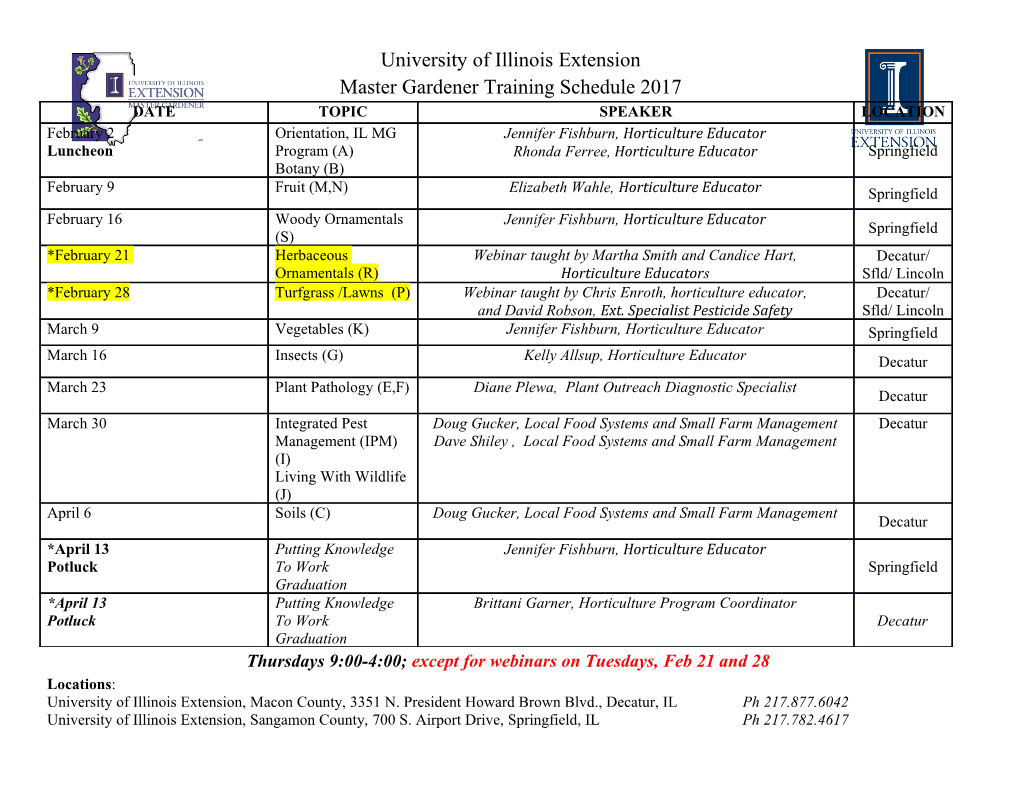
Engineering Failure Analysis 7 (2000) 427±450 www.elsevier.com/locate/engfailanal Damage due to hydrogen embrittlement and stress corrosion cracking Jarmila Woodtli, Rolf Kieselbach* EMPA, Uberlandstrasse 129, CH-8600 Dubensorf, Switzerland Received 3 September 1999; accepted 20 September 1999 Abstract Damage of metals due to the in¯uence of hydrogen and to stress corrosion cracking is quite frequent and leads to dangerous failures as well as to loss of property and large compensational payments by insurance companies. One reason for this, is that some designers and engineers seem to lack sucient knowledge of the basic mechanisms of these phenomena and accordingly often have only vague ideas how to prevent such failure causes. Although the basic concepts can be found in a number of good text books it seems worthwile to recall them in a short comprehensive paper. 7 2000 Elsevier Science Ltd. All rights reserved. Keywords: Embrittlement; Environmental interaction; Hydrogen-assisted cracking; Stress corrosion cracking 1. Introduction A previous survey [1] has shown that approximately one third of all failure cases are caused by environmental eects like corrosion. This failure cause means more than simple rusting of iron and steel as is shown in this paper. Whereas this kind of corrosion is visible and thus can be easily detected, the damage caused by the phenomena discussed in this paper is normally invisible and unforeseeable and therefore much more dangerous. A ®rst example is the failure of a storage tank for compressed hydrogen. The consequences of this can be ascertained from Fig. 1. This failure was caused by the growth of large fatigue cracks which was induced by hydrogen in¯uence. The total damage paid by insurance in this case was approximately US$50 million. Hydrogen damage is more frequent than many people would suspect. Another important source of failure is stress corrosion. In this failure mechanism the damage is produced by simultaneous action of stress, corrosive substance and the properties of the material. An * Corresponding author. Tel.: +41-1-823-5511; fax: +41-1-823-4014. E-mail address: [email protected] (R. Kieselbach). 1350-6307/00/$ - see front matter 7 2000 Elsevier Science Ltd. All rights reserved. PII: S1350-6307(99)00033-3 428 J. Woodtli, R. Kieselbach / Engineering Failure Analysis 7 (2000) 427±450 example of a failure caused by stress corrosion cracking was the accident at the Uster indoor swimming pool in Switzerland. There, a dead concrete ceiling had been suspended over the pool by a great number of bars made from stainless steel (AISI 304, DIN 1.4301). After several years' service some of these bars broke, the roof collapsed and 15 swimmers were killed. The investigation showed that the stainless steel had been severely corroded (Fig. 2). By detailed metallurgical tests it was proven that the failure had been brought about by stress corrosion cracking. A typical indication for this kind of damage is the branched cracks of Fig. 3. Material damage due to hydrogen embrittlement and stress corrosion cracking can be classed as cases which cannot be clari®ed based on mechanical parameters alone. Both types of damage are caused by the ambient medium and are therefore controlled by physical, chemical or electromechanical processes. The appearance of the damage