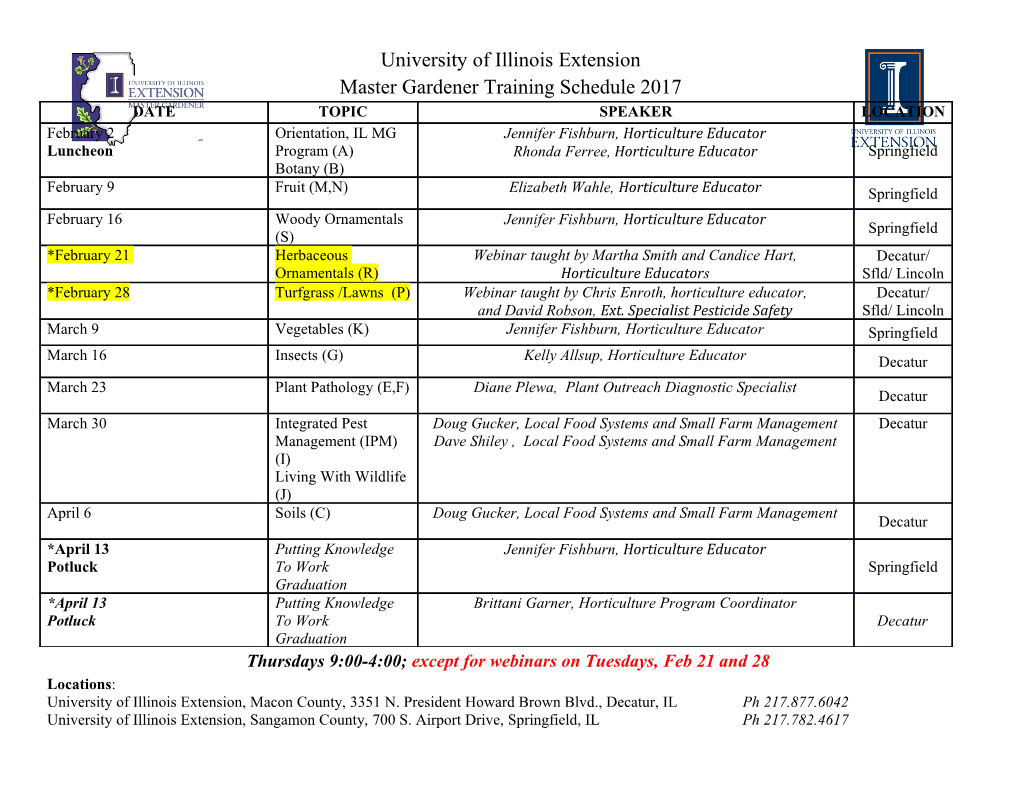
Europaisches Patentamt 0136 542 J European Patent Office Publication number: B1 Office europeen des brevets EUROPEAN PATENT SPECIFICATION F G 01 J 3/46, Date of publication of patent specification: 08.08.90 intci.5: B 41 33/00, G 01 N 21/59 Application number: 84110310.4 Date of filing: 30.08.84 Color printing control using halftone control areas. Priority: 20.09.83 US 533925 Proprietor: KOLLMORGEN CORPORATION 24.08.84 US 643243 10 Mill Pond Lane Simsburv.CT 06070 (US) Date of publication of application: 10.04.85 Bulletin 85/15 Inventor: Benoit, Albert J. Crabapple Lane Sandy Hook, Conn. 06482 (US) Publication of the grant of the patent: Inventor: Boden, Dudley M. 08.08.90 Bulletin 90/32 98 Boulevard Cornwall-on-Hudson, NY 12520 (US) Inventor: Decker, David G. Designated Contracting States: 13 Woodland Drive CHDEFRGBITLISE NewPaltz,NY12561(US) Inventor: Kishner, Stanley J. 5 Mohawk Lane References cited: Pomona, NA 10970 (US) FR-A-2512 950 Inventor: Van Arsdell, Robert D. 11 Helen Drive Wappinger Falls, NY 12590 (US) CM Representative: Konigseder-Egerer, Claudia D. Zugspitzstrasse 65 in D-8104Grainau(DE) CO w Note: Within nine months from the publication of the mention of the grant of the European patent, any person may give notice to the European Patent Office of opposition to the European patent granted. Notice of opposition shall Q. be filed in a written reasoned statement. It shall not be deemed to have been filed until the opposition fee has been LU paid. (Art. 99(1 ) European patent convention). Courier Press, Leamington Spa, England. EP 0136 542 B1 Description This invention relates to a method for controlling multicolor printing processes, including lithography, gravure, letterpress and flexography, whereby predetermined areas on the printed material are measured 5 by a densitometer, either manually, or automatically on the printing press. The results of these measurements are used to control various parameters on the printing press in order to maintain an acceptable level of quality in the printed colors. Up to the present time, control of the printing process has been largely in the hands of the pressmen. He and his have crew had to exercise a great deal of judgment in determining how to adjust printing press w parameters in order to generate a final printed product that is acceptable to the customer. Acceptability is judged by visual assessment. The complexity of modern printing processes demands that the pressmen have a high level of expertise and experience for exercising such judgments. The high operating speeds of modern printing presses, coupled with the high cost of ink and paper, put further pressure on the pressman to exercise control of the press in a timely fashion. If he is not successful, materials, time and effort are is wasted as unacceptable products are printed. Typically, 20% of all ink and paper used for printing is wasted. Several percent of this is due to improper colors and is responsible for millions of dollars of waste per year. Multi-color printing processes most often combine four inks, called process inks, in order to achieve the final printed product. These colors, usually cyan, magenta, yellow and black, are printed sequentially on 20 the same area of the substrate, and interact to produce a wide gamut of colors. Most printed images are produced with halftone screens, yielding images that are arrays of small dots of varying sizes. Both, the amount of ink present in the dots, and the dot sizes, are important in achieving the proper printed color. The use of instrumentation in the printing process can provide timely accurate control. It is more consistent and objective than visual judgment. While the acceptability of a printed product is best judged 25 visually, control of the process in order to maintain a given level of quality is best achieved through the use of instrumentation. A densitometer is an optical instrument used to measure the lightness or darkness of an image. Its numerical output, called optical density, is based in the logarithm of the optical reflectance of the image, and correlates well with visually perceived lightness or darkness. The logarithmic scale, however, is not necessary for the control of printing, and a reflectance measuring instrument based on 30 linear scaling could be used for the same purpose. Designed as a quality control tool, the densitometer utilizes color filters or other means for isolating spectral regions that are complementary to the colors of the process inks in density. Instruments known as reflectometers or spectrophotometers, when used for the same purpose, are equivalent to a densitometer. Patents describing densitometers that provide density readout to the press operator are, e.g., 35 US 2,968,988 and US 4,210,078. Patents that suggest