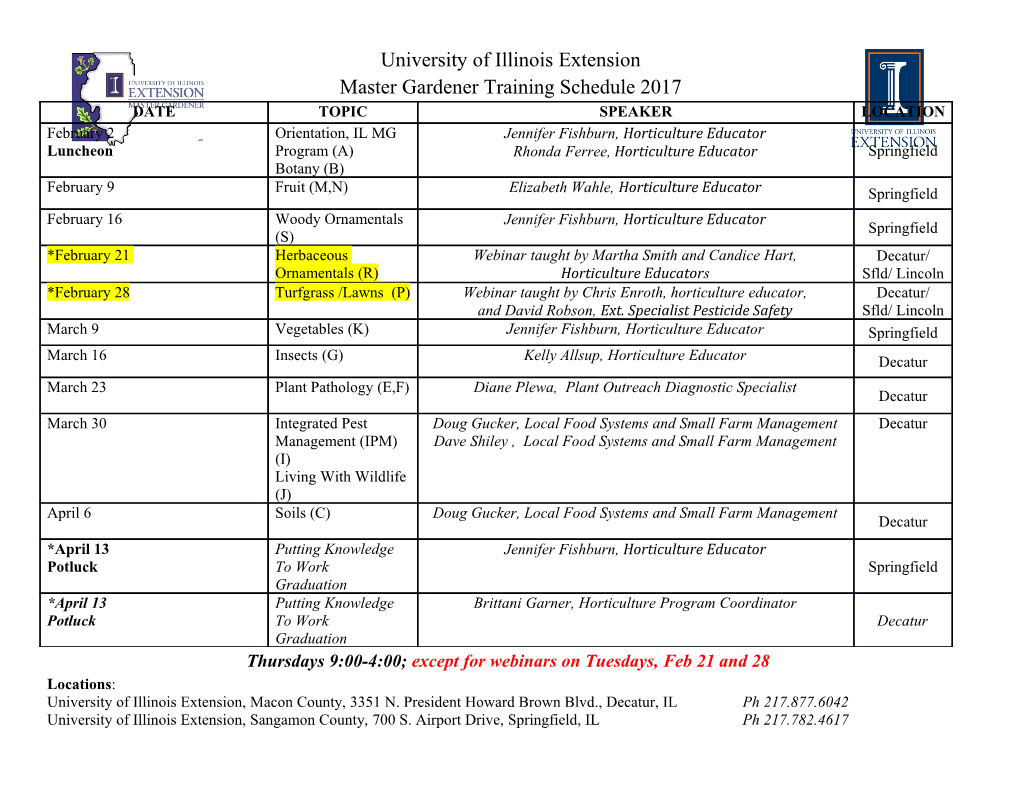
United States Patent (19) 11 Patent Number: 4,585,701 Bartoszek et al. (45) Date of Patent: Apr. 29, 1986 54) COMPOSITES OF POLYVINYLIDENE 3,524,906 8/1970 Schmitt et al. ...................... 525/199 FLUORDE ALLOYS AND 3,968, 196 7/1976 Wiley .............. ... 264/171. THERMOPLASTC POLYMERS AND THEIR 4,051,293 9/1977 Wiley .............................. 428/421 X PREPARATION 4,215,177 7/1980 Strassel ........................ 428/424.6 X 4,221,757 9/1980 Strassel ............................... 264/171 75 Inventors: Edward J. Bartoszek, Jeffersonville, 4,226,904 10/1980 Olivier et al... ... 156/322 X Pa.; Steven F. Mones, Newark, Del. 4,289,560 9/1981. Simons ............ ... 156/244.18 73) Assignee: Pennwalt Corporation, Philadelphia, 4,291,099 9/1981 Strassel ... ... 428/421 4,317,860 3/1982 Strassel ....... ... 428/42 Pa. 4,317,861 3/1982 Kidoh et al. ........................ 428/421 21) Appl. No.: 580,483 FOREIGN PATENT DOCUMENTS 22 Filed: Feb. 15, 1984 0060421 9/1982 European Pat. Off. ............ 264/171 51 Int. Cl'.............................................. B32B 27/08 OTHER PUBLICATIONS 52 U.S. C. ...................................... 428/421; 264/37; 264/171; 264/176 R; 428/424.2; 428/424.6; Pennwalt Technical Data Sheet, "KYNAR(R)/Acrylic 428/424.8 Alloys RC-9637 and RC-9638', 7/22/80. 58 Field of Search .................. 428/421, 424.6, 424.2, 428/424.8; 525/199; 264/171, 176 R, 37; Primary Examiner-Thomas J. Herbert 156/322, 244.18 (57) ABSTRACT 56) References Cited Composites of polyvinylidene fluoride alloys, and in U.S. PATENT DOCUMENTS compatible thermoplastic polymers are prepared by 3,253,060 5/1966 Koblitz et al. ...................... 525/199 two-layer coextrusion with recycling of scrap material. 3,448,183 6/1969 Chisholm .............................. 264/37 3,459,834 8/1969 Schmitt ............................... 525/199 11 Claims, 2 Drawing Figures 2 U.S. Patent Apr. 29, 1986 4,585,701 4,585,701 1 2 which comprises a mixture of a thermoplastic polymer COMPOSITES OF POLY WINYLDENE FLUORIDE which is incompatible with polyvinylidene fluoride and ALLOYS AND THERMOPLASTC POLYMERS previously formed composite material, joining to the AND THER PREPARATION surface of the first heat-plasticized stream within the conduit a second heat-plasticized stream comprising an BACKGROUND OF THE INVENTION alloy of polyvinylidene fluoride and an acrylate poly This invention relates generally to composite con mer, thereby forming a single stratified stream of heat structions of dissimilar polymers and more specifically plasticized material conforming to the cross-section of to composites of polyvinylidene fluoride/polymethyl the conduit, conveying the stratified stream to an extru methacrylate alloy compositions with dissimilar ther O sion die, passing the stratified stream of heat-plasticized moplastic polymers and to the method of making such material through the die, and cooling the stratified constructions by two-layer coextrusion with recycling stream emerging from the die to form a solid polymer of scrap material produced in the process. composite. Polyvinylidene fluoride resin (PVDF) is a high-per Also provided is a polymer composite comprising a formance member of the fluorocarbon polymer class, 15 protective layer comprising an alloy of polyvinylidene combining excellent resistance to chemicals and weath fluoride and an acrylate polymer, which is