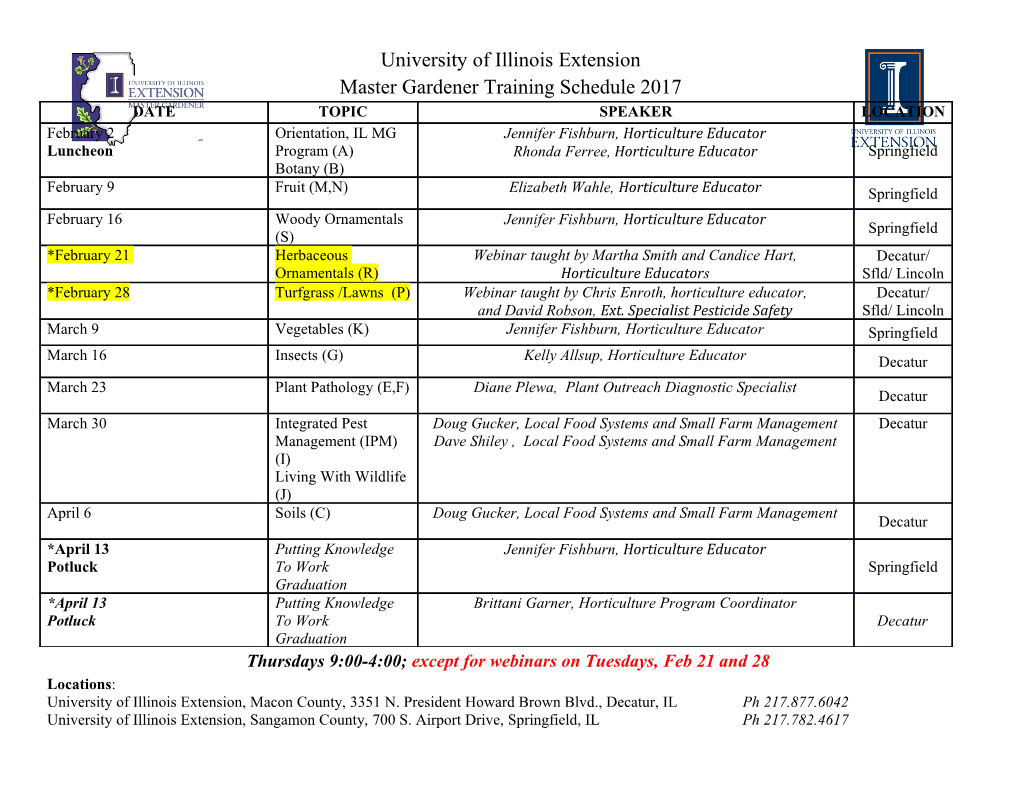
The Pennsylvania State University The Graduate School College of Engineering RESEARCH ON LOW FREQUENCY COMPOSITE TRANSDUCERS FABRICATED USING A SOL-GEL SPRAY-ON METHOD A Thesis in Engineering Science by Robert L. Cyphers c 2012 Robert L. Cyphers Submitted in Partial Fulfillment of the Requirements for the Degree of Master of Science December 2012 The thesis of Robert L. Cyphers was reviewed and approved∗ by the following: Bernhard R. Tittmann Schell Professor of Engineering Science and Mechanics Thesis Advisor Clifford Lissenden Professor of Engineering Science and Mechanics Mark W. Horn Professor of Engineering Science and Mechanics Judith A. Todd Professor of Engineering Science and Mechanics // P. B. Breneman Department Head Head of the Department of Engineering Science and Mechanics ∗Signatures are on file in the Graduate School. Abstract Ultrasonic nondestructive evaluation is currently used in countless applications to maintain a system's operational integrity. Piezoelectric transducers are the devices commonly used in this field to search for defects. A sol-gel fabrication method utilizing a spray-on deposition method has proven to produce ultrasonic transducers useful in harsh environments. This procedure produces thin film transducers, which adhere directly to a substrate making it favorable in use with irregular surface geometries. These transducers operate at relatively high frequencies due to their minute thickness. The objective of this research is to investigate the ability for low frequency operation into the low kilohertz range. Depositing thicker layers of piezoelectric composites, including bismuth titanate and lead zirconate titanate, led to adhesion problems between the metal substrates and ceramic material. Delamination of the piezoelectric elements was determined to be caused by a large mismatch in thermal expansion coefficients. Adaptations were made to the stainless steel substrates being used in order to overcome this problem. Additionally, invar substrates were used to greatly decrease the mismatch in thermal expansion coefficients between the substrate and ceramic composite. Fabricated samples were found to operate efficiently as longitudinal transducers at frequen- cies well into the low kilohertz range. Transducers were tested in modes of pulse-echo and through-transmission, acting as both the transmitter and receiver. The results presented in this thesis show that sol-gel spray-on fabricated transducers have the ability to operate effectively at frequencies as low as 250 kHz. iii Table of Contents List of Figures vi List of Tables viii Acknowledgments ix Chapter 1 Introduction 1 1.1 Introduction to Piezoelectricity . 1 1.2 Temperature Dependence and Electric Domains . 3 1.3 Linear Theory of Piezoelectricity . 5 1.4 Lead Zirconate Titanate . 6 1.5 Bismuth Titanate . 8 1.6 Sintering . 10 1.6.1 Sintering Techniques . 11 1.7 Thesis Objectives and Outline . 13 Chapter 2 Sol-gel Fabrication 14 2.1 Introduction to the Sol-gel Procedure . 14 2.2 Fabrication Process . 15 2.2.1 Sample Preparation . 16 2.2.2 Bismuth Titanate/Bismuth Titanate . 