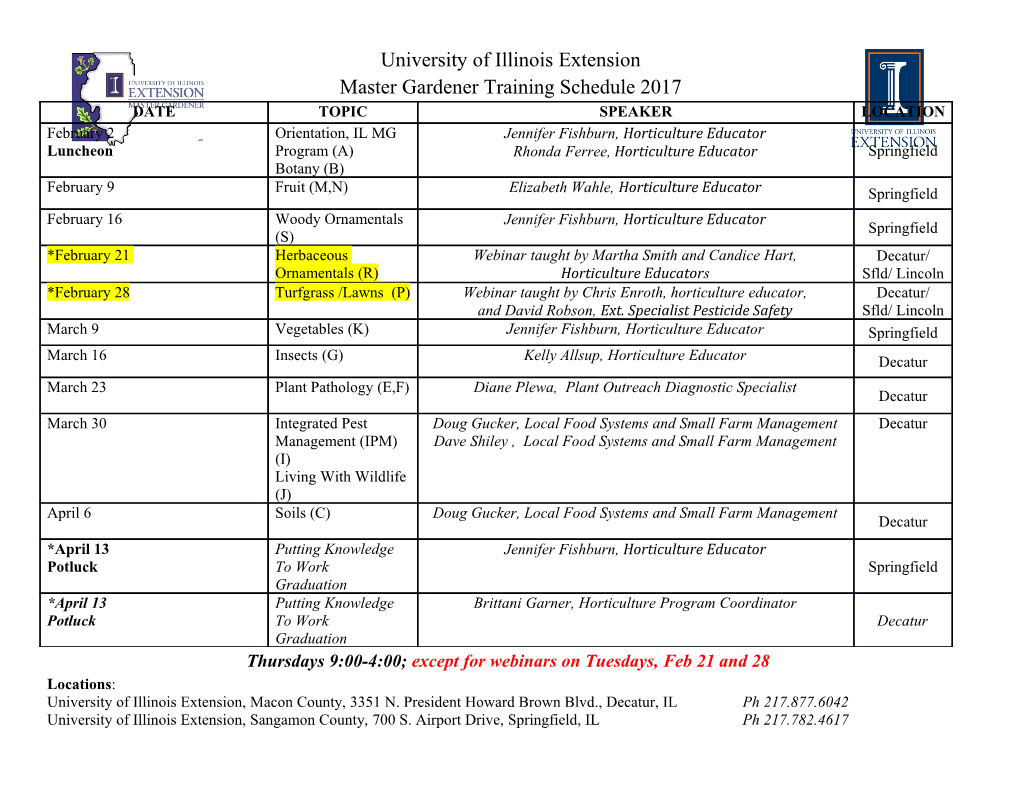
UNIVERSITY OF CINCINNATI Date:___________________ I, _________________________________________________________, hereby submit this work as part of the requirements for the degree of: in: It is entitled: This work and its defense approved by: Chair: _______________________________ _______________________________ _______________________________ _______________________________ _______________________________ Synthesis, Characterization and Kinetic Studies of Mixed Metal Mo-V-Nb-Te Oxide Catalysts for Propane Ammoxidation to Acrylonitrile A thesis submitted to the Division of Research and Advanced Studies of the University of Cincinnati in partial fulfillment of the requirements for the degree of Master of Science In the Department of Chemical and Materials Engineering of the College of Engineering December 2005 by Salil Bhatt B.Tech., Indian Institute of Technology Bombay, India, 2002 Committee Members Dr. Vadim V. Guliants (Chair) Dr. Peter Smirniotis Dr. Soon-Jai Khang Abstract The ample abundance and low cost of propane has recently spurred an interest in the manufacture of acrylic acid and acrylonitrile from propane, both important intermediates in the manufacture of plastics and clothing. Commercially, both are currently manufactured based on a process utilizing propylene as the feedstock, which is high in demand and expensive. Many catalytic systems have been proposed and tested for the oxidation and ammoxidation of propane to acrylic acid and acrylonitrile respectively. Of these, the four component mixed metal oxide system Mo-V-Nb-Te has been found to be the most promising for acrylic acid and acrylonitrile manufacture. The objective of this work has been to study the effect of temperature, catalyst weight and flow rates on the yield and selectivity to various product species and to formulate a reaction mechanism that would assist in making further predictions on the reaction outcome for various reaction parameters. Acknowledgments I would like to express my sincere gratitude to my advisor, Dr. Vadim V. Guliants, for his ideas, support and guidance throughout the duration of the project. His invaluable experience in the field of catalysts has been instrumental in gearing the progress and direction of this work. His dedication to research, science and technology has been an ideal model to follow throughout my thesis work. I am thankful to the Chemical Sciences, Geosciences and Biosciences Division, Office of Basic Energy Sciences, Office of Science, U.S. Department of Energy under the Grant No. DE-FG02-04ER15604, without which the funds needed to accomplish this research would not be available. I would like to thank Dr. Junichi Ida, who has played a vital role in assisting me during preparation of the experimental setup, testing and calibration of the GC detectors and mass flow controllers. Beyond this, he has also extended his invaluable experience in providing much needed suggestions and guidance during the experimental stages of the project. I would also like to thank Mr. Rishabh Bhandari for his assistance in guiding me through various phases of synthesizing the catalyst, characterization and kinetic testing. I would also like to thank Mr. Balasubramanian