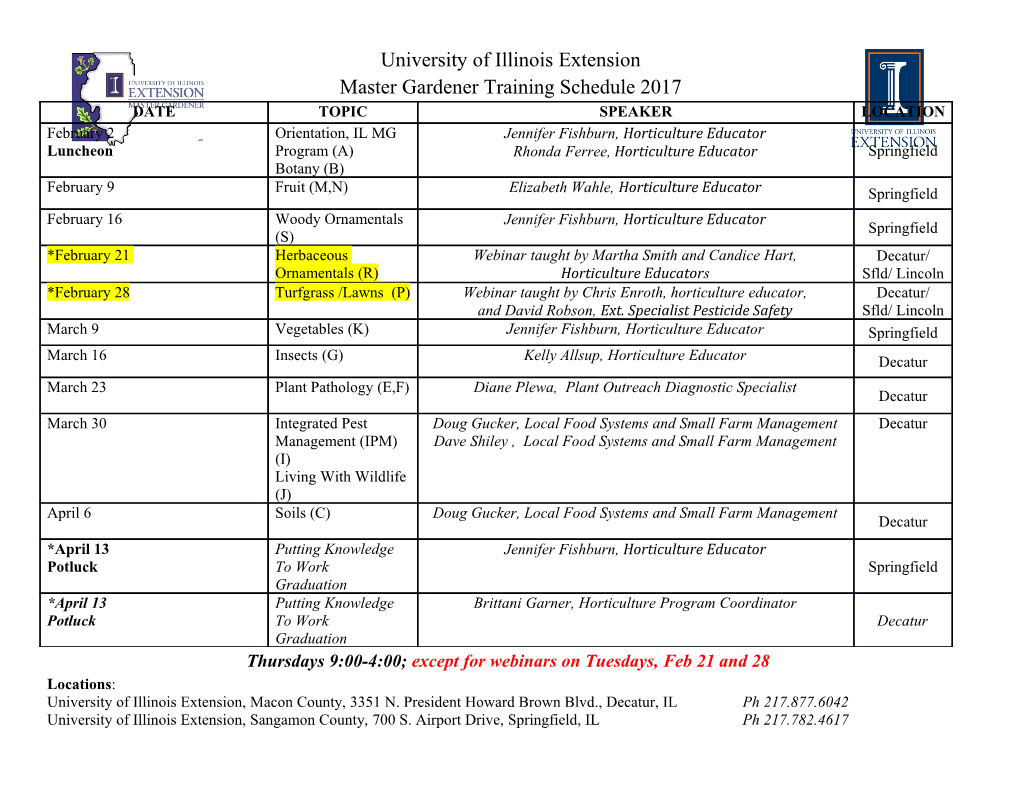
Sludge incineration: good practice and environmental aspects C M. Braguglia*, G. Mininni*, D. Marani* and V. Lotito** *Cnr - Istituto di Ricerca sulle Acque - Via Reno, 1 - 00198 Roma * Cnr - Istituto di Ricerca sulle Acque - via F. De Blasio 5 - 70123 Bari (E-mail: mininnifcbirsa. rm.cnr.it) Abstract. Growing difficulties in the sludge utilization in agriculture or landfill make incineration an attractive alternative for sludge disposal. Capital and operating costs and concern about gaseous emissions may however limit convenience and acceptance. In this paper a model is presented for optimisation of the cake concentration before the furnace, allowing an autogenous operation with a minimization of exhaust gas production. As far as emissions of heavy metals and organic micropollutants at the stack is concerned, results of tests on a demonstrative plant, including a fluidised bed and a rotary kiln furnace, are presented. The tests were carried out in different feeding (sludge alone or spiked with chlorinated hydrocarbons) and operating conditions (temperature of the afterburning chamber). Key words Energy recovery; heavy metals; incineration; PAH; PCDD/F; thermal drying. Introduction Sewage sludge after mechanical dewatering still contains high moisture content (60-80 %) with a relevant low heat value of 6,000-3,000 kJ/kg. Sludge incineration is therefore quite expensive due to high auxiliary fuel consumption. Consequently, optimisation of energy recovery is of predominant importance to minimize capital and operating costs of a sludge incineration plant and to render attractive such option. Typical design approach for energy recovery in sludge incineration performed by fluidised bed furnace considers the useof a sludge drying system, usually performed by an indirect dryer utilizing steam produced in the heat recovery section. Design of dryer, furnace, and boiler strictly depends on solids concentration before and after drying and on the temperature of exhaust gases after boiler. Energy conversion and recovery in a sewage sludge incineration process are discussed enlightening dryer integration in the process. In addition to fuel consumption, the key factor determining feasibility and acceptability of sludge incineration plants is the potential emission of pollutants at the stack, with emphasis on metals and organic micropollutants. In this framework the results of a research activity on sludge combustion carried out by the Water Research Institute of the Italian National Research Council, are presented. Tests were carried out on a demonstrative plant equipped with a fluidised bed furnace (FBF) and a rotary kiln furnace (RKF) with the aim to investigate factors affecting emissions at the stack. Sludge drying and combustion modelling Basic assumptions for mass and enthalpic balances of a drying/incineration process by fluidised bed furnace are reported in Table 1. Enthalpy balances were developed considering specific heat data reported by Perry & Green (1984). An algorithm was developed to calculate cake concentration for autogenous combustion. Methane consumption (Nm3 /kg wet sludge) decreases proportionally vs. feed cake concentration to the furnace. The minimum cake concentration for autogenous combustion is 45.9 %. Incineration of a more concentrated cake requires additional fresh air to keep furnace temperature at 850 °C with consequent increasing production of exhaust gas. Composition of exhaust gases from the furnace is reported in Figure 1. Increasing cake concentration up to the point of autogenous combustion, humidity shows a linear decrease from 28.2 to 24.6 %, while oxygen remains constant at 6 %. After this point the decrease of humidity is exponential due to air dilution, whereas oxygen increases to a maximum value of 12.1 % at a 90 % cake concentration. 