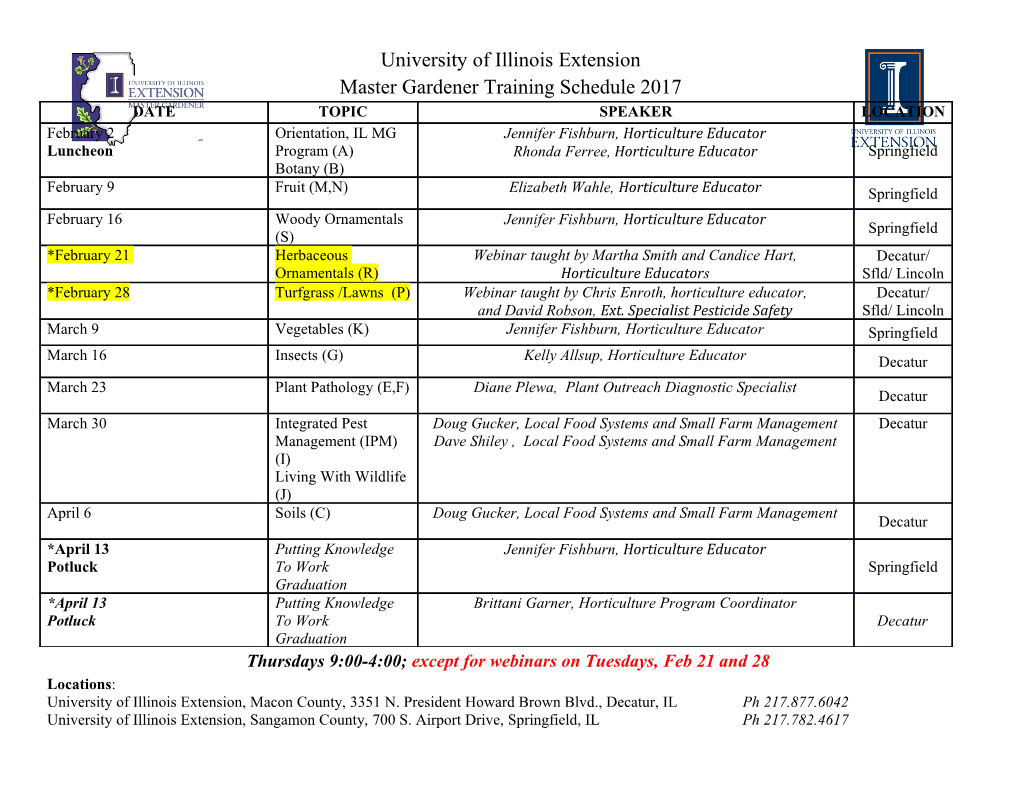
University of Tennessee, Knoxville TRACE: Tennessee Research and Creative Exchange Doctoral Dissertations Graduate School 5-1997 An Experimental Investigation of Creep and Viscoelastic Properties Using Depth-Sensing Indentation Techniques Barry Neal Lucas University of Tennessee - Knoxville Follow this and additional works at: https://trace.tennessee.edu/utk_graddiss Part of the Metallurgy Commons Recommended Citation Lucas, Barry Neal, "An Experimental Investigation of Creep and Viscoelastic Properties Using Depth- Sensing Indentation Techniques. " PhD diss., University of Tennessee, 1997. https://trace.tennessee.edu/utk_graddiss/1255 This Dissertation is brought to you for free and open access by the Graduate School at TRACE: Tennessee Research and Creative Exchange. It has been accepted for inclusion in Doctoral Dissertations by an authorized administrator of TRACE: Tennessee Research and Creative Exchange. For more information, please contact [email protected]. To the Graduate Council: I am submitting herewith a dissertation written by Barry Neal Lucas entitled "An Experimental Investigation of Creep and Viscoelastic Properties Using Depth-Sensing Indentation Techniques." I have examined the final electronic copy of this dissertation for form and content and recommend that it be accepted in partial fulfillment of the equirr ements for the degree of Doctor of Philosophy, with a major in Materials Science and Engineering. Carl J. McHargue, Major Professor We have read this dissertation and recommend its acceptance: Warren C. Oliver, Ben F. Oliver, Thomas G. Carley Accepted for the Council: Carolyn R. Hodges Vice Provost and Dean of the Graduate School (Original signatures are on file with official studentecor r ds.) To the Graduate Council: I am submitting herewith a dissertation written by Barry Neal Lucas entitled" An Experimental Investigation of Creep and Viscoelastic Properties Using Depth­ Sensing Indentation Techniques." I have examined the final copy of the dissertation for fonn and content and recommend thatit be accepted in partial fulfillment of the requirements for the degree of Doctor of Philosophy, with a major in Metallurgical Engineering. u� Carl�. J. McHargue, Chairperson We have read this dissertation and recommend its acceptan Warren C. Oliver, Technical Advisor :;7 ��,if�.� ve -=- Thomas G. C�r Accepted for the Council: Associate Vice Chancellor and Dean of the Graduate School AN EXPERIMENTAL INVESTIGATION OF CREEP AND VISCOELASTIC PROPERTIES USING DEPTH-SENSING INDENTATION TECHNIQUES A Dissertation Presented for the Doctor of Philosophy Degree The University of Tennessee, Knoxville Barry Neal Lucas May 1997 Dedication This dissertation is lovingly dedicated to my wife and sons; Becky, Noah, and CalebLucas and to my parents; Arviland Jane Lucas Thank you all. 11 Acknowledgments There are many people to whom lowe a debt of gratitude for making this work possible. First and foremost, my technical advisor throughout my graduate career, Dr. Warren C. Oliver. It is from his creative imagination that the idea for the hardware built for this study evolved. Not only has he acted as my advisor and mentor throughout the entirety of this work, he has also been my friend. I will always consider him my greatest teacher for it is from him that I have not only learned a great deal of materials science, but also a great deal about what it takes to be a materials scientist. I also wish to thank the other members of my committee, Dr. Carl J. McHargue, Dr. Ben F. Oliver and Dr. Thomas G. Carley. In addition to these official members, special thanks are owed to Dr. George M. Pharr of Rice University for his valuable contributions to the indentation creep portion of this work, and to Dr. Jean-Luc Loubet of the Ecole Centrale de Lyon for the opportunity to work with him on the measurement of the viscoelastic properties of materials with indentation techniques. There are many others who have helped in many ways during the course of this work. Dr. Ting Y. Tsui and Dr. Alexeii Bolshakov, two fellow Ph. D. students who have gone on to great things, are thanked for their assistance at various times during this work. I would also like to thank all of the people at the Oak Ridge National Laboratory with whom I have had the opportunity to work but are too numerous to name. These are the people who have quite often given very unselfishly of both their time and resources with no reason for doing so other than their willingness to help a friend. All of you are graciously thanked and you will be sorely missed. Saving the best for last, lowe everything that I have accomplished to my family to whom this work is dedicated. My wife Rebecca has stood by me through all of the iii long days and nights and never wavered in her love and support. She is quite truly the most remarkable woman that I know. Not