directly ering with ease of processing. It is, in many ways, a bound to a substrate comprising a homogeneous mix bridge between low-cost, general purpose polymers and ture of a thermoplastic polymer which is incompatible higher-cost, ultra-high performance fluoropolymers. with polyvinylidene fluoride, and polyvinylidene fluo One of the outstanding physical properties of PVDF is 20 ride-acrylate polymer-thermoplastic polymer compos its resistance to severe outdoor weathering conditions, ite material. which include ultraviolet radiation and harsh extremes of temperature and humidity. These properties make DESCRIPTION OF THE DRAWINGS PVDF an attractive prospect as a protective cap stock FIG. 1 schematically represents an apparatus for material when laminated to less durable polymers, such 25 as acrylonitrile-butadiene-styrene (ABS) and polyvinyl carrying out the process and preparing the composites chloride (PVC). A convenient method of forming such of the invention by two-layer coextrusion. composites or laminates is by coextrusion. Although FIG. 2 is a perspective view of a two-layer composite coextrusion processes involving dissimilar polymers to according to the invention. form composites are well-known, many are feasible 30 DETAILED DESCRIPTION only if an adhesive layer is employed to make a bond possible between incompatible materials. Generally, As with other fluoroplastics, PVDF is relatively inert coextrusion without an adhesive layer is possible only to most common materials which presents an adhesion with polymers possessing a high degree of compatibil problem when attempting to form composites to PVDF ity, such as within a family or class of polymers. When 35 and other materials. It is possible, however, to incorpo dealing with the relatively inert fluoropolymers, such as rate into the PVDF a substance which will facilitate PVDF, the obtaining of satisfactory adhesion between adhesion without sacrificing its excellent physical and layers in a two-layer coextrusion process has been ex chemical properties. Acrylate polymers such as poly tremely difficult. One such process for forming lami methylmethacrylate (PMMA) are such materials and nates of PVDF and polyurethanes is disclosed in U.S. are compatible with PVDF over the entire range of Pat. No. 4,221,757. The PVDF is selected to have cer compositions. Alloys of the two behave as homogene tain viscosity properties in order to obtain adhesion. ous materials. Alloys of PMMA and PVDF are de Another such process for forming laminates is disclosed scribed, for example, in U.S. Pat. No. 3,253,060. in U.S. Pat. No. 3,968,196 where PVDF is laminated to In the process of the invention, useful acrylate poly polystyrene by the control of viscosity properties. In 45 mers include homopolymers and copolymers of lower any such coextrusion process, scrap material is pro alkyl (methyl, ethyl, propyl, butyl) methacrylates in duced, for example, due to edge trimming of the prod cluding copolymers with minor portions of other acryl uct and during start-up when the correct processing ates and/or ethylenically unsaturated monomers, for conditions are being established to produce product example, styrene, alpha-methyl styrene, and acryloni which meets specifications. This scrap represents a loss 50 trile. In the present invention, we have found that alloys because it cannot be recycled to the process by incorpo of PVDF containing from about 20 to 50% by weight ration into