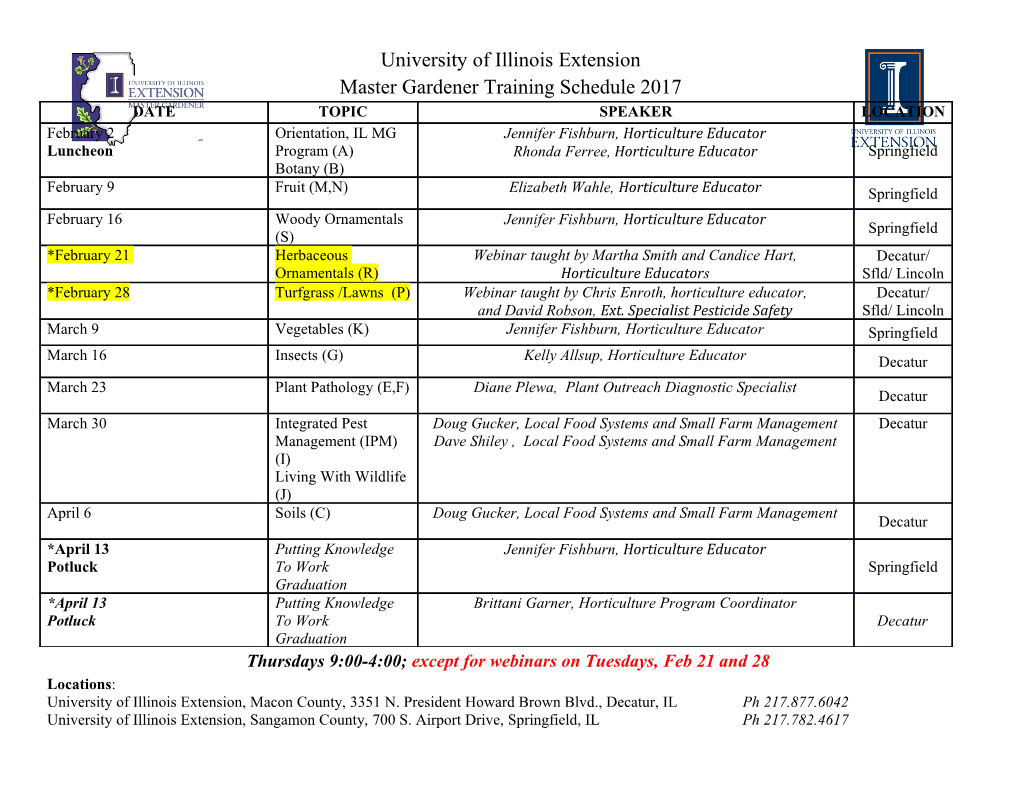
Cooling Tower Industry: Refining, Food and Beverage, Power, Oil and Gas, Pulp and Paper, Chemical Product: pH, ORP, Conductivity Background Information fluid, usually water or a glycol mixture, being cooled. Unlike The term “cooling tower” is used to describe both direct the open cooling tower, the indirect cooling tower has two (open circuit) and indirect (closed circuit) heat rejection separate fluid circuits. One is an external circuit in which equipment. Cooling towers are heat-transfer units, used to water is re-circulated on the outside of the second circuit, remove heat from any water-cooled system. The cooled which is tube bundles (closed coils) which are connected to water is then re-circulated (and thus, recycled) back into the the process for the hot fluid being cooled and returned in a system. Since the process water is re-circulated, the mineral closed circuit. Air is drawn through the re-circulating water concentration increases as a result of the evaporation. When cascading over the outside of the hot tubes, providing the water contains two times the original mineral content, it is evaporative cooling similar to an open cooling tower. said to contain two cycles of concentration. When it contains three times the original mineral content, it has three cycles of The purpose of a water treatment program is to maximize concentration and so on. The other half of the cooling loop the cycles of concentration while minimizing scaling, takes heat from the process through a heat exchanger, corrosion and microbiological growth. The most important condenser or water jacket. factor is scaling, which is typically caused by the over saturation of calcium compounds in the cooling water. Performance of this unit is critical for efficient and economical operation. The heat transfer surfaces must be kept as clean as possible to assure maximum heat transfer. Introduction As the mineral content in the cooling water increases, the While the most common usage of cooling towers has potential for scaling and corrosion increases, threatening traditionally been in the air conditioning industry, many other efficient operation of the heat exchanger. industries can benefit from cooling tower technology such as plastics, dry cleaning, manufacturing, petroleum refining, The heat transfer surface is the hottest area in contact with electrical generation. the cooling water. The solubility of calcium carbonate (CaCO3 found in cooling water) is an inverse function, with In the past, cooling was accomplished by using available respect to temperature, causing calcium carbonate scaling to water from nearby lakes, rivers or municipal systems on a occur on the heat transfer surfaces. The accumulation of a once through basis. Problems that were encountered CaCO3 scale layer reduces the heat transfer capability, included plugging of the heat exchanger by suspended causing corrosion and creating hot spots, resulting in thermal solids (slit or mud) and biological growth within the stress. All of which affect the efficiency and life span of the equipment. The expense of the equipment involved and the heat exchanger. One basic way of preventing scaling, is to increasing restrictions by the EPA, have placed a much bleed off or blowdown a fraction of recycled water and greater emphasis on the treatment and re-use of water by replace it with fresh water (make-up water) of a lower means of re-circulating cooling towers. This has significantly mineral concentration. A complete analysis of the make-up reduced industry’s demand for fresh water and the quantity water is required to determine the maximum concentration of of effluent produced. minerals that can be tolerated without causing deposits to form. Cooling Towers A direct, or open circuit cooling tower is an enclosed Cooling towers are heat-transfer units, used to remove heat structure with internal means to distribute the warm water fed from any water-cooled system. The type of heat removal in a to it over a labyrinth-like packing or "fill." The fill provides a cooling tower is termed “evaporative” in that it allows a small vastly expanded air-water interface for heating of the air and portion of the water being cooled to evaporate into a moving evaporation to take place. An indirect, or closed circuit site stream to provide significant cooling to the rest of the cooling tower involves no direct contact of the air and the water stream. The cooled water is then re-circulated (and thus, recycled) back into the system. Cooling towers may AN 10A01B20-01E http://www.yokogawa.com either use the evaporation of water to reject process heat If scale cannot be removed physically, either and cool the working fluid to near the wet-bulb air because it is difficult to get to or it is simply too temperature or rely solely on air to cool the working fluid to adherent, then acid treatment can be used. By near the dry-bulb air temperature. The wet-bulb temperature either reducing the pH of the circulating