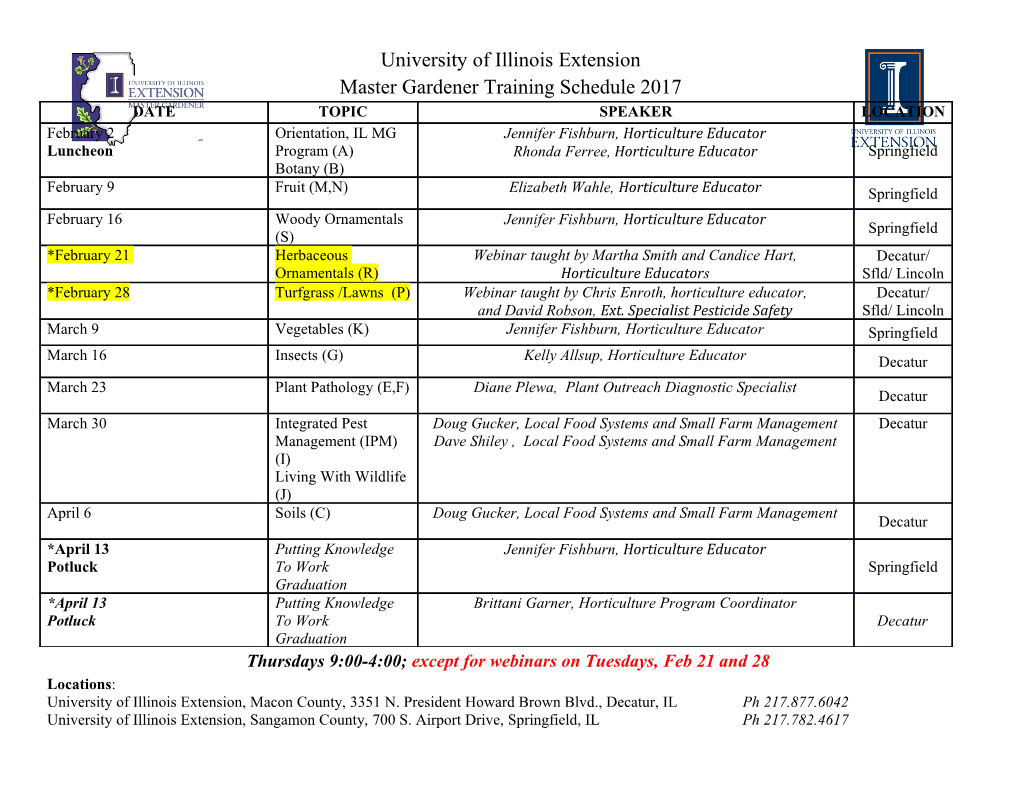
Precision Tools Precision Tools Gear Cutting Tools & Broaches Pursuing advanced high-speed technology that is both user and environmentally friendly Since developing Japan's first broaching machine in the late 1920s, Fujikoshi has developed a variety of tools and machine tools to handle advancements in production systems. Fujikoshi continues to lead the way by developing machining systems that integrate tools and machines. Pursuing advanced high-speed technology that is both user and environmentally friendly Since developing Japan's first broaching machine in the late 1920s, Fujikoshi has developed a variety of tools and machine tools to handle advancements in production systems. Fujikoshi continues to lead the way by developing machining systems that integrate tools and machines. ndex Gear Cutting Tools Gear Cutting Comparison and Types 25 Broaches Design of Broach ools Guidance NACHI Accuracy of Gear Shaper Cutters 26 Technical Introduction Basic Design and Cutting Method 61 Materials and Coating of Gear Cutting Tools 5 Cutting Condition and Regrinding 27 Hard Broaches 45 Calculation of Pulling Load 62 Gear Cutting T Disk Type Shaper Cutters Type1Standard Dimensions 28 Broach for MQL 46 Face Angle and Relief Angle 63 Technical Introduction Disk Type Shaper Cutters Type2Standard Dimensions 30 Off-normal Gullet Helical Broach 47 Finished Size of Broaches 64 Hard Hobbing 6 Disk Type Shaper Cutters Type2Standard Dimensions 31 Micro Module Broaching 48 Helical Gear Shaper Cutters High Speed Dry Hobbing 7 Essential Points and Notice 65 Disk Type Shaper Cutters Type3Standard Dimensions 32 Clutch Keyway Dimensions for Broaching Process High Performance Shaving Cutter 9 Guidance oaches Deep Counterbore Type Shaper Cutters Standard Dimensions 33 Br Dual Forming Rack 10 Terms of Internal Broaches 49 Pull End 66 Sproket Shaper Cutters Standard Dimensions 34 Terms of Surface Broaches 50 Hobs Nomenclature of Broaching Machine 51 Retrievr End 70 Hob Cutting Action and Nomenclature 11 Shaving Cutters Cycle of Broaching 52 Inclination Angle of Hob and Hobbing Methods 12 Feature and Nomenclature of Shaving Cutters 35 GPA 71 Multi-thread Hob and Short Pitched Hob Design 13 Shaving Methods and Features 36 Internal Broaches Tooth Profiles of Hob and Sign 14 Shaving Mechanism and Cycle Diagram 37 Work Piece Samples of Internal Broaches 53 NACHI Accuracy of Gear Hobs 15 NACHI Accuracy of Shaving Cutters 38 Involute Spline Broaches 54 Standard Keyways for Hobs 17 Standard Number of Cutter Teeth and Simple Calculation for Cutter Width 39 Push Broaches 55 Cutting Condition and Regrinding 18 Helical Broaches 56 Solid Gear Hobs Standard Dimensions 19 Forming Racks Fine Pitch Gear Hobs Standard Dimensions 20 Feature and Rolling Principles 40 Surface Broaches Involute Spline Hobs Tooth Profile 21 Example 41 Work Piece Samples of Surface Broaches 57 Parallel Side Spline Hobs Standard Dimensions 22 Type of Racks and Basic Dimensions 42 Connecting Rod Broaches 58 Roller Chain Sproket Hobs Standard Dimensions 23 Fir Tree Type Broaches 59 Other Types of Gear Cutting Tools Steering Rack Broaches 60 Gear Shaper Cutters Gear Chamfering Tools 43 Feature and Nomenclature of Gear Shaper Cutters 24 