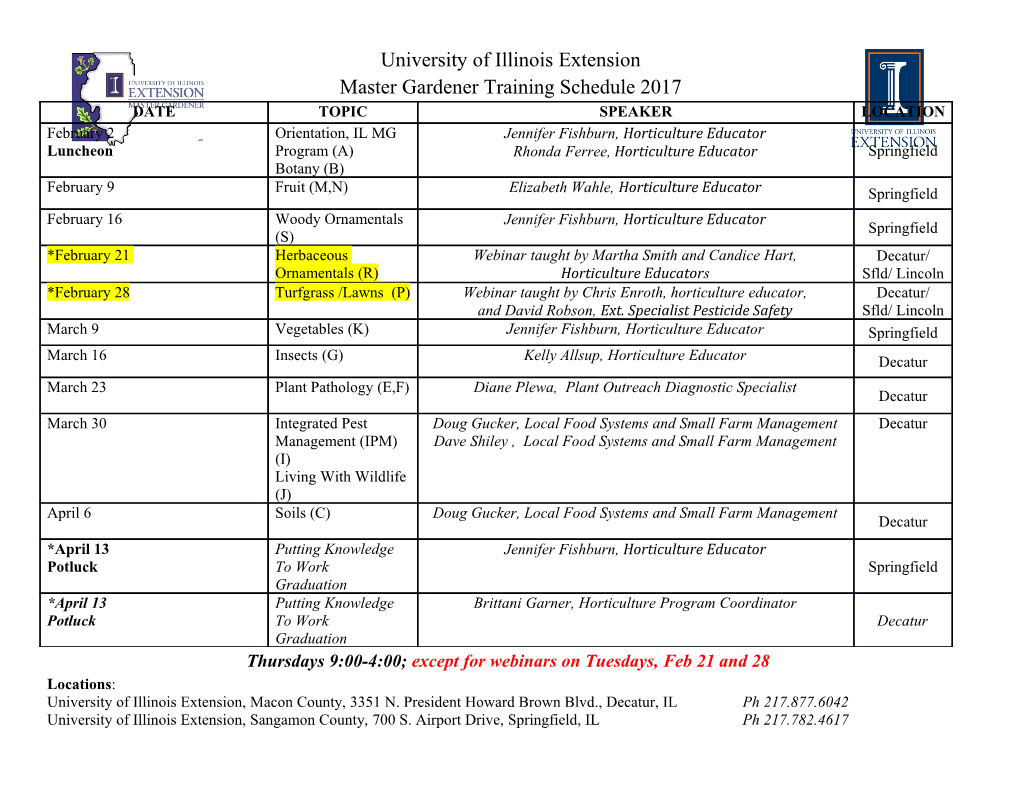
MID-SIZED NEW GENERATION: RECIPROCATING INTERNAL COMBUSTION ENGINES OR COMBUSTION TURBINE? Presented to Power-Gen International 2017 Melanie J. Schmeida, P.E., Louis Perry Group, a CDM Smith Company 165 Smokerise Dr., Wadsworth, OH 44281, [email protected], 330-760-0645 Abstract For any new natural gas-fired power generation project, a developer or owner must wrestle with the question “what is the right technology?”. For very small projects, the answer often defaults to reciprocating engines. For very large projects, it is combustion turbines in a combined cycle configuration. But for the facilities in between, the right answer is not always so clear. This paper compares reciprocating engines to simple cycle combustion turbines for a nominal 50 MW gas-fired plant in the Midwest, connected to the electric grid. It evaluates capital costs, operating costs, reliability, operational flexibility, system responsiveness to dispatch requirements, and site considerations. Background Inexpensive shale gas has resulted in an increased interest in natural gas-fired power generation in many parts of the nation. The profusion of this new generation, its implications on the utility and distributed generation markets, and project viability are topics of many publications. For the purposes of this paper, it is sufficient to say new natural gas-fired electricity generation is attractive for an owner in the Midwest, and evaluation of their needs indicates approximately 50- MW electric generating capacity is the appropriate size. Additionally, the purpose of the facility is electric generation only; no thermal energy in the form of steam or hot water is being considered. For all generating facilities, the best-fit technology needs to be evaluated carefully. Developers and owners are making large investments, and need to consider many factors to ensure appropriate returns on that investment. However, conventional wisdom would dictate that a “small” natural gas-fired generating facility is best served by reciprocating internal combustion engines (RICE), as it would be expected to operate intermittently, and that a “large” generating facility is best served by a combined cycle system(s) as it would be expected to operate nearly continuously. But what about this 50-MW facility, which is “mid-sized”? What is the appropriate technology for this installation? When this study was first contemplated, the primary technology options were intended to be RICE, a simple cycle combustion turbine (CT), and a combined cycle system. However, we quickly determined that the combined cycle arrangement was not going to be cost effective. It is conceivable that a combined cycle plant might be the right choice for a mid-sized facility if the Page 1 of 13 thermal energy can be used and/or the facility will run continuously, but with our premise that the thermal energy has no value beyond additional electric generating capacity, the payback for the additional capital expense was not reasonable. Therefore, this paper focuses on a comparison between RICE and simple cycle CT for this application, contemplating the major questions of: • How much should it cost? • How will it be used? • Where will it be located? • How much will it actually cost? It is also worth noting that, while this study utilizes a specific example site, the items evaluated can be applied to any project. How Much Should It Cost? As a starting point in the evaluation, typical engineering, procurement, and construction (EPC) costs for the technologies were evaluated to establish viability. Property costs were excluded, as the site was already owned, as were permitting and other owner costs since those would be similar regardless of the technology selected. Estimated EPC Costs 1800 1600 1400 1200 1000 RICE $/kW 800 CT 600 400 200 0 Figure 1: Published Estimated RICE and CT EPC Costs (see References) Based on a sampling of published cost information, average EPC costs for RICE technology is approximately $1100/kW, and $800/kW for CT. The sample selected was based on installations in the 20-100MW size range, where such delineation was possible, and data points that appeared to be outliers were discounted. Page 2 of 13 Similarly, typical O&M costs were evaluated for the two technologies. Fuel costs, which represent the largest portion of overall operating costs, were excluded, as differences in those costs can be accounted for in the differing efficiencies of the equipment. Apples-to-apples data comparison for these costs proved more difficult, since the data can be represented in a variety of ways. The non-fuel O&M costs in Figure 2 address both fixed and variable costs for a typical installation. For the most comparable data, over the expected unit life, the average annual O&M cost for RICE was approximately $0.016/kWh and $0.007/kWh for CT. Estimated O&M Costs 0.030 0.025 0.020 RICE 0.015 $/kWh CT 0.010 0.005 0.000 Figure 2: Published Estimated RICE and CT Non-Fuel