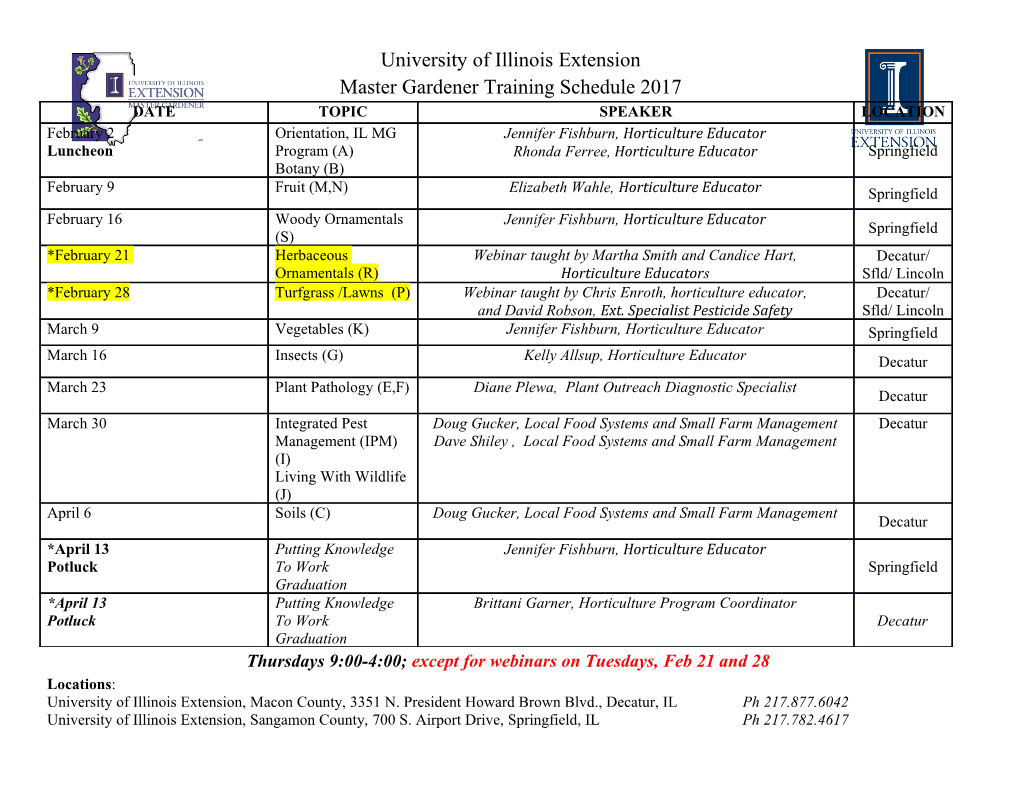
18 – Welding Issues and Code Applications Steve McCracken EPRI Welding & Repair Technology Center Commission Materials Programs Technical Information Exchange Public Meeting May 24, 2017 Rockville, MD © 2017 Electric Power Research Institute, Inc. All rights reserved. Presentation Outline . Welding Issues – Nickel-base Filler Metal Weldability Testing – Development of 52M Filler Metal Alternative – Irradiated Material Welding Solutions . Code Applications – Code Rules for Welding on Irradiated Material – Repair by Carbon Fiber Reinforcement – N-871 – Excavate and Weld Repair for SCC Mitigation – N-847 – Branch Connection Weld Metal Buildup for SCC Mitigation – N-853 – Pad Reinforcement Repair of Atmospheric Storage Tanks – N-865 2 © 2017 Electric Power Research Institute, Inc. All rights reserved. Research Focus Area 1 Nickel-base Filler Metal Weldability Testing Steve McCracken EPRI WRTC © 2017 Electric Power Research Institute, Inc. All rights reserved. High-Cr Ni-Base Filler Metal Weldability Testing • Weldability testing at OSU ‒ Cast pin tear test (CPTT) ‒ Strain-to-fracture (STF) ‒ Transvarestraint (TVT) ‒ Characterization studies ‒ Solidification temperature range (modeling & SS-DTA) • 82, 52, 52M, 52i, 52MSS, Transvarestraint Test SN690Nb, 52M-Ta-Mo Cast Pin Tear Test • Fundamental study of ductility-dip and hot cracking mechanisms • Crack healing by liquid back filling • Effect of SS dilution on hot cracking resistance Gleeble Strain-to-Fracture Test 4 © 2017 Electric Power Research Institute, Inc. All rights reserved. 52M Hot Cracking on Stainless Steel Base Material • Nine high-Cr Ni-base weld metal specifications • Twenty-two stainless steel base materials with varying Si, S, and P compositions • Crack no-crack plots show influence of Si, S and P • Guidelines presented to minimize hot cracking ‒ Composition control ‒ Dilution control ‒ Bead placement control ‒ Buffer layer control 5 © 2017 Electric Power Research Institute, Inc. All rights reserved. High-Cr Ni-Base Filler Metal Screening Test • Industry Need: Field deployable test to screen 52M heats and 52M variants • Approach: Narrow groove high restraint geometry design (EPRI & IHI) to promote DDC with validation by computer modeling • Next Step: Investigate single bead approach with GTAW parameters (weave, sync-pulse, etc.) that may promote DDC 6 © 2017 Electric Power Research Institute, Inc. All rights reserved. WRTC Reports on 52M Weldability Issues • WRTC: Measures to Minimize 52M Hot Cracking on Stainless Steel Base Materials – Update Report 3002003140, December 2014 • WRTC: Screening Test for High- Chromium Nickel-Base Weld Metals – Preliminary Studies Report 3002005527, September 2015 • WRTC: Weldability Testing of High- Chromium Nickel-Base Weld Metals – Resistance to Solidification Cracking Report 3002007909, December 2016 7 © 2017 Electric Power Research Institute, Inc. All rights reserved. Research Focus Area 1 Development of 52M Filler Metal Alternative Steve McCracken EPRI WRTC © 2017 Electric Power Research Institute, Inc. All rights reserved. Alternative 52M Development Scope – Long Range Plan . Fundamental research performed to understand cracking mechanisms and weldability problems