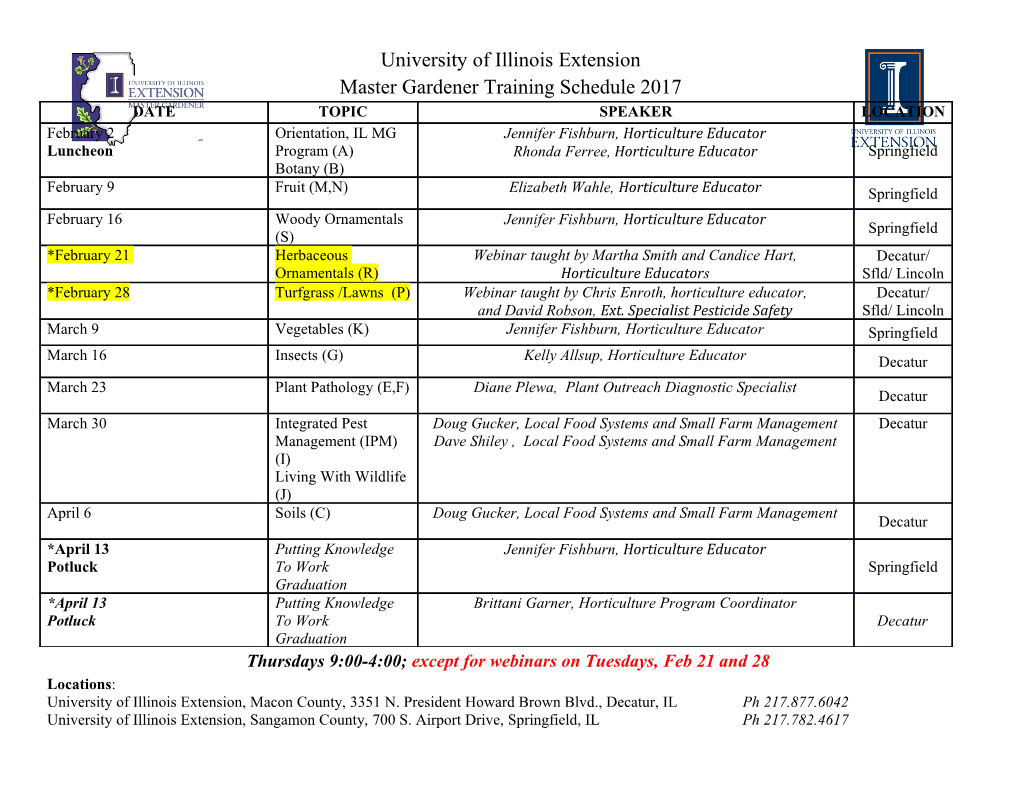
Organocatalysis in Continuous Flow Sebastiaan A. van den Berg Thesis committee Promotor Prof. Dr H. Zuilhof Professor of Organic Chemistry Wageningen University Co-promotor Dr T. Wennekes Assistant professor, Laboratory of Organic Chemistry Wageningen University Other members Prof. Dr J. van der Gucht, Wageningen University Prof. Dr F. P. J. T. Rutjes, Radboud University Nijmegen Dr T. Noël, Eindhoven University of Technology Dr C. Wiles, Chemtrix B.V., Geleen This research was conducted under the auspices of the Graduate School VLAG (Advanced studies in Food Technology, Agrobiotechnology, Nutrition and Health Sciences). Organocatalysis in Continuous Flow Sebastiaan A. van den Berg Thesis submitted in fulfilment of the requirements for the degree of doctor at Wageningen University by the authority of the Rector Magnificus Prof. Dr A.P.J. Mol, in the presence of the Thesis Committee appointed by the Academic Board to be defended in public on Friday, April 1st 2016 at 1.30 p.m. in the Aula. Sebastiaan A. van den Berg Organocatalysis in Continuous Flow, 225 pages. PhD thesis, Wageningen University, Wageningen, NL (2016) With references, with summary in English ISBN 978-94-6257-663-6 “Be not afraid of growing slowly, be afraid only of standing still.” Chapter 1 Introduction 1 Chapter 2 Microwave-Assisted Formation of Organic Monolayers from 1-Alkenes on Silicon Carbide 27 Chapter 3 Clickable Mesoporous Silica via Functionalization with 1,ω-Alkenes 43 Chapter 4 Continuous-Flow Alcohol Protection and Deprotection Reactions Catalyzed by Silica-Supported Sulfonic Acid 61 Chapter 5 Clickable Polylactic Acids by Fast Organocatalytic Ring-Opening Polymerization in Continuous Flow 81 Chapter 6 General Discussion 111 Supporting Information for Chapter 2 129 Supporting Information for Chapter 3 139 Source code of surface composition determination script 143 Supporting Information for Chapter 4 153 Source code of kinetic parameter estimation script 181 Supporting Information for Chapter 5 185 Summary 207 Acknowledgments 211 Publications 213 Overview of completed training activities 215 About the author 216 Introduction Introduction 1 Chapter 1 Flow chemistry Chemistry, in its most basic form, studies the composition, structure, and change of matter. As far back as the Greek and the Egyptians, people have tried to understand the building blocks that make up matter around us. People also tried to change one kind of material into another, because the aimed for material had desirable properties. An early example would be soap. By adding water to ashes, the water would extract potassium carbonate from the ashes and become basic. Using this caustic solution, the low-value material fat can be turned into the high-value material soap. If we look back a few hundred years, we find another example. So-called “alchemists” tried to turn one material into another, more valuable material: they tried to turn lead into gold. Although this process is not possible by chemical means it underlines the basic goal of chemistry: changing the properties of materials to make them more useful and valuable. While the alchemists were unsuccessful in transmuting lead into gold, they did discover many other interesting processes and laid the foundation for modern-day chemistry. Fast-forward to the twenty-first century. Chemistry has given us important materials such as medicines, fertilizers, polymers, and petrochemicals. These are made from smaller building blocks via processes that have been discovered over many years of research. The batch-wise way we make these molecules also changed very little from the time of the alchemists. Round-bottom flasks, reflux condensors, and other glassware remained surprisingly similar to those used two hundred years ago. On the one hand this points to the effectiveness of these instruments. On the other hand it reveals a lack of progress in this area and the use of these round-bottom flasks and other glassware indeed has drawbacks. This thesis is concerned with the application of the next generation of chemical glassware: miniaturized continuous flow reactors, which show great potential in reaction optimization, efficiency, and safety. Specifically, this work tries to 2 Introduction implement (solid-supported) catalysis in these miniaturized reactors to enable faster and greener chemistry. This introduction will therefore elaborate on continuous flow, microreactors, and solid-supported catalysis. Continuous Flow Modern chemists, at the forefront of scientific discovery, work on a relatively small scale in the lab, often milligrams to grams. Reasons for working on this small scale are the costs and safety issues associated with large amounts of chemicals. The name of the game in the research lab is often “get the molecule”, which focuses on discovery of new molecules with desirable properties. In industry, it is not only about discovering new molecules, but also producing