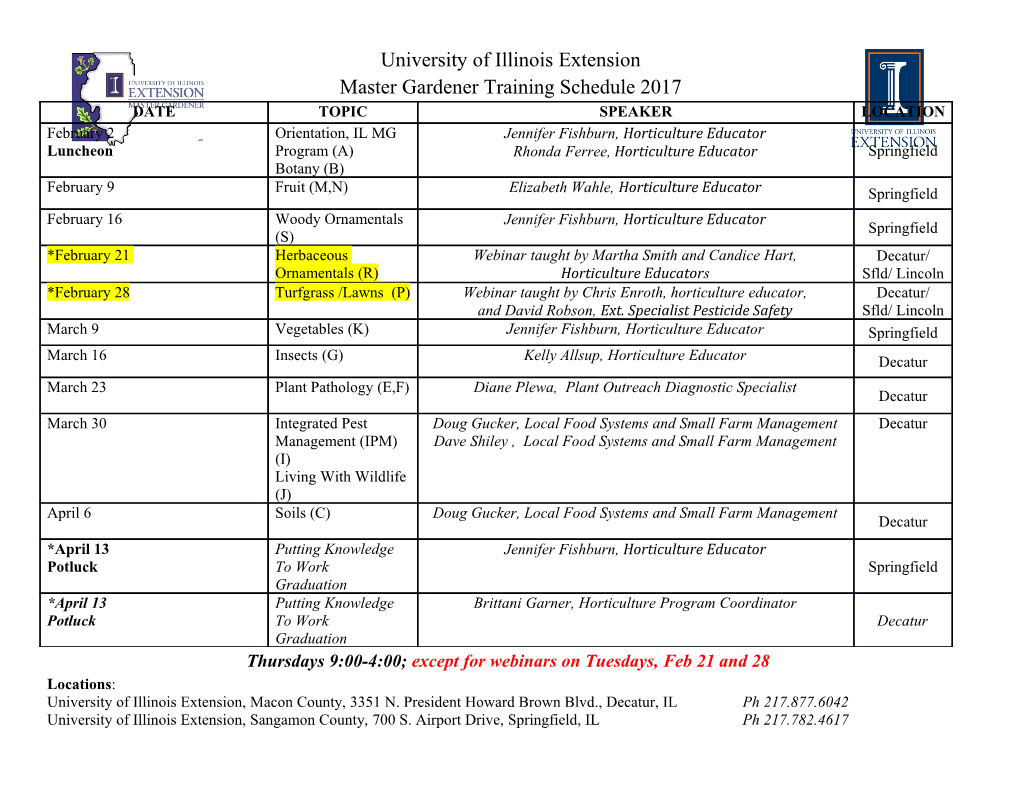
DIXIÈME RENCONTRE INTERNATIONALE DU GERPISA TENTH GERPISA INTERNATIONAL COLLOQUIUM La coordination des compétences et des connaissances dans l’industrie automobile Co-ordinating competencies and knowledge in the auto industry 6-8 Juin 2002 (Palais du Luxembourg, 15, rue Vaugirard, 75006 Paris, France) A COMPARATIVE STUDY ON PRODUCT AND R & D STRATEGIES OF MAJORS ASSEMBLERS OF BRAZILIAN CAR INDUSTRY Enéas G. de CARVALHO* MODULARIZATION AND TECHNOLOGICAL CHANGES IN THE CAR INDUSTRY Modularization Despite the increasing quantity of electronic components incorporated by the cars in recent years, they still are basically a complex and systemic mechanical product. At the same time, cars have what has been called integral architecture, that means, “with a more complex relationship of parts and functions that requires each of the parts to be optimally designed to achieve its overall performance.” (Fujimoto and Takeishi, 2001: 3)1. Such characteristics are an impediment to design a car integrally in “modular”2 terms, with standardised interfaces facilitating a connection between respective modules and vehicles in a singular operation the kind “plug and play” (Chanaron, 2001)3. Even considering this strong structural limitation in comparison, for instance, to products as portables computers, sound equipment and bicycles, it is possible to observe a fierce attempt, since the middle of the 90s, of modularization by the western car industry, * Department of Economics of The State University of São Paulo at Araraquara (Brazil) and Researcher at Grupo de Estudos de Economia Industrial (GEEIN). 1 “For instance, consider the driving comfort (ride) of a car. Delicated factors, like a minor difference in the geometry of the suspension, or whether the principal axis of the engine is sightly in front or behind the axle, can greatly influence the overall character of the car. In order to function as a system, each part must be designed optimally in this type of product. Further, if Toyota is manufacturing the car, the car must be basically be designed by Toyota ” (Fujimoto and Takeishi, 2001: 4). 2 At least the present car with an internal ignition engine and with steel architecture of o,8mm (Fujimoto, quoted by Lynch, T. M. et. al. 2000). This situation could be reversed with the arrival of new technologies of cars with propulsion engine (see next note). 3 “There is no unique definition for a module whicth would be accepted by both the OEMs and the suppliers. In professional magazines, some are using module for brake system, others for a chassis with wheels, others even a complete vehicle assembled by a sub-contractor. A module could be defined as a set of components and/or sub-systems which are pre-assembled off-line and delivered to final assembly line ready to be fitted on the vehicle or engine in the one single operation, i.e. on a “plug and play” approach. Such na approach is named modular assembly ” (Chanaron, 2001: 3). 2 particularly the Europeans ones. This tendency has been concomitant with a significant change towards an enlargement of outsourcing, also adopted by the western car manufacturing. In this last case, the motivation seems to be the possibility to decrease wages cost faced by the parts manufacturers and also to diminish risks and the amount of investments necessary to increase these activities, particularly regarding the markets of emergent countries (Fujimoto, 2001; Sturgeon and Florida, 1999). The adoption of these strategies implies in an important delegation of responsibilities to the modules suppliers, who would assume part of the design and manufacturing functions, and consequently, a significant role inside the productive chain. It is particularly this aspect which makes the Japanese car manufacturing concerned and cautious about the idea of modularization (Chanaron, 2001). According to Japanese experts, the main obstacles to modularization are related to costs administration, assignment and innovation process. According to them, there is no clear evidence that the modularization leads to a systematic production cost reduction – wages difference between manufactures and parts suppliers in Japan is smaller than the ones faced by the western ones. On the other side, modularization might lead to an extra cost by synchronisation between manufactures and modules suppliers. Additional transaction costs have to be considered when is necessary to change suppliers, as well as extra direct costs generated by introduction of significant changes in design. In both cases, the additional costs would come from the choice of a single supplier required by the modularization (Chanaron, 2001). A second main obstacle, also called black box syndrome, refers to a potential loss, by the manufactures, of the traditional control over the total costs, of the development of lead