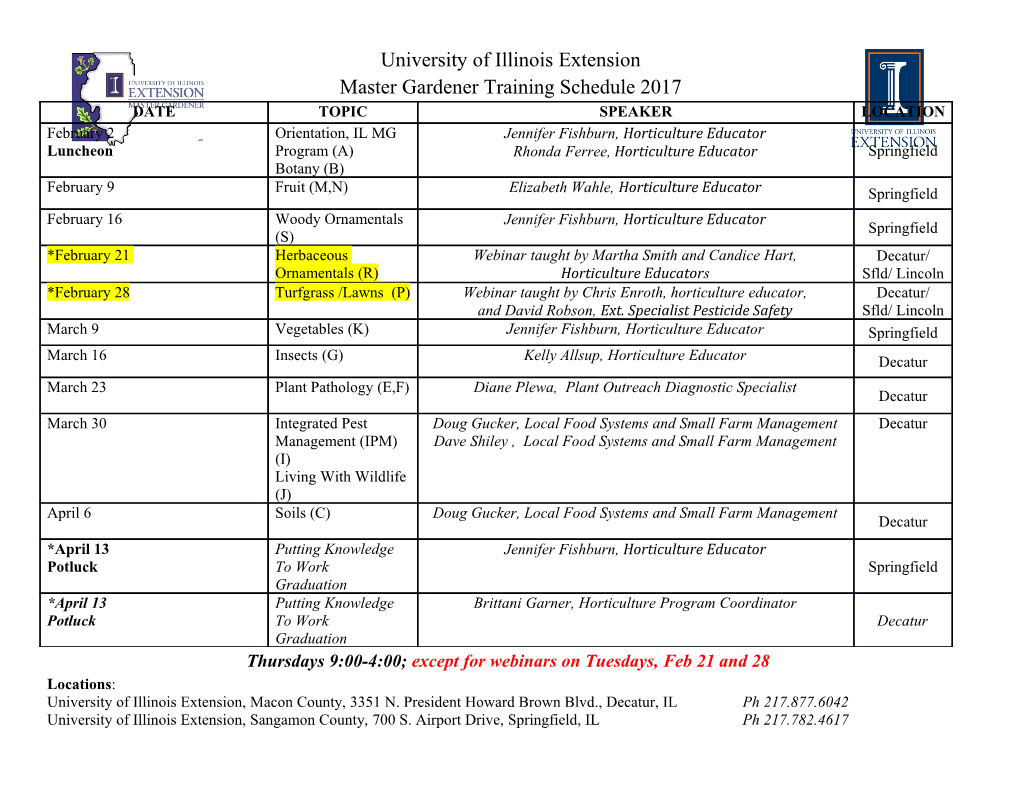
Ruthenium Melt Catalysis PRODUCING CHEMICALS FROM SYNTHESIS GAS By John F. Knifton Texaco Chemical Company, Austin, Texas A range of commodity chemicals and fuels can be generated directly from synthesis gas by ruthenium melt catalysis. Careful selection of the catalyst components enables a wide range of oxygenates to be produced, while other advantages of this flexible process include high productivity and the ease with which the products may be recovered and the catalyst recycled. In platinum-metal catalysed organic syn- present a renewable surface may avoid many of thesis, the primary purpose is to produce pure the problems of deactivation seen with con- products in high yields, with good ventional heterogeneous catalysts (4). reproducibility and ease of product isolation. Frequently, the melt is called upon to play While both homogeneous and heterogeneous more than one role in a chemical process. It catalysis systems may fulfill these roles in may, for example, simply act as a solvent for laboratory or industrial processes, an alterna- reactants and products; it may be a catalyst; it tive approach, that has many of the inherent may supply one or more of the reactants, as well advantages of both systems, is the use of molten as aid in controlling the heat of reaction. The salts as catalyst and/or reaction media. salts may be used singly (for example molten Molten salts may be classified into simple Na2C03, ZnCL or AlC13), or as eutectic ionic salts (for example the alkali and alkaline mixtures (such as Li2C03-Na2C03-K2C03, earth metal halides), simple and polymeric CuC1-CuCl2-KC1, and AlC13-BuPyC1) where oxyanionic salts (such as metal nitrates, car- the lower liquidus temperatures may be bonates, phosphates, borates), and salts contain- advantageous. ing organic cations and/or anions (including the Molten salts have already found numerous quaternary phosphonium and ammonium salts) technical applications in industrial catalytic (I). The high thermal stability of many of these processes. Examples include the Transcat, melts, together with their low vapour pressure, Deacon and SO2 oxidation processes (I ,2). The good thermal and electrical conductivity, and literature illustrating the diverse uses of melt low viscosity provides them with a range of catalysis with the platinum group metals important physical and chemical advantages includes applications in chlorination (z), oxida- over conventional homogeneous and tion (5) and selective hydrogenation (6) process- heterogeneous catalyst systems (2). Molten ing, as in Equation i: salts, such as the quaternary phosphonium n salts, dissolve a broad range of metals, oxides and complexes; high reaction rates and yields are often possible (for example organic syn- U theses in molten tetrachloroaluminate solvents In the case of synthesis gas (carbon (3) and fused alkali metal salts (4)) with ease of monoxide/hydrogen) chemistry, Fischer- producdcatalyst separation and recovery. Tropsch production using Ir4(C0)12dissolved Where chemical synthesis occurs at a melt-gas in NaC1-AlC13 melts has now been demons- interface, as in gas reactions, the ability to trated (7); ethane is the major product fraction, Platinum Metals