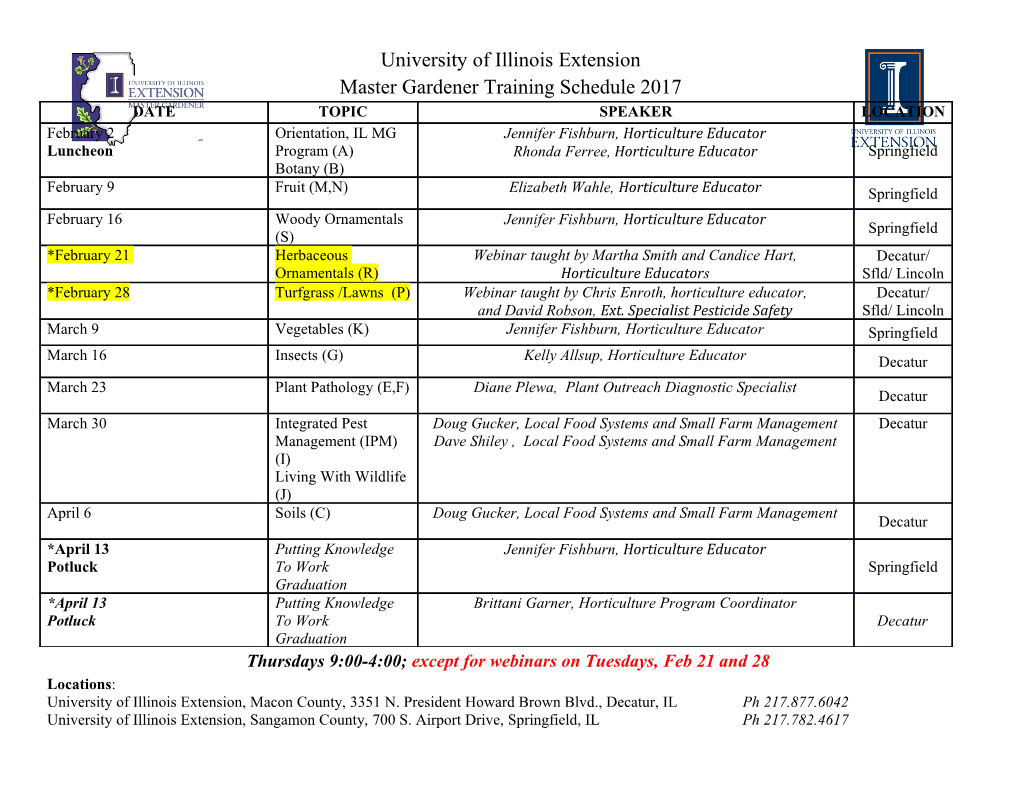
THE IEC/IEEE TRAIN COMMUNICATION NETWORK RAILWAY OPERATORS AND MANUFACTURERS HAVE STANDARDIZED A DATA COMMUNICATION NETWORK THAT INTERCONNECTS PROGRAMMABLE EQUIPMENT BETWEEN AND WITHIN RAIL VEHICLES. THIS DATA BUS ARCHITECTURE OFFERS A BASIS FOR STANDARDIZATION OF FUTURE RAILWAYS APPLICATIONS. Automatic coupling of railway vehi- dards Committee Working Group 1 con- cles has existed since the mechanical Jenny cou- tributed to this work in the late phase and pler at the turn of the 19th century. The railway adopted TCN as IEEE Std. 1473-1999 Type industry’s next challenge is automatic coupling T with no modifications the same year.2 of the vehicle’s electronic equipment through a An international standardization of data data bus. This requires a worldwide standard- communication is necessary at both the train ization of onboard data communication. A and vehicle levels. Trains with varying com- joint effort by the International Railways position during daily service—such as metros, Union (Union Internationale des Chemins de or suburban and international trains—need a Fer, or UIC), Utrecht, Netherlands, and the standard form of data communication for train Hubert Kirrmann International Electrotechnical Committee control, diagnostics, and passenger informa- (IEC), Geneva, Switzerland has laid the tion. Such communication should configure ABB Corporate Research groundwork for this standardization. The UIC itself when vehicles are coupled on the track. groups all national rail operators worldwide and At the vehicle level, a standard attachment ensures cross-border traffic by standardizing of equipment would serve manufacturers, sup- Pierre A. Zuber track profiles, pneumatic hoses, traction volt- pliers, and operators. Manufacturers could ages, operating procedures, and so on. The IEC assemble pretested units, such as doors manu- DaimlerChrysler is well known to IEEE members for its impres- factured by subcontractors, which include their sive collection of standards in the electric world, own computers. Parts suppliers who interface Rail Systems and as the “electric sister” of the ISO. with different manufacturers could reduce Deputies from over 20 countries, includ- development costs by adhering to one standard. ing many European nations, the US, Japan Railroad operators could reduce spare parts and and China representing major railways oper- simplify maintenance and part replacement. ators and manufacturers, worked several years within the IEC’s Working Group 22 (WG22) General architecture on the definition of the Train Communica- The TCN architecture addresses all relevant tion Network. The TCN was adopted as the configurations found in rail vehicles. It com- international standard IEC 61375 in 1999.1 prises the train bus connecting the vehicles and The IEEE Rail Transit Vehicle Interface Stan- the vehicle bus connecting the equipment 0272-1732/01/$10.00 2001 IEEE 81 TRAIN NETWORK aboard a vehicle or group of vehicles, as shown in Figure 1. A vehicle may carry none, one, or several vehicle buses. Train bus The vehicle bus may span sev- eral vehicles, as in the case of Node Node Node mass-transit train sets (multi- ple units) that are not sepa- rated during daily use. In Vehicle bus Vehicle bus Vehicle bus closed train sets where the train bus needs no sequential Figure 1. Train communication network. numbering of nodes, the vehi- cle bus may serve as a train bus, as shown in Figure 2. 