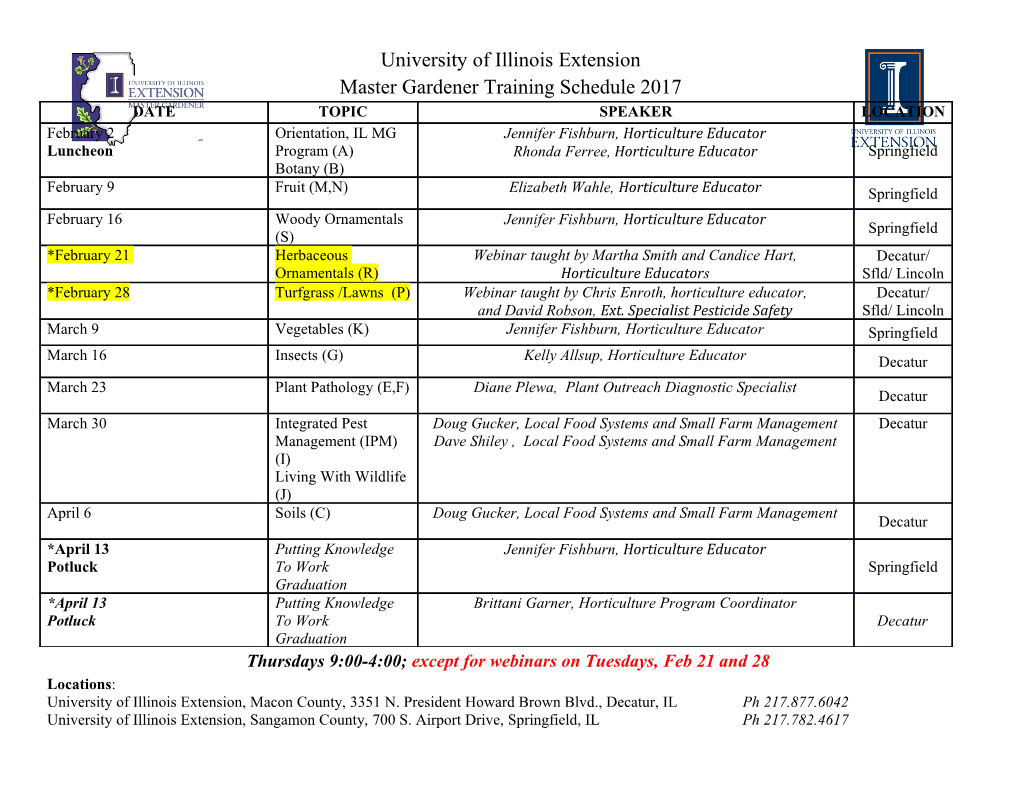
OPTIMAL BLADE DESIGN FOR WINDMILL BOATS AND VEHICLES B. L. Blackford Physics Department Dalhousie University Halifax, Canada B3H 3J5 Abstract This paper discusses the theoretical problem of designing the optimal windmill blade for use on windmill boats and vehicles. The analysis shows that the optimal design for this application is considerably different from that for a conventional stationary windmill. A practical procedure for blade design is given, and experimental results from a 4 m catamaran boat, using a A m diameter wind turbine, and from a wheeled vehicle, using a 1.2 m diameter wind turbine, are presented. The boat achieves an upwind speed of -503! of the wind speed and the vehicle achieves "1002, in agreement with theory. 1. INTBODÖCriON propulsion was revived by the "oil crisis" and the subsequent search for altemative energy sources. (2),(3),(4) During the past several years we A windmill boat is a wind-driven boat in which a have worked on the theory of windmill boats and windmill type air turbine is mechanically coupled vehicles and have carried out niogerous to an underwater propeller. Kinetic energy ex­ experiment8^5),(6), (7)_ objective was to tracted from the wind by the windmill blades is develop a fundamental understanding of these used by the underwater propeller to push the boat devices and, thereby, to identify the parameters directly against the wind. Fig. 1. The boat moves which are iii{>ortant for their efficient, fast forward because the moraentum added to the water can operation. In the present paper we extend this be greater than that removed from the air, despite work to the problem of designing the optimal unavoidable energy losses in the system. In a windmill blade for this application. A detailed similar manner, a wheeled vehicle can move against account of the general theory of wiodmill boats and the wind by coupling the windmill blades to a driv­ vehicles is given in references (5) and (6). ing wheel. In addition to the capability of sail­ ing directly upwind, windmill boats and vehicles can also sail at any other direction relative to 2. BLADE ELEMEOT THEOKÏ the wind, by orienting the windmill blade to face the apparent wind, Fig. 1. 2.1 WIND BLADE Historically, the concept of windmill boats and vehicles can be traced back tu the early 1900*8, by The modem theory of propeller design, and also of numerous patents and published articles in Europe windmill blade design, was developed during the and America.^'-) More recently, interest in wind early 1900's by Betz, Prandtl and Goldstein. 103 A thorough review of the subject was given where C is the overall efficiency factor **o£ the by Glauert^l''^ and we follow his approach and driving mechanism, 0<4<1. notation where possible. More recently, the propeller theory was revived by Larrabee^11), tailored to computer use and applied to several The driving mechanism consists of the drive shaft, cases, the most notable success being an improved gears, bearings and underwater propeller, or drive propeller for the Gossamer Albatross raan-pouered wheel for the case of the vehicle. The underwater monoplane. propeller is the major source of inefficiency fur the case of che boat. Our objective here is to use and extend this pro­ peller theory to design the optimum windmill blade Associated with the extraction of power from the and underwater propeller for a windmill boat. Let wind, there is a backwards force, dFy, on the air W be the windspeed and assume that the craft turbine which is given by the longitudinal travels straight upwind* at a speed u, expressed as component of the aerodynamic force acting on the u - f W. For given u/W, we seek to optimize the blade elements, i.e. blade design so as to maximize the net forward force. Referring to Fig, 2, the apparent windspeed experienced by the rotating blade element at radius r is given by dF„ = -P^CNV^CCL COS*+CD sin^) dr . (4) 2 V - C[(u+W)(l-a)]^ + ((l+a')nrf )l/2 (i) The net forward force (dF-dFy) is given by combining Eqns. (2), (3) and (4): where the quantity a expresses the fractional decrease in the wind by the time it reaches the propeller and quantity a* accounts for the induced dF-dFy = -pycGLNV^[c_5. (sini(i-e cos4>) - rotation of the windfield at the propeller tlOJ. The quantity a satisfies 0<a<l/2 and both a and a' (cosiji+esin^) ]dr (5) depend on r and are functionally related to each other. If the propeller was absent, or inopera­ tive, a and a' would be zero