Rev., 1985,29, (2), 63-72 63 see Equation ii or, under flow conditions, ease of product-catalyst separation, typical of isobutane and propane. A further examination, heterogeneous catalyst systems, once the reac- by Collman and his colleagues, implicates tion is complete. chloromethane (or methanol) as the primary Optionally, a second or third transition metal intermediate, with methane, ethane, and may be added to the ruthenium to further chloromethane the major carbon-containing modify its performance and to steer the product products (8). distribution toward specific aliphatic CO + 3H2 ->C~HL (major) + CH4 + oxygenates. These modifiers may be derivatives C3Hs (tr) + C4Hlo (tr) ii of rhodium, cobalt, manganese, rhenium, Ruthenium Melt Catalysis zirconium and titanium, in either halogen-free In other, potentially far-reaching applica- or halogen-containing forms. tions of melt catalysis by the platinum group Some specific applications of this technology metals, we at Texaco have demonstrated the include (Equations iii to viii): synthesis of a range of commodity chemicals [I] Ethylene glycol synthesis directly from and fuels directly from synthesis gas by the use synthesis gas using ruthenium-rhodium catalysts of ruthenium-containing molten salt catalysis. or ruthenium alone (9). Products include ethylene glycol, C1-C4 [2] C1-G AlcohoVacetate ester fuel alcohols, acetic acid, acetate esters, C2+ olefins products, which are potential octane enhancers, and vicinal glycol esters. In its simplest form, using ruthenium in combination with cobalt, this new class of melt catalyst comprises one or titanium or zirconium (I 0). more ruthenium sources, including ruthenium [3] Selective methanol production with the carbonyls, oxides and complexes dispersed in a lowmelting (m.p. <I 50°C) quarternary phosphonium or ammonium salt, for example tetrabutylphosphonium bromide. The key components are selected such that: U [A] The catalyst mix is a solid under ambient conditions. mole) m ( [B] The quarternary salt melts below the m temperatures of carbon monoxide hydrogena- tion so that, under typical operating conditions, ln it is a highly polar, non-volatile, liquid media PRODUCTIVITY that readily solubilises the ruthenium catalyst A precursor and the synthesis gas components, thereby ensuring rapid rates of carbon ETHERS, monoxide hydrogenation to the desired ali- phatic oxygenates. *GLYCOL [C] Optionally, upon cooling, the N rutheniumquarternary salt may resolidify, GLYCOL allowing ease of separation of the liquid organic - products from the solid inorganic catalyst com- ponents by decantation or distillation. ETHYLENE 05 1.0 15 20 The melt catalyst enjoys, thereby, certain of RHODIUM OR RUTHENIUM CONTENT (m mole) Fig. 1 Ethylene glycol synthesis from the intrinsic advantages of both homogeneous synthesis gas showing the effect on and heterogeneous systems; the inherent high productivity of the ruthenium-rhodium selectivity and reproducibility of liquid catalyst molar ratio homogeneous catalysts under normal carbon Effect of varying rhodium, 0; Effect of varyine ruthenium x monoxide hydrogenation conditions, and the Platinum Metals Rev., 1985,29, (2) 64 ruthenium-manganese combination (10, I I). advantages of the mixed