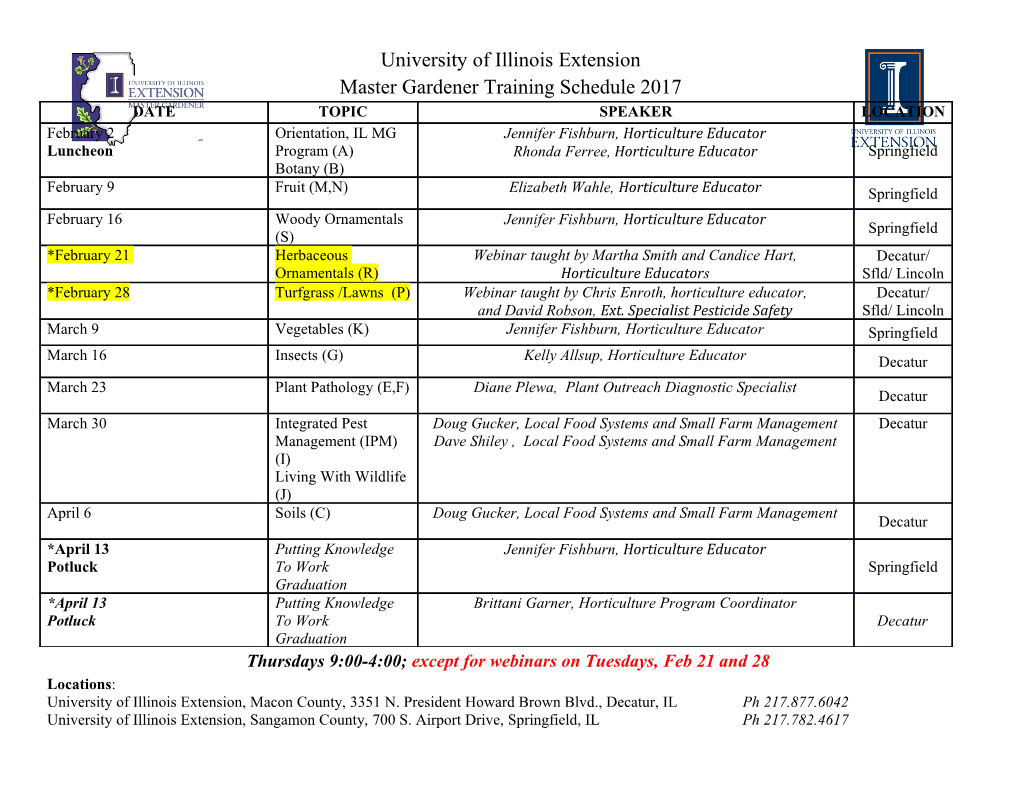
Henrik Metsäranta METAL 3D PRINTING The advantages of 3D printing metals Faculty of Engineering and Natural Sciences Bachelor’s Thesis May 2021 i ABSTRACT Henrik Metsäranta: Metal 3D Printing Bachelor’s Thesis Tampere University Bachelor's Programme in Engineering Sciences May 2021 This thesis explores metal 3D printing technologies, its advantages, and its applications. The most popular methods of 3D printing metallic materials are powder bed fusion (PBF) methods, direct energy deposition (DED), and binder jetting. The text discusses the main differences and similarities of these 3D printing methods. Direct metal laser deposition (DMLS) and selective laser melting (SLM) use a laser to sinter and melt metal powder, respectively. Electron beam melting (EBM) uses an electron beam to melt metal powder, and it is mainly used to process brittle metals. DED deposits and melts the metal simultaneously; it can use powder or wire as the feed material. Finally, binder jetting consists of fusing layers of metal powder together with a binder material. Binder jetting requires lots of post processing but is very cost efficient. The main advantages of metal 3D printing are the almost unlimited design possibilities and one-step manufacturing. Being able to design a component with a computer, then directly manu- facture the component with a 3D printer has led to rapid prototyping. Miniature and fully functional prototypes can be produced in a matter of days. The freedom of design has led to the production of newly designed parts. This includes parts with entirely new design, as well as parts, which were previously assembled from several components. Many components are being redesigned, espe- cially to achieve a light weight. Metal 3D printing is being utilized mostly by the medical and automotive industries. The med- ical industry uses it to produce customized implants and new medical tools. The automotive in- dustry uses it for prototyping, producing light weight components, and producing rare spare parts. In general, metal 3D printing is used to produce expensive, specialized, and low-volume parts. In the future, metal 3D printing may become less expensive, which can open new possibilities. How- ever, due to the high cost, metal 3D printing will not replace most conventional methods of pro- duction. Keywords: Metal 3D printing, design, applications The originality of this thesis has been checked using the Turnitin OriginalityCheck service. ii CONTENTS 1. INTRODUCTION .................................................................................................. 1 2. ADDITIVE MANUFACTURING ............................................................................. 2 3. METAL 3D PRINTING METHODS ........................................................................ 6 3.1 Powder Bed Fusion Methods ............................................................... 6 3.1.1 Direct Metal Laser Sintering (DMLS) and Selective Laser Melting (SLM) ................................................................................ 7 3.1.2 Electron Beam Melting (EBM) ..................................................... 10 3.2 Binder Jetting ..................................................................................... 12 3.3 Direct Energy Deposition ................................................................... 13 4. ADVANTAGES OF METAL 3D PRINTING ......................................................... 16 4.1 Design and Customization ................................................................. 16 4.2 Physical and Mechanical Properties ................................................... 17 4.3 Waste Material ................................................................................... 20 5. APPLICATIONS .................................................................................................. 22 5.1 Medical Industry ................................................................................. 22 5.2 Automotive Industry ........................................................................... 23 6. CONCLUSIONS .................................................................................................. 25 iii LIST OF FIGURES Figure 1. Basic principle of modern 3D printing. [2] ....................................................... 2 Figure 2. 3D printing market size and future predictions. [4] [adapted from 3D Hubs, The 3D Printing Trends Report Q1 2019] ..................................... 3 Figure 3. A visualization of a STL file. [6] ...................................................................... 5 Figure 4. Schematic diagram of a simple powder bed delivery system. [11] .................. 7 Figure 5. Comparison of microstructures of SLS and SLM produced parts. [12] ........... 8 Figure 6. Schematic diagram of an EBM system. [17] ................................................. 