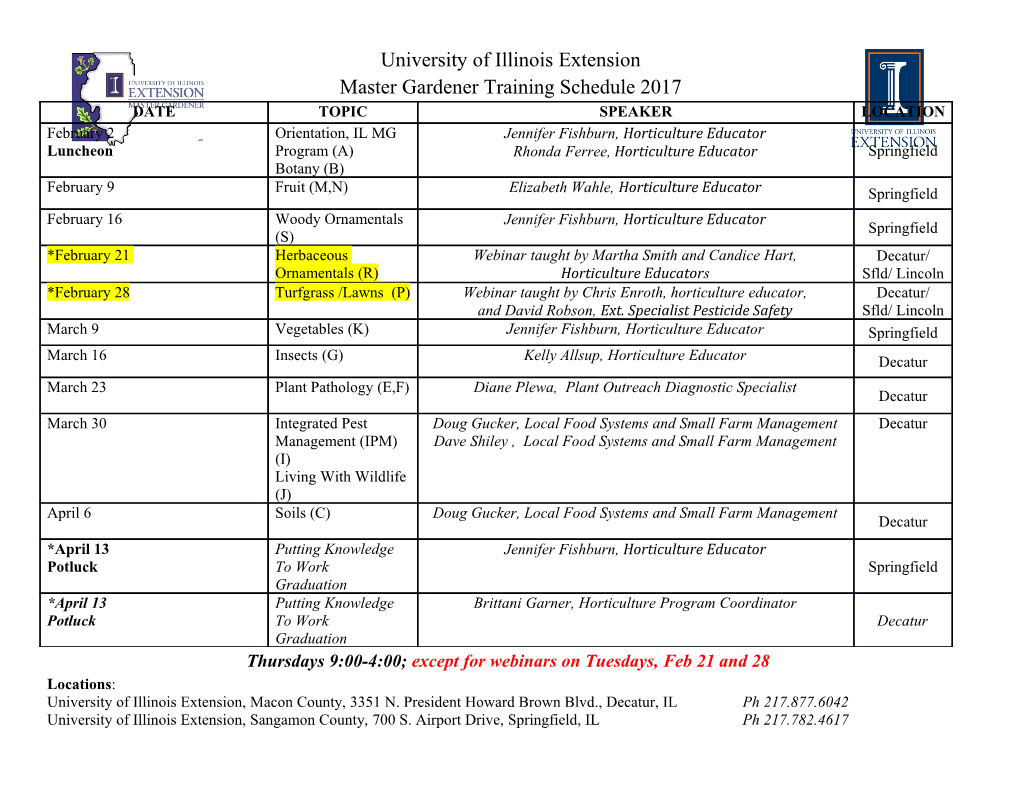
COMPUTERS IN EDUCATION JOURNAL, VOLUME 8, ISSUE 3, SEPTEMBER 2017 1 Introduction of Computational Fluid Dynamics in a Thermal-Fluids Laboratory Nelson Fumo Abstract—The capability and accuracy of computational fluid In order to simplify the use of CFD for analysis and design, dynamics (CFD) software facilitates its use in all engineering some authors have published studies on tools and teaching fields. This is creating a need for future engineers to have methodologies oriented to help students understand the physical knowledge of model development using CFD software by the time problem and analyze the phenomena [5-6]. In this sense, Lopez they acquire the degree. As supported by other studies, the incorporation of CFD into the undergraduate curriculum is et al. [7] presented a comparison between results obtained for a possible at junior or senior level. This paper presents the main controlled layout simulated by both physical and computational aspects of an approach used in a laboratory course to introduce models. students to a commercial CFD software. The approach includes In this paper, the approach used to introduce students to CFD the use of a previously developed CFD model of a parallel pipe heat in a laboratory course is presented. The elements of the exchanger to obtain simulation results and compare them with approach are to introduce the student to the terminology experimental data in order to validate the model. As a post- laboratory activity, the validated model can be used for further associated with CFD, give insight into the basic principles of investigation on the heat exchanger performance without the need CFD, recognize the quality of a CFD model by understanding of running additional experiments. the concept of validation, and realize the benefits of having a validated model. The approach also allows comparison of Index Terms— CFD model, heat exchanger, laboratory course, experimental results with CFD results [1]. In this order of ideas, model validation Lopez et al. [7] suggest that CFD can also constitute a powerful tool in the educational process of learning engineering concepts since the instructor lend the inherent difficulty of the I. INTRODUCTION computational model to the simplicity of a case study that can ith advances in capabilities of commercial be calibrated experimentally. W Computational Fluid Dynamics (CFD) software, its uses The previous statements are supported by CFD software and applications have increased in all areas of engineering. developers through training that can be used by teachers or These advances are creating a culture where engineers are students. For example, Professor Milovan Peric [8] explains expected to use CFD software without post-graduate education how engineering software can be integrated with traditional [1]. As a result, there is an increasing need to integrate CFD as curriculum to improve the understanding of conduction, a computer-assisted learning and simulation tool into radiation, convection and conjugate heat transfer. undergraduate engineering courses and laboratories [1-3]. For example, Adair and Jaeger [1] presented results that confirm the II. THE LABORATORY COURSE AND EXPERIMENT effectiveness of a suitable curriculum for students to use The course description for MENG 3211 Mechanical computational fluid dynamics as part of a fluid mechanics