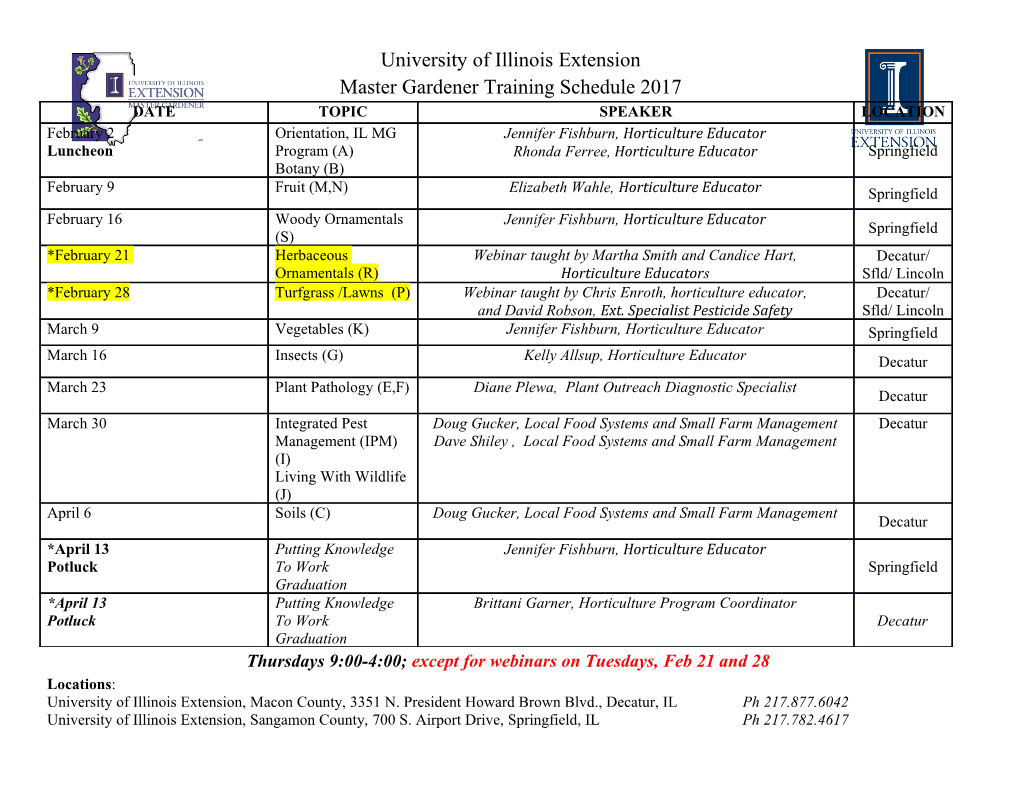
PROCESS ENGINEERING Fabrication of Short-Fibre Reinforced SiCN by Injection Moulding of Pre-Ceramic Polymers A. Müller-Köhn, M. Ahlhelm, A. Neubrand, H. Klemm, T. Moritz, A. Michaelis Pre-ceramic polymers were used as organic vehicle in this study forming a ceramic matrix after pyrolysis. Carbon short-fibres were chosen as fibre materials. Because of inadequate processing properties of the used pre-ceramic polymer, blending with thermoplastic waxes and process additives was necessary. An amorphous Si–C–N network was obtained as the matrix of the short-fibre composite after pyrolysis of the polysilazane precursor. In this study, the influence of different fibre types, fractions and lengths on com- pounding and moulding has been analysed. Torque measurements were used for characterising the flow ability and the thermal stability of the feedstock. Simulation of injection moulding processes was used as tool for predicting the form filling of test moulds as well as for supporting future development and moulds construction. In fibre-reinforced parts, the fibre distribution and alignment affect the mechanical proper- ties. With injection moulding simulation, the fibre alignment can be predicted and arranged. This offers the chance for smart comprehensive design of parts and moulds to match the mechanical requirements. The resulting composite parts have been analysed regarding their microstructure and mechanical properties. 1 Introduction of a ceramic powder as filler and a ther- visualized and analysed for strength or Producing advanced ceramics by injection moplastic binder system acting as organic damage tolerance improvement. In previous moulding allowed the application in areas ve hicle. So far, in industrial application, the publications, it was shown that a PIM simu- of high cost pressure. In powder injection thermoplastic polymers are completely re- lation, in this case with Moldex3D® (Sim- moulding, the so-called feedstock consists moved after shaping. The polymer content paTec Simulation & Technology Consulting in the feedstock reaches 35–50 vol.-%. GmbH), is a valuable tool for predicting the Problems, arising with the binder removal, flow behaviour of a ceramic powder-filled A. Müller-Köhn, A. Ahlhelm, H. Klemm, were found to cause defects during binder polymer melt and its effects on the final cer- T. Moritz, A. Michaelis burnout or high shrinkage during further am ic part. Fraunhofer Institute for Ceramic thermal treatment [1]. In contrast to estab- After pyrolyzing, a highly porous, amorph- Technologies and Systems (IKTS) lished powder injection moulding, the appli- ous ceramic matrix is formed, which could 01277 Dresden cation of pre-ceramic polymers allows using provide a basis for Ceramic Matrix Com- Germany the organic vehicle as ceramic matrix after posites (CMCs). Previous work used pre- pyrolysis. In this way, high solids loading, ceramic polymers with ceramic powders in A. Neubrand almost zero shrinkage and reduced porosity order to achieve Si–C, Si–C–N or Si–O– Fraunhofer Institute for Mechanics of shall be reached. C–N ceramics [2–5]. The ceramic compos- Materials (IWM) The application of pre-ceramic polymers in ites showed for example low density, high 79108 Freiburg injection moulding requires special proper- strength at high temperatures, high and Germany ties of the polymer. The pre-ceramic poly- stable friction coefficient and