11 Figure 7. Schematic of a binder jetting system [18]. .................................................... 12 Figure 8. Schematic of a DED system [8].................................................................... 14 Figure 9. DMLS produced satellite antenna. [24] ........................................................ 16 Figure 10. Scanning electron microscope picture of 316L stainless steel: (a) fresh powder, (b) 16 times recycled powder. ................................................. 21 Figure 11. 3D printed orthopaedic hip replacement. [31] ............................................. 22 iv LIST OF SYMBOLS AND ABBREVIATIONS AM Additive manufacturing CAD Computer aided design DED Direct energy deposition DMLS Direct metal laser sintering EBM Electron beam melting PBF Powder bed fusion RP Rapid prototyping SLM Selective laser melting SLS Selective laser sintering STL Standard triangle language . 1 1. INTRODUCTION Additive manufacturing (AM), rapid prototyping (RP) and 3D printing are terms, which describe additive forms of production. They are often used interchangea- bly, and even though they are similar terms, they do differ. AM is a broad term, and covers a large variety of technological methods, including RP and 3D print- ing. AM covers the construction of any physical 3D objects by consecutively add- ing layers of material on top of each other, without a physical model to build on. Technically, it could be as simple as building a brick wall. First, the brick wall is designed in a way that it will endure, then it is built from a stable base to a com- plete wall. Simple AM methods can be traced far back in history due to the broad- ness of the term. What makes AM unique is the initial approach in production. Rather than using subtractive methods of production, or using a mold, AM meth- ods construct the product directly, without molding or subtracting material. This approach to manufacturing has provided exciting new opportunities for de- signing and fabricating parts. Some of the most innovational aspects of AM is producing 3D printed organs for humans. A 3D printed bladder has even been successfully transplanted. Although 3D printing is providing possibilities for pro- ducing new materials and objects, it is also changing the way current designs are being changed. Metals are a group of materials, which is often overlooked when considering AM. This text has a look at how and why metal 3D printing is being utilized in the world. What are the advantages of 3D printing metals? If the ad- vantages are big, could 3D printing replace conventional methods of production in the future? These are questions that this text will attempt to answer by looking into methods of 3D printing metals, the design and mechanical aspects, and the current applications of 3D printed metals. 2 2. ADDITIVE MANUFACTURING The concept of a modern additive layer by layer approach is shown in figure 1, which contains an illustration of a system with a laser power supply. This is an example of a 3D printing method. Material is added in thin layers and is then melted using a laser beam. The material is added layer by layer to form the shape going from rectangular base on the left to a more complex end shape on the right. Figure 1 contains a somewhat simple shaped object in construction; however, it illustrates the basic concept of 3D printing extremely well. The same concept ap- plies to more complex objects. Figure 1. Basic principle of modern 3D printing. [1] Modern AM methods are usually referred to as RP or 3D printing. They consist of fabricating a physical object from a virtual design. The virtual model is first created on a computer, then it is built using a flexible automated system. The difference between RP and 3D printing is very small, and the terms can often be used synonymously. RP was initially a method of producing prototypes for prod- ucts in a fast manner, so that large investments in producing prototypes could be avoided. Even though RP machines were expensive, it was usually cheaper to produce a prototype using RP technology rather than invest in a full line of pro- duction to produce the prototype. RP technology was exceedingly expensive, but as the technology further developed over time and prices decreased, the term 3D printer was born. 3D printing is essentially focused on using cheaper machines 3 with more limited functionality than RP. 3D printing is considered to be a produc- tion method, whereas RP is only applicable for constructing prototypes. Nowa- days, RP has come so far that 3D printers are affordable for private citizens. In In the past, AM technology was used by top-level scientists, researchers, and
Details
-
File Typepdf
-
Upload Time-
-
Content LanguagesEnglish
-
Upload UserAnonymous/Not logged-in
-
File Pages35 Page
-
File Size-