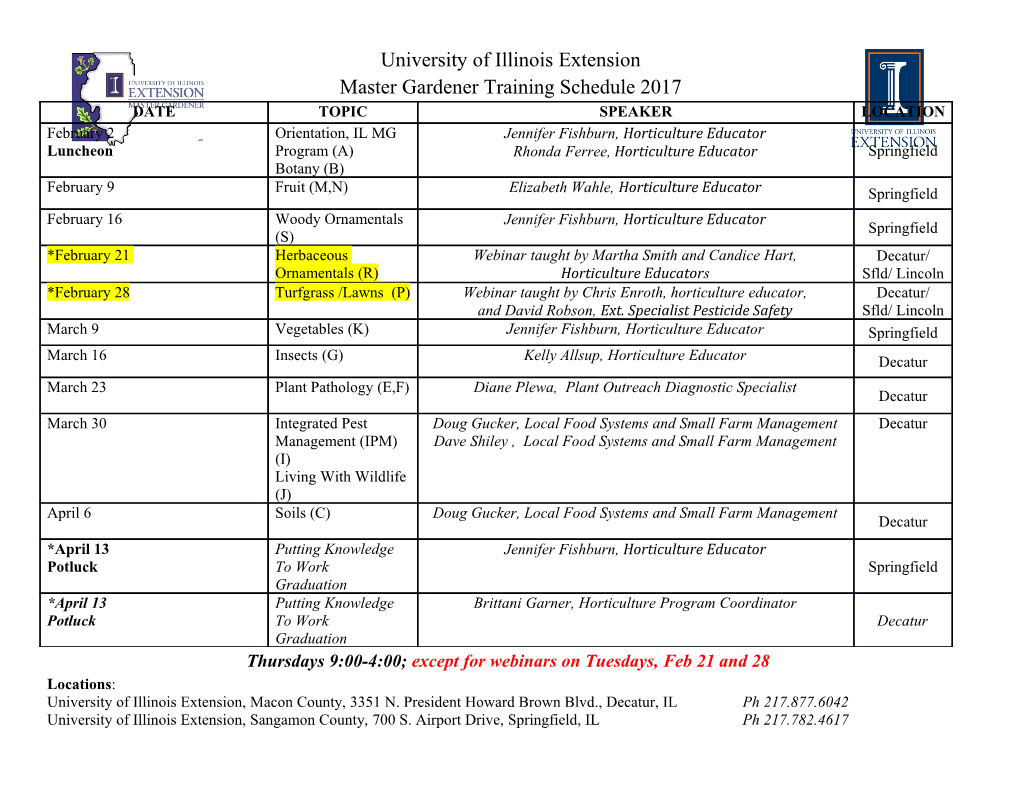
Fundamentals of Mass Transfer and Kinetics for the Hydrogenation of Nitrobenzene to Aniline Reinaldo M. Machado, Air Products and Chemicals, Inc. No. 01-2007 Introduction The catalytic hydrogenation of nitrobenzene to From a historical perspective, aniline is perhaps one aniline in a continuously mixed slurry reactor is of the more important synthetic organic chemicals a complex chemical process. A number of com- ever manufactured. In 1856, Sir William Henry Perkin, peting mass transfer and kinetic rate processes a student at the Royal College of Chemistry in London, contribute to the overall observed reaction rate. discovered and isolated a purple dye during the oxi- Scale-up and optimization of the process require dation of impure aniline1. The discovery of this dye, that the contributing rate processes are under- known as mauve, created quite a stir and Perkin, stood individually and their impact on the total seeing the value of his discovery, proceeded to scale process is quantified. Laboratory reactors must be up the synthetic process for the production of mauve, operated under conditions that will allow mean- which included the synthesis of aniline. This process ingful process characterization and scale-up. was to become one of the first commercial processes to generate a synthetic organic chemical. Two classical mechanistic routes to aniline from During the last three decades, polyurethane plastics nitrobenzene are possible depending upon pro- have emerged as a growth industry and aniline once cess conditions and the effects of gas/liquid and ALR Application Note again plays a key role as an industrial intermediate liquid/catalyst mass transfer. Intermediates formed used in the manufacture of MDI, 4,4’-diphenylmeth- during these competing chemical routes can act ane diisocyanate, a key commercial monomer in the as catalyst poisons that can radically change manufacture of polyurethane plastics. reactor performance. Aniline is produced by the reduction of nitrobenzene, This paper will describe and characterize these which is produced from the nitration of benzene in a competing processes for scale-up. mixture of sulfuric and nitric acid. Originally, nitroben- zene was reacted with dispersed iron in the presence Keywords: Mass transfer, kinetics, scale-up, of HCl to generate aniline and an iron oxide sludge. hydrogenation, aniline, nitrobenzene, slurry, agita- tion, liquid-solid, catalyst, pulse kinetics, reaction NO2 NH2 HCI (1) rate. + 9/4 Fe + H2O + 3/4 Fe3O4 This process generated large quantities of waste and was eventually replaced by the catalytic hydrogena- tion of nitrobenzene in a three-phase slurry reactor. Aniline can also be produced in the gas phase by the reduction of nitrobenzene with hydrogen over fixed catalysts2. This paper focuses on the characterization CH2, Bulk of a slurry process for the reduction of nitrobenzene to n aniline. Catalyst NO2 NH2 CNitrobenyine, Bulk Catalyst () + 3 H2 + 2 H2O Concentratio The catalytic hydrogenation of nitrobenzene to aniline Gas Liquid Bulk in a continuously mixed slurry reactor is a complex Film Film Liquid chemical process. dp 0 Distance 2 A number of competing mass transfer and kinetic rate Solid / Liquid Film processes contribute to the overall observed reaction Figure 1 rate. Scale-up and optimization of the process require Typical concentration profile during hydrogenation of nitrobenzene. that the contributing rate processes are understood individually and that their impact on the total process Literature rate be quantified. Laboratory reactors must be operat- A review of the literature can yield a confusing ed under conditions that will allow meaningful process description of the overall process kinetics of nitroben- characterization for scale-up. zene hydrogenation with authors reporting reaction orders for nitrobenzene and hydrogen between zero The key rate processes are illustrated in Figure 1, and one depending upon reaction conditions3-6. which shows schematically typical concentration A general review of the kinetic studies is given in profiles during the hydrogenation of the nitrobenzene: the doctoral thesis by Füsun Yücelen7. Most kinetic first, the rate of hydrogen mass transfer from the gas studies generate global kinetic rate models based on phase to the liquid phase; the rate of hydrogen and hydrogen uptake and overall conversion. However nitrobenzene mass transfer from the bulk liquid phase some detailed studies using analytical methods to to the outer surface of the catalyst; the rate of hydro- identify the individual intermediate species have also gen and nitrobenzene mass transfer into the porous been used to characterize reaction kinetic processes8. catalyst; and finally, the adsorption and kinetic rates of the hydrogen and nitrobenzene on the inner catalytic Additionally, most