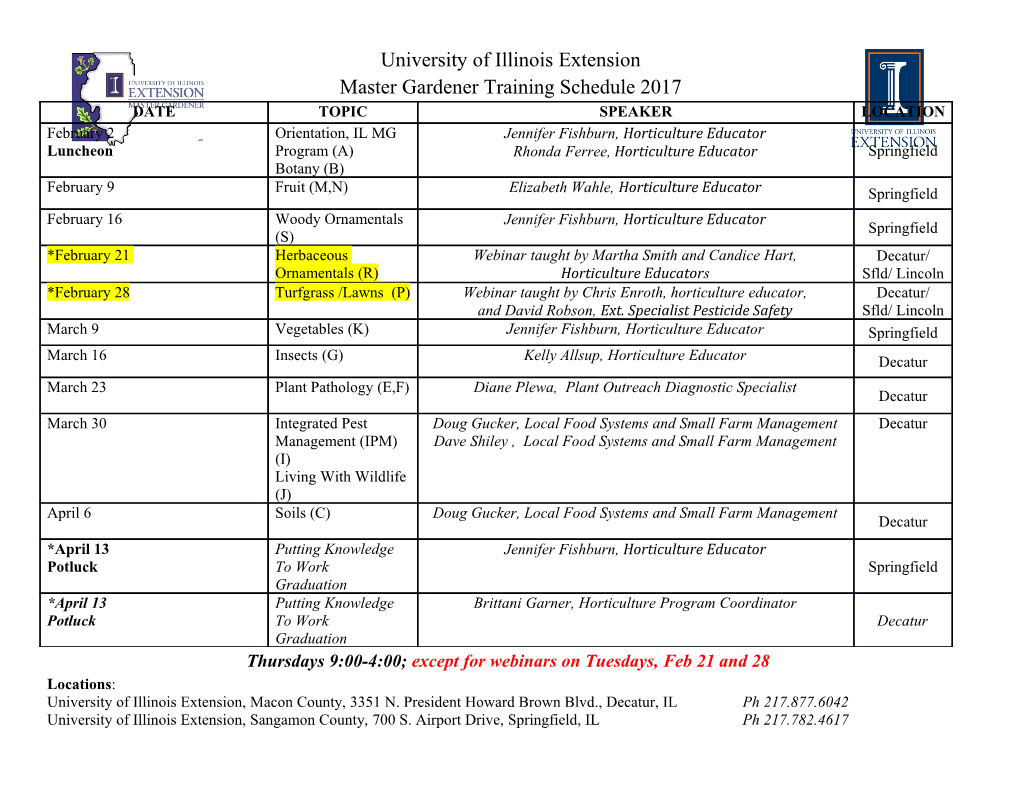
technical trends Longer-lasting low-cost diamond tools Ken Brookes discusses an investigation into diamond impregnated tools for stone and civil engineering which took place at the EPMA 2011 Annual Conference in Barcelona, Spain. iamond impregnated, metal- comprehensive paper on Dry cutting better understanding of the cutting process bonded cutting tools have diamond impregnated tools based on with these types of tools. been around for well over water-atomised powders. Prealloyed powders for DIT, available half a century, and the As the author explained, for the previ- since 1997, had obtained a significant posi- Dmany and varied metal binders have been ous 15 years PM research into diamond tion in the market, particularly in Europe, the subject of much empirical research. impregnated tools (DIT) for stone and civil where more than 40% of the Co had been Unlike gem diamonds, industrial diamond engineering applications had targeted the substituted in these new powders. These powders have always been remarkably development of pre-alloyed powders and were mainly based on the systems Fe/Co/Cu inexpensive, whilst some of the more the introduction of “free” or pressureless and Fe/Cu. exotic binders have become comparatively sintering. The aim was a reduction of Co For some applications, the lower price of costly. Required properties are slightly content in the DIT binder and a signifi- synthetic diamond made the bond the most unusual but critical. The binder metal cant decrease in production costs through expensive component of a DIT, encouraging should be easy to sinter, hold diamond employing pressureless sintering instead of the use of pre-mixed bonds from cheaper particles firmly, and be sufficiently wear- HIP or hot pressing (the particular investi- powders. In parallel with this research activ- resistant to grip each diamond until this gation described in this paper apparently ity, Iturriza had explored the possibility of superhard component is worn away, but employed only hot pressing, and it was not improving the competitiveness of diamond- soft enough to expose new diamond sur- made clear whether a change to pressureless impregnated tools by using cheap water- faces as and when needed. sintering was envisaged). Two additional atomised powders as raw material in bond One aspect of current research in lines of R&D activity had been to increase formulations. His investigation therefore this area was discussed by Dr Iñigo productivity in high-pressure/high-tem- followed three experimental mixtures of Itumiza of CEIT and the University of perature diamond synthesis and to reduce water-atomised powders, including densifi- Navarra, San Sebastian, Spain, in his the cost of industrial diamond, backed by cation, chemical interaction with diamond, hardness and wear resistance of these mix- Table 1. Chemical characteristics and density of experimental powder mixtures. tures processed by hot pressing, as well as Main components Alloying elements Theoretical density g/cm3 the performance of prototype cutting tools based on them. M1 Fe/Cu Sn. Ni, Mo 8.21 Three experimental powder mixtures M2 Fe/Cu Sn, Ni. Mo 8.22 (M1, M2 and M3) were prepared as Fe/ Cu-base materials, blending different types M3 Fe/Cu Sn, Cr, Mo 8.16 of water-atomised powders, as summarised in Table 1 (actual compositions were not provided by the author). Base materials were mixed with graphite in two different pro- portions, 0.5 and 0.8 wt%. Water-atomised powders were blended in a Turbula T2C mill for 15 min at 30 rev/min, but for the graphite addition speed was increased to 20 rev/min to avoid segregation. Metallic powder mixtures were, as needed, subse- quently mixed with different qualities of synthetic diamond particles for 15 min at 20 rev/min. Nominal grit size of the diamond Figure 1. The effect of powder consolidation temperature on (a) density and (b) hardness for was 40/50 mesh and concentration between the different mixtures. C12 and C14. Green compacts 6 x 7 x 20 30 MPR May/June 2012 0026-0657/12 ©2012 Elsevier Ltd. All rights reserved. Figure 2. SEM micrographs corresponding to M1, M2 and M3, Figure 3. SEM micrographs corresponding to the base materials with processed by hot pressing at 875°C. graphite additions, processed by hot pressing at 875°C. mm were made by cold pressing the powder grit applying 4 N at steps of 15min. Finally, in the highest hardness after cooling in the under 200 MPa, achieving a green density of prototype 230 mm diameter circular saw hot pressing cycle. The increase in hardness 70% TD (theoretical density). blades were produced at CEIT with powder was associated with sintering temperatures Hot pressing temperatures ranged from family M1, to assess cutting performance between 825 and 875°C, where austenitisa- 750 to 875°C, with 3 min holding times, on granite. tion took place for M3 + graphite, allowing using vacuum/inert atmosphere in the The evolution of both density and hard- carbon diffusion