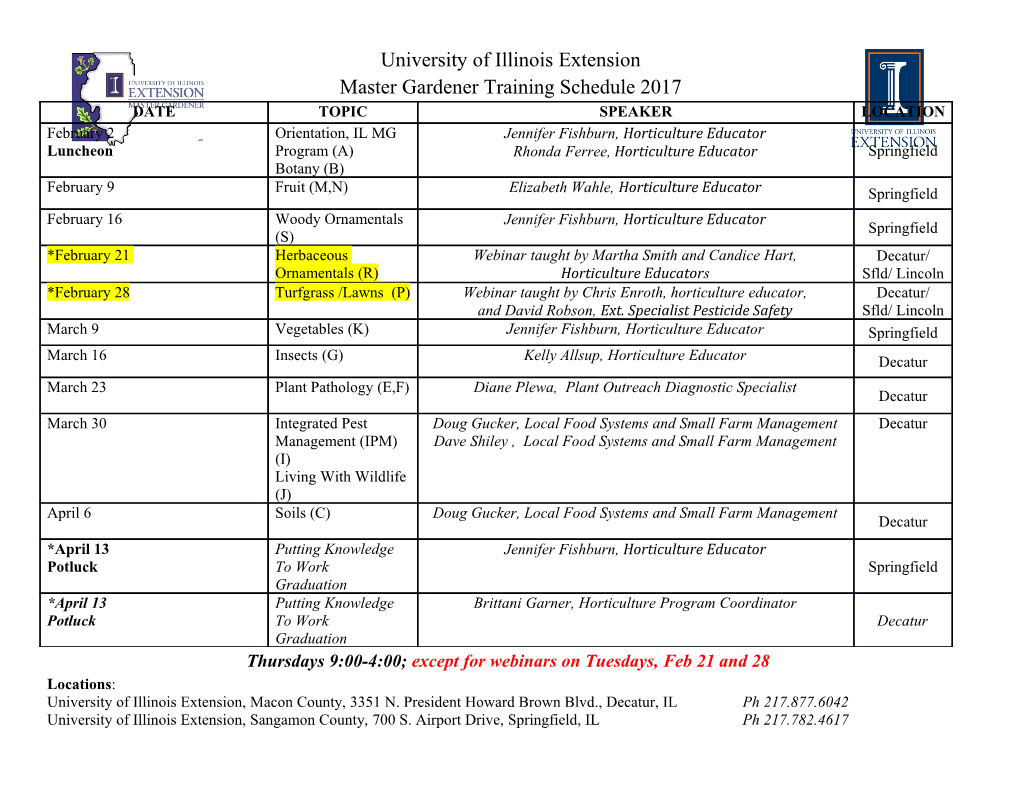
--- U.S. Department ---s of Transportation People Saving People National Highway http://www.nhtsa.dot.gov Traffic Safety Administration DOT HS 808685 Final Report January 1998 Development, Evaluation, and Demonstration of a Tractor Trailer Intelligent Communication -and Power Link a This document is available to the public from the National Technical Information Service, SpringfIeld, Virginia 22161 1 Report No 2. Government Accession No 3 Recipient's Catalog No DOT HS 808 685 4 Title and Subtitle 5 Report Date Development, Evaluation, and Demonstration of a January 1998 Tractor Trailer Intelligent Communication and 6 Performmg Organization Code Power Link 7 Author(s) 8 Performmg Organization Report No T. J. Wissing; J. Mazur; M. Leonard; F. Goeschel; C. Luebke 9Performmg Organization Name and Address 10 Work Umt No (TRAIS)n code Eaton Corporation Corporate Research & Development 2620 1 Northwestern Highway 11 Contract of Grant No P.O. Box 766 DTNH22-95-R-0700 1 Southfield, MI 48037 12 Sponsormg Agency Name and Address 13Type of Report and Penod Covered U. S. Department of Transportation Final Report Federal Highway Administration and National Highway Traffic Safety Administration 14 Sponsoring Agency Code 400 Seventh Street, S.W. Washington, DC 20590 15 Supplementary Notes Team members: PACCAR, Grote Industries, Inc., American Trucking Association Foundation, Great Dane Trailers Inc., Thermo Ring Corporation, Caterpillar, and Eaton Corporation 16 Abstract Technology offers a significant potential to improve the productivity and safety of the motor carrier industry. To date, the application of new technology to commercial vehicles has been limited to single unit trucks and truck tractors because of constraints inherent in the present combination-unit truck trailer electrical powering and communication system.A number of possibilities have been suggested to address this issue including, but not limited to, radio/telemetry communication among units in the combination, multiplexing, voltage enhancement, wiring system upgrade, and additional electrical circuits.This report explores the multiplexing approach. This approach switches six of the seven wires in the standard SAE J1067 cable and 5560 connector to two 51939 communication lines and four full time power lines, leaving one wire for ground.The system uses personal computer hardware and power switching in custom modules.Additional safety and productivity enhancing features have been added to the combination unit to demonstrate the potential of the systems. These features are: 1) advanced lighting multiplex modules, 2) trailer ID, 3) trailer air brake reservoir low pressure, 4) ABS warning light in the cab, 5) trailer parking brake status/brake status, 6) trailer air suspension pressure, 7) tandem axle load, 8) rear object detection, 9) side object detection, and 10) refrigeration status in the trailer. 17 Key Words 18. Distribution Statement Multiplex Electrical Connector Document is available to the public through the National Cable Wiring Communication Technical Information Service, Springfield, VA22161 19 Security Classif (of this report) 20Security Classif (of this page) 21 No of Pages 22 Price Unclassified Unclassified 41 Form DOT F1700.7 (8-72) Reproduction of completed page authorized TABLE OF CONTENTS Page 1. PROGRAM OVERVIEW......................................................................................................... 2 1.IOBJECTIVE........................................................................................................................................ 3 1.2TECHNICAL APPROACH..................................................................................................................... .3 1.3TEAM MEMBERS ANDRESPONSIBILITIES............................................................................................ .4 2. SYSTEM OVERVIEW.............................................................................................................5 2.1DESIGN SUMMARY............................................................................................................................. 5 2.2 JUSTIFICATION OF DESIGN APPROACH................................................................................................ 7 2.3HARDWARE AND SOFTWARE ARCHITECTURE..................................................................................... .8 2.4COMPATIBILITY WITH EXISTINGSYSTEMS............................................................................................ 9 3. DETAILED SYSTEM DESCRIPTION................................................................................ 11 3.1GABLE DESIGN &EMGTESTING...................................................................................................... 