ruthenium-rhodium [4] Acetic acid production directly from syn- system include improved glycol productivity thesis gas catalysed by halogen-promoted and ability to operate at lower synthesis gas pre- ruthenium-cobalt combinations (I I). ssures. It may be noted that (see Table I): ... (I) CH20H 111 The productivity of the ruthenium- I rhodium melt catalyst is high; liquid weight CH2OH gains may exceed 200 weight per cent (expt. 2) Ru + Rh and turnover frequencies surpass 5 x 10-7s at C.H2.+ ]OH + CnH2"+]OAc iv / 220°c. corn2 (2) Glycol : alkanol weight ratios of I : I .37 have been realised (expt. 6). (3) Both alkanol and diol products may be V readily isolated by fractional distillation of the crude liquid product and the solid residual Ru + Co + I vi yc;3cooHruthenium-rhodium catalyst recycled. Through the addition of aliphatic carboxylic The primary requirements in selecting the acid coreactants, this chemistry may be further quaternary Group VB salts (Table I) as suitable extended to: reaction media are that they be thermally stable [5] The production of vicinal glycol esters under typical carbon monoxide hydrogenation (Equation vii) (I 2). conditions and that they melt below the reaction [6] The generation of ethylene and propylene temperature (200 to 25oOC) to give stable, from synthesis gas (13) by a novel two-step highly polar, fluid media for- solubilisation of procedure involving the intermediate genera- the transition-metal component. tion of ethyl and propyl esters (Equation viii). Figure I illustrates how both the ruthenium CH200CR vii and rhodium catalyst components are beneficial to the formation of ethylene glycol, expressed here in terms of total glycol +glycol ether CO/H2 + RCOOH P200CR productivity, for the Ru(acac) ,-Rh(acac) d BuJBr catalyst precursor. Maximum glycol kCIEOOCR+ production is achieved with increasing rhodium A +C 2H 4 Vlll... addition, up to rhodium: ruthenium ratios of -+ C3H700CR C3H.5 about I:I. Very little diol is generated, however, in the absence of either the ruthenium Ethylene Glycol component (see Figure I), or the quaternary Ethylene glycol commands a 4.5 x 109 Ib/yr phosphonium salt (Table I, expt. 5). While the market in the United States of America, and presence of ruthenium is necessary to the while this largevolume petrochemical is pre- formation of glycol, the data of Figure I, sently generated entirely by ethylene oxide together with the isolation of mixed ruthenium- hydrolysis, there has been considerable research rhodium clusters such as RU~R~(CO)]~(9), activity during the past decade into alternate point to the role of the second metal, rhodium, routes to polyhydric alcohols either directly, or in providing improved diol selectivity. indirectly, from synthesis gas. We have demons- trated the preparation of ethylene glycol and its Alcohol-Ester Fuels monoalkyl ether derivatives from synthesis gas A second class of platinum metal melt (Equation iii) using ruthenium or a ruthenium- catalysts-comprising a ruthenium source, rhodium catalyst combination dispersed in a such as Ru~(CO)U,optionally in combination low-melting
Details
-
File Typepdf
-
Upload Time-
-
Content LanguagesEnglish
-
Upload UserAnonymous/Not logged-in
-
File Pages10 Page
-
File Size-