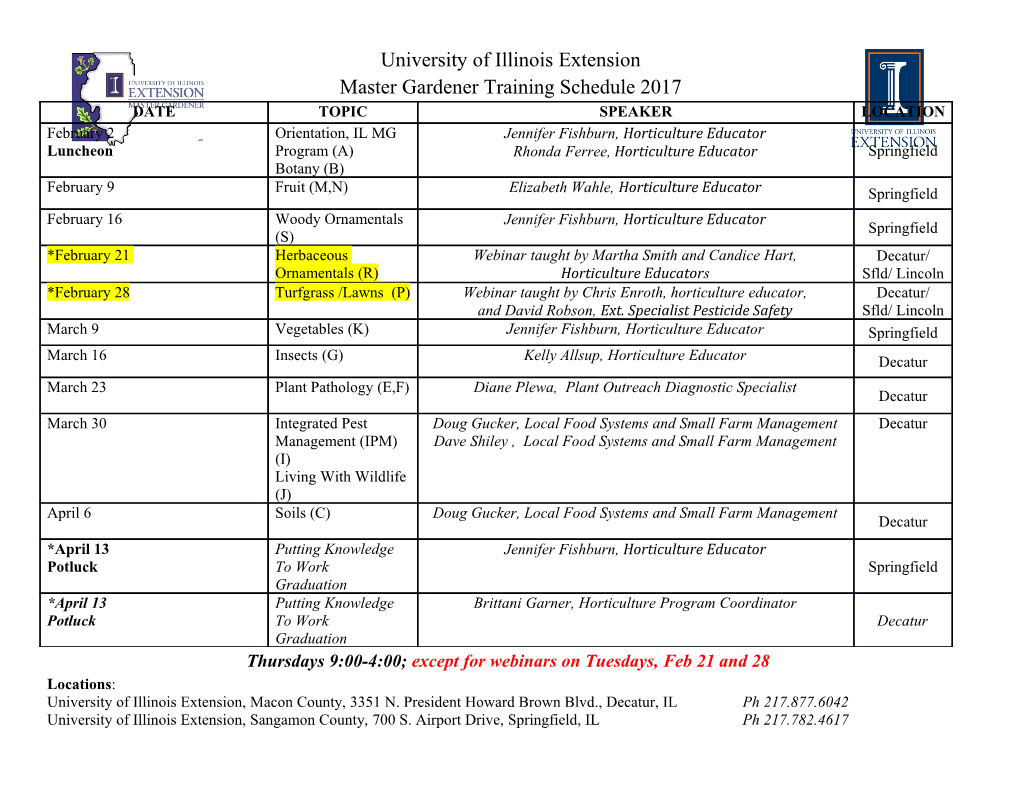
Appendix A - Conversion from Molar to Molal In electrochemistry the molality concentration scale is usually used which gives the concentration of moles solute per kg solvent. The concentration from a molar scale is as follows: Cj mj=------~------ (AI) PL -0.001 I,Mj cj M j [kg/kmol] denotes the molecular weight, PL [kgIL] is the density of the solution and is usually unknown. An approximation for it is the apparent molar volume cP; . where the molar volume VL of a solution is the result. (A2) Vw is the molar volume of water at the appropriate temperature, nw denotes the number of water molecules and ni that of ions. cP; is thus the volumetric difference of a solution and pure water related to one mol of an electrolyte. Masson (1929) showed cP; to be proportional to the square root of the electrolyte concentration: (A3) cpO is the apparent molar volume of an electrolyte MpXq at infinite dilution. For a single electrolyte equ. (A3) is a good approximation. For mixtures the following is valid: (A4) (A5) (A6) and thus for a single ion: cpV = cp.o + s. r;;---Mx (A7) I I I V..... Mpxq Appendix A - Conversion from Molar to Molal 151 However, cP; can therefore be calculated for one salt at its concentration c. Equ. (A 7) can be rewritten: cP v =cP0 + Si # (AS) I I ~(z~ p+zi q)/2 where the ionic strength f for a salt MpXq on a molar basis is: Ie =t (z~ cM+ zi cJ= t (z~ p cMpXq + zi q cMpXJ (A9) In order to calculate the apparent molar volume of a multicomponent solution, it is assumed to be only a function of f at a given temperature. This relies on experimental results that negligible volume change will occur when mixing solutions of equal ionic strength [Young & Smith (1954)]. Equ. (A9) is thus valid in a salt mixture, where (AIO) In order to calibrate the proportionality factor Si the following conversion was made: cPOH+ = 0 and S H+ =0 (All) Hel in water serves as an example for this where the concentration dependency of the density must be known. According to Hamed and Owen (195S): (AI2) Plotting cP; versus the square root of the concentration yields cPo and S. With the zero contribution according equ. (AI2) the following is valid: (A13) With the mixing rules (equs. (A4) and (AS)) <P and S of any other cation can be estimated if density data for the chloride salt are available. Equ. (AI2) can be rewritten and for a single ion is thus: c.{p cPv-M) (P -p )= I W I I (AI4) W L 1000 and accordingly for n ions: (AI5) and finally: 152 Appendix A - Conversion from Molar to Molal I n P =P --~{- cpv -M)c (AI6) L w 1000 ~ \Pw iii A compendium of Masson parameters can be found from Milero (1972) and Harned and Owen (1958). In order to convert the equilibrium constant of the law of mass action we rely on the following limits, where v denotes the stoichiometric factor: (AI?) !iToKm =IT (mJ'i (AI8) j~1...n i=l and litn( P (AI9) 'i~\mi5...J= where P [kg/L] is the density ofthe solvent. For a homogeneous reaction there IS: (A20) and for a heterogeneous reaction