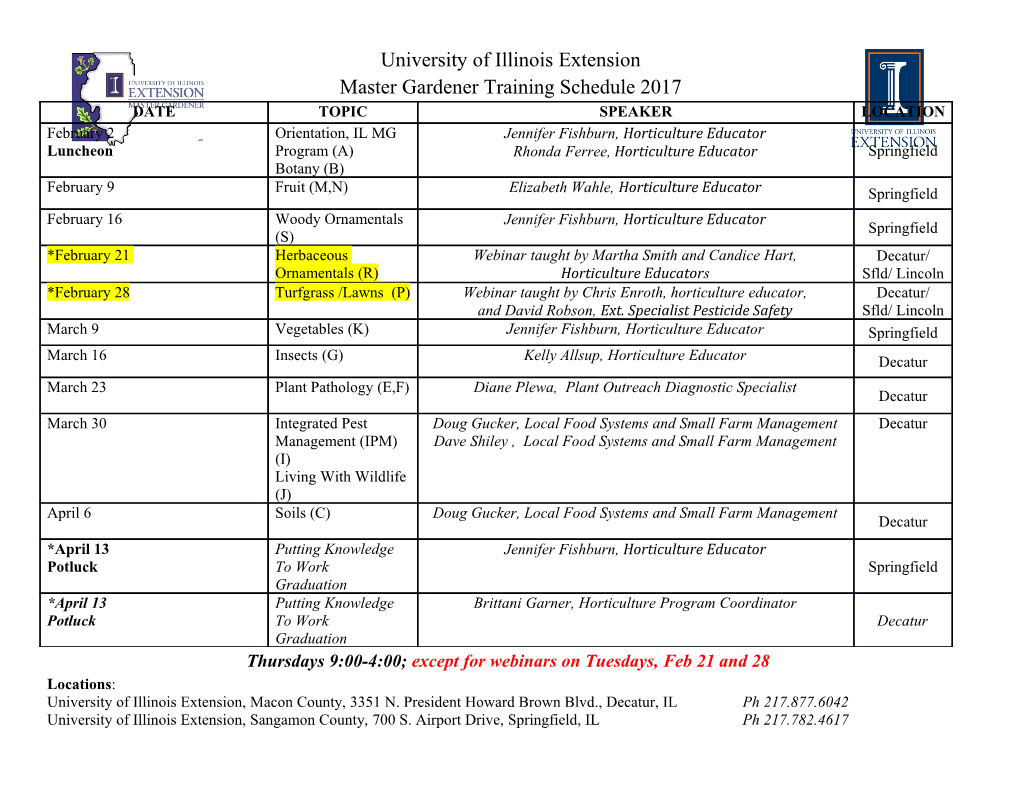
“Mircea cel Batran” Naval Academy Scientific Bulletin, Volume XIX – 2016 – Issue 1 Published by “Mircea cel Batran” Naval Academy Press, Constanta, Romania // The journal is indexed in: PROQUEST / DOAJ / DRJI / JOURNAL INDEX / I2OR / SCIENCE LIBRARY INDEX / Google Scholar / Crossref / Academic Keys / ROAD Open Access / OAJI / Academic Resources / Scientific Indexing Services / SCIPIO ABOUT THE MAINTENANCE OF THE RADIAL AND AXIAL SHAFT BEARINGS FROM PROPULSION PLANT WITH GAS AND STEAM TURBINES Ion Adrian GIRBA1 Dorin-Silviu BANU2 Anastase PRUIU3 Daniel MARASESCU4 1PhD attendee Eng. Military Tehnical Academy 2PhD attendee Eng. Military Tehnical Academy 3Professor PhD Eng., Marine Engineering and Naval WeaponsDepartament 4PhD attendee Eng., Marine Engineering and Naval WeaponsDepartament Abstract: The paper presents the main rules imposed by classification societies for design the shaft for propulsion plant with gas and steam turbines. It also analyzes the main maintenance activities to ensure their safe operation. Key words: turbine, bearing, maintenance, vibration. INTRODUCTION The bearings design and location should result in The naval gas turbines were and are used in a longer in service, reliability and economic propulsion plants on military ships. As time goes efficiency. To reach this benchmark must consider the applied research in the field of naval it showed the following factors: that gas turbines can be used in propulsion - load and speed; installations in combination with other gas - working temperature; turbines,or combined with diesel engines or steam - lubrication; turbines which can be equipped comercial ships - shaft location; also, like fast transient passenger or cargo ships, - service time; LNG ships (where in combination with steam - assembly/disassembly; turbines, gas turbines have developed a very - noise; good yield reported at fuel consumption and - environmental conditions. performance of speed and power developed). Plain bearings are divided into two categories Naval propulsion plants with gas turbines ( depending on the direction of the loading force: NPPGT) experienced a continuous development - radial bearings; on ships, found it separately or in multiple - thrust bearings. combined cycles configurations, depending on the Radial bearings according to the power turbine operational characteristics of the vessel. The main are : constructive configurations of NPPGT are: • lubricated bearings with rings used up to 5 bars - CODOG(COmbined Diesel Or Gas turbine), pressure at low power turbine at speed slip-one - CODAG (COmbined Diesel And Gas up to 12 ms-1; turbine), • bearings lubricated under pressure, having high - CODELAG (COmbined Diesel-Eectric and sliding speeds that can reach about 60÷80 ms-1, Gas turbine ), used in high power turbine and thus incurring high - COGOG (COmbined Gas Or Gas turbine), pressures that can reach a average pressure of - COGAG (COmbined Gas And Gas turbine), 20 bar on the journal. - COGAS (COmbined Gas And Steam turbine) • The efficiency of these two types of bearings - COGES (COmbined Gas Electrical Steam have two basic elements, the material from which turbine). They are used on board of commercial are made