Engineering Lab II at the University of Texas at Tyler states: course at intermediate undergraduate level. “Introduction to basic Thermal/Fluid sciences laboratory Supported by previous studies, Stern et al. [2] and Adair and procedures and practices with uncertainty analysis. Jaeger [1] suggest that the use of simulation technology in Experimental topics include fluid flow, heat exchanger basics, education enhances the curriculum, increases learning and basics of refrigeration…” One of the lab activities is based efficiency and understanding, improves effectiveness of hands- on the parallel heat pipe heat exchanger described in Section 4. on learning methods, is effective in a combination of physical Although it is not a problem in the MENG 3211 course, Lona and simulation laboratories, and produces a positive student et al. [9] pointed out that the first problem in teaching heat response. A positive response comes from the fact that as CFD exchangers is the difficulty felt by the students that are not is used in many areas of engineering, the students find relevance familiar with the equipment. They suggest that the software can to many other courses in their curriculum and build on allow the student to analyze the effects of his/her decisions over knowledge gained in other courses such as fluid mechanics, heat exchanger parameters and operational conditions [9]. This thermodynamics and numerical methods [4]. is achieved through the approach used in this course, which is This work was submitted on June 21, 2017. Nelson Fumo is with The University of Texas at Tyler, Tyler, TX 75799 USA (e-mail: [email protected]). 2 COMPUTERS IN EDUCATION JOURNAL, VOLUME 8, ISSUE 3, SEPTEMBER 2017 ( ) ( ) similar to the approach used by Lopez et al. [7]. The approach = (3) can be summarized as acquiring experimental data to validate ℎ2−1 − ℎ1−2 ℎ2−1 analytical equations used for heat exchanger analysis (Section ln� � ∆ ℎ1−2 3), and then use the CFD model (Section 6) for further analysis B. The ε-NTU Method without running additional experiments. Although the intention The Logarithmic Mean Temperature Difference method has is to introduce CFD to the students in this course, it is expected some inherent disadvantages. The main disadvantage is when that a much deeper physical insight can be achieved by means the inlet and outlet temperatures need to be determined. This of a model developed with a general-purpose commercial generally requires an iterative procedure. An easier way is to computational fluid dynamics (CFD) software program [10] eliminate the inlet and the outlet temperatures from the analysis such as STAR-CCM+. which can be done by considering the ability of a heat The apparatus described in Section 4 is used as the physical exchanger to transfer a given amount of heat. This is called problem to simulate the heat exchanger performance by effectiveness (ε) of a heat exchanger and is defined as measuring flow rates and temperatures. The same geometry has been reproduced in a CFD model (Section 6), and temperatures = (4) are used to compute and compare the thermal heat capacity of the heat exchanger. By doing this comparison, students become where is the maximum possible heat transfer. The actual heat aware of the importance of validation, realize the agreement transfer is readily determined by performing an energy balance between measured and computed