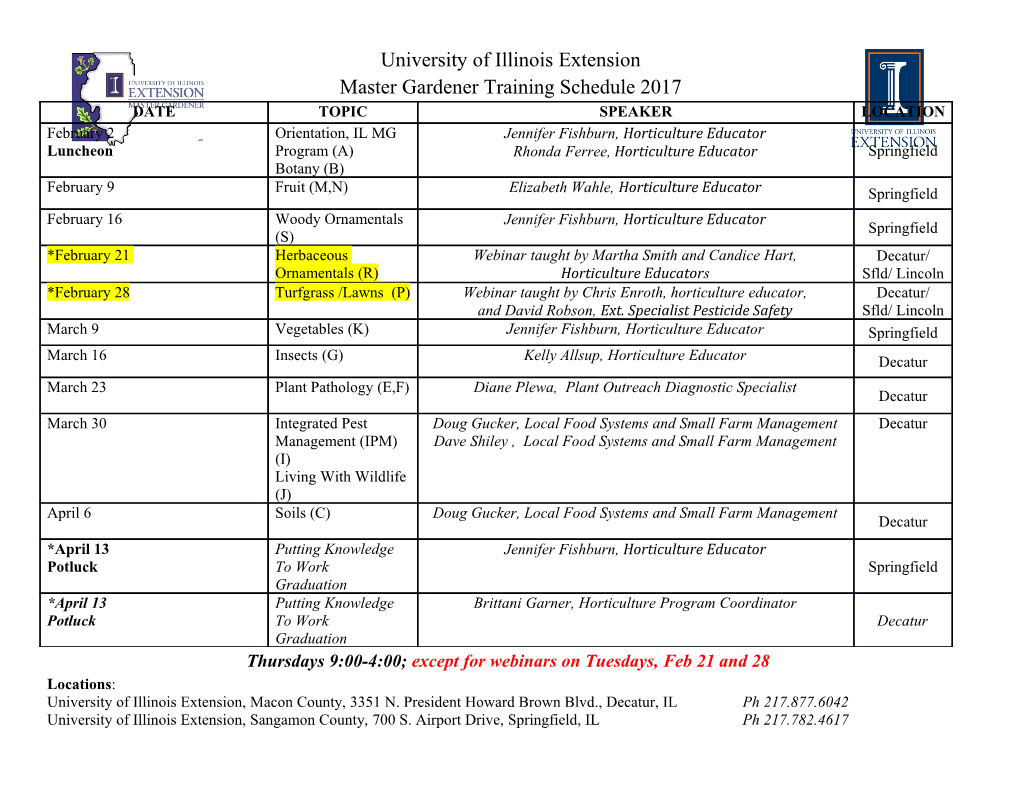
AEROELASTIC CONCEPTS FOR FLEXIBLE AIRCRAFT STRUCTURES Sebastian Heinze Aeronautical and Vehicle Engineering Royal Institute of Technology SE-100 44 Stockholm, Sweden TRITA/AVE 2007:29 ISBN 978-91-7178-706-4 TRITA/AVE 2007:29 KTH Farkost & Flyg ISSN 1651-7660 Teknikringen 8 ISRN KTH/AVE/DA-07:29-SE 100 44 Stockholm ISBN 978-91-7178-706-4 Akademisk avhandling som med tillst˚and av Kungliga Tekniska hogskolan¨ fredagen den 15 juni 2007 kl. 13.15, Kollegiesalen F3, Lindstedtsv¨agen 26, Stock- holm, for¨ teknisk doktorsgrads vinnande framl¨agges till offentlig granskning av Sebastian Heinze. Typsatt i LATEX Tryck: Universitetsservice US AB, Stockholm 2007 c Sebastian Heinze 2007 Aeroelastic Concepts for Flexible Aircraft Structures 1 Preface The work presented in this doctoral thesis was performed between April 2003 and May 2007 at the Department of Aeronautical and Vehicle Engineering at the Royal Institute of Technology (KTH) in Stockholm, Sweden. Financial support has been provided by the European research project Active Aeroelastic Aircraft Structures (3AS), the Swedish Defence Materiel Administration (FMV) and the Swedish National Program for Aeronautics Research (NFFP). I would like to express my gratitude to my supervisor, Dan Borglund, for outstanding support and advice during the past years, and for all the good times together. Furthermore, many thanks to the head of the Division of Flight Dynamics, Ulf Ringertz, and to my former and current colleagues at Far & Flyg, in particular Carin, David, Fredrik, Gloria, Marianne, Martin, Martin, and Ulrik for all companionship and inspiration. Also, many thanks to Professor Moti Karpel for his contribution to my work. I am very grateful to my family and friends for encouraging and supporting me at all times. Finally, special thanks to Maria for all the love and understand- ing, and for giving me strength in the recent years. Aeroelastic Concepts for Flexible Aircraft Structures 3 Abstract In this thesis, aeroelastic concepts for increased aircraft performance are devel- oped and evaluated. Active aeroelastic concepts are in focus as well as robust analysis concepts aiming at efficient analysis using numerical models with un- certain or varying model parameters. The thesis presents different approaches for exploitation of fluid-structure interaction of active aeroelastic structures. First, a high aspect ratio wing in wind tunnel testing conditions is considered. The wing was developed within the European research project Active Aeroelastic Aircraft Structures and used to demonstrate how structural flexibility can be exploited by using multiple control surfaces such that the deformed wing shape gives minimum drag for different flight conditions. Two different drag minimization studies are presented, one aiming at reduced induced drag based on numerical optimization techniques, another one aiming at reduced measured total drag using real-time optimization in the wind tunnel experiment. The same wing is also used for demonstration of an active concept for gust load alleviation using a piezoelectric tab. In all studies on the high aspect ratio wing, it is demonstrated that structural flexibility can be exploited to increase aircraft