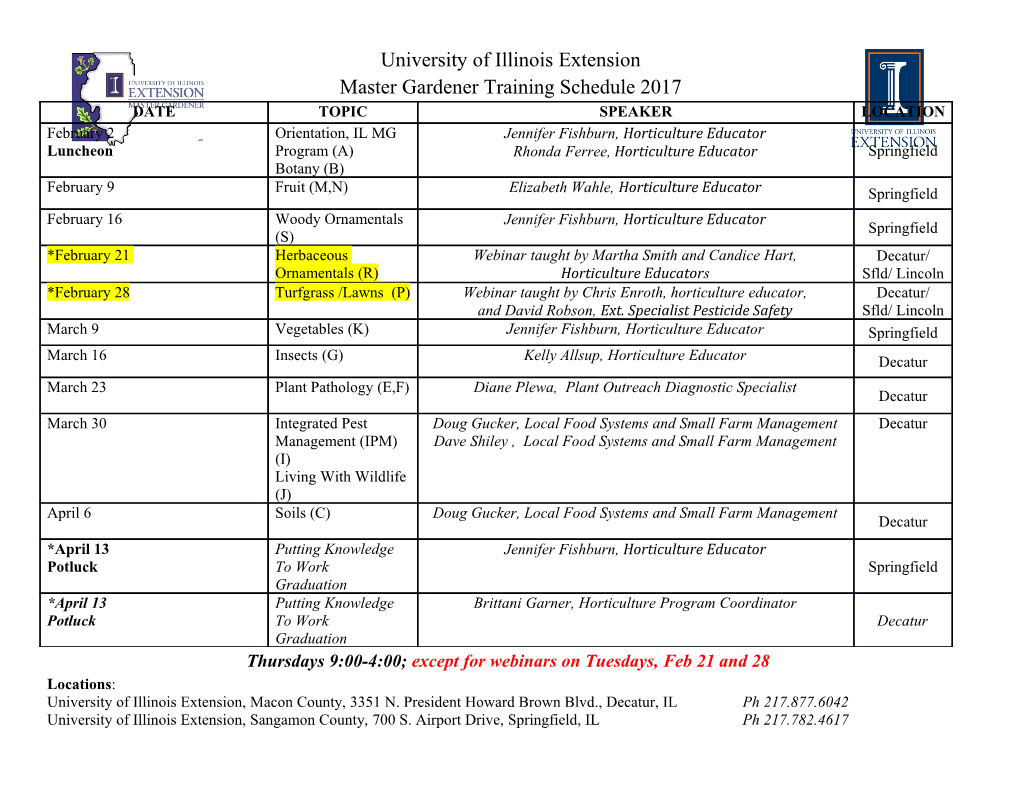
A basic component essential to the successful performance of today's high oompreosion engine is the %Tangshaft, The loads imposed on.the crankshaft have placed great impor- tance on its fatigue'life. A prime facto'r affecting the fatigue life of a crankshaft in the size of the crankshaft fillet radiuu area. Beginning with the 1964 model produotion, Oldsmo- bile Division initiated ,the practice of tangentially rolling crankshaft fillcte. Tho result kas been a 50 per cent increaoc in fatigue life. The deep fillet rolling proooas, originally develoflcd in 'West Germany, das selected by Oldsmobile after aeveral years of investi- gating various metal working processing methods. N 1959, a program was started at completed in 1961, involved running ' $1ol&mobile to investigate ways to many tests on various type dressers in increase the fatigue life of the crankshaft, cooperation with diamond dressing tool with particular attention being given to companies, diamond tool manufacturers, the crankshaft's critical radii. Various and machine builders in an attempt to manufacturing methods and variations develop the type of dresser required. of existing processes pertaining to crank- Everything from cam dressing with grit shaft production were studied and tested, tools to carbide form rolls, both recipro- including rolling, shot blasting, shot cating and plunger type, was tried. peening, and liquid peening. Impregnated and set-stone formed The methods and processes studied all diamond wheels also were used in the had various shortcomings. For example, attempt to precision dress the crankpin the shot blasting method for increasing grinding wheels. Single point diamond fatigue life was rejected because of the tools following a profile cam were put size of the equipment required, the high through various tests with a minimum maintenance costs, and the uneven force amount of success. Eventually, a rotary reactions on the crankshaft radii sub- diamond wheel dresser following acproi;k:- jected to this process. The basic design msdeveloped. This development of a crankshaft also made this process mavea major role in the suc- unpredictable and unreliable because of cessful practice of tangentially rolling interferences which blocked the various crankshaft fillets. shot and media lines of force-inter- ferences such as those caused by the Preliminary Tests Proved Worth counterweights and sidewalls of the of Tangentially Rolled Fillets crankshaft. I In early 1962, Oldemobile's Product Another process considered was under- Engineering Group. was developing a '' cutting as well as rolling of the fillets. new engine of lightweight design, with The equipment and tooling concepts prime importance being givcn to econ- available at that time indicated that this omy of opera tion and weight-to-horlic- process would be impractical. Various power ratio. The dcvclcpmcntal program tests performed showed that distortions did not cail for a major redesign of the resulted which were unacceptable by crankshaft but did require the crankshaft Oldsmobile quality utandards. Distortion to have rr higher factor of safety. The job Fig, I -CRANKSHAFT FATIGUE TEST 9 of the crankshaft bearing nrcas, as well of meeting this requirement was givcn EQUIPMENT,A crankshaft rpcclmcn I, havlnK as the entire crankshaft, would rcquire to the Production Ihgineering Croup, tangentially