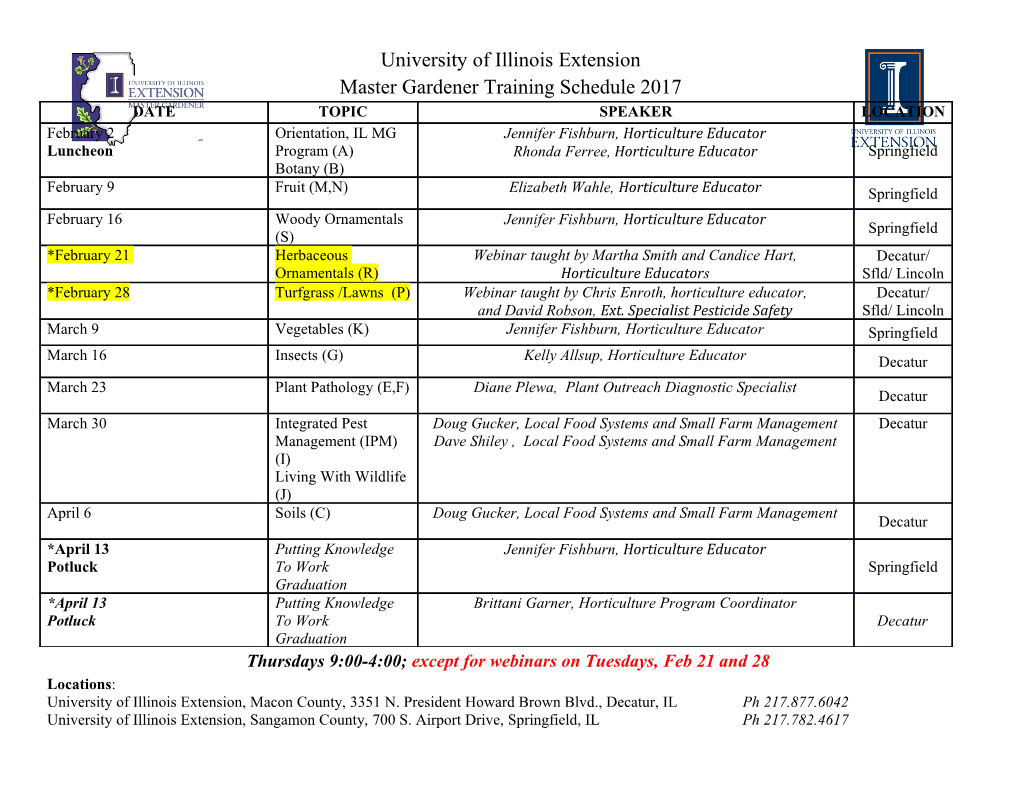
Section 3 Viscoelasticity; (still in scalar form; no tensors yet!) In this section we consider the issue that our material may be viscoelastic. That is the material can exhibit both viscous and elastic properties at the same time. Viscoelasticity is important, particularly for polymers both in the solid and liquid state. The approach is mostly directed at the liquid (melt) state, however the mathematical analysis is also relevant to viscoelastic solids. Viscoelasticity is relevant to polymer melts, concentrated biotech solutions such as xantham gum. It is also relevant to certain foodstuffs (custard, sauces), personal products (shaving cream, lotions, shampoo), and a range of other materials, such as explosives, rocket fuel & certain natural materials. An understanding of viscoelasticity is useful in relation to help understand certain processing issues, in addition it is useful in characterising rheologically complex materials. This is important in terms of quality control. The mathematics involved in the modelling is relatively simple but needs a bit of thought. The modelling is highly suitable for setting Tripos questions! Processing issues where viscoelasticity is important. 1 Processibility. pellets post processing Rheology extruder die Extrusion line must work 24hrs/day CET 2B. Section 3, Viscoelasticity-2011 1 2 Die swell = Di/Do Newtonian = 1.14 Do Di Viscoelastic fluid = 1 – 5 big factor when making tubes 3 Extrusion Instabilities production rate sharkskin – optically observed Usually bad, sometimes good CET 2B. Section 3, Viscoelasticity-2011 2 Rheometers. Cone and Plate Rheometer Torque Cone angle = 14 0 1.5 mm Rotation or oscillation Parallel Plate Rheometer Torque 1 mm Rotation or oscillation 12 mm Couette Rheometer Torque 30 mm Rotation or oscillation 20 mm 22 mm CET 2B. Section 3, Viscoelasticity-2011 3 Viscoelasticity measurement Parallel plate or cone and plate rheometers. A device where ideally the strain or stress is uniform. A) Apply strain , measure stress. Controlled strain rheometer Or B) Apply stress , measure strain. Controlled stress rheometer yield stress – TA Ares, Controlled strain rheometer. £20,000-50,000/machine Upper shaft measures torque Torque measurement Force rebalance transducer Sample Between h ~ 0.3-1 mm plates 25 – 50 mm stepper motor To transducer Lower shaft to (1) Steady stepper Sample (angular velocity) motor Mode 1 (2) Oscillate (angular frequency) Mode 2 γ (strain) To motor Mode 3 (3) Step strain CET 2B. Section 3, Viscoelasticity-2011 4 Different test geometries. Parallel plate geometry Cone and plate geometry h difficult to achieve close fit between plates without damaging equipment r tan h r r r r r φ r φ φ strain γ strain γ h r tanα tanα r ω r ω ω strain rate γ strain rate γ h r tanα tan α both depend on radius both independant on radius γ γ h r tan α Rφ bottom plate R φ bottom plate γ = rφ γ = rφ = φ h r tan α tan α Stain rate depends on r Strain rate independent of r This is the best option, but often parallel plates are used CET 2B. Section 3, Viscoelasticity-2011 5 Rheometers measure