relatively high mers have to be meltable with a certain damage tolerance in comparison with other Corresponding author: A. Müller-Köhn freezing point, they shall show a low viscos- ceramics [6]. For injection moulding, only E-mail: ity and limited thermal cross-linking. These short fibres are suitable for processing of [email protected] aspects demand compromises in ceramic CMCs analogical to manufacturing of fibre- yield of the polymer. reinforced plastics [7]. Carbon short-fibres Keywords: CMC, injection moulding, Injection moulding process simulation can were also used in warm-pressing of CMCs carbon fibre, fibre reinforced provide accurate and detailed predictions in the LPI-route for producing brake discs or of 3D-fibre orientation, which can be also pads for automotive application [8]. E 46 cfi/Ber. DKG 97 (2020) No. 7-8 PROCESS ENGINEERING Tab. 1 Precursor properties Tab. 2 Fibre properties Trade Name Melting Temperature Density Ceramic Yield Length Fibre Type Finish [°C] [g/cm³] [%] [mm] Water-based Toho Tenax® HT C124 6 ML 33 S66 75 1,01 73 (removed by washing) SGL Sigrafil C 0,5 00B none 0,5 Ceraset HTT1800 N/A 1,02 86,3 Toho Tenax® HT M100 none 0,1 In comparison to these materials different stability were conducted at production tem- Tab. 3 Powder properties properties are expected since fibre spread- perature (150 °C). As input data for process Powder Type Trade Name d50 ing in injection moulded parts will be more simulation, temperature conductibility (DIN [µm] dominant than the pressed fibre bundles. EN 821), specific heat capacity (DIN 51007) SiC Sika Unikiln FCP07 3,0 Nevertheless, advanced properties are ex- and thermal expansion coefficient (DIN pected like high and stable friction coeffi- 51045) were determined, thermal conduc- cient, excellent thermal shock resistance tivity was calculated (Tab. 4). Tab. 4 Simulation data input and damage-tolerant behaviour [6, 8, 9]. The rheological behaviour of the prepared Temperature conductibility 0,61 mm2/s feedstocks was characterised by high-pres- (DIN EN 821) 2 Experimental sure capillary rheometry (RH10, Malvern Specific heat capacity 0,911 J/(g ⋅ K) Instruments/DE) at 130, 140 and 150 °C, (DIN 51007) 2.1 Materials respectively, with a 1,5 mm diameter die. Thermal expansion 2,94 ⋅ 10–5 /K Two different types of polysilazane were The apparent shear rate was increased coefficient (DIN 51045) −1 used as pre-ceramic polymers. For shaping stepwise in the range 50–5000 s . The Thermal conductivity 1,0 W/(m ⋅ K) the meltable ML33 S66 (Clariant/DE) and compound showed typical shear thinning Density 1,41 g/cm³ for infiltration Ceraset HTT1800 resin (KDT behaviour without any flow anomalies. The Inc./US) were chosen. The properties of the specific volume in correlation of pressure meltable precursor concerning viscosity and and temperature (pVT) was determined Moldex3D® (Simpatec/DE, CoreTec Inc.TW) wetting behaviour for the filler material according to ISO 17744 under isobar cool- uses an Improved Anisotropic Rotary Dif- were not adequate. For this reason, appli- ing (6 K/min) in a pressure range between fusion (iARD) technique in contrast to the cation of thermoplastic waxes as plasticizer 200–1600 bar from 40–170 °C by PVT100 conventional Folgar-Tucker-model-based and lubricants were necessary. pVT-measuring-system (SWO Polymertech- techniques. The obtained material charac- Characteristic data of pre-ceramic polymers nik