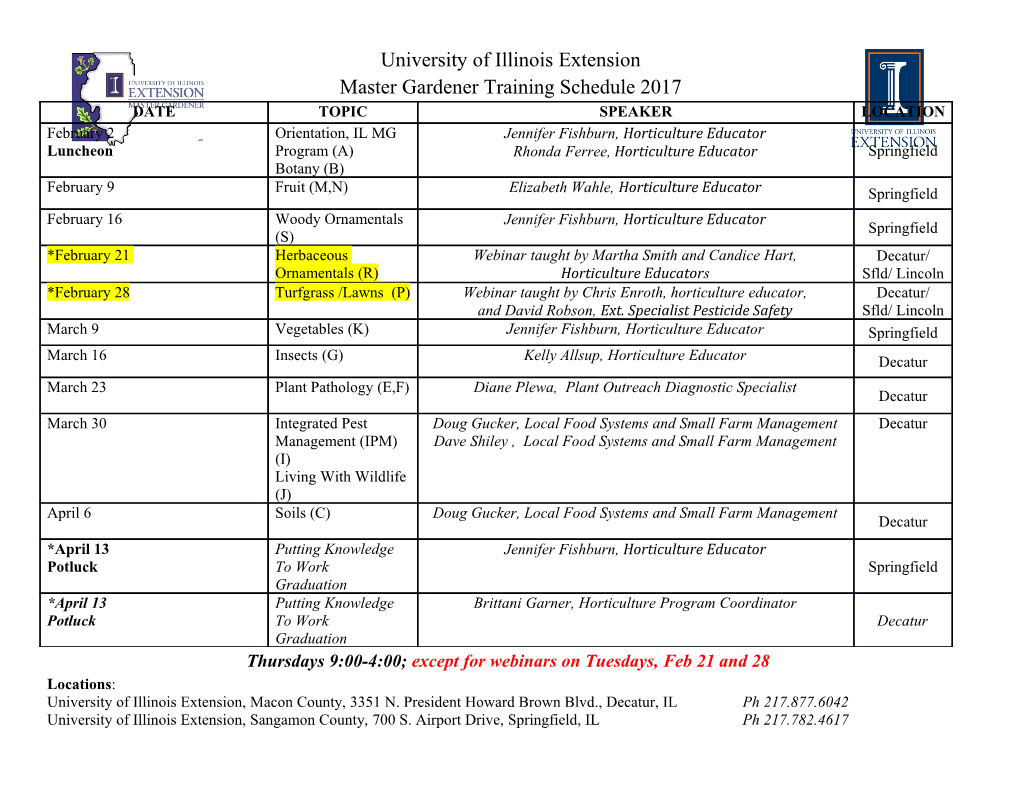
ROBUST DESIGN FOR STRUCTURAL OPTIMIZATION PROBLEMS DUE TO PARAMETER UNCERTAINTIES C. Zang Department of Mechanical Engineering, University of Wales Swansea, Singleton Park, Swansea SA2 8PP, UK M.I. Friswell Department of Aerospace Engineering, University of Bristol, Queen’s Building, Bristol BS8 1TR, UK J.E. Mottershead Department of Engineering, University of Liverpool, Brownlow Hill, Liverpool L69 3GH, UK ABSTRACT SS The sum of squares due to the overall experimental µy mean Product performance is now, more than ever, a critical The number of rows in the orthogonal array matrix requirement for success in manufacturing. However, n significant uncertainty exists in material and geometrical experiments n The replication number of the design parameter X parameters, such as modulus, thickness, density and X j i residual strain, and also in joints and component assembly. i The variance in the structural dynamics (noise and vibration at the j level µ The mean for each parameter X response) is critical to the system performance. Approaches Xi i to identify and remove sources of variability play an important role in the design of products. This paper presents 2 σX The Variance for each parameter Xi a technique based on robust design for structural i ∆ The expanded standard deviation optimisation problems due to parameter uncertainties. The Xi Monte Carlo method is commonly used, but is expensive due to the large number of random samples required to GTSS The grand total sum of squares accurately simulate the structural system response to the TotalSS The sum of squares due to the variation about the uncertain parameters. In this paper, orthogonal arrays are mean used to study the effect of uncertainty in many design parameters simultaneously. The analysis of variance (ANOVA) is applied for determining the principal variables and their contribution to the dynamic response. The methodology is illustrated with an example of a spot welded 1. INTRODUCTION column model. The results show the feasibility of this approach for the robust design in order to minimise the The improvement in performance is vital in the development variance in the dynamic response due to the variability of the of any system such as a vehicle. This is usually performed parameters. using tools of engineering design optimisation in order to meet design targets. However, design optimisation may not always satisfy the desired targets due to the significant NOMENCLATURE uncertainty that exists in material and geometrical parameters such as modulus, thickness, density and residual strain, as well as in joints and component assembly. Ways to X The i-th variable parameter i minimize the effect of variations of uncertainty on the yi The system response of the i-th experiment performance are of paramount concern to researchers and µy The overall mean from the orthogonal array matrix practitioners in the academic and engineering fields. experiment Robust design, that explicitly recognises the effects of the µ y j The average of the nX responses for each level j uncertainty variation and improves the effectiveness and X i i efficiency of design optimisation, provides an approach to achieve a more consistent performance of product features. Robustness in structural dynamics aims to make the variance of the noise and vibration response of a product 2. THE TAGUCHI METHOD insensitive to the variations of the design variables. In recent years, various approaches to robust optimisation have been Taguchi’s approach to the product design process may be developed. The genetic algorithm has been applied to the divided into three stages: system design, parameter design, robustness of optimal design solutions to reduce vibration and tolerance design [14]. System design is the conceptual transmission in a lightweight 2-D structure [1-3]. The change design stage where a system is developed that functions in the performance of the optimal structures due to small under an initial set of nominal conditions. Parameter design geometric perturbations, representing manufacturing is the stage at which a targeted concept is optimised by tolerances, was also investigated by a robustness analysis. using specific set levels that makes the system less sensitive Sandgren and Cameron [4] used a hybrid combination of a to noise, thereby enhancing the system’s robustness. genetic algorithm and non-linear programming for robust Tolerance design aims to specify the allowable deviations in design optimisation of structures with variations in loading, the parameter values, loosening tolerances where possible geometry and material properties. A fuzzy finite element and tightening where necessary. The following steps briefly approach may be used to model vague uncertainties in describe the Taguchi method for finding the optimum setting structural