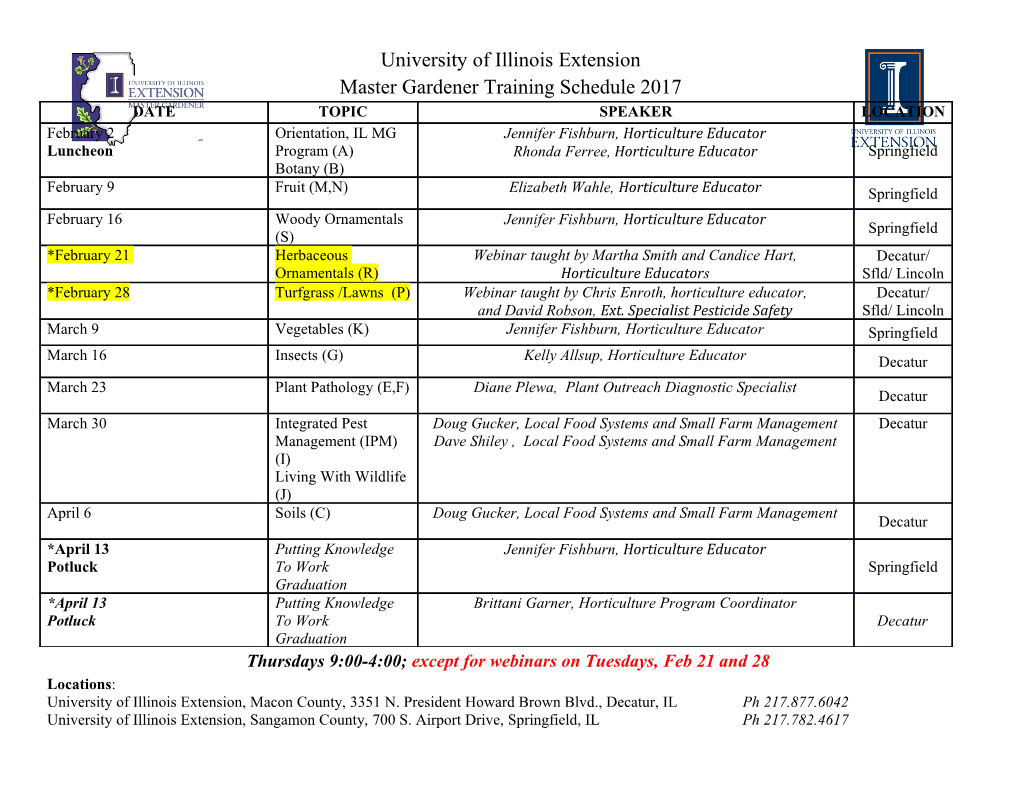
MIT SOLAR ELECTRIC VEHICLE TEAM The MIT Solar Electric Vehicle Team (SEVT) TEAM GOALS: is a student organization dedicated to • Facilitate continuous demonstrating the viability of alternative innovation and deve- energy-based transportation. The team was lopment in all fields founded in 1985 and since 1993 has worked related to solar under the auspices of MIT’s Edgerton electric vehicles Center. through international participation and We build each vehicle from the ground competition up, allowing us to apply our theoretical knowledge while gaining hands-on • Give our sponsors manufacturing experience and project publicity through management skills. Team members work positive exposure and with professors and industry to overcome press coverage. the design and fabrication challenges • Provide members of inherent to this complex project. Since the MIT community its creation, the SEVT has built nearly 15 with incomparable vehicles and competed successfully in experience in engin- national and international races, most eering, management, recently the 2015 World Solar Challenge in marketing, and Austrailia. We are currently constructing business. our newest race vehicle for competition in the 2017 World Solar Challenge. • Be active in the com- munity, promoting We share our enthusiasm for applied alternative energy and engineering and renewable technologies by transportation. actively reaching out to local schools and • Inspire children the Greater Boston community. Through to pursue careers our interactions, we hope to educate in science and the public about alternative energy and engineering. transportation, as well as inspire the next generations of innovators. WHAT IS SOLAR RACING? In a solar car race, highly specialized Each solar car is accompanied by provement in efficiency and perfor- vehicles that run entirely on solar lead and chase vehicles to provide mance of their vehicles. Each vehicle power are driven across continents support and ensure the safety of is the focus of a major group effort at highway speeds. These vehicles both the solar car and other vehi- that involves leadership, planning, are designed and built by teams cles on the road. Before each race, business, marketing, and publicity. of engineering students. Today’s officials perform strict inspections, two largest races are the World So- a process known as scrutineering, As the years have passed, the Chopper del Sol Valkyrie Arcturus lar Challenge in Australia, and the to ensure the vehicles comply with technology used in our cars has North American Solar Challenge. race rules and safety standards. continuously improved. The fol- ‘11 World Solar Challenge (15th) ‘14 American Solar Challenge ‘15 World Solar Challenge The vehicles drive during the day lowing timeline charts the evolu- ‘12 American Solar Challenge (10th) and stop at night, covering 3000 Teams exploit the latest technolo- tion of our vehicles and their suc- to 4000 km in three to twelve days. gies to make every possible im- cesses at races around the world. Solectria 4 Solectria 5 Galaxy Aztec Manta Manta GT Manta GTX Manta Elite Tesseract Eleanor ‘87 Swiss Tour de Sol ‘88 Swiss Tour de Sol (6th) ‘90 GM Sunrayce (6th) ‘92 American Tour de Sol ‘95 GM Sunrayce (1st) ‘97 Sunrayce (2nd) ‘99 World Solar Challenge ‘01 American Solar ‘03 World Solar Challenge ‘09 World Solar Challenge (15th) ‘88 American Solar Cup (1st) ‘91 American Tour de Sol (2nd) ‘98 Suzuka Dream Cup (1st in class) Challenge (10th) (3rd) (5th overall, 2nd in silicon ‘87 World Solar Challenge ‘89 American Tour de Sol (1st) ‘93 American Tour de Sol (5th) ‘05 American Solar class) (9th) (3rd) ‘92 Swiss Tour de Sol (2nd) (1st) ‘98 World Solar-Car Rally Challenge (3rd) ‘89 Canadian Solar Cup (1st) ‘94 American Tour de Sol (3rd) ‘05 World Solar Challenge ‘90 American Tour de Sol (1st) (6th) (1st) ELECTRICAL SYSTEM PERFORMANCE The high voltage system includes the array, battery pack, and motors, while driver controls such as the steering wheel, throttle, Max speed: 70 mph (motor can go ANATOMY OF camera, and horn make up the low voltage system. up to 90 mph) AERODYNAMIC BODY A SOLAR CAR Cruise speed: 60mph A CAN network links the primary vehicle computer to various monitoring components in order to alert the driver of any irregu- Each car’s aerodynamic shape is de- Flux represents several steps for- Weight: 450 lbs (without driver) larities, and enables constant communication between the solar signed in Rhino, simulated in Ansys, and ward in solar vehicle technology. Dimensions: 4.45 m x 1.72 m car and the support vehicles. tested in the Ford Wind Tunnel. Flux’s The latest race regulations have shape is asymmetric which reduces drag included significant rule changes by 2/3 what it would be for a symmet- designed to bring solar vehicles ric design. Additionally, the asymmetric closer to commercial passenger shape allows the car to sail in cross-winds cars. Vehicles are now required to which helps reduce have a driver-controlled parking drag even further. brake, and the solar aray area has been significantly reduced. CANOPY Driver entrance and windshield Flux uses an asymmetric design to minimize aerodynamic drag. SOLAR ARRAY We were able to aerodynamically optimize the shape of the car with Flux has a 4 m2 array made up of silicon cells. CFD (computational fluid dynam- Power from the array is controlled by two cus- ics) using Ansys. tom-designed maximum power point trackers, for an estimated output of 1200 W. The electrical system for Flux was also redesigned for efficiency. One design change is that Flux CHASSIS & SUSPENSION has one motor on one of the rear wheels, allowing a simpler, lighter Flux’s chassis is a composite monocoque chas- electrical system but having mini- sis which is integrated into the composite lower mal effects on driving the car. body. Designed to protect the driver from impacts, it serves as the backbone of the car. The composite The car’s monitoring and con- chassis in particular saves weight and allows better trol electronics have also been integration between chassis and body. The roll-bar, reworked, providing increased still made out of steel, curves over the driver’s head safety for the driver and greater and protects the driver if the car were to ever roll. communication between the solar car and the support vehicles. This data has been useful not only in Both the two front wheels and the driven rear improving the design of our next wheels have dual wishbone suspensions to im- car, but also allows our strategy prove handling and reduce energy dissipation over team to create predictive func- bumps