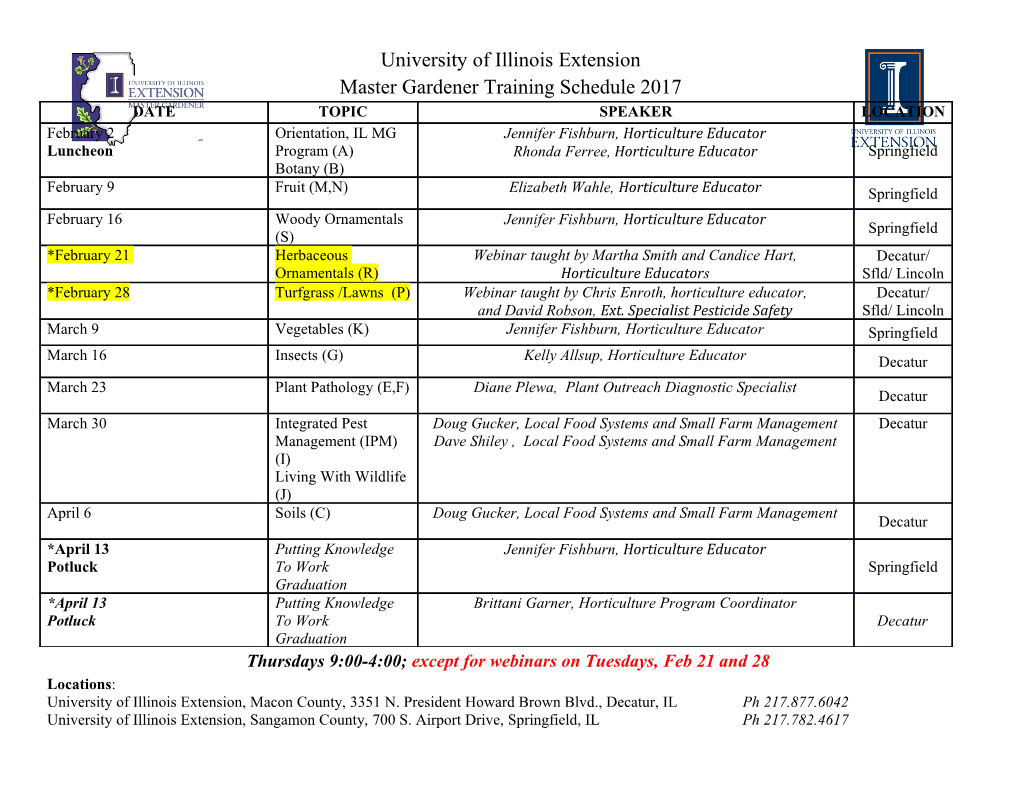
Topics in Shear Flow Chapter 2 – Pipe Flow Donald Coles! Professor of Aeronautics, Emeritus California Institute of Technology Pasadena, California Assembled and Edited by !Kenneth S. Coles and Betsy Coles Copyright 2017 by the heirs of Donald Coles Except for figures noted as published elsewhere, this work is licensed under a Creative Commons Attribution-NonCommercial-ShareAlike 4.0 International License DOI: 10.7907/Z90P0X7D The current maintainers of this work are Kenneth S. Coles ([email protected]) and Betsy Coles ([email protected]) Version 1.0 December 2017 Chapter 2 PIPE FLOW 2.1 Generalities On both historical and pedagogical grounds, fully developed flow in a smooth pipe of circular cross section is an ideal point of entry for technical fluid mechanics. The reason is that a crucial quantity, the friction at the wall, is proportional to the axial pressure gradient, which is usually easily measured. More than a century ago, exper- iments by Hagen, Poiseuille, Couette and others used this property to confirm the hypothesis of Newton that the viscosity of ordinary fluids, particularly water and air, is a real physical quantity that depends on the state of the fluid but not on the particular motion. These early experimenters encountered turbulence in larger facilities at higher speeds, and the issue quickly became the need for a better qualitative and quantitative appreciation of turbulence. In fact, it was an investigation of transition in pipe flow by Reynolds that led to the discovery of the fundamental dimensionless number that bears his name. Study of turbulent flow in smooth round pipes led about 1930 to development of the mixing-length model, which in some situa- tions still represents the best available approach to the problem of turbulent flow near a wall. An important mechanism, just beginning to be understood, involves the effect of the no-slip condition at the 59 60 CHAPTER 2. PIPE FLOW wall on turbulent fluctuations. Pipe flow is the vehicle of choice for exploring the effect of wall roughness and the effect of drag-reducing polymers on turbulent flow. Pipe flow is also a useful vehicle for in- vestigating heat transfer, with numerous practical applications. Sec- ondary flow in non-circular pipes exposes the non-Newtonian nature of the Reynolds stresses, unfortunately without exposing any plau- sible constitutive relations. Other variations on pipe flow, such as flow with curvature or flow with an abrupt change in cross section, reveal strong effects on mixing processes. Similarity laws originally developed for pipe flow provide a point of contact with the boundary layer and the wall jet. The main experimental disadvantage of pipe flow is difficulty of access for instrumentation, particularly optical instrumentation. A major source of experimental scatter in fundamental work is failure to provide sufficient length for the flow to become fully developed. 2.1.1 Equations of motion The Reynolds equations of mean motion were derived in SECTION 1.3.4 for the cylindrical polar coordinates sketched in FIGURE 2.1. These equations are easily specialized for the case of steady flow in a round pipe of radius R. To make the notation consistent with that for plane flow, take the axial, radial, and azimuthal coordinates as (x; r; θ) and the corresponding velocity components as (u; v; w). Take the mean flow to be fully developed, which is to say rectilinear. Thus v = w = 0, and u =6 0. All derivatives of mean quantities with respect to θ are zero, as are all derivatives with respect to x except @p=@x, this term being the engine that drives the flow. The continuity equation is moot. For simplicity, the overbar indicating a mean value will be suppressed hereafter except in the Reynolds stresses. The three momentum equations are reduced to @p 1 d du 0 = − + r µ − ρu0v0 ; (2.1) @x r dr dr @p 1 d 0 = − + ρw0w0 − r ρv0v0 ; (2.2) @r r dr 2.1. GENERALITIES 61 Figure 2.1: Cylindrical polar coordinate system and notation for pipe flow. 1 d 0 = − r2 ρv0w0 : (2.3) r2 dr The fluctuations u0; v0; w0 vanish at the wall. The three equations (2.1){(2.3) are rigorously correct, and must be satisfied by the mean flow under the specified conditions. The equations are obviously not complete, since there are three equations for six unknown quanti- ties. Two of the Reynolds stresses, −ρu0u0 and −ρu0w0, fail to ap- pear. Of these, the absence of the mean product u0w0 is expected if the turbulent motion is random. Given a sampled value for the axial fluctuation u0, it is reasonable to suppose, in view of the axial symmetry of the problem, that positive and negative values for the azimuthal fluctuation w0 are equally probable. That this argument can be dangerous will be demonstrated in SECTION 2.5.5, where it leads to a wrong conclusion for the viscous sublayer near a wall. In the case of −ρu0u0, the failure of the Reynolds equations even to con- tain this streamwise normal stress is embarrassing. It appears that nothing can be learned about this stress from the laws of mechanics in Reynolds-averaged form. At the same time, it is this Reynolds stress −ρu0u0 that is most easily and most commonly measured. 