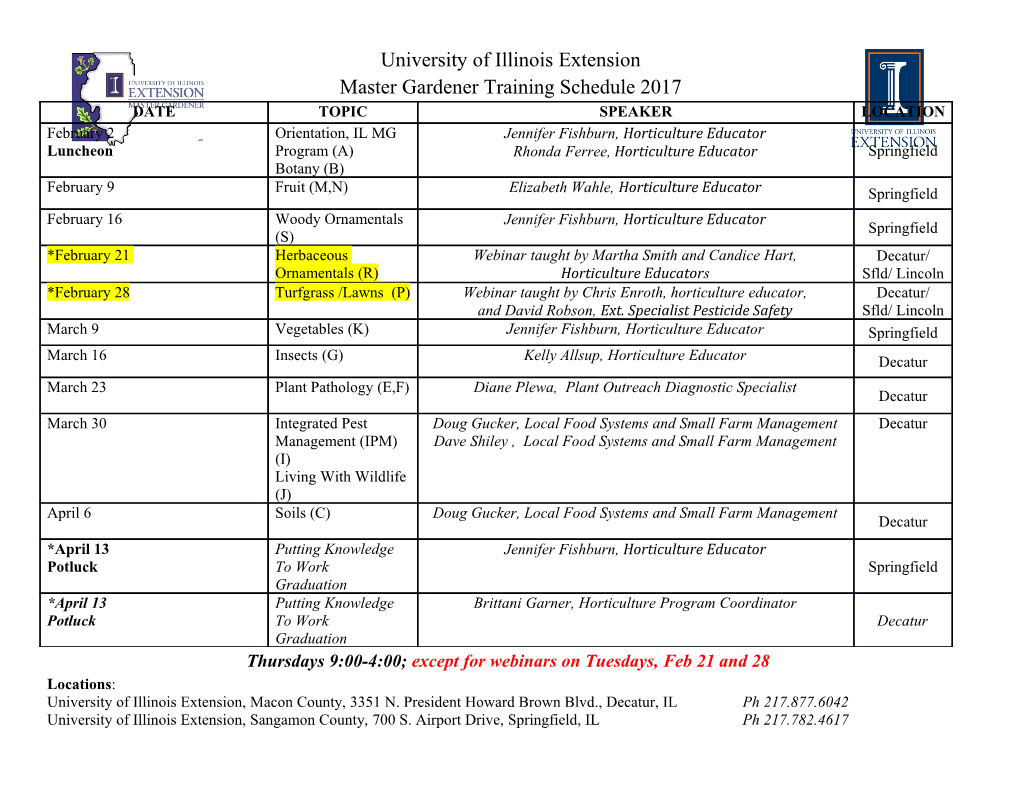
Quality Management System Standards wo studies have revealed that over- attributable to numerous factors, some that all awareness of the ISO 9000 Inter- are obvious and inherent in our business Tnational Quality Management culture, such as accelerated schedules and ISO 9000 System Standards among U.S. businesses is delivery requirements, increased labor still below 50 percent [1] [2]. This article costs, increased customer expectations, and standards are good is intended to increase general awareness international competition. Another factor for helping owners, shareholders, execu- that is significant in this evolution is the business practices tives, and project managers address “Human Factor.” Basically, people have inevitable decisions regarding the stan- pride in their work and in general do not that will improve dards. In particular, project managers are like to have it “inspected,” especially with faced with the daily responsibility for the potential fear of being wrong. communications, ensuring provisions exist for implementing The most significant factor with the requirements described in the standards entire quality management issue is: Who is efficiency, and applicable to project-specific products responsible for product or service quality and/or services. throughout the processes of performing the profits while Currently, it is true that ISO quality work internal and external to each organi- standards apply to fairly well defined busi- zation? It is this very factor that is the root reducing errors, ness sectors and applications. However, cause for some continued confusion over over time these standards will prove their ownership of quality with many companies scrap, and rework. inherent quality improvement benefits for in U.S. business sectors. The most funda- any application. Also, as more owners, mental step in starting any quality manage- executives, and project managers recognize ment effort is to formally address this issue that baseline requirements in the standards so there is no doubt about the various qual- are merely good business practices that will ity-related roles within the company. The improve communications, efficiency, and primary tool of the Quality Professional for profits while reducing errors, scrap, and assisting the company with quality efforts is rework, the standards will automatically the quality management plan (discussed become prerequisites for managing pro- later). jects and operating companies. Project The three primary quality management managers will benefit by more accurately issues that most companies are currently measuring project quality performance. addressing for their own specific reasons are Total Quality Management (TQM), International Quality Movement Malcolm Baldrige National Quality Award, The concept of quality management has and ISO 9000 Quality System Standards. rapidly evolved and matured during the Each of these has its own set of objectives, Paul W. Gladieux past decade. Quality, as it applies to the conditions and criteria. A simple review operations of a business, has moved for- and comparison of the following TQM ward from the classical “Inspection Func- principles, Baldrige values/concepts, and tion” (error detection) to the more modern ISO system elements reveals common qual- “Quality Management Systems” approach ity-related data as it applies to overall com- (error prevention). This evolution is pany performance. 22 PM Network • February 1995 Figure 1. Timeline Toward ISO 9000 Standards [6] European Spain and Removal of Coal and Steel EC Greece Portugal Trade Community Established Joins EC Join EC Barriers ’51 ’58 ’81 ’86 EC – 92 ? ? ’49 ’57 ’73 ’85 ’87 ★ ★★ NATO Treaty of Rome Denmark EC Single European Act (SEA) Belgium Ireland White Amended Treaty France and U.K. Paper of Rome Germany Joins EC Italy Luxemburg Netherlands TC – 176 ISO 9000 ISO 9000 Formed Standards Standards Published Revised ’80 ’87 ’94 ★ Treaty of Rome: Goal to create integrated community-wide market free of restrictions on movement of goods, services, people, and capital. ★★ SEA: Goal of completing the Single Internal Market by 1992 and restructuring decison-making procedures. TQM/Baldrige/ISO Principal support for the program quality system registration. Achieving Total Quality Management. During the comes from The Foundation for the registration does not guarantee defect- early and mid ’80s many events took Malcolm Baldrige National Quality free products and services; however, it place that helped shape what is now Award, established in 1988. The award does demonstrate that a company has a generally accepted as TQM principles. is named for Malcolm Baldrige, who system in place for affecting and improv- Some of the events included The served as Secretary of Commerce from ing quality—a distinct competitive Department