860 meters (without repeater) Wire Train Bus MVB MVB To respond to the demand for train-level standardization, 0 node 0 vehicle bus 1 vehicle bus 2 vehicle buses WG22 specified the Wire (conduction vehicle) (standard MVB) (standard and not) Train Bus (WTB) as part of (a) the TCN architecture. The WTB interconnects vehicles 200 meters (without repeater) over hand-plug jumper cables MVB or automatic couplers, as shown in Figure 3. 1 vehicle bus Not standard vehicle bus WG22 considered several (b) media. It rejected coaxial cable because of its poor mechani- 200 meters (without repeater) cal resistance to shock and MVB MVB vibration. Optical fiber was also dismissed because of dif- 1 vehicle bus 0 vehicle bus ficulties in building automat- (c) ic couplers that could withstand shock and vibration Figure 2. Open train with the Multifunction Vehicle Bus as vehicle bus (in some vehicles) and as well as harsh weather con- the Wire Train Bus as train bus (a); connected train sets with the Wire Train Bus as the train ditions. Therefore, as its name bus and the Multifunction Vehicle Bus interconnecting an (inseparable) vehicle set (b); closed implies, the WTB uses a twist- train, such as a tilting train, with the Multifunction Vehicle Bus both as a train bus and as a ed shielded-wire pair, which vehicle bus—a nonstandard bus can also be integrated as vehicle bus (c). has demonstrated its reliabili- Port Bottom Top Starboard Trunk cable Ascending Descending Jumper cable Master 1 2 1 2 12212 Node Node Node Node 1 Node End vehicle Intermediate vehicle(s) Intermediate vehicle(s) End vehicle Node number 6301 02 03 04 Figure 3. Wire Train Bus. 82 IEEE MICRO ty in several European trains. WTB cable Redundant nodes Vehicle Originally the WTB shared Vehicle Jumper the UIC cable with the stan- Line A Line B dard wires carrying the DC Classic Classic signals for controlling lights, 2 1 1 2 UIC lines loudspeakers, and doors in UIC WTB node lines WTB node WTB node international vehicles. Due to Line B Jumper Line A these wires limited capacity and in view of future require- UIC jumper cable ments, the UIC decided to add to the UIC cable a dedi- Figure 4. WTB cabling (top view). cated, twisted shielded-wire pair capable of carrying data at 1 Mbps. The WTB layout is by principle redundant; one Manchester encoding cable runs on each side of the Manchester encoding is a robust, synchronous encoding scheme used by several buses such as Ethernet. It vehicle, as shown in Figure 4. encodes bits in fixed time slots (cells); a “1” represented as a positive transition in the middle of a cell and a The WTB can span 860 “0” as a negative transition (or the reverse). Since there is always one transition per bit, the signal clock may meters, a distance correspond- be easily recovered from the signal. ing to 22 UIC vehicles, In its simplest form, Manchester is decoded by sensing the zero crossings of the signal. This uses inexpen- without a repeater. This sive RS-485 transceivers, such as those used by the MVB. Sensitivity is increased by sampling the signal at its requirement allows connecting peaks, see Figure