16 2.2.3 PZT/Bismuth Titanate . 19 2.2.4 Sintering . 21 2.2.5 Electrodes and Poling . 22 Chapter 3 Previous Work 24 Chapter 4 Low Frequency Ultrasonic Transducers 28 4.1 Thickness Dependence . 28 4.2 Initial Testing . 29 iv 4.3 Adhesion Difficulties and Solutions . 31 4.4 Thermal Expansion . 32 4.5 Attempts of Solving Adhesion Problem . 34 4.5.1 Matching Layer . 35 4.5.2 Flat-Bottom Well Samples . 36 4.6 Shallow Well Samples . 37 4.6.1 Low Frequency Testing of the Shallow Well Transducers . 41 4.7 Conclusions . 45 Chapter 5 Invar 46 5.1 The Invar Anomaly . 46 5.2 Invar Substrates . 48 5.3 FFT Analysis . 55 Chapter 6 Conclusions 58 6.1 Results . 58 6.2 Recommendations for Future Work . 59 Bibliography 61 v List of Figures 1.1 Two-dimensional representation of bismuth titanate (Bi4T i3O12) single domain; (a) unstrained and (b) under a tensile load. Figure adapted from [1]. 2 1.2 Illustration of a transducer operating in pulse-echo mode. Point 1 represents the launching of the ultrasonic wave and point 2 is its reflection. 3 1.3 (a) Polycrystalline material before poling, the arrows show the random orientation of electric domains within the material. (b) A large electric field is applied to the material at an elevated temperature and held as it cools. (c) Cooled material with resulting net polarization. Illustration from [2]. 4 1.4 Perovskite crystal structure of PZT below its Curie-Weiss temperature. Adapted from [3]. 6 1.5 Phase diagram of PZT [4]. 7 1.6 Dependence of several d constants on Zr composition near the MPB [4]. 8 1.7 Crystal Structure of bismuth titante (Bi4T i3O12) [5]. 9 1.8 The effects of the sintering process [4]. 10 2.1 Spray gun used during deposition. 17 2.2 General fabrication procedure for sol-gel spray-on Bi4T i3O12=Bi4T i3O12 trans- ducers. 18 2.3 Ultrasonic horn used to mix the sol-gel material in this procedure. 19 2.4 Generalized fabrication procedure for sol-gel spray-on P ZT=Bi4T i3O12 transducers. 20 2.5 Sintering samples with the blowtorch. 22 2.6 Oil Bath Poling Unit. 23 3.1 Comparison of samples sintered using microwaves, (a) and (b), and samples sin- tered with a blowtorch, (c) and (d) [6]. 25 3.2 P ZT=Bi4T i3O12 transducer operating in pulse-echo mode [7]. 26 3.3 Bi4T i3O12=Bi4T i3O12 transducer's first echo signal amplitude over a range of temperatures [7]. 26 3.4 P ZT=Bi4T i3O12 transducer's first echo signal amplitude over a range of temper- atures [7]. 27 4.1 Ten spray Bi4T i3O12=Bi4T i3O12 transducer pulsed at 2.25 MHz. 30 4.2 Ten spray Bi4T i3O12=Bi4T i3O12 transducer pulsed at 1.80 MHz. 31 4.3 Two examples of Bi4T i3O12=Bi4T i3O12 which experienced total delamination post-sintering. 31 4.4 A P ZT=Bi4T i3O12 which experienced cracking delamination during sintering. 32 4.5 Thermal expansion of bismuth titanate over a range of temperatures [8]. 35 vi 4.6 Thermal expansion of PZT over a range of temperatures [9]. 35 4.7 Flat-bottom well designed Bi4T i3O12=Bi4T i3O12 transducer . 36 4.8 Illustration of the shallow well design substrate. 38 4.9 Images of the fabricated Bi4T i3O12=Bi4T i3O12 shallow well sample. 