O&M Costs (see References) Operating and maintenance costs for RICE include maintenance labor, engine parts and materials such as oil filters, air filters, spark plugs, gaskets, valves, piston rings, and electronic components, and consumables. The recommended service includes inspections/adjustments and periodic replacement of engine oil and filters, coolant, and spark plugs every 500 to 2,000 hours. A top-end overhaul is recommended between 8,000 and 30,000 operating hours, which includes a cylinder head and turbocharger rebuild, and a major overhaul is performed after 30,000 to 72,000 operating hours, which involves piston/liner replacement, crankshaft inspection, bearings, and seals. For CTs, the maintenance requirements are less than RICE, and include labor for routine inspections and procedures, and major overhauls. Generally, routine inspections are required every 4,000 operating hours to ensure that the turbine vibration is within tolerance. A gas turbine overhaul is needed every 50,000 to 60,000 operating hours, which includes a complete inspection and rebuild of components to restore the gas turbine to nearly original performance. Note that operating hours for CTs are not directly comparable to RICE operating hours, as virtual hours are added to CTs for starts/stops and excessive load changes. Page 3 of 13 As shown, typical installed and non-fuel O&M costs are lower for CTs than RICE. The potential advantage of a RICE facility comes into play when operating characteristics and usage considerations are evaluated. Since maintenance costs for RICE installations do not increase with cycling and multiple starts and stops of the equipment, effective O&M costs begin to levelize between the technologies when employed in facilities that will experience this type of operation. How Will It Be Used? As engineers, we often seek an optimized solution, a “best fit”. With this mindset, the intended purpose of the generating facility can often drive the technology selection, since the technical characteristics of the equipment inherently lend themselves to different applications. However, careful consideration is still needed, and final selections are, of course, still rooted in economics. These technologies can be used for a variety of purposes in generating facilities, such as peaking generation, frequency stabilization and renewable generation support, to address reliability and resiliency concerns, and for capacity sales. As part of the comparison for these uses, some of the key differing technical features are shown in Table 1 below. Table 1: Basic Technical Comparison RICE CT Heat Rate (Btu/kWh) 7400-8200 8100-9200 Max Efficiency (%) Full Load 48-50 40-43 50% Load 48-50 30-33 Footprint (ft2/kw) 0.28-0.38 0.02-0.08 Time to Full Load (min) 5 15 Ramp Rate (%/min) 100-130 20-50 Turndown (singe unit) 25% 30% CHP Applications Hot Water/Steam Steam Dual Fuel / Fuel Range Low BTU Low and High BTU RICE heat rates are lower and efficiencies higher than CT, which results in lower fuel costs for the same output. Since fuel is the single largest operating expense for a generating facility, this is an important factor. Additionally, RICE efficiency remains steady throughout the load range, whereas CT efficiency decreases at reduced loads. The load range is broader for RICE than CT, both for a single unit, as well as for the total facility due to multiple smaller machines instead of one larger machine. Reciprocating engines are also able to start-up and reach full load capacity more quickly, and can withstand dramatic changes in load and many starts and stops with minimal impacts to the equipment and maintenance cycles. The ramp rate, both up and down, is substantially higher for RICE than for CT. Although CTs can be cycled, excessive load changes and starts and stops effectively adds operating hours, dramatically increasing maintenance costs. Page 4 of 13 Based on these characteristics, either RICE or CT appears to be the better fit for certain operational scenarios. When the hours of operation and load range are closer to intermediate load than to a high-cycling type of operation, the lower capital and O&M costs for the CT typically result in a higher return on investment, despite the lower efficiency. When the load profile is more volatile, the lower fuel and O&M costs for the RICE typically results in a higher return on investment, despite the higher installed cost. Table 2: Operating Characteristics – Best Fit RICE CT Load Profile Peaking to Intermediate Intermediate to Base Starts/Stops Many Few Capacity Factor Low High Hours of Operation Low High Operating Range Low Load Mid Load Peaking Generation For peaking applications, both RICE and CT can be viable options. Most of the literature advocates RICE for its fast start capabilities and broader load range as a better match to changing grid needs.
Details
-
File Typepdf
-
Upload Time-
-
Content LanguagesEnglish
-
Upload UserAnonymous/Not logged-in
-
File Pages13 Page
-
File Size-