Torques; so we need to express Torque in terms of fluid shear stress. r1 r1 Cone and plate = r rdr = 2 r2 dr 0 0 Force 2 3 r 3 1 r1 Parallel plate more tricky because is a function of r. CET 2B. Section 3, Viscoelasticity-2011 6 Rheological “ Rheometric” measurements. We now examine the types of deformation that can be applied using, for example, a Rheometrics controlled strain rheometer. a) Stress growth, steady shear, stress relaxation B Strain Start from rate 0 rest, = 0 time A C Stress Newtonian Stress relaxation time t = 0 t = t Stress growth 1 Steady state t < 0 = 0 t > 0 = o t > t1 = 0 measure stress as a function of time for above strain rate history. (A) Stress growth (Viscoelastic response) (B) Steady shear (Non Newtonian behaviour)? (C) Stress relaxation (Viscoelastic response) Time dependence can be explored Steady shear is the most used deformation, obtain “flow curve” CET 2B. Section 3, Viscoelasticity-2011 7 b) Step strain . At t= o, instantaneously strain material by t , subsequently measure stress relaxation as a function of t . γ0 = γ0 t Step in strain Strain rate 0 time 0 Stress Stress relaxation time t = 0 Relaxation modulus G(t) G(t) = (t) γ0 0 Elastic rubber Viscoelastic response 1/e Often exponential t Characteristic relaxation time -3 3 10 – 10 s CET 2B. Section 3, Viscoelasticity-2011 8 c. Oscillatory “rheometric” deformation Time dependence γ . γ γ0 . γ0 0 strain angular frequency i t Apply = o sin t Strain = oe i t then = o cos t Strain rate = i oe measure = o sin(t + ) variable o = max strain amplitude, typically 0.1 (10%) = angular frequency, typically 10-2 – 103 rad/s ~ 1 hour to complete limit of oscillator the experiment i t = o cos t or = i oe it + = osin(t + ) or = oe = o sin t cos + o cos t sin component of stress component of stress in phase with in phase with Elastic bit! Viscous bit! ’ ’’ Defn = G o sin t + G o cos t α strain So G' = o cos , G" = o sin Pa o o Storage Modulus Loss Modulus Elastic Viscous CET 2B. Section 3, Viscoelasticity-2011 9 = G* γ Complex modulus G* (another way of saying the same thing). it+ t ' " oe = G = G + iG = it t oe Elastic Loss Modulus Modulus So G' + iG" = o e i o now (e I = cos + i sin ) ' cos So G = o G" = o sin N/m2 o o As before So * i t 0G'sin t 0 G''cos t or 0G e Another definition For a given strain, γ if we know and from the rheometer 0 0 dimensions of viscosity 1 G'2 + G"2 2 Complex viscosity = Pas For given , and known o. G’ :- Storage modulus G’’ :- Loss modulus * η :- Complex viscosity These properties capture the viscoelastic properties of a material, but the values will depend on the test frequency ( time scale applied). CET 2B. Section 3, Viscoelasticity-2011 10 Measure o and using TA instruments rheometer or other instrument, then we know the following, for a given 1. G’ storage modulus. 2. G” Loss modulus. 