62 CHAPTER 2. PIPE FLOW Consider the three equations of motion (2.1){(2.3). The third equation (2.3) has the integral r2ρv0w0 = constant, and the constant is zero whether evaluated on the axis or at the wall. The second equation (2.2) is more instructive. Formal integration from r to R, with the boundary condition p = pw at the wall, gives R Z 0 0 − 0 0 0 0 w w v v p + ρv v = pw − ρ dr : (2.4) r r When the lower limit is taken at the pipe axis, r = 0, the integral diverges unless v0v0 = w0w0 on the axis. The equality is intuitively obvious. If two traverses are made along a diameter of the pipe to measure in one case the radial velocity fluctuation v0 along the traverse direction and in the other case the azimuthal velocity fluc- tuation w0 normal to it, the two measurements must be statistically equivalent on the axis. As the lower limit r in equation (2.4) approaches the upper limit R, the definite integral is eventually small compared with the term ρv0v0 on the left. In some vicinity of the wall, therefore, a useful approximation suggests itself; 0 0 p + ρv v = pw = constant : (2.5) This approximation will be examined more closely in SECTION X1. Finally, the quantity in parentheses in the first momentum equation (2.1) is evidently the total shearing stress τ, here defined with a change in sign in the derivative and in v0 because y = R − r is a more natural independent variable for an observer viewing the flow from the wall; du τ = − µ − ρu0v0 : (2.6) dr At the wall of the pipe, where all velocity fluctuations vanish, the corresponding value is du τw = −µ : (2.7) dr w 1Unclear reference, possibly 5.2.1 2.1. GENERALITIES 63 By assumption, the terms in parentheses in equations (2.1) and (2.2) do not depend on x, so that @2p @2p = = 0 : (2.8) @x2 @r@x It follows that @p=@x is a constant, independent of x and r, although p itself depends on x and also on r if the flow is turbulent, according to equation (2.4). Equation (2.1) in the form @p 1 drτ 0 = − − (2.9) @x r dr can therefore be integrated from r to R, with the boundary condition τ = τw when r = R, to obtain R2 − r2 @p Rτw − rτ = − : (2.10) 2 @x On putting r = 0, this becomes D @p τw = − ; (2.11) 4 @x where D = 2R is the diameter. The last expression is also easily obtained from a global momentum balance on a length of the pipe, given that @p=@x is constant. Elimination of @p=@x between equa- tions (2.10) and (2.11) yields finally the linear stress profile shown in FIGURE 2.2, τ r = : (2.12) τw R So far, the flow has usually not been specified to be either laminar or turbulent. In either case, equation (2.11) provides an accurate and unambiguous method for determining τw for fully de- veloped flow, and this property is the main reason that pipe flow is discussed here before all other flows involving walls. In a real pipe, there will be problems with entrance flow and development length, to be discussed in SECTION 2.2.1. The fact that the stress τ de- fined by equation (2.6) is linear in r also provides an opportunity for proof and calibration of instruments, such as hot-wire anemometers, 64 CHAPTER 2. PIPE FLOW Figure 2.2: The parabolic mean-velocity profile and the linear shearing-stress profile for steady laminar flow in a circular pipe. commonly used for measurement of the Reynolds shearing stress. See, for example, NEWMAN and LEARY (1950), KJELLSTROM¨ and HEDBERG (1970), and PATEL (1974). A more cogent use of equation (2.12), as one criterion for equilibrium at second order of a developing turbulent flow, will be taken up in SECTION 2.5.1. 2.1.2 Laminar flow If the flow is laminar, p is independent of r, according to equation (2.2), so that @p=@x becomes dp=dx. The velocity profile is the integral of equation (2.12), given τ = −µdu=dr, that takes the value u = uc (c for centerline) at r = 0 and satisfies the boundary condition u = 0 at r = R.
Details
-
File Typepdf
-
Upload Time-
-
Content LanguagesEnglish
-
Upload UserAnonymous/Not logged-in
-
File Pages144 Page
-
File Size-