the base resin due to the incompatibility of of the acrylate polymers provide excellent adhesion to PVDF with the base resin which causes a deterioration incompatible polymer substrates and still retain a signifi in the properties of the composite. We have now found cant share of the PVDF polymer properties. By adjust that composites of PVDF alloys with other thermoplas 55 ing the PVDF/acrylate ratio to from about 50/50 to tic polymers including acrylonitrile-butadiene-styrene 80/20 (by weight) and preferably from about 60/40 to terpolymer (ABS), polycarbonate (PC), PC/ABS al 70/30, an optimum balance of physical properties and loys, polyvinylchloride, methylmethacrylate-acrylo chemical resistance for any given application can be nitrile-butadiene-styrene (MABS), and other acrylic achieved. Although PVDF homopolymers are pre polymers can be prepared without need for an adhesive ferred, vinylidene fluoride copolymers containing layer or the requirement for matching of viscosity prop minor amounts, e.g., up to about 30% by weight, of erties, with the ability to recycle scrap composite mate other ethylenically unsaturated monomers such as tetra rial to the process. fluoroethylene, chlorotrifluoroethylene, hexafluoropro pylene, ethylene and the like, can also be used and such BRIEFSUMMARY OF THE INVENTION 65 copolymers and included in the term polyvinylidene In accordance with this invention, there is provided a fluoride as used herein. The alloy not only provides for process for making a polymer composite comprising direct adhesion of the two polymer layers but also per conveying in a conduit a first heat-plasticized stream mits the grinding or cutting and recycling of scrap com 4,585,701 3. 4. posite polymer material to the thermoplastic polymer The bringing together and adhering of the PVDF substrate layer. The presence of the acrylate polymer alloy and the incompatible thermoplastic polymer is provides sufficient compatibility between the thermo achieved by using a coextrusion process. Coextrusion is plastic polymer and the PVDF to avoid significant a well known technique and can be accomplished, for deterioration of the properties of the thermoplastic example, by using either a multimanifold coextrusion polymer substrate layer. The scrap composite material die or the coextrusion feedblock approach. FIG. 1 illus can be derived from either the current or a previous trates apparatus which employs the feedblock tech extrusion process. nique, where the individual melt streams come into For economic reasons, it is recommended that the contact before entering the die, which may be prefera PVDF alloy layer be kept as thin as possible, although 10 ble because the materials are in contact for a longer this is not a performance necessity and layer thicknesses time. In a normal two extruder process, the cap stock of up to 0.015 inch or more can be used with preferred material, in this case the PVDF alloy, can be run in the thicknesses being from about 0.002 to 0.004 inch. Two smaller satellite extruder 2 (if the two extruders are of approaches can be used in order to make a thin PVDF different sizes). The cap stock material is melted in the alloy layer suitable as a cap stock material for ultravio 15 extruder barrel and pumped through satellite adaptor let sensitive polymer substrates.
Details
-
File Typepdf
-
Upload Time-
-
Content LanguagesEnglish
-
Upload UserAnonymous/Not logged-in
-
File Pages6 Page
-
File Size-