the two bodies, the bearings liner and and military vessels. Naval propulsion plants type the journal in rotation, and the quality of the COGAS, according to research in the field, can lubricant (oil in turbines case). Considering these yield up to 60% . elements, based on hydrodynamic theory of THE BEARINGS USED IN GAS AND STEAM lubrication, were established the relations through TURBINES MANUFACTURE which one can calculate the lubricant film The bearings usually are plain bearings for large pressure distribution self-supporting. turbines, but becouse the naval gas turbines are Since the oil layer which is in contact with the derived from the turbines used in aviation the bearing (bush) has zero velocity, and the one bearings we will find coud be rolling bearings. which is in contact with the journal has the speed thereof, the intermediate layers have different 214 DOI: 10.21279/1454-864X-16-I1-038 © 2015. This work is licensed under the Creative Commons Attribution-Noncommercial-Share Alike 4.0 License. “Mircea cel Batran” Naval Academy Scientific Bulletin, Volume XIX – 2016 – Issue 1 Published by “Mircea cel Batran” Naval Academy Press, Constanta, Romania // The journal is indexed in: PROQUEST / DOAJ / DRJI / JOURNAL INDEX / I2OR / SCIENCE LIBRARY INDEX / Google Scholar / Crossref / Academic Keys / ROAD Open Access / OAJI / Academic Resources / Scientific Indexing Services / SCIPIO speeds between zero and the journal shaft speed. Due to the rotation of the spindle, the lubricant layer is driven in the interstice between the spindle and bushings. Because the surface between the bearing and the journal shaft is tapering in interstitial area, there is an increase of oil pressure generating hydrodynamic force for self-supporting which interrupting contact between the journal and bearing liner. Thus according to oil pressure whitch generates hydrodynamic force, calculate the load force of the journal, the eccentricity of journal in bearing and bearing oil film thickness must be at least greater than the sum between maximum roughness of bearing and spindle surfaces. In the figure 1a is shown the pressure distribution on the circumference of the bearing, and in the figure 1b is shown the distribution of pressure along the length of the bearing liner. Fig.1b – Contact pressure distribution along the length (l) [9] In some cases for a beter eficiency stability of the journal in bearing liner and rotor vibration damping was chosen the plain bearing in the lemon shape which has two bearing surfaces, both above and below. The average pressure of the bearing is determined by the relationship (1): , (1), where pa is admissible pressure So can do the calculation of wear: (2), Fig.1a – the pressure distribution on the circumference of the bearing liner [9]; - Vu - the volume of material removed by wear,or n-journal speed;d – the inner diameter of the wear volume accepted; - k- coefficient expressing the proportionality bearing liner; dj- diameter of the journal (fig. b); between the material couple and lubrication P- radial force or load force of journal; hmin – the conditions; minimum oil film thickness;hmax – maximum oil - P - radial force resulting from the relationship (1) film thickness; p- average