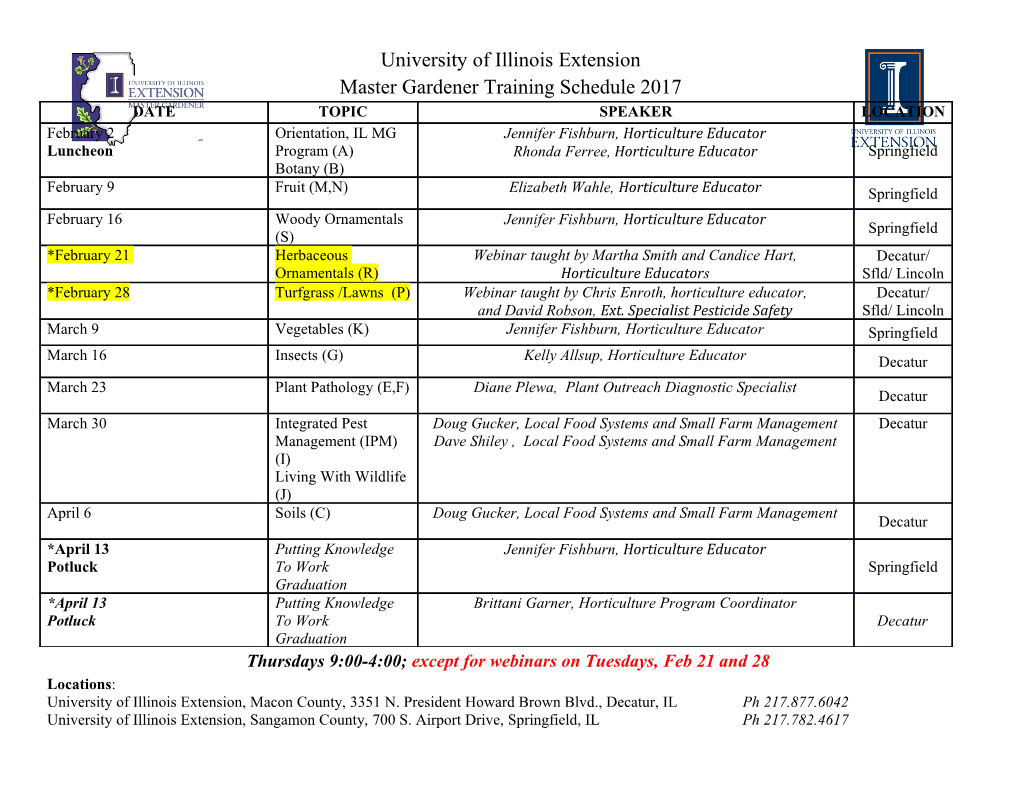
Chapter 5 Principles of Force Convection 5.1 Introduction The preceding chapters have considered the mechanism and calculation of conduction heat transfer. Convection was considered only insofar as it related to the boundary conditions imposed on a conduction problem. We now wish to examine the methods of calculating convection heat transfer and, in particular, the ways of predicting the value of the convection heat-transfer coefficient h. Our development in this chapter is primarily analytical in character and is concerned only with forced-convection flow systems. Subsequent chapters will present empirical relations for calculating forced-convection heat transfer and will also treat the subjects of natural convection. 5.2 Viscous Flow 5.2.1 Flow on a flat plate (external flow) Consider the flow over a flat plate as shown in Figures 5.1 and 5.2. Beginning at the leading edge of the plate, a region develops where the influence of viscous forces is felt. These viscous forces are described in terms of a shear stress between the fluid layers. If this stress is assumed to be proportional to the normal velocity휏 gradient, we have the defining equation for the viscosity, = 5.1 푑푢 The휏 휇region푑푦 of flow that develops from the leading edge of the plate in which the effects of viscosity are observed is called the boundary layer. Some arbitrary point is used to designate the y position where the boundary layer ends; this point is usually chosen as the y coordinate where the velocity becomes 99 percent of the free-stream value. Initially, the boundary-layer development is laminar, but at some critical distance from the leading edge, depending on the flow field and fluid properties, small disturbances in the flow begin to become amplified, and a transition process takes place until the flow becomes turbulent. The turbulent-flow region may be pictured as a random churning action with chunks of fluid moving to and fro in all directions. The transition from laminar to turbulent flow occurs when = = > 5 10 (transiant) 푢∞푥 휌푢∞푥 5 휐 5 휇10 푅푒(laminar)∗ 5 푅푒Where≤ ∗ = free stream velocity, m/s. 푢 ∞= distance from leading edge, m. 2 푥 = =kinematic viscosity, m /s. 휇 휐 휌 = 5.2 푢∞푥 푅푒 푥 휐 Figure 5.1: Sketch showing different boundary-layer flow regimes on a flat plate. Figure 5.2: Laminar velocity profile on a flat plate. 5.3 Laminar Boundary Layer on a Flat Plate Consider the elemental control volume shown in Figure 5.3. We derive the equation of motion for the boundary layer by making a force-and-momentum balance on this element. To simplify the analysis we assume: 1. The fluid is incompressible and the flow is steady. 2. There are no pressure variations in the direction perpendicular to the plate. 3. The viscosity is constant. 4. Viscous-shear forces in the y direction are negligible. Figure 5.4 Elemental control volume for force balance on laminar boundary layer. The mass continuity equation for the boundary layer. + = 0 5.3 T휕푢he momentum휕푣 equation of the laminar boundary layer with constant properties. 