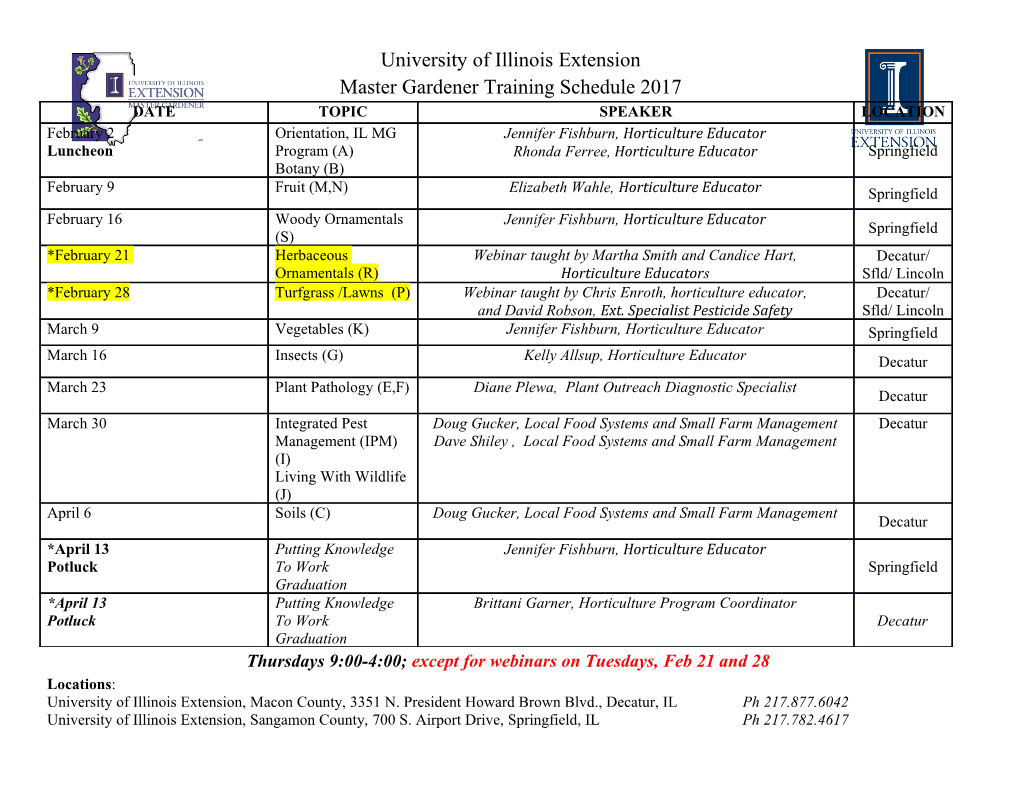
Module 37 Surface hardening Lecture 37 Surface hardening 1 NPTEL Phase II : IIT Kharagpur : Prof. R. N. Ghosh, Dept of Metallurgical and Materials Engineering || | | Keywords : Non‐uniform properties in engineering components, methods of surface hardening, shot peening, hard facing, induction hardening, surface modification by diffusion, carburizing, post carburizing heat treatment, core refining, case hardening, origin of residual stress, nitriding, Fe‐N phase diagram, effect of surface hardening on fatigue resistance of engineering components Introduction The last six lectures were devoted to heat treatment of steel. We have seen that hardening followed by tempering gives the best combination of strength and toughness. Formation of martensite is primarily responsible for the development of very high strength in steel. However you need to cool a component made of steel very fast to get martensite both at its surface and at its centre. Although it may be rather easy to achieve a high cooling rate at the surface but maintaining a high cooling rate at the centre may be extremely difficult particularly if the section size of the component is large. Therefore the microstructure at the centre of a thick section is likely to be different from that at its surface. There are several applications where we do not need uniform microstructure or property across the section. For example components like turbine shaft, gear, spindle and axle need to have a hard surface but a soft core. In general high strength means low toughness. If the section size of a component is too high to be fully hardened we may still have a soft core. It might be one of the methods of fulfilling such a criterion. There are several other ways the strength or the hardness of the surface can be increased without adversely affecting the toughness of the core. Some of the most common techniques are as follows: Induction hardening Case carburizing + case hardening Nitriding Shot peening Hard facing, coating or surface alloying In this module we shall learn about some of these. The properties of steel or any other engineering material depend a great deal on the processing route that is followed and its composition. For example we know that cast metals have coarse inhomogeneous grains with preferred orientation. Subsequent processing consisting of homogenization, forging, rolling and annealing may result in a uniform fine grain structure having isotropic properties. As a result there may be a substantial improvement in its strength and ductility. In the case of steel the possible options are much more varied. In short all materials may 2 have an inherent base property or microstructure which can be altered or improved by adopting an appropriate processing route. The performance of a component depends NPTEL Phase II : IIT Kharagpur : Prof. R. N. Ghosh, Dept of Metallurgical and Materials Engineering || | | primarily on the properties of the material of which it is made. The interrelation between the four is best described by the tetrahedron shown in fig 1. Performance Processing: Properties micrstructure Material Fig 1: Tetrahedron showing the interrelation between material, its processing route and its property on the performance of a component. Non‐uniform properties in engineering components: It is extremely difficult to have a uniform microstructure within a material unless it is extremely thin. This is because the evolution of microstructure within a material depends on the local processing parameters. Often it is difficult to maintain identical conditions at every point within a material unless it is extremely thin. The effect is more pronounced in the case of steel that goes through a solid state transformation during cooling. The cooling rate within a component is a strong function of its section size. It is impossible to maintain identical cooling rate within a component of finite dimension. Therefore we have to live with non‐uniform properties in engineering components since it cannot be avoided in components of reasonable thickness. This is illustrated with the help of an example in slide 1. Steel I beam is one of the most common structural components. A cross section of I beam is shown in slide 1. Its flange which is highly stressed is thick but its web where the stress is not so high is relatively thin. I beams are made by hot rolling at a temperature while the structure of steel is austenite. On completion of rolling I beam is allowed to cool in air. The average cooling curves of the flange and the web of the beam have been super imposed on the CCT diagram of 0.2%C steel. The cooling rate within the web is a little faster than that in the flange. Therefore 3 the microstructure of the web is likely to be finer than that in the flange. It is likely to have relatively less %ferrite but more %pearlite in comparison to those in the flange. The web is therefore expected to be stronger than the flange although it is not