pressure; pmax- maximum pressure; e- eccentricity ; - L – the length done by the journal in the relative motion in relation to bearing during operation period imposed. (3), (4), represent the journal speed, where n is the journal speed and, iar Lh represents operating period imposed The equation (1) becomes: 215 DOI: 10.21279/1454-864X-16-I1-038 © 2015. This work is licensed under the Creative Commons Attribution-Noncommercial-Share Alike 4.0 License. “Mircea cel Batran” Naval Academy Scientific Bulletin, Volume XIX – 2016 – Issue 1 Published by “Mircea cel Batran” Naval Academy Press, Constanta, Romania // The journal is indexed in: PROQUEST / DOAJ / DRJI / JOURNAL INDEX / I2OR / SCIENCE LIBRARY INDEX / Google Scholar / Crossref / Academic Keys / ROAD Open Access / OAJI / Academic Resources / Scientific Indexing Services / SCIPIO (5), and: (6) For acceptable wear volume Vu and an operating period imposed Lh resulting allowable bearing liner value represented by the product pma νa . Calculation of wear is to compare the actual value with which admissible: [MPa·ms-1] (7) , where the permissible values given in the literature are based on the bearing material. Since the power consumed by friction is found in the relation pmν , it can do a calculation of the average temperature. Thus for fluid friction, a convetional coefficient of friction μ is defin. Figure 2 - Hydrodynamic Pivoted Shoe Journal (8), Bearing [12,pg.5] For very heavy shafts is important the positioning η – dynamic viscosity of the lubricant; mode of pivots so loading force on the journal ν – speed spindle; does not act between the journal shoes. Thus, in pm – average pressure; figure 3 it can be seen the effects of the conditions hmin – the thickness of the fluid layer. described above, it prevents formation of the bearing film and cause damage to the bearing and (9) shaft, the journal shoes surfaces will corrode, and eccentricity will increase. Relocation shaft in a (10), pivoted shoe journal bearing while rotating between journl shoes will produce vibrations (figure 3 – right position). - Ff - the power consumed by friction; - t – average temperature; - t0 – ambient temperature; - ta – allowable temperature; - μ – friction coefficient; - K – overall coefficient of heat transfer through the bearing housing; - A – the outer surface of the bearing body in contact with air. At high power turbines can meet journal bearings with two pivoted shoe journal bearing surfaces , or three, four or more surfaces for high speeds. In Fig.3 – Corectly pivots bearing pozition mounting figure 2 is a pivoted shoe journal bearing, which for eliminate high vibrations and bearing and proved to be the best solution for the elimination shaft damanges [7] of the phenomenon of oil whirl.. Axial bearings are used for taking over the axial forces acting on the rotor. They may be: • at high power turbine bearings rings with one disc; • at low power turbines, bearings with shaft collar on each side of the liner thrust bearing for withstanding axial. 216 DOI: 10.21279/1454-864X-16-I1-038 © 2015. This work is licensed under the Creative Commons
Details
-
File Typepdf
-
Upload Time-
-
Content LanguagesEnglish
-
Upload UserAnonymous/Not logged-in
-
File Pages10 Page
-
File Size-