휕푥 휕푦 + = 2 5.4 휕푢 휕푢 휕 푢 휕푝 2 휌 �푢 휕푥 푣 휕푦� 휇 휕푦 − 휕푥 Figure 5.5: Elemental control volume for integral momentum analysis of laminar boundary layer. The mass flow through plane 1 in Figure 5.5 is = 퐻 푚Voṅ Kármán∫0 휌푢 approximate푑푦 solution of equations 5.3 and 5.4 gives . = 4 64푥 1 �2 훿 푅푒푥 The exact solution of the boundary-layer equations = 5.5 5푥 1 �2 훿 푅푒푥 The velosity profile of the stream in x-direction within the baundary layer is given by: = 5.6 푢 3 푦 1 푦 3 ∞ And푢 the2 훿 energy− 2 �훿 �equation of the laminar boundary layer is: + = + 2 5.7 휕푇 휕푇 휕 푇 휇 휕푢 2 2 푢 휕푥 푣 휕푦 훼 휕푦 휌푐푝 �휕푦� For low velocity incompressible flow, we have + = 2 5.8 휕푇 휕푇 휕 푇 2 There푢 휕푥 is푣 a휕푦 striking훼 휕푦 similarity between equation 5.8 and the momentum equation for costant pressure, + = 2 5.9 휕푢 휕푢 휕 푢 2 푢 휕푥 푣 휕푦 훼 휕푦 Example 5.1: Mass Flow and Boundary-Layer Thickness -3 Air at 27◦C and 1 atm flows over a flat plate at a speed of 2 m/s. Calculate the boundary-layer thickness at distances of 20 cm and 40 cm from the leading edge of the plate. Calculate the mass flow that enters the boundary layer between = 20 cm −5 and = 40 cm. The viscosity of air at 27◦C is 1.85×10 kg/m· s. Assume푥 unit depth in the푥 z direction. Solution The density of air is calculated from . 3 = = = 1.177 kg/m ( )( 5 ) 푝 1 0132∗10 푅푇 287 27+273 휌 = 푢∞푥 . 푅푒푥 = 20휐 = = = = 25,448 At : . × 푢∞푥 휌푢∞푥 1 177∗2∗0 2 푥 . 푥 = 40 푐푚 푅푒 = 휐 = 휇 1 85=1050−5,896 At : . × 휌푢∞푥 1 177∗2∗0 4 The푥 boundary푐푚 layer푅푒푥 thickness휇 is1 calculated85 10−5 from: . = 4 64푥 1 �2 훿 푅푒푥 . At = 20 , = = 0.00582 m. ( ) 4 64∗0 2 1 �2 푥 푐푚 훿 25488. At = 40 , = = 0.00823 m. ( ) 4 64∗0 4 1� 푥 푐푚 훿 50896 2 To calculate the mass flow that enters the boundary layer from the free stream between = 20 cm and = 40 cm, we simply take the difference between the mass flow in the푥 boundary layer푥 at these two x positions. At any x position the mass flow in the boundary layer is given by the integral = 훿 푚̇ ∫0 휌푢 푑푦 = 3 푦 1 푦 3 ∞ 2 훿 2 훿 푢 푢 − 3� � 1 3 5 = = 2 2 8 훿 푦 푦 ∞ ∞ 0 푢 훿 − 훿 푢 훿 푚̇ =∫ 휌 ( � )�=푑푦(1.177휌 2(0.00823 0.00582) = 0.00354 kg/s 5 5 ∞ 40 20 ∆푚̇ 8 휌푢 훿 − 훿 8 ∗ − 5.4 Thermal boundary layer Just as the hydrodynamic boundary layer was defined as that region of the flow where viscous forces are felt, a thermal boundary layer may be defined as that region where temperature gradients are present in the flow. These temperature gradients would result from a heat-exchange process between the fluid and the wall. Consider the system shown in Figure 5.6. The temperature of the wall is , the temperature of the fluid outside the thermal boundary layer is , and the thickness푇푤 of the thermal boundary layer is designated as . At the wall, the푇∞ velocity is zero, and the heat transfer into the fluid takes place by훿 conduction.