with 52M . Development of alloy composition for new filler metal – Model welding behavior and mechanical properties of target compositions – Validate modeled behavior with button melting experiments . Manufacture weld wire for target composition – Kobe Steel selected to manufacture target weld wires – Perform laboratory weldability testing . Assess weldability and perform validation NDE of new filler metal – Assess process parameters for GTAW and GMAW – Make large scale mockups for weldability and NDE – Perform mechanical, corrosion, & crack growth rate testing – Assess feasibility of alternative advanced welding processes (laser welding, magnetic stir, hybrid, etc.) 9 © 2017 Electric Power Research Institute, Inc. All rights reserved. 52M-Hf and 52M-Ta Experimental Alloys Selected Table 1: Target Composition Al B C Co Cr Cu Fe Mn Mo Nb 0.01 < 0.001 0.035 <0.01 30 0.03 8 0.6 (note 1) 0.5 Ni P S Si Ta Ti Zr Hf N ― Rem < 0.01 < 0.001 0.2 <0.01 0.2 < 0.01 (note 1) < 0.008 ― Note 1: Vary Hf-Mo and Ta-Mo as shown in Table 2a and 2b respectively Table 2a: Range of Hf and Mo . Matrix of compositions in Tables 2a and 2b used to Heat # Hf Mo optimize final target composition with best 1 0.25 <0.03 2 0.25 3.9 resistance to ductility-dip cracking (DDC) and 3 <0.001 <0.03 solidification cracking 4 <0.001 3.9 Table 2b: Range of Ta and Mo – CPTT showed 52M-Hf & 52M-Hf-Mo wires had poor Heat # Ta Mo resistance to solidification cracking 5 3.8 <0.03 – CPTT showed 52M-Ta & 52M-Ta-Mo wires had improved 6 3.8 3.9 resistance to solidification cracking 7 <0.005 <0.03 8 <0.005 3.9 – STF showed 52M-Ta-Mo had improved resistance to DDC 10 © 2017 Electric Power Research Institute, Inc. All rights reserved. Procurement of 52M Ta-Mo & Hf-Mo Weld Wires . 52M-Hf and 52M-Hf-Mo variants are complete . 52M-Ta and 52M-Ta-Mo variants are complete . All variants at WRTC in Charlotte 11 © 2017 Electric Power Research Institute, Inc. All rights reserved. Weldability Testing 52M-Hf & 52M-Ta Variants • Weldability observations – oxide, wetting, etc. • Dual GTAW wire feed system used to build weld specimens of varying composition ‒ 52M-Ta, 52M-Ta-Mo wires mixed to study influence Transvarestraint of composition on weldability • Weldability testing at OSU ‒ Cast pin tear test (CPTT), Strain-to-fracture (STF) test, transvarestraint (TVT), Gleeble hot ductility and material characterization studies Dual Wire Feeder Strain-to-Fracture Test Specimen Oxide Observations Cast Pin Tear Test 12 © 2017 Electric Power Research Institute, Inc. All rights reserved. Progress and Future Work • Complete ‒ Computational modeling and DOE studies of solidification behavior ‒ Button melting and weldability experiments ‒ Manufacture of target 52M-Hf, 52M-Hf-Mo, 52M-Ta & 52M-Ta-Mo wires ‒ Cast pin tear testing (CPTT) of 52M-Hf & 52M-Hf-Mo wires ‒ Strain-to-fracture (STF) testing of 52M-Ta & 52M-Ta-Mo variants ‒ CPTT dilution testing of 52M-Ta variants with CF8A ‒ Characterization of 52M-Ta & 52M-Ta-Mo wires • In Progress ‒ Hot ductility testing and transvarestraint testing ‒ Procurement of 40 kg lot of 52M-Ta-Mo welding wire (delivery 4th quarter 2017) • Near Future ‒ Test with various welding processes and joint configurations (1st quarter 2018) ‒ Mechanical