rolled fillets, war held by a roonant tuning fork assembly 2 whore frcqucncy of vibrn- a straightening operation, which ruicd which has as onc of its reuponsibilitics tion wcrr controlled by an clcctro-magnetic out further devclopmcntal testing. thc proccsuing of cr;inkshafu. Previously excitation unit 3. The tcrt equipment wus opcr- ateci at 200 cyclea per recond to reduce tcrting Concurrent wit11 the Oldsxnobilc pro- tricd rnctlrodu to increirsc the fatigue: lifc timc. A control war dcvclo~~edto operate thc gram to increase crankshaft fatigue life of crankshafts were I-cinvcstigatcd, New excitation unit at the 200 cpr nuturd frequency was a program to obtain Ixttcr control trials were run, new tcotti wcrc made. of the tuning fork arcernbly at a rct load. Data r, obtained from thc tent wcrc plotted (bottom) to of the radii on crankpin diameters. 'l'his I he results wcrc not encouraging, determine the effect varioun fillet hydraulic rolling program, started in 1956 and succcsufully It then was brought to Oldsrnobilc's prcsrurcs had on crankahaft endurance limits. GENERAL MOTORS ENGINEERING JOURNAL controlled by varying the rolling pressure. This meant that reliability couId be T By ROBERT 0. MARKLEWITZ controlled. The results of the preliminary tests were used in a further testing Oldsmobile Division program of a more intense nature. Final Tooling Developed The concept of the present prod#wtion equipment used by Oldsmobile to tangen- tially roll crankshaft fillets was observed Cold rolling operation firsthand in West Germany and France provides 50 per cent where rolling equipment of a similar nature was in operation. increase in fatigue life The first crankshafts experimentally rolled in thc West German plant werc returned to Oldsmobilc for fatiguc tcsts. + LIFE CYCLES , Test resuits indicated that the cranklihafts attention that a manufacturcr in West Fig. 2-EFFECT OF VARIOUS HYDRAULIC ., had excellent fatigue life. Inspired by ROLLING PRESSURES ON CRANKSHAFT Germany had dcvelopcd a process of ENDURANCE. These data were obtained from thcse results, a group of newer model deep rolling fillcts and contours on tests run at a constant bending moment of crankshafts was shipped to the West crankshafts, stecring knuckles, and var- 5,000 in-lb. Confidence bands ..were extremely German manufacturcr. After being clone and werc omitted from the,graph for pur- ious automotive parts that wcrc bcing poses of clarity. returned to Oldsmobile and tested, no produced in France, West Germany, improvemen t in fatigue Iifc was noted, Holland, and Italy. It also was lcarned performed to detcrminc information on The reason for the fatigue lifc increase that the crankshaft fillets bcing rolled physical properties. Samples were used on the earlier model crankshaft and the were undercut. 'l'his application was of from several crankshafts to measure lack of it on the newer model crankshaft interest to Olcismobilc, even though the tensile strength, yield strength, and was not immediately apparent. particular fcaturc of undercutting was enduiance limit (Fig. 3). After reviewing the various tests and not desirable. While static tests were being performed, visually inspecting the fillets that had Thc possibility of developing a mcthod a crankshaft was. comple tcly strain gaged been' rolled, it was discovered that the . for tangentially rolling both the crankpin for dynamic