523 Table 1. Assumptions for enthalpic and mass balances in sludge drying and incineration (Task Force on Thermal Destruction, 1992) Parameter Values Elemental analysis of loss on ignition of dry solids C 53 %, H 7.7%, O 32.7 %, N 5.6 %, S 1 % Outlet temperature from the dryer 100 °C Extraction of non condensable gas from the dryer 1.5 kg/kg evaporated moisture Gross heat value of volatile solids (VS) 22,486 kJ/kg Gross heat value of methane 38,083 kJ/Nnf Heat losses (% of inlet and/or developed) 5 % in the furnace and the boiler; 7 % in the dryer Loss on ignition with respect to dry solids 70% Excessof air for methane combustion 20% Excessof air for VS combustion What needed to attain at least 6 % of oxygen in the gas Exhaust gas temperature 850°C Conversion of nitrogen in VS to NO 10% — C02 —H20 — N2 —02 Sludge solids concentration (weight fraction) Figure 1. Composition of exhaust gas from fluidised bed furnace As far as thermal drying is concerned, the theoretical model was developed considering the use of an indirect dryer with a recycle of dried product to agglomerate sludge, thus increasing specific exposure surface and avoiding clogging. Normally, it is necessary to feed the dryer with sludge at a solid concentration higher than 60 %. It is also useful to by-pass part of feed cake and mix it with the dried product to reach the pre-set cake concentration before incineration. The scheme of the dryer is shown in Figure2. The theoretical model of the incineration furnace implies the following sequential calculations: 1) minimum critical concentration (xu)cr allowing to operate the furnace in autogenous conditions; 2) maximum quantity of heat which can be recovered in the boiler downstream the furnace when the furnace is fed at the (xu)cr concentration, considering that gases exit the boiler at 250 °C; 3) feed concentration (xo)cr to the dryer producing a dried cake at (xu)CT recovering the heat calculated at point 2); 4) if x0<(xo)cr it is possible to determine the function xu=f(x0) by imposing the balance of the recoverable heat in the boiler with that needed in the dryer; 5) if xo>(x0)cr it is possible to determine the excess heat which is produced in the boiler not needed for drying which is available for electric energy production with an overall efficiency of 31.8 %; 6) the sequential procedure can be repeated with xu-0.9 (feeding the cake to the furnace at the highest practicable concentration). 524 Vapours and incondensable Re cycle stream 0,9-0.6 By - pass stream k _ (0.9; Xu) 1 Figure 2. Scheme of an indirect dryer with internal recycle and by-pass Figure 3 shows the function xu=fi(xo): when the cake concentration is lower than 21.1 % heat produced in the boiler is not sufficient to dry the sludge at the concentration needed for autogenous combustion. With cake concentration higher than 21.1 % excess heat is available if dried sludge is produced at 45.9 % or otherwise it is possible to obtain dried sludge at higher concentration. 