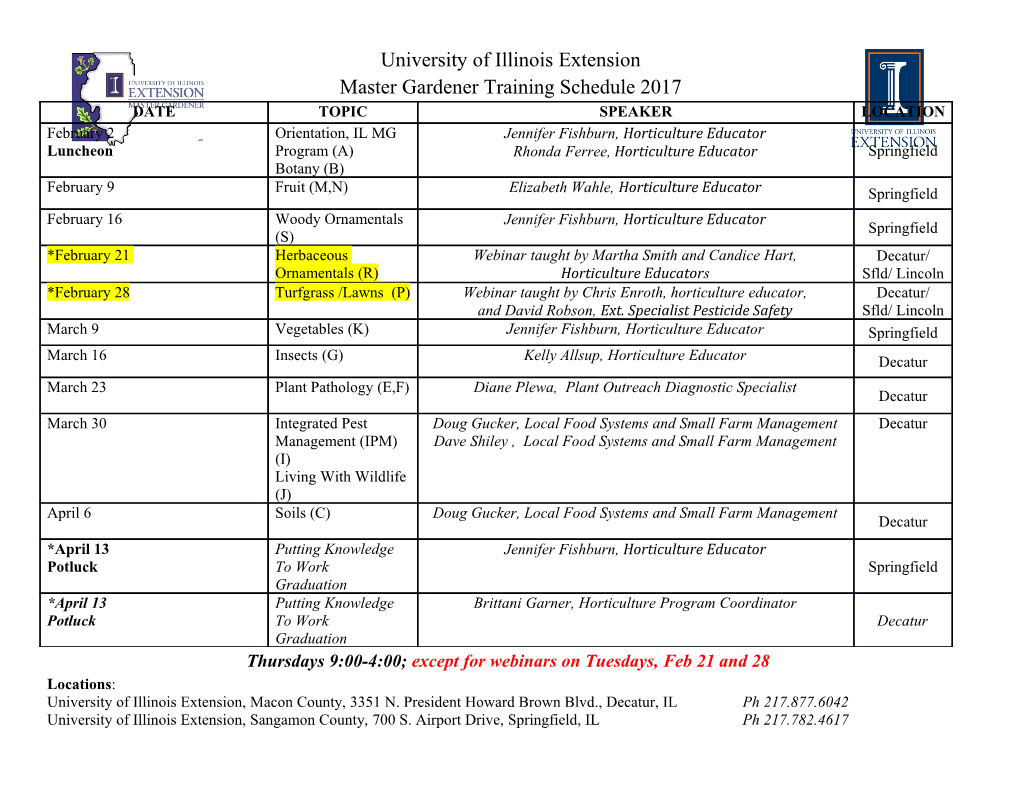
AB Guidance on Subsea Metrology International Marine Contractors Association IMCA S 019 www.imca-int.com February 2012 AB The International Marine Contractors Association (IMCA) is the international trade association representing offshore, marine and underwater engineering companies. IMCA promotes improvements in quality, health, safety, environmental and technical standards through the publication of information notes, codes of practice and by other appropriate means. Members are self-regulating through the adoption of IMCA guidelines as appropriate. They commit to act as responsible members by following relevant guidelines and being willing to be audited against compliance with them by their clients. There are two core activities that relate to all members: u Competence & Training u Safety, Environment & Legislation The Association is organised through four distinct divisions, each covering a specific area of members’ interests: Diving, Marine, Offshore Survey, Remote Systems & ROV. There are also five regional sections which facilitate work on issues affecting members in their local geographic area – Asia -Pacific, Central & North America, Europe & Africa, Middle East & India and South America. IMCA S 019 This guidance has been produced by IMCA, under the direction of the Offshore Survey Division, by Simon Barrett and Jose M Puig of DOF Subsea UK, with the assistance of Keith Vickery of ZUPT and Frank Pritz of Parker Maritime ASA. This guidance has undergone technical review by members of the the OGP (the International Association of Oil & Gas Producers) Geomatics Committee. www.imca-int.com /survey The information contained herein is given for guidance only and endeavours to reflect best industry practice. For the avoidance of doubt no legal liability shall attach to any guidance and/or recommendation and/or statement herein contained. © 2012 – International Marine Contractors Association Guidance on Subsea Metrology IMCA S 019 – February 2012 1 Executive Summary . .1 2 Glossary . .3 3 Introduction . .5 3.1 Terminology . .6 4 Subsea Metrology Requirements . .7 4.1 Typical Required Accuracies . .9 5 Subsea Metrology Survey Methods . .11 5.1 LBL Acoustic Metrology . .11 5.2 Diver Taut Wire Metrology . .15 5.3 Digital Taut Wire Metrology . .16 5.4 Photogrammetry . .17 5.5 INS Metrology . .20 5.6 Subsea Metrology Systems Compared . .22 6 Subsea Metrology Deliverables . .23 6.1 Computations . .23 6.2 Reporting and Documentation . .24 7 References and Further Reading . .25 Appendices A Dimensional Control Requirements for Metrology . .27 A1 Rotation of Dimensional Control Offsets . .27 B Typical Subsea Metrology Diagram . .29 C Comparison of Subsea Metrology Systems . .31 1 Executive Summary Subsea metrology is the process of acquiring accurate and traceable dimensional measurements for the design of subsea structures, primarily interconnecting pipelines. Pipeline interconnections are required to join subsea assets to complete the flow of hydrocarbons from the reservoir to processing and storage facilities. The objective of the subsea metrology survey is to determine accurately the relative horizontal and vertical distance between subsea assets, as well as their relative heading and attitude. This information is then used by pipeline engineers to design connecting pieces to join the assets together. This document explores five of the most common subsea metrology techniques related to interconnecting pipelines – long baseline (LBL) acoustics, diver taut wire, digital taut wire, photogrammetry and inertial navigation systems (INS). The purpose of the document is to: u Describe, compare and contrast the techniques; u Provide information on the techniques which may be useful to surveyors and surveying organisations; vessel personnel (marine, diving, ROV, etc.); design engineers, fabricators and client organisations. An example is the accuracy of the metrology and how this impacts fabrication tolerances/fit of the interconnecting pipeline, where lack of fit influences the ability to install and create a pressure tight joint as well as possibly influencing the working life of the interconnection. Long baseline (LBL) acoustics is the most commonly used subsea metrology technique in use today. This method is most widely used because it is adaptable, has redundancy and the results can be processed within hours. It is also attractive because the results can be referenced to an absolute datum. The disadvantages are that it is susceptible to subsea noise and it is equipment and time intensive. Diver taut wire metrology is essentially a tape measurement of the direct distance between hubs. This method was the first subsea metrology procedure employed by divers and was designed primarily for diver operations on horizontal spools. It is still widely used. Digital taut wire is