we have to consider the density of the diluent (PDIL) and of water (Pw): K C = K m (PDIL)lJ:..viIDIL (Pwt£vit (A21) Appendix B - Activity Coefficient Conversion The chemical potential of a binary electrolyte MpXq reads as: I1Mx = P fit! + RT In(y; mM )]+ q fIt~ + RT In(y;' mx )] (Bl) with mM = P m and mx = q m is: IlMx = m~x + RT In (m p+q pP qq)+ RT In(YM P Yx q) (B2) with (B3) Since there exists no solution of single cations or anions what can be measured is a mean or average activity coefficient: (B4) and 1 m± = (mft m'Jr):; (B5) with s=p+q. The expression for the chemical potential of a dissolved salt is then: I1Mx = I1MxEll + RT In ( m ± y ±)S (B6) In real solutions, the activity of water is quite close to one as the dilution ratio of the salts increases. In order to represent accurately the activity of water, several significant digits would be required. To avoid this problem, in many compilations of data it is common to tabulate data in terms of the osmotic coefficient ¢w. It is derived considering non-idealities in the van't Hoff equation with membrane processes and is defined as [Horvarth (1985)]: 1000 C/Jw = --n-- Inaw (B7) MwLmi i=l It can be derived from the Gibbs excess enthalpy as to 154 Appendix B - Activity Coefficient Conversion ifYw -1 = (BS) i=l The conversion of activity coefficients of electrolytes from one scale to another is presented by Robinson and Stokes (1965) as to: • mole fraction to molal: (B9) • mole fraction to molar: (BlO) • molal to molar: y± -_(PL -0.001 eMi) y±(e) -_(_e_) y±(e) (B11) Pw m Pw • molar to molal: y~c) = (1 + 0.001 mMJ Pw y± = (m Pw )Y± (B12) PL e For non-electrolytes a similar procedure can be derived on the basis of the chemical potential on molar scale: e) ) J1; =J1;O(e)+RTln( ei;ai with CO =lmollL (B13) and on mole fraction scale: J1i = J1;o + RT In(xi Y?»)= J1;o + RT In(a;) (B14) thus lnY,(c) =In(~.')+ J1,0 -J1,O(e) (B15) y,i') c, RT The last term in this equation is independent of concentrations and is thus defined considering the following limit: lim yid = 1 (B16) Cj ---to 1 withe ~ 0: Appendix B - Activity Coefficient Conversion 155 l;",(ln y;(') In(2)J= In(-I In(c )= 11; - 11;° (c) (BI7) ,;---..:\ y;(X) + x; y;- )+ , RT The ratio c;lx; at c ~ 0 approaches the molar concentration of the solvent, cs• It follows: r,") = r,'" ( :; )( ;,: ) (BI8) The same procedure holds for the molality scale conversion with reference (see equ. (B13)) CO = I kgIL, where ms is the molal solvent concentration: r"m, = r,'" ( :: )(; ) (BI9) Appendix C - Operation and Design of a Sieve Tray A large part of industrial extraction columns are made up of sieve trays. They are either used in a non-agitated mode or more often in a reciprocating mode. A rapid reciprocating motion imparted to the liquid in a tower results in an improved mass transfer. This action can be accomplished without moving parts or bearings coming into contact with the liquid phase and thus has found an application for handling hazardous and corrosive liquids in the chemical