GmbH/DE). teristics were fitted into the Moldex3D® are summarised in Tab. 1. Ceramic yield was Porosity of pyrolyzed samples was deter- (Release 10) material models. The meshing determined after pyrolysis in argon atmos- mined by high-pressure mercury porosim- of different test geometries was done by phere at 1000 °C and 1 K/min heating rate. etry (Micromeritics AutoPore IV 9500). Moldex 3D Mesh which bases on the Rhi- Three different commercial types of carbon Mechanical testing was performed by noceros Modeling Tools for Designers v. 4.0 short-fibres with diameter of 7 µm, 100 µm the 4-point-bending test (in dependence (Robert McNeel & Associates). and 500 µm as well as 6 mm in length with on DIN EN 843-3, however with testing or without water-soluble coating were used geom etry as fired), Young’s modulus was 2.4 Sample preparation in this study. The influence of different fibre measured by the sonic resonance method. After heating at 100 °C for removing re- fractions and lengths was analysed. Before For testing, the sample geometry was not sidual moisture, the fibres and powders compounding, the water-soluble coating modified. The SEVNB-method was used were compounded with the polymers in a had been removed by washing. The differ- for measuring fracture toughness [10]. The double Z-blade kneader (LKII, Linden/DE) ent type of fibres are summarised in Tab. 2, ratio of the notch depth a to the specimen at 150 °C for 1–2 h. The compound was properties of used powders are shown in height W was 0,22 (1,5 mm notch depth for granulated on a cutting mill (Pulverisette Tab. 3. 7 mm specimen height). 19, Fritsch/DE). The fibre content varied between 17–25 vol.-%, smaller fibre con- 2.2 Characterisation methods 2.3 Injection moulding simulation tent in feedstock number 3 was selected Feedstock development was started in a The injection moulding of fibre-reinforced because of reduced fibre degradation and torque rheometer (Plastograph, Brabender/ composites struggles with fibre-induced better flowability. The compound compos- DE) equipped with a W50 measuring mixer anisotropic mechanical properties strongly itions are described in Tab. 5. with a chamber volume of 55 cm³. This as- depending on the fibre alignment. In a re- Shaping was carried out on an injection sembly allowed compounding of small ma- sult, the moulded products may have high moulding machine (Allrounder 370C, Ar- terial amounts under practice-oriented con- internal stress. The flow-induced fibre orien- burg/DE) at a feedstock temperature of ditions. Measurements of the cross-linking tation and anisotropic shrinkages in injec- 150 °C and a mould temperature of 40 °C. behaviour, wetting properties and mixture tion moulding are complex 3D-behaviours. The injection unit was equipped with hard- cfi/Ber. DKG 97 (2020) No. 7-8 E 47 PROCESS ENGINEERING Tab. 5 Feedstock composition careful heating up to 950 °C within 270 h. Material Polymer Solid Fibre Fibre Powder Powder Reinfiltration process was executed under Feedstock Type Content Loading Type Content Type Content vacuum with Ceraset HTT1800. Curing 25 vol-% 25 vol.-% and following pyrolysis were also done in 1 C –SiCN 29,1 mass-% 50 vol.-% 0,1 mm SiC f 25,5 mass-% 45,4 mass-% oxygen-free argon flow of 5 l/h and heating 25 vol.-% 25 vol.-% up to 950 °C within 72 h.
Details
-
File Typepdf
-
Upload Time-
-
Content LanguagesEnglish
-
Upload UserAnonymous/Not logged-in
-
File Pages7 Page
-
File Size-