performance. Other studies in this thesis investigate the applicability of robust control tools for flutter analysis considering model uncertainty and variation. First, different techniques for taking large structural variations into account are evalu- ated. Next, a high-fidelity numerical model of an aircraft with a variable amount of fuel is considered, and robust analysis is applied to find the worst-case fuel configuration. Finally, a study investigating the influence of uncertain external stores aerodynamics is presented. Overall, the robust approach is shown to be capable of treating large structural variations as well as modeling uncertainties to compute worst-case configurations and flutter boundaries. Aeroelastic Concepts for Flexible Aircraft Structures 5 Dissertation This thesis is based on a brief introduction to the area of research and the following appended papers: Paper A D. Eller and S. Heinze. An Approach to Induced Drag Reduction with Experi- mental Evaluation. AIAA Journal of Aircraft, 42(6):1478-1485, 2005. Paper B M. Jacobsen and S. Heinze. Drag Minimization of an Active Flexible Wing with Multiple Control Surfaces. TRITA-AVE 2006:50, Department of Aeronautical and Vehicle Engineering, KTH, 2006. Submitted for publication. Paper C S. Heinze and M. Karpel. Analysis and Wind Tunnel Testing of a Piezoelectric Tab for Aeroelastic Control Applications. AIAA Journal of Aircraft, 43(6):1799- 1804, 2006. Paper D S. Heinze and D. Borglund. Robust Flutter Analysis Considering Modeshape Variations. TRITA/AVE 2007:27, Department of Aeronautical and Vehicle Engi- neering, KTH, 2007. Submitted for publication. Paper E S. Heinze. Assessment of Critical Fuel Configurations Using Robust Flutter Analysis. Presented at the 47th AIAA/ASME/ASCE/AHS/ASC Structures, Struc- tural Dynamics, and Materials Conference, Newport, Rhode Island, May 2006. Submitted for publication. Paper F S. Heinze, U. Ringertz, and D. Borglund. On the Uncertainty Modeling for External Stores Aerodynamics. To be presented at the CEAS/AIAA/KTH Inter- national Forum on Aeroelasticity and Structural Dynamics, Stockholm, Sweden, June 2007. Aeroelastic Concepts for Flexible Aircraft Structures 7 Contents Preface 1 Abstract 3 Dissertation 5 Introduction 9 Aeroelasticity . 11 Aeroelastic phenomena . 11 Aeroservoelasticity . 14 Active Aeroelasticity . 15 Analysis and Testing . 16 Staticdeformations. 17 Oscillations and flutter . 19 Robust analysis . 21 Contribution of this work 23 Future work 25 References 27 Division of work between authors 31 Appended papers Aeroelastic Concepts for Flexible Aircraft Structures 9 Introduction Modern Formula One race cars, like the one shown in Figure 1, consist of highly optimized components with a lifespan hardly exceeding a single race. A lot of effort is spent in research and development of improved components, often inspired by findings within aeronautical research. The aerodynamic Figure 1: Formula One race car - in many ways related to aeronautics (photo- graph from BAE Systems). properties of such a car are taylored to control the airflow around the vehicle in order to obtain low aerodynamic drag and maximum downforce to provide the highest possible wheel traction. Aircraft wing airfoils, originally