A. A clock synchronized to the signal by a phase-locked loop evaluates the position of the of older vehicles not equipped peak. To allow the phase-locked loop to adjust itself, useful data must be preceded by a preamble with a known with the new data bus onto a sequence, consisting usually of alternating 0s and 1s. train. It also allows bypassing of In WTB, the phase-locked loop is enhanced by signal processing techniques, similar to those used in DSL. vehicles with a low battery volt- age—a major concern because 1 0 1 0 1 0 1 0 1 0 1 0 1 0 1 1 0111111 of battery discharge when vehi- Line cles are in the marshaling yard. The WTB may have to oper- ate under harsh environmental conditions where oxidation of preamble data contacts can occur. To clean oxidized connectors or con- Figure A. The Manchester encoding scheme signal sequence. tacts, a fritting voltage (clean- ing action of the coupler’s contact) can be superimposed on the lines. node. In general, there is one node per vehi- The binary data are not transmitted over cle, but, as shown in Figure 3, there may be the cable as a sequence of 1s and 0s, techni- more than one or none at all. cally known as nonreturn to zero. Instead, the At the end of the inauguration, all vehicles bits have a Manchester encoding scheme, recognize the train topography, including offering several advantages (see “Manchester encoding” sidebar). • their own address, orientation (right and The WTB’s most salient feature (and a left), and position with respect to the bus unique trait in the railroad industry) is that it master (aft and fore); automatically numbers nodes in sequential • other vehicles’ number and position in order and lets all nodes distinguish between the train; the train’s right and left sides and aft and fore • other vehicles’ type and version (loco- directions. Each time the train composition motive, coach, and so on) and their sup- changes, for example, after adding or remov- ported functions; and ing vehicles, the train bus nodes execute the • their own and other vehicles’ dynamic inauguration procedure, which connects elec- properties (for example, the presence of trically and assigns a sequential address to each a driver). MARCH–APRIL 2001 83 TRAIN NETWORK End node Intermediate node(s) End node Trunk cable Terminators Jumper cable Terminators (inserted) (inserted) +- +- +- +- +- +- +- +- Bus controllers Bus controllers Bus controllers Bus controllers Two channels active One channel active One channel active Two channels active Figure 5. Detailed view of WTB. Each node comprises two high-level data For instance, nodes may wake up from low- link (ISO 3309) control channels, one for power sleep mode to active mode in the mid- each direction (forward, backward) as shown dle of an inaugurated composition, nodes in Figure 5. During operation, the end nodes could start operating as backup in cases where insert their termination resistors to close the a working node fails, or one of the redundant bus, while the intermediate nodes establish lines might fail (only one line is shown in Fig- bus continuity between the end nodes. On ure 5) and this may not affect numbering.
Details
-
File Typepdf
-
Upload Time-
-
Content LanguagesEnglish
-
Upload UserAnonymous/Not logged-in
-
File Pages12 Page
-
File Size-