testing (tensile, bends, etc.) • N + 1 ‒ Full scale mockup for CGR testing (cold wire GTAW process) 13 © 2017 Electric Power Research Institute, Inc. All rights reserved. Research Focus Area 2 Irradiated Material Welding Solutions Jon Tatman EPRI WRTC © 2017 Electric Power Research Institute, Inc. All rights reserved. Laser Welding Techniques for Repair of Irradiated Material . Improved heat input estimation techniques to establish definitive helium induced cracking threshold . Development of optimal laser welding parameters for expected materials and repair configurations (groove, fillet, overlay) – Stainless steel parameter development completed in 2014 – Parameter development for nickel-base material planned in 2017 . FEA modeling performed to validate irradiated SS parameter development . Low Heat Input Laser Beam Welding for Repair of Irradiated 10 Reactor Components - EPRI WRTC Report 3002003146 * 1 * * * * * * Effective Heat Heat Effective Input (KJ/cm) * * 0.1 JOG-GTAW-BM - No Cracking JOG-GTAW-BM - Cracking JNES-GTAW-BM - No Cracking JNES-GTAW-BM - Cracking JNES-GTAW-WM - No Cracking JNES-GTAW-WM - Cracking LBW-BM - No Cracking LBW-BM - Cracking LBW-WM - No Cracking LBW-WM - Cracking LBW - Remelt Trials - No Cracking LBW - Remelt Trials - Cracking JNES-GTAW-WM - GBD LBW-BM - GBD LBW - Remelt Trials - GBD * - Denotes single pass result 0.01 0.1 1 10 100 Helium Concentration (appm) 15 © 2017 Electric Power Research Institute, Inc. All rights reserved. Advanced Laser Welding Equipment Development . Prototype of field-deployable auxiliary beam stress improved (ABSI) laser weld head has been developed . Weld head design is tailored for underwater welding applications . Designed to perform “dry- underwater” weld operations . Fabrication of initial prototype is complete, will be tested in underwater chamber to confirm operability . Initial testing will be reported in 2017 16 © 2017 Electric Power Research Institute, Inc. All rights reserved. Improved Heat Input, Weld Dilution, and Power Ratio Equations . New effective heat input and dilution equations are in development . Equations have been validated for GTAW and LBW processes – GTAW validation: 2013 Tech Report – 3002000412 – LBW validation: 2015 Tech Update – 3002005531 . Initial trials have begun to determine effects of weld parameters and chemical composition on critical efficiency values of austenitic stainless steel material 17 © 2017 Electric Power Research Institute, Inc. All rights reserved. Presentation Outline . Welding Issues – Nickel-base Filler Metal Weldability Testing – Development of 52M Filler Metal Alternative – Irradiated Material Welding Solutions . Code Applications – Code Rules for Welding on Irradiated Material – Repair by Carbon Fiber Reinforcement – N-871 – Excavate and Weld Repair for SCC Mitigation – N-847 – Branch Connection Weld Metal Buildup for SCC Mitigation – N-853 – Pad Reinforcement Repair of Atmospheric Storage Tanks – N-865 18 © 2017 Electric Power Research Institute, Inc. All rights reserved. Research Focus Area 6 Code Rules for Welding on Irradiated Materials Steve McCracken
Details
-
File Typepdf
-
Upload Time-
-
Content LanguagesEnglish
-
Upload UserAnonymous/Not logged-in
-
File Pages53 Page
-
File Size-