values, and give themselves on any of the two fluid streams. Assuming constant specific the opportunity to visualize velocity fields and temperature and heat, the actual heat transfer is computed as pressure profiles by means of graphical displays of the CFD simulation results [7]. = ( ) = ( ) (5) III. PARALLEL PIPE HEAT EXCHANGER �̇ � − �̇ �ℎ ℎ − ℎ The maximum possible heat transfer is defined as In a parallel pipe heat exchanger, also referred to as a double pipe heat exchanger, one pipe is placed within another pipe = ( ) = ( ) (6) having a larger diameter. The two fluid flows may be in the same direction (parallel flow) or in the opposite direction �̇ � ℎ − ℎ − (counter flow) as shown in Fig. 1. where refers to the lowest heat capacity of the two Important considerations for selecting or designing a heat fluids. �̇ � exchanger are heat transfer performance, physical size, total Using the heat capacity rate ratio, = , and knowing that the Number of Heat Transfer∗ Units is defined as weight, and cost. This laboratory activity is related to the heat transfer performance. For heat exchangers performance = , ε and NTU of a parallel pipe heat⁄ exchanger can be calculated using the following relationships: analysis, two methods are widely used: the Logarithmic Mean Temperature Difference method and the ε-NTU method [11]. Parallel flow:⁄ [ ( )] = (7) A. The Logarithmic Mean Temperature Difference Method − 1+∗ 1− The heat transfer rate ( ) is computed as ∗ 1+ = ln[1 (1 + )] (8) = (1) 1 ∗ ∗ 1+ − − Counter flow: with the Logarithmic Mean Temperature∆ Difference ( ) [ ( )] = (9) defined as −[ 1(−∗ )] 1− ∆ ∗ − 1−∗ 1− Parallel flow: = ln (10) ( ) ( ) ∗ = 1 1− (2) ∗ ℎ2−2 − ℎ1−1 1− � 1− � ℎ2−2 Equations (9) and (10) are undetermined for = 1, but ∆ ln� − � ℎ1 1 applying L’Hospital’s rule, and NTU can be written∗ as Counterflow: Fig. 1. Double Pipe Heat Exchanger, Parallel Flow and Counter Flow. FUMO: INTRODUCTION OF COMPUTATIONAL FLUID DYNAMICS IN A THERMAL-FLUIDS LABORATORY 3 = (11) estimate the uncertainty for UA are detailed in [12]. However, as an example of the use of the Taylor Series Method for 1+ propagation of elemental uncertainties into the result, the = (12) equations used for the counterflow are given in the Appendix. 1− The resulting uncertainties for UA for the four sets of data are It is important to understand that the heat exchanger thermal presented in Table 3. capacity (UA) is a parameter of the heat exchanger and is TABLE I independent of the method used. DATA FOR COUNTERFLOW EXPERIMENTS Experimental Data 1 IV. THE LABORATORY EQUIPMENT Water in tube Water in shell Temperature °C (°F) Fig. 2 shows the Hampden Model H-6878 apparatus used in IN OUT IN OUT the laboratory course. The apparatus consists of different valves 16.1 (61) 25.6 (78) 57.8 (136) 50.0 (122) to define the paths for the cold and hot water streams through Flow rate m3/hr (GPM) the different heat exchangers. The cold and hot flow rates are 0.454 (2.0) 0.681 (3.0) measured with rotameters. Inlet and outlet temperatures are Experimental Data 2 measured with type T thermocouples. In the laboratory the cold Water in tube Water in shell and hot water are taken directly from the supply pipes available Temperature °C (°F) from the building piping systems.
Details
-
File Typepdf
-
Upload Time-
-
Content LanguagesEnglish
-
Upload UserAnonymous/Not logged-in
-
File Pages8 Page
-
File Size-