necessary to make it NPTEL Phase II : IIT Kharagpur : Prof. R. N. Ghosh, Dept of Metallurgical and Materials Engineering || | | stronger. Here is an application where the differential properties of an engineering component are not being properly exploited. There are several other uses where intentionally the structure of the material is altered either by local change in composition or by local deformation or by adopting differential cooling rates at different places so as to improve its performance as an engineering component. We would look at a few such examples. Non uniform properties in engineering components I beam A3 flange A1 + P web T Flange Slide 1 web Web: least stressed: thin Ms + M Flange: high stress: thick time I Beam: hot rolled sections Case: where we have % C ~ 0.2 to learn to live with it. Surface hardening: Which is stronger ? exploit such features. Surface hardening: why & how? Components like gear, shaft or spindle need a hard / wear resistant surface but a soft / tough core. Section size of such components is often too large to be uniformly hardened even on severe quenching. More over the time lag between the transformations at the surface and the core results in an unfavorable tensile residual stress at the surface. Recall the general thumb rule that the region that transforms later is likely to have compressive residual stress. The surface is likely to transform first in steel having the same composition all through its section. Therefore surface would have residual tensile stress. Depending on its magnitude it may lead to cracking or distortion. The presence of residual tensile stress is also harmful as it would reduce fatigue life of critical components like turbine shaft or landing gear of an aircraft. The purpose 4 of surface hardening is to develop a hard surface with compressive residual stress, to improve its wear resistance, to increase its fatigue life and to avoid susceptibility to distortion and cracking. The most commonly used methods of surface hardening are as follows: NPTEL Phase II : IIT Kharagpur : Prof. R. N. Ghosh, Dept of Metallurgical and Materials Engineering || | | • Shot peening: general applicable to all metals • Coating / hard facing • Surface (local) heating & cooling: steel • Surface diffusion & subsequent treatment Shot peening: Shot peening technique is applicable to all metals and alloys that are amenable to plastic deformation. The part to be hardened is placed in a chamber where extremely fine hard particles moving at a high speed keep striking at its surface. The energy of the moving particles is high enough to cause local plastic deformation at its surface. The stress on the material a little beneath the surface is not high enough to cause plastic deformation. However it would be under elastic stress as long as the shot peening process continues. When it stops residual stress would develop at the surface because of the elastic recovery that occurs in the region a little beneath the surface. Proper control on the process parameters such as the particle size, its kinetic energy, the angle of incidence and the time may be necessary to develop favorable residual stress pattern at the surface. It is compressive in nature. Therefore it would inhibit crack initiation. Landing gears of aircrafts are subjected to shot peening to develop residual compressive stress on its surface. Even automotive gears, following carburizing, are subjected shot peening to raise the value of compressive residual stress (to as high as 1000 – 1200 MPa), particularly at depths of 30 – 40 microns. This help resist crack propagation during service as result of fatigue loading. Hard facing: Engineering components that are required to resist solid particle erosion, abrasion, fretting or cavitation are usually given a hard surface coating. This consists of a fine dispersion of hard metal carbides in a compatible metal matrix. Thermal spray is the most commonly used technique to apply such coatings on the component. There are specially designed setups with spray guns that suck the coating material along with oxygen and fuel gas that ignites into a flame to melt the matrix of the coating material while it deposits on the surface of the component. The most commonly used coating materials are mixtures of chromium or tungsten carbides in either cobalt or nickel‐chromium alloy matrix. Hard facing is also a commonly used technique to salvage worn out parts so that they could be reused. Induction hardening: a method based on local heating followed by cooling: 5 This is applicable only for steel. An induction coil is used to heat the component to be hardened. Only the surface gets heated. Its microstructure transforms into austenite from a mixture of ferrite and cementite, but the structure of the core remains intact as it remains cold NPTEL Phase II : IIT Kharagpur : Prof. R.
Details
-
File Typepdf
-
Upload Time-
-
Content LanguagesEnglish
-
Upload UserAnonymous/Not logged-in
-
File Pages22 Page
-
File Size-