3. *Complex viscosity Storage Modulus 104 G’ * G’ dominates G’ & G’’ (Pa) η* (Pa s) Loss Modulus Cross over G’’ 10-1 G’’ dominates 10-3 103 Angular frequency of oscillation rads/sec Rheometer measures Torque and from this we need shear stress Typical viscoelastic data that we wish to model. (See appendix) 1. Oscillatory Viscoelastic response. linear viscoelastic response ,γ Frequency sweep Strain sweep * 4 G’ G’ 10 G’’ G’’ linear non linear region 10 10-2 102 10-3 103 Strain angular frequency at fixed frequency 0 ~ 1 rads/sec at fixed strain γ0 CET 2B. Section 3, Viscoelasticity-2011 11 2. Steady Shear 104 Linear region Apparent Carreau viscosity a (Pa s) shear thinning 10 . shear rate γ Silly Putty; real data. Silly Putty frequency sweep, strain = 1%, 160204 1000000 100000 10000 * / Pa.s 1000 G' G" 100 G Pa, / ' G " / Pa, 10 1 0.01 0.1 1 10 100 Frequency / rad.s-1 CET 2B. Section 3, Viscoelasticity-2011 12 Modelling of viscoelasticity We are going to build a model that, eventually is going to be able to predict both the linear viscoelastic and non linear shear thinning behaviour of a viscoelastic material such as a polymer melt. Stage 1 The linear viscoelastic part Coupling of linear viscous and elastic elements The Maxwell element series coupling of elastic and viscous component elastic constant g η viscosity linear spring linear dashpot Maxwell often favoured for stress relaxation The Voigt element. parallel coupling viscous γ = γ1 = γ2 = 1 + 2 . = η γ Voigt often favoured for creep (constant stress experiments) We will follow Maxwell, but you should “play with” Voigt model. The Maxwell Model (Differential form) (, γ) 1γ1 2γ2 Local (1, 1) (22) = g = 1 1 2 2 entropy elastic Coupling = 1 = 2 Stress continuity viscous friction of chain CET 2B. Section 3, Viscoelasticity-2011 13 = 1 + 2 Strain additivity 1 = 2 = Then = 1 + 2 Governing ordinary differential equation relaxation times (s) d d 1 = + or = η (Pa s) dt dt g g (Pa) d d 1st order ODE g = + Maxwell equation dt dt where the relaxation time of the element is given by /g, (s) Example. Response of Maxwell element Spring and dashpot in series a..Steady shear . = gγ γ . t = ηγ d = 0 dt t d = 0 Then = dt 0 Linear response, Newtonian. We will have to make the model Non Newtonian later Maxwell model predicts Newtonian behaviour in simple shear.Most complex VE Fluids are shear thinning and so we will have to fix this later. b. Stress relaxation after steady shear d = - t - t dt 0 t . = 0 e γ0 d = - dt . γ γ = 0 t 0 t0 -[t-t ]/ = 0 e 0 . -[t-t ]/ t = ηγ0e 0 t0 All elastic ∞ exponential decay -3 3 All viscous 0 time constant , 10 - 10 CET 2B. Section 3, Viscoelasticity-2011 14 c. Oscillatory motion. (Important and frequently used) Use complex notation it Variables (γ , ) Apply t = oe 0 i (t ) Measure (t) = oe it Strain rate t = i oe * i t i t (t) = G 0 e = G' + iG'' 0 e d t = iG' + iG" ei t dt o d d Remember, g = + , so, Maxwell equation dt dt Substitute for γ, i t i t 1 it gi e = iG' + iG" e + G' + iG " e ] o o o Yields 2 2 g g * g G' = 2 2 , G" = 2 2 , = 1/2 1 + 1 + 1 + 22 0 G’ 0 0 G’’ 0 0 η* = g = η ∞ G’ g ∞ G’’ 0 ∞ η* 0 Elastic domination Newtonian* Plateau G’ Elastic G’ & G’’ (Pa) η* (Pa s) Shear thinning G’’ complex viscosity viscous cross over domination Loss angular frequency CET 2B.
Details
-
File Typepdf
-
Upload Time-
-
Content LanguagesEnglish
-
Upload UserAnonymous/Not logged-in
-
File Pages36 Page
-
File Size-