is also similar: in both cases delayed low ductility fractures or cracks appear and the material is embrittled only locally in locations where contact has occurred with the damaging medium. The role of hydrogen in the mechanism of stress corrosion cracking has been known since the 1970s so that preventative measures have since been introduced. Although hydrogen-induced cracking and stress corrosion cracking are similar phenomena, both types of damage are usually described and treated separately. The reason for this is the complexity of the damage mechanism which is dependent on the particular material and damaging medium. In some cases a combination of both mechanisms can be found which is then called hydrogen-induced stress corrosion cracking. The following paragraphs deal with this subject from a failure analysis point of view. 2. Hydrogen damage 2.1. General aspects Hydrogen embrittlement is usually understood as the unwanted delayed brittleness of a material Fig. 1. Factory after rupture and explosion of a storage tank for hydrogen. J. Woodtli, R. Kieselbach / Engineering Failure Analysis 7 (2000) 427±450 429 Fig. 2. Fracture surface of broken hanger of dead concrete roof, made from stainless steel. Fig. 3. Branched cracks of stainless steel bar of Fig. 2. 430 J. Woodtli, R. Kieselbach / Engineering Failure Analysis 7 (2000) 427±450 which is caused by the presence of hydrogen within the material. Practically all metal materials can be damaged by the absorption of hydrogen, if a sucient quantity can penetrate into the material. The sources of the hydrogen, the paths it takes to enter the material and the embrittlement mechanisms are extremely diverse. These factors must therefore be established in each particular case. Only then can preventative measures be taken at the correct location or during the correct stage of a process. The aim of this paper is to explain both the embrittlement mechanisms and the characteristic visible forms of the damage. These are illustrated by individual examples. For the failure analysis and the resulting preventative measures the following aspects of hydrogen embrittlement need to be understood: . the source of the hydrogen; . the absorption of the hydrogen into the metal; . transport processes; . the embrittlement mechanism and visual appearance. 2.2. Source of the hydrogen Hydrogen always enters metals as exogenous contamination. A component or system can be contaminated by hydrogen in various stages of its useful life. This begins in the metallurgical process [4], because the hydrogen solubility in the molten metal is much higher than when it is in the solid condition (see Fig. 4). This hydrogen loading is reversible to a great extent, because it is caused mainly by the storage of the hydrogen in the interstitial positions of the lattice. Irreversible damage only occurs if the hydrogen can euse or if it can accumulate as gas in the hollow spaces. This type of hydrogen damage is of importance in welding practice and is exhibited for instance in the development of cold cracks or ®sh eyes (or ¯akes). This type of damage is also produced during casting. Another source of hydrogen during the manufacturing process is the galvanising process or ¯ash pickling. The hydrogen is produced by the cathodic partial reaction of the electromechanical processes which is why the damage caused is designated