these molecules as efficiently as possible on a much larger scale, often between tons and kilotons per year. The batch-wise production process for a given molecule discovered on a small scale often cannot simply be scaled up a thousand fold for industrial purposes. Why is that? Let us take a simple example. We have a small round-bottom flask that can hold 100 mL of liquid. A fast reaction was identified to produce a certain molecule. In the process to get this prized molecule we have to cool the round-bottom flask because the fast reaction generates a lot of heat. Without cooling a thermal runaway would cause an explosion. The volume of the flask is 0.0001 m3, while the surface area is 2 0.01 m giving it a surface-to-volume ratio of 100. On a lab scale an ice bath is sufficient to cool this 100 mL round-bottom flask. Now let us assume we scale up this process a thousand fold, to a 100 L round- bottom reactor. The surface area of this “flask” is now roughly 1 m2. The surface-to- volume ratio has decreased to 10. This means that there is less surface area per volume available to dissipate heat. On this 100 L scale the reaction is now harder to cool and keep under control. Because of these cooling issues thermal runaway also becomes a much bigger problem as the resulting explosion would now involve a thousand times more material. 3 Chapter 1 Figure 1. Scale up of a laboratory process can be done by increasing the reactor volume often leading to issues with heat transfer and mixing. Scale up can also be performed by translating the process to a flow process that is readily scaled up in a larger flow system or by running the reaction in parallel. Localized hot spots may form in the 100 L reactor due to reduced mixing and heat transfer capacities. These hot spots could lead to unwanted by-products and a lower yield, which makes the process more costly and less environmentally friendly. From a safety standpoint the reaction would be ideally carried out in one thousand 100 mL round-bottom flasks or even one million 0.1 mL flasks as an “explosion” would only involve minute quantities of material. As one can imagine this would require high infrastructure investments and would be very labor-intensive and cumbersome. Working up a million or even just a thousand batch-wise reactions is simply not feasible. Now imagine a 0.1 mL round-bottom flask with a tap on the bottom and a tube attached to the top. The surface-to-volume ratio will be higher due to its smaller volume. Therefore, the heat transfer is better allowing the reactor to be kept at a specific temperature. As soon as the tap is opened the product stream comes out 4 Introduction with almost only target material because the reaction is quick. The reaction flask is continuously refilled with reagents and only a small amount of material is reacting at a given time. Even if thermal runaway occurs the explosion will only involve 0.1 mL of material. Nevertheless, the small reactor continually produces product. Given enough time it will produce the same amount of material as the 100 L reactor, albeit a lot safer and with less downtime. In the above example the reaction is continuously carried out in a flowing medium. This concept is called continuous flow chemistry. In continuous flow chemistry streams of dissolved reagents are combined and mixed. The reagents react and are carried away in the solvent stream. This continuous flow concept can be combined with the small reactor described above to create so-called “microreactors”. At its most basic level a microreactor is a small platform with channels, inlets, and outlets. The reaction can be performed in a small chip in which microchannels (several hundreds of micrometers in diameter) have been created, but other types of reactors exist as well, e.g. tubular reactors or falling-film reactors. The underlying concept remains the same: the chemistry is performed in a continuously flowing fashion. The internal volume of the microreactor chip can be anywhere from tens of nanoliters1 to several milliliters. The microreactor chip can be made of materials such as PDMS (a polymer), stainless steel, silicon, and glass.2 PDMS has a low solvent compatibility (not suited for organic solvents) and glass cannot handle reactions in which fluorine or fluoride is formed. Nevertheless, glass and metal are most commonly found in synthetic applications.3 For extreme applications of flow chemistry silicon carbide can be used, which is more resistant to corrosion than stainless steel. Silicon carbide reactors were used for the harsh conditions of the Wolff-Kishner reaction in which a carbonyl is reduced using potassium hydroxide and aqueous hydrazine at 200 °C and 14 bar.4 Each reactor material therefore has its own distinct advantages and disadvantages, depending on the reaction that is being performed.
Details
-
File Typepdf
-
Upload Time-
-
Content LanguagesEnglish
-
Upload UserAnonymous/Not logged-in
-
File Pages225 Page
-
File Size-