푡 Thus the local heat flux per unit area is: = 5.10 푞 휕푇 퐴 −푘 휕푦� From Newton’s푤푎푙푙 law of cooling = ( ) 5.11 푞 퐴 푤 ∞ whereℎ h 푇is the− 푇convection heat-transfer coefficient. Combining these equations, we have = 휕푇 ( ) 5.12 −푘휕푦�푤푎푙푙 ℎ 푇푤−푇∞ Figure 5.6: Temperature profile in the thermal boundary layer. Then we need only find the temperature gradiant at the wall to evaluate . Therefore, the temperature distribution is: ℎ = = 5.13 휃 푇−푇푤 3 푦 1 푦 3 휃∞ 푇∞−푇푤 2 훿푡 − 2 �훿푡� The thermal boundary layer can calculated from the equation below: = 1 1 5.14 . 3 �3 훿푡 1 −1 푥표 �4 �3 훿 1 026 푃푟 � − � 푥 � � When the plate is heated over the entire length, = 0, and 표 = 푥 . 5.15 훿푡 1 −1 �3 Where훿 1 026 the푃푟 Prandtl number is dimensionless when a consistent set of units is used: = = = 5.16 휇 휐 �휌 푐푝휇 푘 푃푟 훼 �휌푐푝 푘 The local convective heat transfer coefficient is calculated from the equation as below: = 0.332 1 −1 5.17 1 3 �3 1 푢∞ �2 푥표 �4 �3 ℎ푥 푘 푃푟 � 휐푥 � � − � 푥 � � The equation may be nondimensionalized by multiplying both sides by , producing the 푥 dimensionless group on the left side, 푘 = 5.18 ℎ푥푥 푥 called푁푢 the Nusselt푘 number afterWilhelm Nusselt, who made significant contributions to the theory of convection heat transfer. Finally, = 0.332 1 −1 5.19 3 �3 1 1 푥표 �4 �3 �2 푁푢푥 푃푟 푅푒푥 � − � 푥 � � or, for the plate heated over its entire length, = 0 and 표 = 0.332 푥 0.6 < > 50 5.20 a 1 1 �3 �2 푁푢푥 푃푟 푅푒푥 푃푟 Equation (5.20 a) is applicable to fluids having Prandtl numbers between about 0.6 and 50. It would not apply to fluids with very low Prandtl numbers like liquid metals or to high- Prandtl-number fluids like heavy oils or silicones. For a very wide range of Prandtl numbers, Churchill and Ozoe have correlated a large amount of data to give the following relation for laminar flow on an isothermal flat plate: . = 1 1 > 100 5.20 b �2 �3 0 3387.푅푒푥 푃푟 1 푥 2 �4 푥 푁푢 0 0468 �3 푅푒 푃푟 �1+� 푃푟 � � Equations (5.17), (5.19), and (5.20 a) express the local values of the heat-transfer coefficient in terms of the distance from the leading edge of the plate and the fluid properties. For the case where = 0 the average heat-transfer coefficient and Nusselt number may be obtained by푥표 integrating over the length of the plate: = 퐿 = 2 5.21 ∫0 ℎ푥푑푥 � 퐿 푥=퐿 assumingℎ ∫0 푑푥 the heatedℎ section is at the constant temperature . For the plate heated over the entire length, 푇푤 = = 2 5.22 ℎ�퐿 푁푢Or���� 퐿 푘 푁푢푥=퐿 = = 0.664 5.23 ℎ�퐿 1� 1 2 �3 퐿 퐿 Where:푁푢���� 푘 푅푒 푃푟 = 5.24 휌푢∞퐿 퐿 For푅푒 a plate휇 where heating starts at = , it can be shown that the average heat transfer coefficient can be expressed as푥 푥표 = 2 3� 푥표 4 1−� �퐿� 표 ℎ �푥 −퐿 ℎ푥=퐿 � 퐿 퐿−푥표 � In this case, the total heat transfer for the plate would be = ( )( ) 표 The푞푡표푡푎푙 foregoingℎ�푥 −퐿 analysis퐿 − 푥표 was푇푤 based− 푇∞ on the assumption that the fluid properties were constant throughout the flow.
Details
-
File Typepdf
-
Upload Time-
-
Content LanguagesEnglish
-
Upload UserAnonymous/Not logged-in
-
File Pages39 Page
-
File Size-