Swaminathan, Mrs. Li Yuan and Mr. Neelakandan Chandrasekaran not only for their valuable suggestions and feedback but for their co-operation and moral support. Last but not the least; I would thank all of my other group mates for their valuable feedbacks and suggestions. Table of Contents List of Tables iii List of Figures iv Chapter 1 Introduction 1 Chapter 2 Current trends in acrylonitrile processing 5 2.1 Introduction 5 2.2 Structure of bulk mixed Mo-V-Nb-Te-Ox catalyst 10 2.3 Synthesis and Characterization of Mo-V-Nb-Te oxides 13 Chapter 3 Reaction Kinetics 19 3.1 Introduction 19 3.2 Kinetics as a function of propane conversion 22 3.3 Calculation of activation energy for propane conversion 26 3.4 Evaluation of reaction rate orders 29 3.4.1 Reaction rate order for oxygen 30 3.4.2 Reaction rate order for ammonia 31 3.4.3 Reaction rate order for propane 33 3.5 Reaction mechanism 35 Chapter 4 Design of a productive ammoxidation catalyst 46 4.1 Introduction 46 4.2 Effect on the purity level of nitrogen gas during calcination 47 4.3 Effect of catalyst composition 50 Appendix A Experimental Setup 52 A.1 Description of equipment 52 A.2 Schematic and design of the experimental setup 56 Appendix B Procedure for Chemical Analysis 59 B.1 Temperature ramp settings 59 B.2 Valve switching 62 Appendix C Calibration 63 C.1 Calibration of Mass Flow Controller 63 C.2 Calibration of the GC detectors 65 Appendix D Simulation code listing 66 References 70 ii List of Tables 1. Industrial processes under study or development for oxidative transformation of light alkanes 01 2. Comparison of different catalysts for propylene ammoxidation 06 3. Comparison of different catalysts for propane ammoxidation 08 4. Comparison of surface areas of Mo-V-Nb-Te catalyst obtained using different synthesis routes 17 5. Comparison of kinetic activity for catalysts synthesized using hydrothermal and dry-up methods 18 6. Temperature vs. reaction rate using 0.073g of catalyst & 36.5 ml/min flow rate 27 7. Reaction rate orders for individual products w.r.t. individual reactant species 29 8. Reaction rate constants for propane ammoxidation pathway 37 9. Reaction rate constants for propane ammoxidation pathway with propylene to acrylonitrile as an added path 38 10. Reaction rate constants considering propylene as an intermediate 40 11. Retention times of primary organic species (minutes) 61 12. Retention times of light and inorganic gases using just Porapak Q column 61 iii List of Figures 1. Electronegativity and catalytic behavior of metal oxides 07 2. Reaction pathway for conversion of propane to acrolein 09 3. Structure of the M1 phase 10 4. Structure of the M2 phase 11 5. XRD of catalyst prepared by (a) Dry-up and (b) hydrothermal methods 16 6. SEM image of catalyst prepared using dry-up synthesis 17 7. SEM image of catalyst prepared using hydrothermal synthesis 17 8. Effects of reaction temperature upon conversion, selectivities and yields 23 9. Variation of selectivity of various components at different propane conversions 24 10. Variation of the yield of various components at different propane conversions 24 11. Natural logarithm of reaction rate vs. inverse of temperature 28 12. Natural logarithm of rate of formation of product species