0,9 -* 0.8 - Dried sludge limit concentration 0.5 - for autogenous combustion=45.9 % 1 0.25 Cake concentration to the dryer (weight fraction) Figure 3. Dried sludge concentration vs. cake concentration Electric energy production from surplus steam for a plant serving one million of inhabitants was evaluated for two levels of sludge drying (45.9 and 90 %). The amount of electric energy obtained in the former case is 0.362 - 0.378 MW higher than in case of drying at 90 %. This can be explained considering that the enthalpy of the extra production of steam (about 1,830 kJ/kg dry solids) with a 90 % cake does not balance the heat required for sludge drying from 45.9 to 90 % (3,180-3,260 kJ/kg dry solids). Environmental aspects of sludge incineration Incineration leads to a great reduction of sludge and theoretically should result in the total conversion of the hazardous organic compounds to inorganic end products. Unfortunately, burning conditions are not ideal and generally they cause inefficiencies, mainly due to non-uniform temperature and mixing conditions inside the furnace. Cooling of hot gases in the combustion zone 525 due to the contact with the cool walls or locally reducing conditions can induce partial destruction and pyrolysis reactions. These inefficiencies lead to the formation of toxic organic compounds, referred to as products of incomplete combustion. Among them, special attention is devoted to PAHs for their relative abundance in the emissions and potential impact on human health (Akimoto et al., 1997, Ana et at, 1999, Eiceman et aL, 1979, Mascolo et al, 1999). Some authors showed that they are the starting compounds for soot formation, which is suspected to be the active site for solid - gas reactions leading to PCDD/F formation (lino et al., 1999 a and b, Schoonenboom and Olie, 1995, Stieglietz et al. 1991). On the contrary, others observed that the conditions favouring PAH production generally suppress PCDD/F formation (Benestad et al., 1990, Oehme et al. 1987). Metals regulated in incineration systems include Ag, As, Ba, Be, Cd, Co, Cr, Cu, Hg, Pb, Mn, Ni, Sb, Se, Sn, Tl, V and Zn (The European Parliament and the Council of the European Union, 1994, van der Vlies and te Marvelde, 1992, Italian Ministry of the Environment, 1998, Linak, 1997). Among these metals, zinc typically presents the highest concentrations in sewage sludge. Lead, copper, chromium, manganese, nickel, cadmium, and arsenic may also be found in significant concentrations in sewage sludge, whereas mercury is typically present only at low concentrations. Some research has specifically addressed the fate of metals in sewage sludge incineration (Dewling et al., 1980, Gerstle and Albrinck, 1982, Parrish et al., 1991, Balogh, 1996). These works have shown that several metals are enriched in fly ash with respect to their concentration in the bottom ash, suggesting that volatile metal species are formed in the combustion furnace and carried away in the flue gas. Combustion temperature, excess air, feed composition (chlorine, sulfur, and water content) are the parameters that may affect metal speciation in the combustion chamber and consequently metal partitioning among the incineration residues (Fournier et al.
Details
-
File Typepdf
-
Upload Time-
-
Content LanguagesEnglish
-
Upload UserAnonymous/Not logged-in
-
File Pages8 Page
-
File Size-