and rough surfaces. tions that can give us an edge during the race. These innovations represent significant improve- MOTOR ments in performance, reliability, BATTERY PACK and safety. A Mitsuba hub motor is mounted on each of the rear FAIRINGS, WHEELS & TIRES wheels, with a maximum power output of 3 hp (2.25 kW) per Flux’s pack is constructed from motor. Flux has less than one tenth the engine output of a Aerodynamic fairings minimize 434 Lithium Ion cells, and has a typical compact car. the drag around Flux’s wheels capacity of 43 Ahr. Microproces- and tires. The carbon fiber sors monitor the temperature and The motor has also been equipped with regenerative brak- wheels and low rolling resistance voltage of the pack in real time, ing, allowing for further charging of the battery pack. tires are manufactured specifi- and alert the driver if any problems cally for solar vehicles. arise. OUTREACH EVENTS LOOKING AHEAD One way in which SEVT distin- This past year we participated The design of Arcturus’s suc- ics team is crafting a streamlined including FLUENT and CFX. guishes itself from other stu- in the Cambridge Science Fes- cessor, Flux, includes lessons body, and one major design change dent engineering projects is tival and saw over 100 students learned from the building, testing is making the vehicle asymmet- The electrical team will be making our commitment to being ac- walk through our shop over and racing Arcturus as well as a ric. By positioning the driver on new changes in its components, tive in the community. Each the course of a Saturday after- few new concepts. one side of the car, the reduced and in particular we are using only year, dozens of K-12 students noon and were able to answer frontal area will minimize drag, one motor to drive the car. Flux visit our shop to learn about any and every question about One of our overarching design and therefore, power consump- will also have redesigned driver our vehicles, alternative energy working on the team, design- goals for Flux is to reduce the tion of the solar car. The aero- interface electronics. The team and the opportunities available ing and buliding solar cars, and car’s weight because it increases dynamics team is trying vari- will be designing and construct- in engineering. We also display competing in the World Solar overall efficiency. Among many ous designs for the canopy, for ing the battery pack in house. vehicles at local events, fairs Challenge. weight optimaztions for each the fairings, and for the airfoil- and museums. compoment of the mechanical inspired body to maximize the system, the SEVT will be switch- favorable laminar flow over the ing to a composite chassis. since body. Most of the modeling SEVT also held a Home- composite panels have a higher is done in Rhino 3D, while the coming Party for the re- strength to weight ratio than steel. meshing and simulation is done turn of the latest car, Arc- Again this year, the aerodynam- through Ansys’s CFD packages, turus, from the 2015 World Solar Challenge. Open to the entire MIT community, students, staff, and faculty alike were able to see the Below: Flux, this year’s car, as car in person, talk to cur- rendered in Rhino.
Details
-
File Typepdf
-
Upload Time-
-
Content LanguagesEnglish
-
Upload UserAnonymous/Not logged-in
-
File Pages8 Page
-
File Size-