vs. natural log of oxygen concentration 30 13. Natural logarithm of rate of formation of product species vs. natural log of ammonia concentration 32 14. Natural logarithm of rate of formation of product species vs. natural log of propane concentration 34 15. Proposed propane ammoxidation reaction pathway 36 16. Proposed route for propane ammoxidation with intermediate propylene 39 17. Predicted vs. observed concentration data for propane 41 18. Predicted vs. observed concentration data for propylene 42 19. Predicted vs. observed concentration data for acrylonitrile 42 iv 20. Predicted vs. observed concentration data for acetonitrile 43 21. Predicted vs. observed concentration data for carbon oxides 43 22. Synthesis route followed for MoVNbTeOx metal oxides 46 23. Comparison of the X-Ray Diffraction pattern for industrial and pre-purified grade nitrogen 48 24. Comparison of kinetic activity of catalysts calcined by industrial and pre-purified grade nitrogen 49 25. Comparison of kinetic performance of catalysts with varying niobium contents 51 26. Diagram of the GC analysis system 56 27. Schematic of six-way valve used for injecting effluent samples 57 28. Schematic of six-way valve connecting Porapak Q and molecular sieve 57 29. Calibration curve for helium gas 64 30. Calibration curve for oxygen gas 64 31. Calibration curve for propane gas 65 v Chapter 1 Introduction The industry today is predominantly reliant on the use of olefins as raw materials for the manufacture of a large number of chemical intermediates. However, the abundant natural abundance and lower cost of paraffin’s as compared to olefins has generated an interest in obtaining these intermediate products through direct catalytic conversion of paraffin’s by bypassing olefin manufacture as an intermediate step, as opposed to the current commercial method of using olefins. Various alternatives are now currently being sought in this regard. Different catalytic systems have been devised and investigated for the successful conversion of the corresponding alkane to the desired reaction product [1- 4]. So far, the one reaction that has been quite successfully implemented using an alkane is that of oxidation of n-butane to maleic anhydride, which is based on the now famous Vanadium-Phosphorous metal oxide system [5-7]. Table 1.1: Industrial processes under study or development for oxidative transformation of light alkanes (C1 – C6) [20] Raw Material Product Stage of development Methane Methanol Pilot plant Methane Syngas Pilot plant Methane Ethylene Pilot plant Ethane 1,2-dichloroethane, vinyl chloride Pilot plant Ethane Acetaldehyde Research 1 Ethane Acetic Acid Research Ethane Ethylene Research Propane Acrolein, Acrylic Acid Research Propane Propyl Alcohol Research Propane Acrylonitrile Demonstrative plant Propane Propylene Research n-Butane Acetic Acid Industrial n-Butane Maleic Anhydride Industrial n-Butane Butadiene Industrial, abandoned Isobutane Methacrylic acid Pilot plant Isobutane Isobutene Research Isobutane t-Butyl Alcohol Research n-Pentane Phthalic anhydride Research Cyclohexane Cyclohexanol, cyclohexanone
Details
-
File Typepdf
-
Upload Time-
-
Content LanguagesEnglish
-
Upload UserAnonymous/Not logged-in
-
File Pages83 Page
-
File Size-