and nuclear industry. However, an alternative to the pulsation of the liquid is by a reciprocating motion of the plates [Lo et al. (1983)]. The sieve tray column (see Fig. C-1) was first patented by Laird (1919) and can be designed either to disperse the heavy or the light phase. The continuous phase passes across each tray and proceeds to the next one through a downcomer or a riser. The dispersed phase is trapped and coalesced at each tray in a layer and redispersed. The axial dispersion is thus limited between two trays within these coalesced layers. The repeated stagewise dispersion and thus surface renewal have generally improved the efficiency in comparison to other types of non-agitated towers. Due to the complex hydrodynamics multi-pass trays are not usual and the column diameter is usually smaller than 3.66 m. The tray deviations from horizontal should be less than ±lmm, which also limits column diameters. In large trays the two halves of the tray are separately removable and the tray spacing should be at least 0.4 m in order to provide entry ports for cleaning and installation. The tray is sealed with a valance or a spiral spring in a cage, since otherwise it gives rise to emulsion formation, and in contrast to absorption/distillation there is no weir. The clearance under the downcomer is usually a quarter of the tray spacing. The hole diameters are much smaller than in gas-liquid systems with 2-8 mm (2 mm is a fabrication limit) and are usually set in triangular (square) arrays on about 16mm centres. There appears to be little effect of the hole size on the extraction rate, but with systems of higher interfacial tension, smaller holes should be favoured. They occupy from 5 to 63% of the available tray area (default 15%). The velocities through the holes should be kept between 0.l5 and 0.3 m/s. If the downcomer is equipped with coalescence aids, the downcomer section must be made correspondingly larger. Further details can also be found in Treybal (1963), Skelland and Conger (1973), Pilhofer and Mewes (1979), Cavers (1983), Humphrey et al. (1994), Robbins and Cusack (1997) and Mewes and Pilhofer (1979). In the following the design and the operation of a sieve tray column is discussed (http://www.uni-kl.de./LS-Bart/DAE). Appendix C - Operation and Design of a Sieve Tray 157 ~HHHH How a tray works dispersed phase through the holes continuous phase through th e downcomcr. across th e tray coalescence zonc dispersion droplct fonnation this is a small. single pass tray Fig. C-l: The sieve tray C.1 Operating and Design Variables Once a sieve tray has been constructed, we can still change conditions on the tray via operation variables. Here, we only consider the internal flow rates of the heavy and light liquid as operating variables. We do not consider changes in temperature but have to balance the pressure drop at each tray for functionality.
Details
-
File Typepdf
-
Upload Time-
-
Content LanguagesEnglish
-
Upload UserAnonymous/Not logged-in
-
File Pages57 Page
-
File Size-