water is a type of temperature measurement that reflects the or a cleaning solution, calcium carbonate physical properties of a system with a mixture of a gas and a should loosen from PVC surfaces. vapor, usually air and water vapor. Where as the dry-bulb temperature is the temperature of air measured by a Care must be taken, not to expose galvanized thermometer freely exposed to the air but shielded from steel surfaces (if present) to acidic conditions. radiation and moisture. In construction, it is an important Galvanized steel is very sensitive to any type of consideration when designing a building for a certain climate acids. The pH of the circulating water should not fall below 6.0. If harsher or more acidic A re-circulating cooling system re-uses the same water by solutions are needed, thorough rinsing is passing it through heat exchangers, cooling canals or required to minimize any damage to galvanized cooling towers to remove the heat that has been transferred surfaces. into it from equipment or industrial processes. Re-circulating cooling towers affect cooling by evaporation of water, and II. Corrosive Salts- Evaporation is the primary also by direct heat exchange with air passing through the cooling effect of the tower, but as it occurs the tower. The basic operating principle is relatively concentration of salts in the water will increase. straightforward, but the associated heat transfer equipment Only by disposing of a percentage of the re- varies widely in both cost and complexity. circulated water and by adding fresh water to the cooling tower can the concentration of Problems encountered in cooling systems are not usually solids (TDS) be kept under corrosive limits. with the equipment, but with the water that is used, there are three problems which are common to all cooling systems: Total Dissolved Solids (TDS) are the total they are corrosion, scale and biological growth. All water amount of mobile charged ions, including contains some level of impurities which cause scale and minerals, salts or metals dissolved in a given corrosion in the heat exchanger equipment. In the tower volume of water, expressed in units of mg per itself, the combination of air and warm water provide an ideal unit volume of water (mg/L), also referred to as environment for biological growth. Dust and other particles parts per million (ppm). (dissolved solids) can also be introduced into the cooling tower depending on prevailing environmental conditions, If cooled water is returned from the cooling adding to maintenance and treatment requirements. tower to be reused, some water must be added to replace or make-up, the portion of the flow Corrosion is caused by impurities in the cooling water that evaporates. Because evaporation consists reacting with the metal in the system component. The result of pure water, the concentration of dissolved is a loss of metal which weakens piping and equipment until minerals and other solids in circulating water leaks or ruptures occur. will tend to increase unless some means of dissolved solids-control, such as blowdown, is These impurities can be categorized into two classes: provided. Therefore, a conductivity analyzer is used to control the “Blowdown Valve” in I. Scaling Impurities- Most of the impurities in conjunction with a level measurement in the cooling water are alkaline, usually in the form sump to control the make-up water flow rate. of calcium bicarbonate and magnesium bicarbonate. The higher the concentration of Corrosion can be minimized by the addition of these impurities, the higher the pH* value of a corrosion inhibitor. Which is a chemical the water will be. These impurities, especially compound that, when added in small calcium bicarbonate, are less soluble at higher concentration stops or slows down corrosion pH values. Therefore, acid (usually sulfuric) is (rust) of metals and alloys. Inhibitors are added to the circulating water to lower the pH1 chemicals that react with a metallic surface, or value and increase the solubility of the the environment this surface is exposed to, impurities so they can be removed by proper giving the surface a certain level of protection. blow down of the system. They must be This is done by relating inhibitor demand to the eliminated before they have a chance to form acid demand. Whenever the acid pump runs, scale within the cooling system. the inhibitor pump runs also. This is based upon the principle that when fresh water (make-up water with its inherent alkalinity) All Rights Reserved, Copyright © 2014, Yokogawa Corporation of America enters the system, acid is required. Inhibitor is tivity level of the impurities present exceeds a also required. The chemical relationship of a given value. This causes a demand for make- particular acid and an inhibitor determine the up water (with a lesser concentration of proper ratio to be used.
Details
-
File Typepdf
-
Upload Time-
-
Content LanguagesEnglish
-
Upload UserAnonymous/Not logged-in
-
File Pages4 Page
-
File Size-