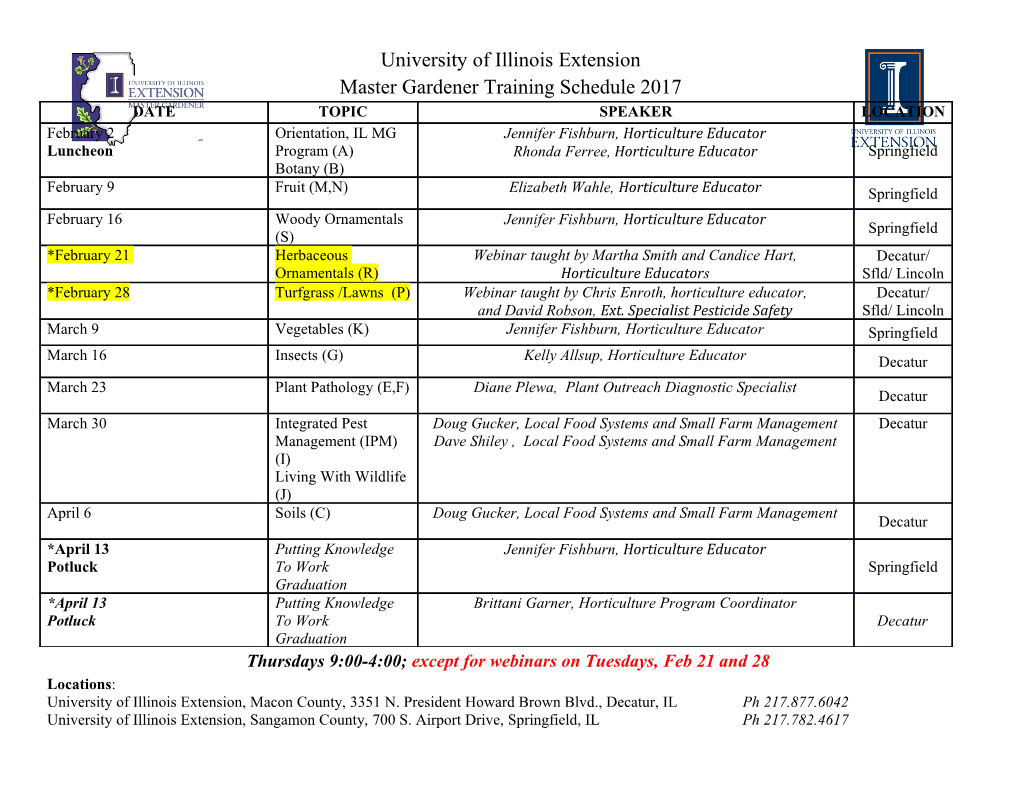
379 A/g/J /i0.7k~n<\ MODEL DEVELOPMENT FOR THE CATALYTIC/CALCINATION OF CALCIUM CARBONATE DISSERTATION Presented to the Graduate Council of the North Texas State University in Partial Fulfillment of the Requirements For the Degree of DOCTOR OF PHILOSOPHY By Jin-Mo Huang Denton, Texas December, 1987 Huang, Jin-Mo, Model Development for the Catalytic Calcination of Calcium Carbonate. Doctor of Philosophy (Analytical Chemistry), December, 1987, 88 pp., 25 tables, 18 figures, bibliography, 60 titles. Lime is one of the largest manufactured chemicals in the United States. The conversion of calcium carbonate into calcium oxide is an endothermic reaction and requires approximately two to four times the theoretical quantity of energy predicted from thermodynamic analysis. With the skyrocketing costs of fossil fuels, how to decrease the energy consumption in the calcination process has become a very important problem in the lime industry. In the present study, many chemicals including lithium carbonate, sodium carbonate, potassium carbonate, lithium chloride, magnesium chloride, and calcium chloride have been proved to be the catalysts to enhance the calcination rate of calcium carbonate. By mixing these chemicals with pure calcium carbonate, these additives can increase the calcination rate of calcium carbonate at constant temperatures; also, they can complete the calcination of calcium carbonate at relatively low temperatures. As a result, the energy required for the calcination of calcium carbonate can be decreased. The present study has aimed at developing a physical model, which is called the extended shell model, to explain the results of the catalytic calcination. In this model, heat transfer and mass transfer are two main factors used to predict the calcination rate of calcium carbonate. By using the extended shell model, not only the catalytic calcination but also the inhibitive calcination of calcium carbonate have been explained. TABLE OF CONTENTS PAGE LIST OF TABLES iv LIST OF ILLUSTRATIONS vi Chapter I. GENERAL INTRODUCTION 1 II. DETAILS OF THE RESEARCH 17 III. CATALYTIC EFFECT OF ALKALI CARBONATES ON THE CALCINATION OF CALCIUM CARBONATE 48 IV. LITHIUM CARBONATE ENHANCEMENT OF THE CALCINATION OF CALCIUM CARBONATE PROPOSED EXTENDED SHELL MODEL 61 V. INHIBITION OF THE CALCINATION OF CALCIUM CARBONATE 75 APPENDIX 83 BIBLIOGRAPHY 85 ill LIST OF TABLES Table Page I. Various Forms Of CaC03 20 II. Melting Temperatures Of Li2C03, Na2C03, K2C03> MgCO 3, And CaC03 26 III. Fluctuation Of Calcination Rates Of Pure CaC03 Due To Temperature Variation In Heating Chamber Of Lindberg Furnace At 800 °C 31 IV. Variance Of Calcination Rates Of Pure CaC03 At A Fixed Position In Heating Chamber Of Lindberg Furnace At 800 °C... 33 V. Calcination Rates Of Pure CaC03 (As Blank) From Eight Different Sample Runs From Lindberg Furnace At 800 °C 34 VI. .Calcination Rates Of Using Fused Salts As Catalysts From Lindberg Furnace At 800 °C 35 VII. Calcination Rates Of Using Some Chemicals As Catalysts From Lindberg Furnace At 800 oc 35 VIII. Calcination Rates Of Pure CaC03 At Different Temperatures From DTA-TGA Analyzer At 700 °C 38 IX. Some Catalytic Calcination Results From DTA-TGA Analyzer At 700 °C 41 X. Precision Of DTA-TGA Technique 42 XI. Transition Temperatures Of Some Chelating Agents 43 XII. Calcination Rates Of Alkali Carbonate- CaC03 Mixtures From Lindberg Furnace At 800 °C 51 XIII. Calcination Rates Of Alkali Carbonate- CaC03 Mixtures From DTA-TGA Analyzer At 700 °C . 