testing. This crankshaft was center section of the fillet radius had not and main journal radii of the Oldsmobile placed in an engine which operated at been cold worked. This was observed in crankshaft was studied and thought various rpm and throttle openings. The photomicrographs taken at a magnifi- feasible. Arrangcrnents were made to recorded traces were analyzed and max- cation of 100X. The problem was ship crankshafts to Wcst Germany for imum operating stresses logged. From resolved into one of rolling tool design. deep fillct rolling, then return thcm to A temporary tooling setup duplicating the fatigue data and material properties I Oldsmobile to undcrgo fatiguc tcsts. obtained, modified Goodman diagrams the West German setup was installed in Preliminary tcsts were performed by were constructed. On these diagrams, the Product Engineering and Dcsign dynamic stresses were plotted and safety Reliability Groups. One of the tcsts for factors dcterrnined . fajigue used a resonant tuning fork .and Based on test results, Oldsmobile knew associated equipmcnt that was sct up to that a crankshaft with tangentially rolled opera tc at 200 cycles per second to rcducc fillets was reliable and would perform testing time (Fig. 1-top). This equipment well. Also, the safety factor could be cnablcd thc computation of endurance limit curvcs (Fig. 1-bottom) in a rnini- mutn of t inw. Once* cranks1i;tft filtip,ti(: lifc rrquirc- ments wcrc cst;d)iisllcd, thc exact p-cssurc nccticd to roll thc fillets had lo be detcrminccl. Several groups of identical crankshafts wcrc rolled at various hychulic pressures. Thesc shafts then wcrc subjected to resonant fatigue tcsts to cvaluatc each group. All tcsts wcrc run at a constant bending moment, which produced failure in a rclativcly Fig. 3-ENDURANCE LIMIT CURVE, The short period of time. Data from the testa steel wed far ex erimentsl crankshafts having Fig, 4-TEMPORARY TOOLING TO ROLL CRANKSHAFT FlLLETS. wcrc plotted to determine the cflcct tansentially .d'hh8 war S.A.E. 1045 modi- The fixture inatallcd hed having e tenrile rtrength oi 105,000 pri and a by Oldrrnobilc to hold the toolin8 for tanrentirlly diffcrcnt rolling prcaaurea had on crank- yield atren t'h of 73,000 pi, Thr hrrdnar, rrnre tolling the filletr 18 rhown poritioned on the shaft cndurancc (Fig, 2), Teats also were w.. 96-99 &. crmkrhrft, THIRD QUARTER 1964 the Oldsmobile plant (Fig. 4). It was 0.065-in. radius (Fig. 8-left), which is the soon discovered that the radius of the mean radius of the Oldsmobile crank- rolling tool had to be identical to the shaft's crankpins and main bearing crankshaft fillet radii and that these radii journals. The rollers are machined using had to be held. It then was realized that a 3/16-in. diameter hole in the center. the crankshah sent from Oldsmobile to This allows the roller to be placed upon West Germany for rolling had been made a mandrel for circular grinding as well with tool room type equipment and their as circular relieving and polishing to fillet radii had been machined to approx- obtain the RMS finish required. The imately 0.060 in. while the original radii of the roliers are relieved 0.014 in. rolling toolslon the German equipment off.center which gives an eccentric relief were 0.070 in.
Details
-
File Typepdf
-
Upload Time-
-
Content LanguagesEnglish
-
Upload UserAnonymous/Not logged-in
-
File Pages5 Page
-
File Size-