time, technical performance and quality levels. “A ‘Intel Inside’ syndrome, translated into ‘Bosch, Delphi (...) or Sony Inside syndrome in the automotive industry, would be extreme limit of such a move. In that case, the risk would be a complete reversal of image and brand from OEM to a particular supplier” (Chanaron, 2001: 8). Finally, there is the risk of having, as a single source, and in a long term, a module supplier less innovative. Promoting competition between potential suppliers is frequently an efficient way to stimulate innovation between them (Chanaron, 2001). In accordance to these concerns, Toyota and Honda adopted a very cautious approach, introducing a partial modularization and under their total control, dismissing a more radical re-engineering of theirs plants, as well as a re-organisation of their suppliers chain, particularly in the case of their affiliated suppliers. In short, they have been developing and producing their own modules, which might be produced later by their affiliated suppliers in the Toyota case, or by its long term partners, as in the Honda case. The two main Japanese manufactures are showing an interest in leading and controlling the process, keeping a complete responsibility and control on design and core competencies in all levels considered essentials by them – the technological, the productive and the strategic ones (Chanaron, 2001). Technological Change In general terms, it seems reasonable to consider four main scenarios regarding forthcoming technological evolution of international car industry. The first scenery, a more conservative one, involves the supposition of continuity of the present technological pattern, based on internal ignition engine, and in a crescent utilisation of electronic components (the 3 so called embodied electronic), in the intensification of Internet and in the introduction of new materials4. This first scenery, however, does not seem be compatible to the prospective requirements of legislation regarding a more efficient utilisation of fuel, particularly regarding the emission of pollutants. Considering that the need to replace the present form of propulsion car engine is almost established, there is a real technological race to define, between feasible alternatives, the more efficient means to accomplish the mentioned replacement. This technological race, which is not confined only to the assemblers and parts manufacturers5, might result in a radical change in car industry and its components (Automotive Industry, October, 1999; Maxton, 1998). At the present stage of the research, more promising technological prospective are indicating the existence of three other possible scenarios. The second one, which seems to attract the attention of Toyota, involves the chance, in the future, to choose between cars working on batteries, on cells fuel, hybrid propulsions, and natural gas, as well as new types of petrol and diesel engines. Considering that, at the present moment, it is not possible to be sure about which technology will be the dominant, Toyota have been exploring either new technologies and developing lean-burn engine technology, which best example is the Toyota D-4 direct-injection petrol engine (EIU, 4th, 1998). The third scenery is associated with hybrid vehicles6 – an electric engine and an internal ignition engine from mineral fuel. The technology of an electric engine, though simpler and well known, seems to faced two problems of difficult solution: the limited capacity of energy storage in the batteries7 and the high cost (and a subsequent restriction) required by a vehicle with two propulsion engine (Automotive Industry, October, 1999)8. The forth scenery is related to cells fuel technology. In this case vehicles could adopt, as energy source, alternatively a mineral fuel – in this case the emission reduction would be 4 It is obvious that the increasing tendency of embodied electronic, new materials, and a more intensive use of Internet, both in the association between the assemblers and suppliers and the assemblers/suppliers and consumers, is considered compatible with all the other scenarios proposed here. The difference between the scenarios depends on the arrival, or not, of technological changes regarding the propulsion car engine. It is possible too, that the introduction of a new propulsion technology has, as a result, an intensification of technologies mentioned previously. Such fact does not seem to compromise the criterion adopted in the present study 5 It involves the main oil companies – “the biggest oil companies have been spent hundred millions dollars in Research and Development with hydrogen”(FT.com, 24th March, 2000: 1, Internet) – the companies related more directly
Details
-
File Typepdf
-
Upload Time-
-
Content LanguagesEnglish
-
Upload UserAnonymous/Not logged-in
-
File Pages25 Page
-
File Size-