of the kinetics studies in the litera- surface of the catalyst particle. ture are conducted at relatively low temperatures with solvents. Optimized industrial processes would rather Two classical, mechanistic pathways to aniline from eliminate the use of solvents and their associated nitrobenzene are possible depending upon process separation processes, which can negatively impact conditions and the effects of gas/liquid and liquid/ overall process economics. Environmental pressures catalyst mass transfer. Intermediates formed during also tend to favor processes that use fewer solvents. these competing chemical routes can act as revers- ible catalyst poisons that can radically change reactor It would generally be preferred to use the reaction performance. It is not within the scope of this paper products of the nitrobenzene reduction, i.e., aniline to exhaustively review the literature or to optimize the and water, as the reaction solvent. Unfortunately, ani- process catalysts, temperature or conditions for the line and water are not miscible at low temperatures; reduction of nitrobenzene to aniline; rather, this paper therefore, higher temperatures must be employed will describe the principles, laboratory methods and to maintain a single liquid phase under process con- analysis techniques for characterizing these competing ditions. No literature studies are reported under these processes. conditions. It is hoped that his study will help shed some light on this process while illustrating the general principles required for characterizing a hydro- genation process from the laboratory scale. ALR Application Note Experimental Nitrobenzene Nitrosobenzene Phenylhydroxylamine Aniline For this set of studies the global reaction kinetics was H2 H2 H2 NO2 NO NOH NH2 determined by continuously monitoring the reaction H exotherm using the METTLER TOLEDO RC1/HP60 high- pressure reactor fitted with a single baffle and gas + Azoxzbenzene induction agitator supplied by Mettler-Toledo Inc.9. N N The METTLER TOLEDO PIC10 pressure controller was O H operated to allow hydrogen gas into the reactor to 2 maintain the desired pressure setpoint while gas was N N Azobenzene not allowed to exit the reactor. H The reduction of nitrobenzene to aniline is exothermic 2 H and generates –56.6 ± 5.9 kJ/mole as measured in 2 N N 2 NH2 this study, making the calorimetric method ideal for H H this process. Reagents were all purchased through Phenylhydrazine Figure 2 Aldrich. Individual species were monitored using inter- Haber’s reaction pathways for the reduction of nitrobenzene to aniline, Strätz10. nal standard gas chromatographic methods. Sponge ® 200 nickel or Raney type catalysts were used in this A. N. Campbell (11) study at concentrations between 0.05 % and 0.10 %. 180 1 Phase Region All reactions were carried out with the agitator operat- 160 W.Alexejew (12) ing at 1000 rpm, which gave a mixing intensity mea- 140 sured at 1.0 watt/liter. 120 2 Phase Region emperature, Celsius T Chemistry 110 The chemistry for the reduction of nitrobenzene to ani- 100 line was originally elucidated by Haber as reported by 80 Strätz10 and is illustrated in Figure . Two paths exist to aniline according to this scheme. 60 The first proceeds from the sequential reduction of Figure 3 Weight % Aniline nitrobenzene: first to nitrosobenzene, next to phenylhy- Aniline/water phase diagram. droxylamine, and finally to aniline. This path, we will see, is favored under conditions aniline. From Figure , temperatures in excess of in which the concentrations of nitrobenzene are low, 160 °C would be required to keep this mixture homo- < 0.15 %. If the concentrations of nitrosobenzene geneous. High temperatures can impact byproduct and phenylhydroxylamine are allowed to increase, the chemistry, reducing aniline yields. However, if aniline formation of azoxybenzene proceeds rapidly followed is fed to the reactor system along with the nitroben- by reduction to azobenzene, phenyl hydrazine, and zene or if water is continuously removed via distil- finally, aniline. lation, the concentration of aniline in a continuous The second path, while ultimately yielding aniline, process can be maintained at aniline concentrations is much slower kinetically on nickel catalysts and is higher than that dictated by the stoichiometry. favored under conditions in which the nitrobenzene concentrations are high, > 0.15 %. During high tem- Therefore, lower temperatures are required to keep the perature studies, the only stable intermediates identi- system homogeneous. In this study the continuous fied and monitored were nitrobenzene, azoxybenzene feed to the reactor consisted of 50 % aniline and and azobenzene, as we will see later. 50 % nitrobenzene,
Details
-
File Typepdf
-
Upload Time-
-
Content LanguagesEnglish
-
Upload UserAnonymous/Not logged-in
-
File Pages14 Page
-
File Size-