systems [5, 6]. Monte Carlo simulation is often of the design variables to make the response insensitive to used to propagate uncertainty, due to its generality and noise factors, which may be regarded as the design and straight-forward approach to modelling the uncertainty of the manufacturing tolerances in a numerical structural analysis. input parameters [7, 8]. The major advantage is that an accurate solution can be obtained and higher order statistical (i). To determine the response characteristic to be movements and the probability distribution of the response optimised, the design parameters and their noise quantities can be computed. However, Monte Carlo factors (uncertainty of design parameters). simulation has to simulate a large number of combinations of the uncertain inputs, called testing conditions, using a (ii). To design the experiment matrix to determine the random number generator. The value of the response is effect of the design parameters and conduct the data computed for each testing condition, and the mean and analysis procedure. After selecting the appropriate variance of the response are then calculated. To obtain orthogonal array for the noise and parameters to fit a accurate estimates of the mean and variance, the Monte specific study, variations in the response Carlo method requires evaluation of the response for a large characteristic due to the noise factors are simulated. number of testing conditions. This can be very expensive. Another popular method, the Taylor Series expansion (iii). To analyse the data and determine the optimum method (or perturbation technique) [9, 10], estimates the levels. After the experiments have been conducted, variance of the response by using the derivatives of the the optimal parameter configuration within the response with respect to each uncertain parameter. The first- experiment design must be determined. The order Taylor series expansion can only give accurate experiment results are analysed using the ANOVA estimates when the variations are small. Otherwise, higher technique and the optimum levels for the parameters order Taylor series expansions must be used, which makes are determined. the formula to evaluate the response quite complicated and computationally expensive. In contrast to the above methods, Taguchi developed an 3. ORTHOGONAL ARRAYS FOR THE DESIGN OF efficient and systematic methodology that applies statistical EXPERIEMENTS experimental design to improve product and manufacturing design [11, 12]. The Taguchi method has been used An experimental design represents a sequence of successfully in Japan and the United States to design experiments to be performed. The most basic experimental reliable, high quality products at low cost in such areas as design method is a full factorial design which investigates all the automobile industry, consumer electronics and the possible combinations, maximising the possibility of finding a aerospace industry. Recently, Lee and Park [13] favourable result. In general, if there are s structural design implemented the Taguchi method for the robust design of parameters, each at r levels, the total number of unconstrained optimisation problems. Standard structural combinations required to guarantee completeness is r s . For examples, such as the three and ten bar truss structures, example, by varying design parameters one at a time, the were treated and illustrated as well as other engineering study of 13 design parameters at 3 levels would require applications. 1,594,323 (313) possible experimental evaluations. Obviously, the size of a full factorial experiment increases In this paper, the Taguchi method will be used for structural exponentially with the number of design parameters. Many optimisation problems with parameter uncertainties. The design parameters will lead to simulations that are dynamic structural performance of a benchmark spot welded computationally intensive and impractical. column structure, inspired by the columns in automotive bodies, is investigated as an example. The effect of The orthogonal array experiment is a method of setting up uncertainty in design parameters, such as the plate experiments that need only a fraction of the experiments thickness and the diameter of the spot welds, are studied required for a full factorial combination. Orthogonal refers to simultaneously using orthogonal arrays and the analysis of the fact that the effect of each variable can be variance (ANOVA). mathematically assessed independently, without considering the effects of the other variables. The combinations are factor effects around the overall experimental mean chosen to provide sufficient information to determine the response. Figure 1 summarizes
Details
-
File Typepdf
-
Upload Time-
-
Content LanguagesEnglish
-
Upload UserAnonymous/Not logged-in
-
File Pages7 Page
-
File Size-