a more sophisticated version of the diver’s tape measurements. Additional sensors provide a more accurate distance measurement; depth is also resolved with pressure sensors and relative hub attitude with digital inclinometers. However it still requires line of sight and is not redundant. There is a limitation on the length of spool measured once the weight of the wire causes sagging giving a linear distance error. Photogrammetric survey has only recently been developed successfully for subsea metrology applications. The basis of photogrammetry is to build a three-dimensional model based on a sequence of two-dimensional photographs. Measuring bars placed on the seabed and reflective markers on the structures provide scaling and reference. The processed images are used to derive a three-dimensional model of the positions of the hubs, the seabed and any other points of interest on the subsea structures. The main advantage of this system is that in a single survey a very high quantity of information can be gathered. The image processing required makes very intensive demands on computer time. Photogrammetry requires good subsea visibility. IMCA S 019 1 INS metrology is relatively new to the offshore industry. The use and availability of inertial navigation systems has greatly increased in recent years. Inertial navigation systems (INS) use three accelerometers and three gyros to compute a position based on a known start point and the measured changes in velocity and attitude. Unaided INS do not need an outside signal or reference to compute a position; because they are self-contained they do not require line of sight, nor are they affected by poor subsea visibility or a noisy subsea acoustic environment. The main drawback of INS metrology is that inertial sensors have drift associated to them. This sensor drift increases over time and requires some form of correction, generally provided by input from other positioning systems. 2 IMCA S 019 2 Glossary CAD Computer aided design C-O Computed minus observed correction CTD Conductivity, temperature and depth sensor DSP Digital signal processing DVL Doppler velocity log DWG Drawing DWPLEM Deep water PLEM EDM Electronic distance measurement FOG Fibre-optic gyro IEEE Institute of Electrical & Electronic Engineers (UK) IMCA International Marine Contractors Association IMU Inertial measurement unit INS Inertial navigation system ISA Inertial sensor assembly LBL Long baseline OP Observation point PLEM Pipeline end manifold PLET Pipeline end termination QC Quality control RLG Ring laser gyro RMS Root mean square IMCA S 019 3 ROV Remotely operated vehicle SVP Sound velocity profile TRF Terrestrial reference frame UTM Universal Transverse Mercator USBL Ultra short baseline UNESCO United Nations Educational, Scientific, and Cultural Organization σ Sigma. Represents one standard deviation from the mean 4 IMCA S 019 3 Introduction This document provides guidance on the most commonly used subsea metrology techniques in use today. These are long baseline (LBL) acoustics, both diver taut wire and digital taut wire, photogrammetry and inertial navigation systems (INS). It covers the basics of subsea metrology, engineering requirements, the different methods and technologies, and some of the advantages and limitations of each technique. The document does not compare or evaluate different manufacturers’ products or services, or the specific performance of systems, and does not endorse or recommend a specific type, model or make of system. However, it should be noted that the use of diagrams and references to proprietary elements and systems may be necessary in a specialised technology such as acoustic positioning. LBL acoustic systems and techniques are covered in more detail as these systems are generally the most adaptable and most widely used in the industry today. However, it should be noted that the pace of technical change and on-going development of deep water fields means that other subsea metrology methods are being developed, including photogrammetric metrology and INS metrology. The objective of subsea metrology is to determine accurately the relative horizontal and vertical distance between subsea assets, as well as their relative heading and attitude. Most commonly this is for pipeline connections and the document uses this work as an example throughout. The information determined by subsea metrology is then used by pipeline engineers to design a connecting piece to join the assets together. These connecting pieces are fabricated from steel allowing for some flexibility; however they require tight fabrication tolerances to ensure they meet their intended design life. Their design is twofold. The primary aim is to connect the pipeline
Details
-
File Typepdf
-
Upload Time-
-
Content LanguagesEnglish
-
Upload UserAnonymous/Not logged-in
-
File Pages35 Page
-
File Size-