1 1 3.2TRACTOR&TRAILERWIRING........................................................................................................... 12 3.3PACKAGING..................................................................................................................................... 14 3.4 ELECTRONICS.................................................................................................................................. 18 3.5SOFTWARE...................................................................................................................................... 22 4. TESTING AND EVALUATION............................................................................................24 4.1BOARDTESTING.............................................................................................................................. 24 4.2TRUCKMUXTM FULLVEHICLE RADIATEDEMISSIONTESTS................................................................. .24 4.3ROADTEST RESULTS..................................................................................................................... .24 5. CONCLUSIONS. 27 6. RECOMMENDATIONS. 28 7. ACRONYMS. 29 8. REFERENCES. 30 9. APPENDICES..........................................................................................................................31 9.1 APPENDIX AALTERNATIVE APPROACH ASSESSMENTS.....................................................................31 9.2 APPENDIX BTRAILERWIRINGDIAGRAM.......................................................................................... 36 9.3 APPENDIX GWIRING HARNESSVOLTAGE DROP CALCULATIONS..................................................... .37 Table of Contents NHTSA’s Office of Crash Avoidance Research conducts and manages research intended to: analyze driver-vehicle interaction; identify specific vehicle design, components, or parameters associated with driver performance errors and resulting collisions; and develop and evaluate vehicle-based collision avoidance countermeasure concepts and devices. There are approximately 1.6 million truck tractors and 3.6 million trailers in use in the motor carrier industry today. Technology offers a significant potential to improve the productivity of the industry and help reduce the approximately 200,000 crashes in which these vehicles are involved each year. To date, the application of new technology to commercial vehicles has generally been limited to single unit trucks and truck tractors because of constraints inherent in the present combination-unit truck trailer electrical powering and communication system. These constraints are a small number of hard-wired circuits. More circuits or equivalent technology are needed to do more with the trailer. Traditionally, the US trucking industry equipment needs have been supplied by the truck/tractor manufacturer (supplying the towing unit) and the trailer manufacturer (supplying the cargo space to move goods). The two units are married at the fifth wheel of the power unit and the king-pin of the trailer. Communication and powering between the tractor and trailer consists of supplying power and control from the tractor to the running lights of the trailer through the standard seven-pin electrical connector (six circuits and one ground). One of the primary reasons for lack of technology change is the limited versatility of the standard six-circuit connection between tractors and trailers operating in the US. Observing this, the defense, aerospace, and computer industries have begun to focus on commercial vehicle applications as a potential new market for their advanced technologies to improve safety, efficiency and productivity. Vehicle/unit locators, vehicle/driver trip loggers, on-board weight measurement and recording systems, vehicle maintenance status monitor/recorder/transmitters, administrative credentials transponders, etc., are envisioned, and in many cases, already being installed on trucks and tractors, resulting in significant operational efficiency benefits. Likewise, side-, rear-, and forward-looking collision avoidance systems, driver performance monitors, anti-lock and electronic braking systems, brake maintenance status monitors, etc., can enhance commercial vehicle operational safety performance. To date, the application of these developing technologies to commercial vehicles has been limited predominately to the power unit or tractor. There is clearly a need to overcome the inherent constraints presently found in the communicating and powering system between tractors and trailers. These constraints are exacerbated in the case of multi-unit combination tractor/trailers, the vehicle type which will likely have an increased future role in improving the productivity of the motor carrier industry. The ability to install advanced
Details
-
File Typepdf
-
Upload Time-
-
Content LanguagesEnglish
-
Upload UserAnonymous/Not logged-in
-
File Pages43 Page
-
File Size-