to the iron-based matrix following sequence: linear heating at 4K/s ness against hot-pressing temperature was and strengthening it. Hardness was of up to 360°C (10 MPa applied pressure), reported for all the materials in Figure 1. relevant importance when the metallic sys- linear heating at 2 K/s up to 450°C (20 The data confirmed excellent sinterability tem was to be used as matrix for diamond MPa applied pressure), isothermal step of the powders; 97% of theoretical density cutting tools, because it was commonly of 30 seconds (30 MPa applied pressure), being achieved at temperatures as low as associated with yield strength and wear linear heating at 2 K/s up to sintering 800°C. Hot pressing within the tempera- resistance. The highest hardness was found temperature (30 MPa applied pressure). ture range 800-875°C resulted in near fully at 875°C for all dense mixtures, so this Both equipment and processing were dense materials. There were no data for temperature was selected to process and totally industrial in order to make easier temperatures above 875°C due to the huge test the experimental powder mixes. At this the reproduction of laboratory results amount of burr generated in the samples temperature the hardness after hot press- in the factory. Rockwell B hardnesses of after hot pressing. Composition differences ing ranged from 90 to 112 HRB except for sintered specimens were measured and the between base powders resulted in significant M3. This hardness range was considered microstructures of matrix and diamond increase in hardness, from 65 to 90-92 HRB; adequate for most applications of diamond surfaces studied by scanning electron Ni/Cu/Mo alloying systems (M1 and M2) tools for dry cutting. microscopy. Semiquantitative chemical were more effective in this regard than Mo/ Figure 2 shows the microstructures analysis was carried out on the surfaces of Cr (M3). This behaviour changed totally of the consolidated iron-based dense polished segments by EDS and wear tests with the addition of carbon to the mixtures. specimens obtained by hot pressing at to measure the abrasion resistance of the With Cr and Mo as alloying elements, the 875°C. Two major phases can be observed bonds. These tests were made on three addition of graphite allowed M3 to take in the microstructures. The bronze-rich samples of each material on SiC 120 paper advantage of its high hardenability, resulting phase appears in white contrast whereas Figure 4. Wear test results for the different mixtures indicated, sintered by hot pressing at 875°C. metal-powder.net May/June 2012 MPR 31 Because the results of hardness and wear resistance tests were compatible with the targeted applications, bond/diamond interactions were analysed. The diamond grade used first was ISD1200, synthetic and uncoated. Parameters included 40/50 mesh (300-420 µm) grain size and C12 Figure 5. Extracted diamonds after sintering at 875°C with M2 mixture. concentration, 3 vol% of diamond. These mixtures were hot pressed at 875°C. After sintering, colour and surface morphology of the extracted diamonds were chosen to characterise diamond stability. Figure 5 shows colour changes in the diamond extracted from M2 mixtures, also observed in diamonds extracted from M1 mixes. With greater carbon content in the mix- ture, less apparent damage was seen in the diamonds. Diamonds processed with M3 powders did not show this appearance, all becoming black. Figure 6 shows SEM micrographs of the diamond particles at higher magnification. Figure 6. SEM micrographs of diamonds collected from segments sintered at 875°C with the Diamond quality was quite low, impurity indicated materials. level high and most of the diamonds frac- the iron-rich phase is in grey contrast. powder, because of their widespread use tured or showed crystallographic defects. Backscattered electron micrographs also in diamond impregnated tool fabrica- Only slight degradation was observed in showed the presence of an additional phase tion. Figure 4 shows volume loss versus the diamond surfaces, implying that better in darker contrast, identified as metal test time. Three samples sintered at 875°C grades would not suffer significantly. oxides in some cases and residual porosity were tested for each material with reported The presence of carbon in the matrix in others. Oxygen content after sintering values being the average for each group of caused differences to the diamond surface was 0.41 wt% in M1 specimens. The main three. The three hardest combinations were morphology, as predicted in Figure 5. phases had limited mutual solubility even also the most resistant to wear. All the new Damage to the diamond surface was more at sintering temperature. This fact helped mixtures were more wear-resistant than extensive when there was no carbon in the to control grain growth, especially in solid- the commercial powders.
Details
-
File Typepdf
-
Upload Time-
-
Content LanguagesEnglish
-
Upload UserAnonymous/Not logged-in
-
File Pages4 Page
-
File Size-