52 IV LIST OF TABLES Continued Table Page XIV. Transition Temperatures Of Alkali Carbonate-CaC03 Mixtures From DTA Curve 55 XV. Calcination Rates Of Pure CaC03 And Pure Na2C03 From DTA-TGA Analyzer 57 XVI. Melting Temperatures Of Alkali Carbonates And Pure CaC03 58 XVII. Calcination Rates Of Usng Li2C03 As Catalyst From Lindberg Furnace At 800 oc 64 XVIII. Calcination Rates Of Using Li2C03 As Catalyst From DTA-TGA Analyzer At 700 °C 65 XIX. Transition Temperatures Of Li2C03-CaC03 Mixtures From DTA Curve 68 XX. Calcination Rates Of CaC03 At Different Temperatures From DTA-TGA Analyzer 71 XXI. Melting Temperatures Of MgCl2 And CaCl2.... 72 XXII. Calcination Rates Of 5% MgCl2 And 5% CaCl2 In CaC03 From DTA-TGA Analyzer At 700 °C 73 XXIII. Calcination Rates Of Additive-CaC03 Mixtures From DTA-TGA Analyzer At 700 °C 78 XXIV. Transition Temperatures Of Additive-CaC03 Mixtures From DTA Curve 79 XXV. Melting Temperatures Of Additives 80 LIST OF ILLUSTRATIONS Figure Page 1. The structure of CaC03 1 2. Influence of C02 concentration and pressure on dissociation temperature of CaC03.... 3 3. Decomposition of a sphere of CaC03 (shell model) 5 4. A reflux reactor 12 5. Block diagram for the Norelco x-ray diffraction unit 22 6. X-ray diffraction pattern of fused material of Na2C03-CaC03 salt 28 7. X-ray diffraction pattern of unfused material of Na2C03-CaC03 salt 29 8. A fixed position in heating chamber of Lindberg furnace to produce reliable results 32 9. Typical thermogram used for the calculation of calcination rate 37 10. A typical thermogram used for the determination of transition temperature. 39 11. Calcination rates of pure CaC03 vs. temperatures from DTA-TGA analyzer 40 12. The extended shell model 46 13. Calcination rate vs. alkali carbonates from Lindberg furnace 53 14. Calcination rate vs. alkali carbonates from DTA-TGA analyzer at 700 °C 54 15. Transition temperature vs. alkali carbonate-calcium carbonate mixtures.... 56 vi LIST OF ILLUSTRATIONS Continued Figure page 16. Calcination rate vs. Li2C03 concentration from Lindberg furnace at 800 °C 66 17. Calcination rate vs. Li2C03 concentration from DTA-TGA analyzer at 700 °C 67 18. Transition temperature vs. Li2C03 concentration 69 VII CHAPTER I GENERAL INTRODUCTION Theory of Calcination Calcium carbonate (CaC03) has the structure shown in Figure 1. During calcination or thermal decomposition of CaC03 a carbon-to-oxygen bond and a calcium-to-oxygen bond are broken. Carbon dioxide (C02) is evolved, and calcium oxide (CaO) remains. Because there is only bond breakage, and no bond formation, the calcination process is an endothermic reaction. \ / 9 \ /9 \ , Lc. \ L, \ o*^ o! O' / A >cax \ / <* \ / X 7 x / Figure 1. The structure of CaC03 The measurements of the dissociation pressures of CaC03 have been made through a range of temperatures by Debray (1), Le Chatelier (2), Brill (3), Pott (4), Zavriev (5), and Riesenfeld (6). Riesenfeld showed that the possibility of formation of a solid solution of CaO in the CaC03 and vice versa is practically excluded. It is, therefore, proved that the dissociation of CaC03 proceeds according to the