only is she a wonderful wife, but also a wonderful mother to my two sons Noah and Caleb. The three of them have been a constant reminder that there are more important things in life than ones work. And finally to my parents, thank you for giving me every imaginable opportunity, which is all anyone can ever ask for. Your never ending support for me throughout every endeavor of my life will never be forgotten. Financial support for this work from Nano Instruments, Inc. and the division of Materials Sciences, U.S. Department of Energy, under contract DE-AC05-840R21400 with Lockheed-Martin Energy Systems, Inc. is gratefully acknowledged. iv Abstract Broad band, quasi-static and frequency specific dynamic techniques adapted to depth-sensing indentation testing have been utilized to measure both time dependent plasticity (creep) at both room and elevated temperatures as well as time dependent elasticity (viscoelasticity) at room temperature. Indentation Creep Using a variety of depth-sensing indentation techniques at both room and elevated temperatures, the dependency of the indentation hardness on the variables of indentation strain rate (stress exponent for creep, n) and temperature (apparent activation energy for creep, Q), and the existence of a steady state behavior in an indentation creep test with a Berkovich indenter were investigated. The indentation creep response of five materials, Pb-65 at% In (at RT), high purity indium (from RT to 75°C), high purity aluminum (from RT to 250°C), a vapor deposited amorphous alumina film (at RT), and single crystal alumina (sapphire) (at RT), was measured. It was shown for the first time that the indentation strain rate, def ined as it/h, could be held constant during an experiment using a Berkovich indenter by controlling the loading rate such that the loading rate divided by the load, Pip, remained constant. This technique yields the most unambiguous determination of the stress exponent for creep and seems to most closely approximate the steady state results from uniaxial testing. The results from the constant P/ p experiments were compared to the results from conventional indentation creep experiments where the load is ramped on at a high rate and then held constant for a period of time. It was shown that the transition from the loading segment to hold v segment shows a transient period with an apparent higher stress exponent for creep which has previously been mistaken for power law breakdown type behavior. The apparent activation energy for indentation creep in indium was found to be approximately 78 kJ/mol, in excellent agreement with the activation energy for self diffusion in the material. The temperature dependence of the indentation creep process in aluminum was found to be best described by an effective diffusion coefficient as described in the literature for bulk aluminum at intermediate temperatures. By performing Pip change experiments it was shown that a steady state path independent hardness could be reached in an indentation test with a geometrically similar indenter. The arrival at a new steady state value of hardness seems to depend on the accumulation of strain rather than a relaxation time. The measurements on amorphous alumina and sapphire demonstrate the technique's ability to measure differences in the time dependent response of materials that can not be tested with other techniques. Viscoelasticity Using a frequency specific dynamic indentation technique, a general method to measure the linear viscoelastic properties of polymers was determined. The polymer tested was an amorphou s unvu1canized natural rubber, poly-cis l,4-isoprene. By imposing a small harmonic force excitation on the specimen during the indentation process and measuring the displacement response at the same frequency, the complex elastic modulus, G*=G'+iG" , of the polymer was determined. The portion of the displacement signal which is "in phase" with the excitation represents the elastic response of the contact and is related to the stiffness (S) of the contact and to the elastic modulus, or storage modulus (G') , of the material. The "out of phase" portion of the displacement signal represents the energy being absorbed by the material, i.e. the VI damping (Coo where 00=2 1t t) of the contact, and thus the loss modulus (G") of the material. It was shown that the storage, S, and loss, Coo, components of the displacement response scale as the respective component of the complex modulus multiplied by the square root of the contact area. Vll Table of Contents Chapter 1 Introduction ... .... ..................... ............ ... ...... ........................... .. 1 1. Introduction........................ ...............................................................
Details
-
File Typepdf
-
Upload Time-
-
Content LanguagesEnglish
-
Upload UserAnonymous/Not logged-in
-
File Pages250 Page
-
File Size-