Reverse Lead Taper Tooth Forming Tool 44 ndex Gear Cutting Tools Gear Cutting Comparison and Types 25 Broaches Design of Broach ools Guidance NACHI Accuracy of Gear Shaper Cutters 26 Technical Introduction Basic Design and Cutting Method 61 Materials and Coating of Gear Cutting Tools 5 Cutting Condition and Regrinding 27 Hard Broaches 45 Calculation of Pulling Load 62 Gear Cutting T Disk Type Shaper Cutters Type1Standard Dimensions 28 Broach for MQL 46 Face Angle and Relief Angle 63 Technical Introduction Disk Type Shaper Cutters Type2Standard Dimensions 30 Off-normal Gullet Helical Broach 47 Finished Size of Broaches 64 Hard Hobbing 6 Disk Type Shaper Cutters Type2Standard Dimensions 31 Micro Module Broaching 48 Helical Gear Shaper Cutters High Speed Dry Hobbing 7 Essential Points and Notice 65 Disk Type Shaper Cutters Type3Standard Dimensions 32 Clutch Keyway Dimensions for Broaching Process High Performance Shaving Cutter 9 Guidance oaches Deep Counterbore Type Shaper Cutters Standard Dimensions 33 Br Dual Forming Rack 10 Terms of Internal Broaches 49 Pull End 66 Sproket Shaper Cutters Standard Dimensions 34 Terms of Surface Broaches 50 Hobs Nomenclature of Broaching Machine 51 Retrievr End 70 Hob Cutting Action and Nomenclature 11 Shaving Cutters Cycle of Broaching 52 Inclination Angle of Hob and Hobbing Methods 12 Feature and Nomenclature of Shaving Cutters 35 GPA 71 Multi-thread Hob and Short Pitched Hob Design 13 Shaving Methods and Features 36 Internal Broaches Tooth Profiles of Hob and Sign 14 Shaving Mechanism and Cycle Diagram 37 Work Piece Samples of Internal Broaches 53 NACHI Accuracy of Gear Hobs 15 NACHI Accuracy of Shaving Cutters 38 Involute Spline Broaches 54 Standard Keyways for Hobs 17 Standard Number of Cutter Teeth and Simple Calculation for Cutter Width 39 Push Broaches 55 Cutting Condition and Regrinding 18 Helical Broaches 56 Solid Gear Hobs Standard Dimensions 19 Forming Racks Fine Pitch Gear Hobs Standard Dimensions 20 Feature and Rolling Principles 40 Surface Broaches Involute Spline Hobs Tooth Profile 21 Example 41 Work Piece Samples of Surface Broaches 57 Parallel Side Spline Hobs Standard Dimensions 22 Type of Racks and Basic Dimensions 42 Connecting Rod Broaches 58 Roller Chain Sproket Hobs Standard Dimensions 23 Fir Tree Type Broaches 59 Other Types of Gear Cutting Tools Steering Rack Broaches 60 Gear Shaper Cutters Gear Chamfering Tools 43 Feature and Nomenclature of Gear Shaper Cutters 24 Reverse Lead Taper Tooth Forming Tool 44 Guidance Technical Introduction Materials and Coating of Gear Cutting Tools Hobbing of hardened gear is possible ools ools Gear Cutting Tool Material Hard Hobbing� Suitable for high accuracy gear hobbing of the shaft and small module Tool Material Hobs Gear Shaper Cutters Shaving Cutters Forming Racks Features �which was difficult in grinding� Gear Cutting T Gear Cutting T HSS� HSD� ○ Toughness Up� Realized high accuracy by hob and spindle one body tooth profiles grinding� � SKH51� △ △ ○ Toughness Up� Achieved longer tool life by Hyper Dual coat and herd metal of new development SKH55� ○ ○ Standard� FM34D� ○ Crater Wear Resistance� FM29A� ○ Wear Resistance� FM23A� ○ Wear Resistance� Power HSS FAX31� ○ � Carbide Hob FAX38� ○ ○ △ Heat Resistance� FAX55� △ △ Wear Resistance Carbide � ○ oduction Guidance Surface Treatment Nitride� ○ ○ Work Piece TiN� ○ ○ ○ Dual ○ ○ ○ echnical Intr T � � Coating Technology Before After Carbide Hob with shank d Hobbing Hardened Steels� Har 50HRC~� CBN Hybrid� TiAIN Multilayered Coating� TiAIN Multifunctional � � Accuracy AG Coat Multilayer Composite Film� Surface � Hardened Steels� Aqua Coat� Modification� 40HRC~ Before Hard Hobbing After Hard Hobbing Before Hard Hobbing After Hard Hobbing TiC Dual Coat� +� GS Hard Coat� Multi-element � � TiN+TiC TiCN Multilayered � TiCN Multilayered � & Multilayer � Coating� Coating� Hybrid� Film Surface Modification + � TiCN Platina Coat� UG Coat Carbon Steels� SG Coat Rigid Film Profils Error Lead Error Cast Irons TiN G Coat '80 '85 '90 '95 '00 '05 Generation Coating Technology Creation Compound・Multilayer・Increase of Film Hybrid Performance NACHI’s coating technology developed from research on physical Performance of Dual Coat Hob vapor deposition (PVD) ion plating. By using the peculiarities of Comparison of Tool life Cutting face ionization acceleration technology, surfaces can be coated with Hard Hob� : Non Coat� (mm) multiple layers of TiN, TiC and TiCN. � Competitor : Coat The tool life of coated products are extended to five times those 1500 of uncoated products because the coatings have very good wear 0.3 TiN Coat resistance and solvent resistance. � 1000 It makes high speed and high performance possible and greatly Wear 0.2 Dual Coat 500 reduces total costs. Number of Gears VB 0.1 0 NACHI Hard Hob Competitor KE250 (Kashifuji) 0 1000 2000 3000 4000 Number of Gears Workpiece Hob Specifications Cutting Conditions Hob� : φ95×L150×φ31.75, 3Thread, RH, 12Number of Teeth, FM34D� Workpieces� : m1.75×PA17.5°×30T×30RH, Tooth Width18mm, SCr420, 150HB� Cutting Condition:� Cutting Speed V=150m/min, Feed F=2.0mm/rev, Cutting Face Module� 2� Outside Dia.� 50mm� Cutting Speed� 2.5mm/rev� Non Coat, Dry Hobbing Number of Teeth� 6� Overall Length� 100� Feed� 2.5mm/rev� Pressure Angle� 20°� Threads� 1� Cutting Method� Climb Cutting� Tooth Width� 28mm� Flutes 12 Coolant -� Material SCM420(60HRC) 5 6 Guidance Technical Introduction Materials and Coating of Gear Cutting Tools Hobbing of hardened gear is possible ools ools Gear Cutting Tool Material Hard Hobbing� Suitable for high accuracy gear hobbing of the shaft and small module Tool Material Hobs Gear Shaper Cutters Shaving Cutters Forming Racks Features which� was difficult in grinding� Gear Cutting T Gear Cutting T HSS� HSD� ○ Toughness Up� Realized high accuracy by hob and spindle one body tooth profiles grinding� � SKH51� △ △ ○ Toughness Up� Achieved longer tool life by Hyper Dual coat and herd metal of new development SKH55� ○ ○ Standard� FM34D� ○ Crater Wear Resistance� FM29A� ○ Wear Resistance� FM23A� ○ Wear Resistance� Power HSS FAX31� ○ � Carbide Hob FAX38� ○ ○ △ Heat Resistance� FAX55� △ △ Wear Resistance Carbide � ○ oduction Guidance Surface Treatment Nitride� ○ ○ Work Piece TiN� ○ ○ ○ Dual ○ ○ ○ echnical Intr T � � Coating Technology Before After Carbide Hob with shank d Hobbing Hardened Steels�
Details
-
File Typepdf
-
Upload Time-
-
Content LanguagesEnglish
-
Upload UserAnonymous/Not logged-in
-
File Pages76 Page
-
File Size-