email protected] (S.L.) * Correspondence: [email protected]; Tel.: +86-29-8709-2391 Academic Editor: Gonzalo Pajares Martinsanz Received: 12 November 2016; Accepted: 24 January 2017; Published: 31 January 2017 Abstract: A new structure bulk tobacco curing barn was presented. To study the temperature and humidity field in the new structure tobacco curing barn, a 3D transient computational fluid dynamics (CFD) model was developed using porous medium, species transport, κ-" turbulence and discrete phase models. The CFD results demonstrated that (1) the temperature and relative humidity predictions were validated by the experimental results, and comparison of simulation results with experimental data showed a fairly close agreement; (2) the temperature of the bottom and inlet area was higher than the top and outlet area, and water vapor concentrated on the top and outlet area in the barn; (3) tobacco loading density and thickness of tobacco leaves had an explicit effect on the temperature distributions in the barn. Keywords: bulk tobacco curing barn; computational fluid dynamics; temperature and humidity field; sensors 1. Introduction In China, the bulk tobacco curing barn has been popularized during the last two decades due to high capacity and curing quality. In 1960, the first farm-scale operation in bulk curing was initiated in North Carolina [1]. Traditional natural ventilation used in the traditional tobacco curing barn was displaced by forced ventilation used in the bulk tobacco curing barn. Different from the traditional tobacco curing barn, the bulk tobacco curing barn added the hot air circulation system and the auto control system, which can save costs of energy and liberate manpower. Due to the application of forced ventilation technology, the diversity of structure of the bulk tobacco curing barn with different air flow directions is gaining a lot of interest in recent tobacco curing studies, specifically, the bulk tobacco curing barns with air rising [2,3], and air descending [4], which are the most common. In general, tobacco flue curing can be divided into yellowing, leaf drying, and stem drying stages [5]. Changes in tobacco flue curing processes are mainly the result of water evaporation and enzymatic reaction [6]. In addition, the quality of curing tobacco is influenced by the air flows, temperature and relative humidity distribution in bulk tobacco curing barn. Computational fluid dynamics (CFD) is increasingly being used to simulate flow field, mass and heat transfer. The capability of CFD modeling to predict air flows and temperature and relative humidity distributions for many applications in thermosyphon [7] and cool store [8] has been demonstrated. Temperature and relative humidity distributions in the tobacco drying process have been studied using artificial neural networks [9]. However, numerical studies focusing on tobacco curing barn were rarely considered. Zhang et al. [10] simulated the temperature field in tobacco oven during the drying process of cut tobacco based on the finite volume method. Wei et al. [11] studied the temperature distribution of tobacco curing barn with experiments and numerical simulation. Bao et al. [12] performed numerical studies for obtaining the temperature, humidity and velocity field Sensors 2017, 17, 279; doi:10.3390/s17020279 www.mdpi.com/journal/sensors Sensors 2017, 17, 279 2 of 15 Sensorssimulation.2017, 17 Bao, 279 et al. [12] performed numerical studies for obtaining the temperature, humidity2 ofand 16 velocity field in the tobacco curing barn. They applied a mixture model and porous medium to simulate the water evaporation process and tobacco leaves. Water-phase was introduced into the in the tobacco curing barn. They applied a mixture model and porous medium to simulate the water curing barn from inlet boundary. Tobacco leaves contained almost all the water in bulk tobacco evaporation process and tobacco leaves. Water-phase was introduced into the curing barn from inlet curing barn. As the water came from tobacco leaves and evaporated in them, it is therefore boundary. Tobacco leaves contained almost all the water in bulk tobacco curing barn. As the water necessary to develop a numerical model that would make possible to introduce water into the came from tobacco leaves and evaporated in them, it is therefore necessary to develop a numerical curing barn from tobacco leaves and predict temperature and relative humidity distributions model that would make possible to introduce water into the curing barn from tobacco leaves and accurately. predict temperature and relative humidity distributions accurately. A new structure bulk tobacco curing barn heated by heat pump was presented and a 3D A new structure bulk tobacco curing barn heated by heat pump was presented and a 3D transient transient CFD model using the