the use of density measurements for automatic inking control are, e.g., US 3,756,725, 3,835,777, 4,003,660 and 4,200,932. None of these patents describe the exclusive use of two different three-color halftone control targets for the instrumental control of multi-color printing. In order to properly control the quality of printed colors, certain parameters of the process need to be 40 measured. Visual assessment alone is not sufficiently reliable, since it is subjective, and varies from one press operator to another. Ideally, these measurements will be made within the printed image, whereby the density of certain key colors could be monitored. Sometimes it is, however, difficult to find an area suitable for measurement. In order to avoid this difficulty, control targets, often called color bars, are used. These are usually printed in a 45 waste area of the sheet and contain a variety of targets for each color. Control targets consist of patches of solid and halftone printing, for each ink individually, as well as in combination with different inks. Provided that changes within the control targets are representative of those occurring within the image, measurements of the control targets can be used as an objective means of monitoring and controlling the color of the printing. Control targets are often disposed at various locations across the printed image, and 50 so a densitometer needs to be positioned at these various locations in order to measure their optical densities. One or more densitometers can be sequentially positioned at these multiple locations, or mounted at fixed positions of a limited number of lateral positions across the width of the press need to be accessed. The most important characteristics of the final print which require measurement and control in both 55 single and multicolor work are tone reproduction (which implies control of dot size) and solid density. The parameters which are essential in this context are those which directly affect the amount of ink layed down on the substrate, and the dot area produced together with the relative magnitude of each of these parameters when more than one color is printed. The amount of ink applied to the substrate can be monitored by measuring, with a densitometer, the so optical density of a solid color bar. The measurement can be made automatically on the press, or manually off the press. Dot area is determined by first measuring the density of a halftone color bar and a nearby solid color bar and then calculating dot area via an equation such as the Yule-Nielsen equation 65 EP 0136 542 B1 -D./n ft 1-10 a = -D /n (1) 1-10 s which is disclosed in Yule, J. A. C. and Nielsen, W. J. "The Penetration of Light into Paper and its Effect on Halftone Reproduction", TAGA Proceedings, 1951, pp. 65—76. In the Yule-Nielsen equation, Dh is halftone density, Ds is solid density and n is a constant factor that accounts for the light scattering properties of the w substrate. The dot area "a" has a value between 0 and 1. The printed dot area is influenced by a multitude of printing parameters, including the pressure between the printing plate and the blanket cylinder, the thickness of the ink film, the ink/water balance and various mechanical properties of the press. Increase in dot area, known as dot gain, must be continually monitored during a run, since excessive dot gain will influence the tone reproduction and color of the printed image. 15 One of the most frequent decisions faced by a press operator arises when the measured density of a halftone color bar, for one of the process colors, increases during the printing run. He must decide whether the density is the result of a thicker film of ink, or dot gain. By measuring the density of a halftone color bar and a solid color bar, this question can be answered, and he can act to reduce the ink flow, or to reduce sources of dot gain. 20 The presence of color bars is not usually desired in the final printed product. Sometimes, the color bars are printed in a region that will later be trimmed so that they can be used for control of printing, and then discarded. In some instances, the color bars can be hidden, as in the folds of a package, or in the binding of a magazine. When color bars cannot be trimmed or hidden, they are usually not printed. In such cases, the use of instrumentation for control is abandoned. 25 It appears, however, that certain color bars can be camouflaged so that their presence is not objectionable. For example, one commonly used control target is used to measure gray balance. This type ' of color bar is disclosed in "The New GATF Color Reproduction Guide" by Z. Elyjiw and F. Preucil, GATF Research Progress No.
Details
-
File Typepdf
-
Upload Time-
-
Content LanguagesEnglish
-
Upload UserAnonymous/Not logged-in
-
File Pages17 Page
-
File Size-