and the apparent wind where e » Cp/C^ is the drag to lift ratio of felt by the blade would be simply (u+W). the aerofoil section. Introducing the dimension­ less speed ratio The power extracted from the wind by the blade elements of length dr is given by the product of s = nr/(u+W) (6) the tangential component of the aerodynamic force acting on the blade element times the tangential velocity component of the blade element, f!r. That and noting that, from momentum considerations, the is. backwards force can be expressed in the alternative form tlO^, dP = ^ycm^iCi sin4i-CDC0s«)rir dr (2) dFy = 2p(^(u+W)^a(l-a)2iir dr , (7) where N is the number of blades, ^ is the apparent The net forward force, Eqn. (5), can then be wind angle, py is the air density, c is the chord written as and CL and Cp are the lift and drag coeffici­ ents of the blade element, respectivelyj Fig. 2. Gj^ and Cp depend upon the particular aerofoil dF-dFw = 4TrpHR^(u+W)^ lÜ^^H(s)s ds (8) section used and upon its angle of attack with S respect to the velocity V. The forward force, dF, derived from the power dP where R is the propeller tip radius, S = fiR/(u+W) can be expressed as is Che tip speed ratio, f = u/W and the function H(s) is given by dF - CdP/u (3) (a) * For simplicity, we limit the discussion here to the upwind direction, with the intention of publishing the complete theory at a later date. (b) ** 5 is fundamentally different from the efficiency factor n used in our previous publications '•^'°>'K 104 = 0.13 would give the nwximom T^^j. This H(.) - C(Xn/f). [Cl-')-^"*"')'] - I . (9) result is somewhat counter intuitive because it [(l»«').+c(l-a)] says that at higher boat speeds the propeller must be designed to extract even less energy from the wind, to obtain the maximum possible normalized, Integrating Eqn, (8) over the blade length from F„gj. Of course, the value of the maximum F^g^j centre to tip, we get the total net forward force, decreases as the boat speed increases See normaliced for a given propeller radius and Fig. (6). apparent windspeed, i.e. It is interesting to compare the above result to FNET 1 s the case of a stationary windmill where the " - ƒ a(l-a)H(a)a ds . (10) optimization condition is simply to obtain the 4»Pw?(u+W)* o maximum possible power output, regardless of the backwards force on the windmill blade. The well-known result for this case is that the Our objective is to design the blade so as to optimal a(s) is given by a(8) = 1/3, except for a maximize Fjjgj with respect to the various reduction of a few percent for 8<1. This is a very parameters. Firstly, we see from Eqn. (9) that the much different result from the case of a windmill efficiency C must be large if high boat speeds, f ^ boat or vehicle, which we have presented here. 0,5, are to be obtained. Small values of the drag/ lift ratio, e, are also helpful. Secondly, we keep C, f and E fixed and address the problem of maxi­ The dependence of F^gx °" other parameters in mizing fffg^j. with respect to a(s), a'Cs) and S, Eqn. (1) is shown in Figs. (4), (5) and (6). The Fortunately, a'(a) depends on a(a) and it can be efficiency factor C has the greatest effect on shown, after a considerable number of steps which FuET, as can be seen in Fig. (4). Reduction of 5 are omitted here, that from 1,0 to 0.6 reduces Fj^gf by a factor of seven, for the particular choice of the other parameters given in the figure- For the case of the boat, the underwater propeller is the major «'(s)- - i(l+e/s)+ i/(l+e/s)2+4a[(l-a)/s2-E/8] (U) source of inefficiency and we therefore see the need for good underwater propeller design. This is discussed further in sections (2.2) and (3.2). which is an exact relation, in contrast to the approximate relation used by Larrabee ^ We The effect of the drag/lift ratio, E, is shown in are then left with the problem of optimizing a(s). Fig. (5), where it can be seen that low values of e It is very difficult, if not impossible, to find an are very important, particularly at the higher tip exact analytical function for the optimal a(a), so speed ratios. Small values of E are obtained by we chose instead to use an empirical technique. using good aerofoil sections, combined with high aCs) was chosen to maximize FjigT» Eqns, (9, 10), aspect ratio blades and high quality construction for a series of discrete values of s, ranging from methods.
Details
-
File Typepdf
-
Upload Time-
-
Content LanguagesEnglish
-
Upload UserAnonymous/Not logged-in
-
File Pages14 Page
-
File Size-