species transport and the discrete phase models to predict the CFD model using the species transport and the discrete phase models to predict the temperature and temperature and humidity distributions in the bulk tobacco curing barn was developed in this humidity distributions in the bulk tobacco curing barn was developed in this study. The objectives of study. The objectives of this study were (1) to validate the CFD model with experimental this study were (1) to validate the CFD model with experimental temperature and relative humidity temperature and relative humidity data during the curing process; (2) to study the description of the data during the curing process; (2) to study the description of the temperature and water vapor mass temperature and water vapor mass fraction profiles in the tobacco curing barn; (3) to study the fraction profiles in the tobacco curing barn; (3) to study the temperature distributions with different temperature distributions with different porosities and particle average diameters. This can be the porosities and particle average diameters. This can be the basis for tobacco curing process and barn basis for tobacco curing process and barn design optimization. design optimization. 2. Materials and Methods 2.1. Description of the New Bulk Tobacco CuringCuring BarnBarn The new structure bulk tobacco curing barn was 8.2 m long, 2.9 m wide and 3.6 m high, and its total volumevolume waswas 8585 mm33. The barn contained two main parts: a tobacco curing chamber and an air return chamber. The ahead vertical wall was hidden to show internal structure in the curing barn as shown inin FigureFigure1 .1. The The tobacco tobacco curing curing chamber chamber and a thend airthe returnair return chamber chamber were were separated separated by a 0.1 by m a thick0.1 m layerthick oflayer polyurethane of polyurethane foam sandwich foam sandwich panel, andpanel two, and heat two pumps heat onpumps the roof on the provided roof provided heat for theheat radiators for the radiators on the both on left the and both right left sides and ofright the polyurethanesides of the polyurethane foam sandwich foam panel. sandwich There were panel. air holesThere andwere emergency air holes and gates emergency on the polyurethane gates on the foam polyurethane sandwichpanel. foam sandwich A steel frame panel. which A steel was frame 7.3 m long,which 2.7 was m wide7.3 m and long, 2.6 2.7 m highm wide was and placed 2.6 inm curinghigh was chamber. placed Tobacco in curing leaves chamber. were tiedTobacco along leaves sticks ofwere bamboo tied along before sticks being of placedbamboo on before the steel being frame. placed And on bamboo the steel curtains frame. And were bamboo hung on curtains both sides were of steelhung frame on both to protectsides of tobaccosteel frame leaves to protect as shown tobacco in Figure leaves2. as shown in Figure 2. Figure 1. StructureStructure of of bulk bulk tobacco tobacco curing curing barn barn.. 1. 1.Left Left wall wall;; 2. L 2.eft Leftfan unit fan; unit; 3. Left 3. radiator Left radiator;; 4. Heat 4. Heatpump pump;; 5. Air 5. holes Air holes;; 6. Emergency 6. Emergency gate; gate;7. Steel 7. Steelframe frame;; 8. M 8.oisture Moisture discharged discharged holes holes;; 9. Inlet 9. Inlet;; 10. 10.Polyurethane Polyurethane foam foam sandwich sandwich panel panel;; 11. 11. Tobacco Tobacco curing curing chamber chamber;; 12. 12. A Airir return return chamber chamber;; 13. RightRight radiator;radiator; 14. RightRight fan unit;unit; 15. R Rightight wall wall.. Sensors 2017, 17, 279 3 of 16 Sensors 2017, 17, 279 3 of 15 Figure 2. Tobacco curing chamber. 1. Bamboo curtain; 2. Steel frame; 3. Stick of bamboo; 4. Tobacco leaves. Figure 2. Tobacco curing chamber. 1. Bamboo curtain; 2. Steel frame; 3. Stick of bamboo; 4. Tobacco leaves. The air entered the air return chamber from the inlet of the roof as shown in Figure 1. The main stream, which was heated by the right radiator, went through the right fan unit. After being blown into theThe tobacco air entered curing the airchamber, return chamberthe stream from went the through inlet of the tobacco roof as leaves, shown going in Figure up 1through. The main the moisturestream, which discharged was heated holes, by the the air right holes radiator, and mostly went the through left fan the unit. right The fan a unit.ir that After went being up through blown into air holesthe tobacco and left curing fan unit chamber, returned the the stream tobacco went curing through chamber tobacco through leaves, the going left upfan throughunit, and the the moisture air that wentdischarged up through holes, moisture the air holes discharged and mostly holes the exited left fan the unit.
Details
-
File Typepdf
-
Upload Time-
-
Content LanguagesEnglish
-
Upload UserAnonymous/Not logged-in
-
File Pages16 Page
-
File Size-