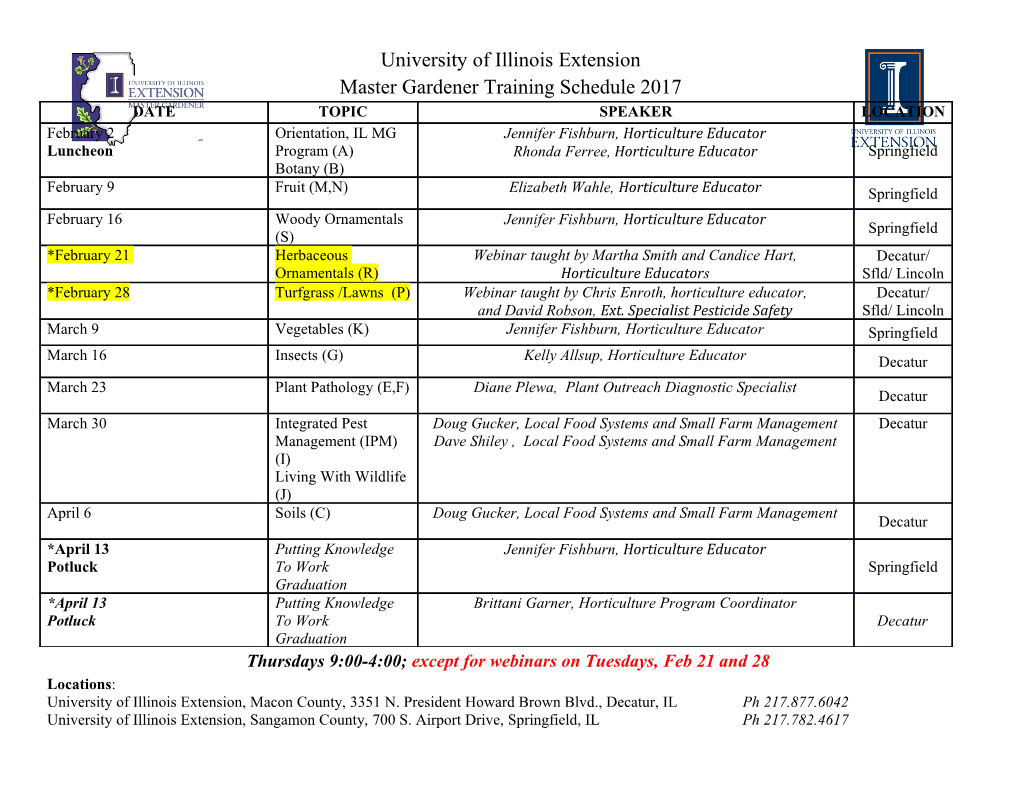
Zintek® 200 XT Zinc flake coatings from Atotech General metal finishing Zinc flake coatings www.atotech.com The neXT level base coat Zinc flake coating systems Zinc flake technology provides a high grade of corrosion pro- tection using combinations of specialized base and top coats. Largely embraced by the fastener industry, such coatings find widespread use within a variety of applications: ranging from fasteners, hose clamps, clips or brake components for the automotive industry, special fasteners in the wind power, con- struction and other industries. Atotech offers a comprehensive range of processes including silver and black finishes for differ- ent application areas. The coatings are completely Cr(VI)-free and fulfill global automotive performance requirements. Features and benefits • Inorganic premium silver zinc flake base coat • Outstanding cathodic corrosion protection • Exceptional performance in Neutral Salt Spray Test (NSST) as well as Cyclic Corrosion Testing (CCT) • Excellent delay in white rust formation • High color stability Corrosion resistance • Very good adhesion Base coat Top coat Durability • Attractive silver appearance 8 µm – >1,700 h* • No hydrogen embrittlement • Free of harmful heavy metals such as Cr(VI), 8 µm – 6 cycles** cadmium, cobalt, lead or nickel 10 µm – >2,000 h* • Combinable with Atotech’s top coats Corrosion resistance acc. to *ISO 9227 / **Ford L-467 and layer thickness may vary depending on part geometry, substrate and application method. Zintek® 200 XT Zinc flake coatings from Atotech © Atotech 07/18 Atotech © Application Top coat combinations • Dip-spin • With inorganic Zintek® Top • Rack-spin • With organic Techseal® • Spray • With organic Techdip® Parts (application) Application parameters • Fasteners • Application viscosity: 40 – 50 sec • Chassis parts • Curing time: 15 – 45 min • Stamping parts • Curing temperature: 220 – 260 °C • Brake components • Recommended 30 min at 250 °C object • Springs temperature • Clips Coefficient of friction Technical data • No defined coefficient of friction (µtot) • Delivery density: 1.40 – 1.55 g/cm³ (at 23 °C) • Stability in sealed drums: 24 months • Theoretical coverage rate: 25 m²/kg (based on 8 µm dry film) Corrosion performance (8 μm layer thickness) Start >1,800 h* Start 6 cycles** Atotech Group Untergasse 47 65468 Trebur-Geinsheim +49 6147 50130 [email protected] Corrosion Protection Competence Center www.atotech.com.
Details
-
File Typepdf
-
Upload Time-
-
Content LanguagesEnglish
-
Upload UserAnonymous/Not logged-in
-
File Pages2 Page
-
File Size-