following reaction only: A N CaC03(s) ^ CaO(s) + C02(g) Johnson (7) showed that for a number of heterogeneous equilibria similar to the dissociation of CaC03, the dissociation pressure is connected with the heat of reaction, AH, and the dissociation temperature, T, by the following equation: AH log P = 4.576 T 4.576 J is the thermodynamically indeterminate constant. Actually, the dissociation temperatures are not rigid values since they vary with the counteracting C02 pressure and concentration, as shown in Figure 2 (8). If the temperature and pressure are in equilibrium, regardless of their values, dissociation is static. But if there is a minute change in one of these variables, such as a decrease in C02 pressure or concentration or an increase in temperature, dissociation immediately proceeds with evolution of C02 gas and the simultaneous formation of CaO. 760 690 ^3 610 P | 532 E» O 454 CO E E 380 § 310 ifi £ 2281 a. 152 77 740 780 820 860 900 Temperature, *C Ficfu^© 2. Influence of C02 concentration and pressure on dissociation temperature of CaC03. This means that if the dissociation pressure of CaC03 is only 380 nun Hg, corresponding to 50% C02 concentration, then the dissociation temperature is reduced to 848 °C. In all cases there is a definite relationship between C02 pressure, and dissociation temperature. The dissociation always proceeds gradually from the outside surface inward. Usually the depth of penetration moves uniformly inward on all sides of the particle, like a growing veneer or shell. That means that at a given instant the central core is undecomposed CaC03 and the outer shell is CaO. So, Furnas (9) and others have suggested the shell model (Figure 3) for the decomposition of CaC03. Theoretically, the calcination rate is determined by the interrelationships between three major rate processes: (1) Heat Transfer Heat must first be transferred to the surface of the mass and then through the outer layer of CaO to the reaction zone. Haslam and Smith (10) have treated the calcination as a problem of the heat transfer alone. (2) Mass Transfer The C02 released at the reaction zone must escape through the outer shell of CaO. Consequently, at finite rates of decomposition the pressure at the reaction zone must be greater than that at the surface of the sphere. The increase in pressure requires an increase in the temperature HEAT IN REACTION CARBON ZONE DIOXIDE OUT Figure 3. Decomposition of a sphere of CaCO, (shell model). of the reaction zone to maintain decomposition. According to Le Chatelier's principle, the quick removal of C02 will speed the calcination. (3) Chemical Reaction A considerable number of studies for the calcination of CaC03 have been reported (11,12,13,14). According to their reports, the experimental results have usually been treated as though chemical kinetics is the only rate-limiting step. Actually, the reported data of the activation energy for the reaction varied greatly, from 35.5 to 50.1 Kcal/mol (12,13,14,15). Statement of the Problem Lime (CaO) is considered to be one of the oldest materials known to mankind. It is certain that the Egyptians used lime and limestone in building the pyramids between 4000 and 2000 B.C.
Details
-
File Typepdf
-
Upload Time-
-
Content LanguagesEnglish
-
Upload UserAnonymous/Not logged-in
-
File Pages96 Page
-
File Size-