as electromechanical induced hydrogen cracking. At ®rst the hydrogen diuses in the material (Fig. 5) and is then taken up into traps. In relatively soft steel or aluminium alloys, the hydrogen can recombine to form gas molecules on internal defects such as non- metallic inclusions. Due to the high gas pressure [2] separations are produced parallel to the surface (bubble formation). In Fig. 6 the fracture surface of a tensile specimen is illustrated in which a large number of ®sh eyes can be detected. The fracture happened during a tensile test which had a reduced tensile strength from 487 to 529 N/mm2 (speci®ed value: 540 N/mm2) (Fig. 7). The hydrogen, which can be recognised fractographically from the cleavage aureole around the pores and the non-metallic inclusions, originated from humid feed material or badly dried oven lining. The greater the number of pores within the casting, the greater the amount of enclosed hydrogen (see Fig. 8). This type of hydrogen embrittlement is also called internal hydrogen embrittlement and is explained by the pressure theory based on thermodynamic principles. The equation for the balance between the atomic and gaseous hydrogen is: p c 135 p 6500=RT, 1 H H2 where c is the hydrogen concentration in ppm and p the hydrogen pressure in MPa in the solid H H2 phase of the adjacent gas phase. R is the gas constant and T is the absolute temperature. Accordingly, 1 ppm of dissolved hydrogen is balanced by gaseous hydrogen at room temperature and at a pressure of 2 Â 105 MPa. The embrittlement is due to the fact that the excess dissolved hydrogen disperses into inclusions, pores or microcracks and, because of the high pressure (e.g. in the form of blistering ¯akes) J. Woodtli, R. Kieselbach / Engineering Failure Analysis 7 (2000) 427±450 431 or under external forces, results in cracks to the lattice. Even when it is considered that for kinetic reasons the actual pressures reached are one or two times lower, there would still be considerable pressure which could have an impact on the lattice. High tensile strength and cold drawn steels with apparent elasticity limits exceeding 650 N/mm2 are at particular risk. The embrittlement is approximately proportional to the logarithm of the hardness and in addition is related to the value of the diusion coecient for hydrogen (see Fig. 9) [3]. Martensitic structures are considerably more susceptible than bainitic structures, ferrite, austenite or precipitation-hardened steels. Moreover, coarse grained materials are more susceptible to brittleness than ®ne. In steel, the diusible hydrogen should be forced out during the surface treatment between 190 and 2208C [9] because the eusion rate is far too low at room temperature (see Fig. 10). Fig. 4. Solubility of hydrogen in iron as a function of temperature and of pressure. 432 J. Woodtli, R. Kieselbach / Engineering Failure Analysis 7 (2000) 427±450 Fig. 5. Coecient of diusion for hydrogen in ferrite (F) and austenite (A) respectively; Lattice diusion (G) [3]. J. Woodtli, R. Kieselbach / Engineering Failure Analysis 7 (2000) 427±450 433 Fig. 6. Fish eyes on the fracture surface. Fig. 11 shows blistering phenomena on a galvanised steel surface (unalloyed carbon steel tempered to 460 HV5).
Details
-
File Typepdf
-
Upload Time-
-
Content LanguagesEnglish
-
Upload UserAnonymous/Not logged-in
-
File Pages24 Page
-
File Size-