designed for producing lifting force, were found convenient for producing downforce by placing them upside down above the wheels. As for aircraft, however, increased normal force always comes at a cost of increased induced drag. Adjusting the wing shape and the angle of attack is thus a tradeoff between high downforce needed in turns and low drag desired on straight parts of the track, as shown in Figure 2. It is desirable to change the wing configuration during the race in order to get optimum performance in the entire range of operating conditions. In the 1990s, several racing teams began to use flexible wings, where the angle of attack decreased due to increased aerodynamic loading at increased velocities, 10 S. Heinze Airflow Airflow Drag Drag Downforce Downforce High downforce Low drag Desirable in low−speed turns Desirable at high speed BUT: High drag BUT: Low downforce Figure 2: Performance tradeoff for wing design. thus providing less downforce and less drag at higher speeds. Figure 3 shows the mechanism that is based on the exploitation of the aeroelastic interaction between the structure and the aerodynamic loads. The wing flexibility is repre- Zero airspeed Low airspeed High airspeed Undeformed Small deformation Large deformation Figure 3: Flexible wing. sented by a spring element replacing the rigid attachment of the wing. The idea was to design a wing that would deform under aerodynamic loading, yielding an optimum wing shape at all speeds. At high speeds, the wing is deformed towards a lower angle of attack, thus reducing the drag in high-speed parts of the track, whereas the wing deforms less and maintains a higher angle of attack at low velocities. Unfortunately, the flexible wings caused some structural failures, and in the late 1990s, new regulations were issued that banned the use of elastic wing struc- Aeroelastic Concepts for Flexible Aircraft Structures 11 tures by restricting the maximum horizontal and vertical deformation of the wing under a given loading condition [1]. This simple example illustrates that flexibility can be exploited to gain performance of a structure with aerodynamic interaction, but also that flexibility introduces aeroelastic interaction that may cause the structure to fail. Aeroelasticity Aeroelasticity is the multidisciplinary science dealing with the interaction of aerodynamic forces and structural deformations. As a structure moves through the air, the motion will cause aerodynamic loads, leading to deformations of the structure. The deformation in turn has an impact on the airflow, thus changing the aerodynamic loading. Apparently, there is a closed loop of aerodynamic and structural interactions, and depending on the properties of the structure and the airflow, different phenomena can occur. Aeroelastic phenomena Aeroelastic phenomena can be divided into different groups depending on the participation of specific members of the fluid-structure system. Figure 4 il- lustrates the disciplines that interact in aeroelasticity. The aeroelastic system Aerodynamic properties Static Flight aeroelsticity mechanics Dynamic aeroelasticity Elastic
Details
-
File Typepdf
-
Upload Time-
-
Content LanguagesEnglish
-
Upload UserAnonymous/Not logged-in
-
File Pages157 Page
-
File Size-