of Defense Master Plan on 1981 until his tragic death in 1987. The advantage. System development/registra- TQM, the Commerce Department’s award criteria framework addresses tion takes 9 to 24 months, depending on concerns with foreign competition, seven core values and concepts: leader- the company scope of operations. The numerous new books on workplace ship; information and analysis; strategic 1994 revised standards include guide- changes including Japan’s work quality planning; human resource lines and contractual models: processes, and the influences of U.S. development and management; man- Guidelines quality gurus W. Edwards Deming, agement of process quality; quality and ISO 9000-01 Guidelines on Selection Joseph M. Juran, Phil Crosby, and operational results; customer focus and and Use Armand V. Feigenbaum. The principles satisfaction. ISO 9004-01 Guidelines on Manage- of TQM include determine customers’ ISO 9000 Quality Systems Stan- ment/System Elements requirements; perform to customers’ dards. The five generic quality manage- Contractual Models requirement; implement defect preven- ment standards were developed by the ISO 9001 20 Quality Management tion systems; performance measurement International Organization for Stan- Elements (full scope) by cost of quality; zero defects as com- dardization (Technical Committee TC- ISO 9002 19 Quality Management pany performance standard; everyone 176) based in Geneva, Switzerland [3]. Elements accountable for meeting requirements The committee was commissioned in ISO 9003 16 Quality Management (total employee involvement). 1980 and the standards were published Elements Malcolm Baldrige National Quality in 1987. The standards (includes three Award. This award was created by Pub- for contractual definition) provide a For example, ISO 9001, Quality lic Law 100-107 and signed into law on basis for implementing and improving Management System Elements (20 full August 20, 1987 [4]. The Award Pro- quality management and quality assur- scope), includes: gram, responsive to the purposes of ance within any product or service 4.1 Management Responsibility Public Law 100-107, led to the creation company. Ultimately the standards pro- 4.2 Quality System of a new public-private partnership. vide the basis for a company to achieve 4.3 Contract Review PM Network • February 1995 23 ■ ISO 9000 Figure 2. Timeline Toward Quality System Excellence TQM ? ? Malcolm No Quality Meet ISO 9000 Baldridge World-Class System Specifications Standards Award System Military ISOs Plus Deming Beyond Standards Industry-Specific Prize Deming Standards ??When Do You Implement TQM Principles? 4.4 Design Control require numerous products to be identi- standpoint (see historical key dates, 4.5 Document and Data Control fied with applicable CE Product Marks below). Also, ISO has not received the 4.6 Purchasing prior to entry into the European mar- visibility in the U.S. that TQM/Baldrige 4.7 Control of Customer-Supplied ket (CE—Communaute Europeene—is have, primarily because the perception Product a six-character label, the 3rd through is that ISO 9000 is only a requirement 4.8 Product Identification/Traceability 5th characters specify under which to perform work in Europe. Some 4.9 Process Control accrediting body certification was pro- companies have spent thousands of 4.10 Inspection and Testing vided) [9]. ISO 9000 quality system dollars trying to achieve Baldrige status 4.11 Inspection, Measuring, and Test implementation and registration in and then usually figure out that they do Equipment many cases will be the method used to not even have the basic quality man- 4.12 Inspection and Test Status verify, through documentary evidence, agement system that ISO addresses. 4.13 Control of nonconforming Product that products conform to specified Finally, the ironic part is that ISO will 4.14 Corrective and Preventive Action requirements. help provide the system framework for 4.15 Handling, Storage, Packaging, The standards have been adopted describing the quality data required for Presentation and Delivery by numerous countries around the TQM and Baldrige, even though ISO 4.16 Control of Quality Records globe and overwhelmingly adopted may not be a company requirement 4.17 Internal Quality Audits and implemented in the EC. U.S. rep- (see timeline towards quality system 4.18 Training resentatives from the Department of excellence) [5]. 4.10 Servicing Commerce and Office of European It is important, for perspective, to 4.20 Statistical Techniques Community Affairs are concerned that have the following key dates in mind in American companies have not posi- the development of quality concepts: tioned themselves soon enough for EC-92 Timeline Toward ISO achieving
Details
-
File Typepdf
-
Upload Time-
-
Content LanguagesEnglish
-
Upload UserAnonymous/Not logged-in
-
File Pages5 Page
-
File Size-