38 4.10 Images of the fabricated P ZT=Bi4T i3O12 shallow well sample. 39 4.11 The top two images are the waveform at center frequency and a plot of sig- nal amplitude of the first back wall reflection as a function of frequency for the Bi4T i3O12=Bi4T i3O12 transducer. The bottom two are the same for the P ZT=Bi4T i3O12 transducer. 40 4.12 P ZT=Bi4T i3O12 shallow well transducer operating in pulse-echo mode at 550 kHz. 41 4.13 P ZT=Bi4T i3O12 shallow well transducer coupled to an added length of stainless steel. 42 4.14 Waveform of the P ZT=Bi4T i3O12 shallow well transducer coupled to an added length of stainless steel operating in pulse-echo mode at 500 kHz. 43 4.15 Waveform of the P ZT=Bi4T i3O12 shallow well transducer operating as the re- ceiver in through-transmission at 500 kHz. 44 4.16 Waveform of the P ZT=Bi4T i3O12 shallow well transducer operating as the re- ceiver in through-transmission at 250 kHz. 44 5.1 Illustration of the \invar effect.” The dashed line represents the thermal expansion of normal metal alloys, whereas the solid line represents that of invar. The differ- ence between the two curves represents the spontaneous volume magnetostriction [10]. 47 5.2 Image of P ZT=Bi4T i3O12 on invar substrate. 49 5.3 Waveform of P ZT=Bi4T i3O12 transducer on invar substrate operating in pulse- echo mode at its center frequency. 50 5.4 Frequency sweep of P ZT=Bi4T i3O12 transducer on invar substrate operating in pulse-echo mode. 51 5.5 Waveform of P ZT=Bi4T i3O12 transducer on invar substrate operating in pulse- echo at 600 kHz. 52 5.6 Waveform of P ZT=Bi4T i3O12 transducer on invar substrate operating in pulse- echo at 250 kHz. 53 5.7 The top images are the waveforms captured of the P ZT=Bi4T i3O12 transducer on an invar substrate acting as the receiver/transmitter in through-transmission at 500 kHz. The bottom are the same, but operating at 250 kHz. 54 5.8 FFT of the P ZT=Bi4T i3O12 transducer on an invar substrate operating at its center frequency of 1.1 MHz. 55 5.9 The image on the left shows the frequency spectrum for the P ZT=Bi4T i3O12 transducer on an invar substrate pulsed at 600kHz. The image on the left shows the same pulsed at 250 kHz. 56 5.10 The top two images are the frequency spectrums associated with the waveforms captured of the P ZT=Bi4T i3O12 transducer on an invar substrate acting as the receiver/transmitter in through-transmission at 500 kHz. The bottom two are the same, but operating at 250 kHz. 57 vii List of Tables 1.1 Curie-Weiss Temperatures for Several Materials [2] . 4 1.2 Electrical and Mechanical Properties of PZT Ceramic [11]. 8 4.1 Measured piezoelectric properties of fabricated shallow well transducers. 39 5.1 Linear Thermal Expansion Coefficients of Invar and Stainless Steel [12]. 48 5.2 Measurements of d33 and capacitance of the P ZT=Bi4T i3O12 on invar substrates. 49 viii Acknowledgments I would like to thank my father Bob, and my mother Pam, for all of their support, in all forms, throughout my academic career, especially the past year and a half.
Details
-
File Typepdf
-
Upload Time-
-
Content LanguagesEnglish
-
Upload UserAnonymous/Not logged-in
-
File Pages71 Page
-
File Size-