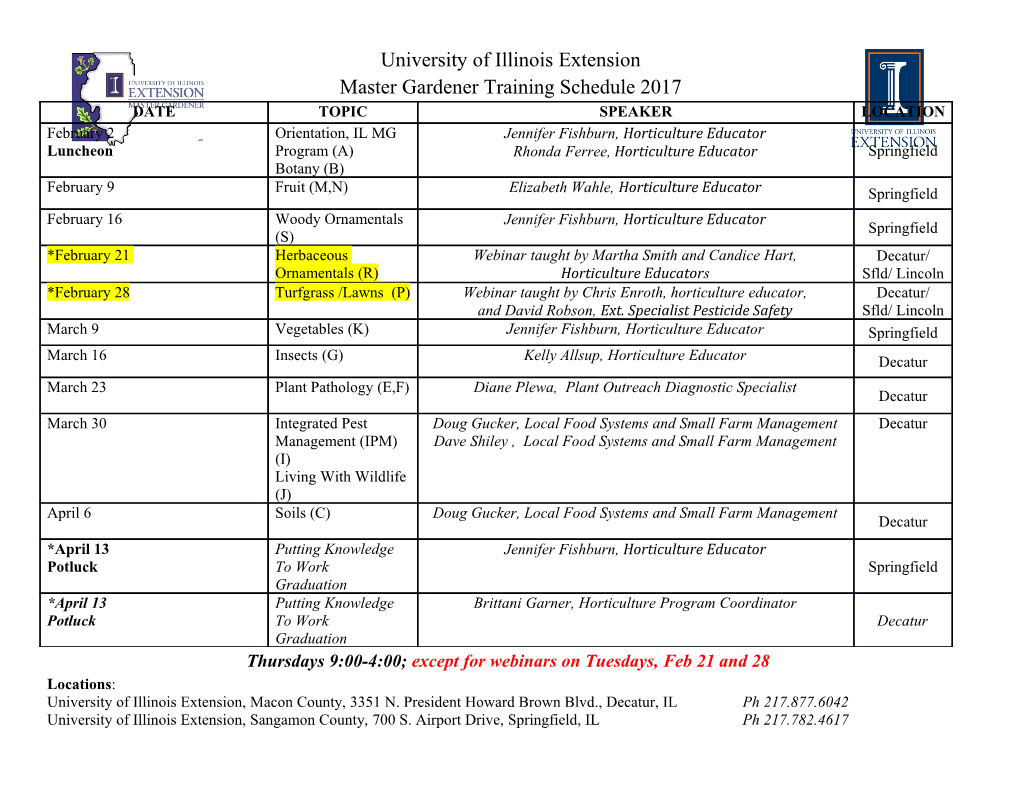
metals Article Crack Propagation Mechanisms for Creep Fatigue: A Consolidated Explanation of Fundamental Behaviours from Initiation to Failure Dan Liu and Dirk John Pons * ID Department of Mechanical Engineering, University of Canterbury, Christchurch 8041, New Zealand; [email protected] * Correspondence: [email protected]; Tel.: +64-3369-5826 Received: 10 July 2018; Accepted: 2 August 2018; Published: 8 August 2018 Abstract: Background—Creep-fatigue damage is generally identified as the combined effect of fatigue and creep. This behaviour is macroscopically described by crack growth, wherein fatigue and creep follow different principles. Need—Although the literature contains many studies that explore the crack-growth path, there is a lack of clear models to link these disparate findings and to explain the possible mechanisms at a grain-based level for crack growth from crack initiation, through the steady stage (this is particularly challenging), ending in structural failure. Method—Finite element (FE) methods were used to provide a quantitative validation of the grain-size effect and the failure principles for fatigue and creep. Thereafter, a microstructural conceptual framework for the three stages of crack growth was developed by integrating existing crack-growth microstructural observations for fatigue and creep. Specifically, the crack propagation is based on existing mechanisms of plastic blunting and diffusion creep. Results—Fatigue and creep effects are treated separately due to their different damage principles. The possible grain-boundary behaviours, such as the mismatch behaviour at grain boundary due to creep deformation, are included. The framework illustrates the possible situations for crack propagation at a grain-based level, particularly the situation in which the crack encounters the grain boundary. Originality—The framework is consistent with the various creep and fatigue microstructure observations in the literature, but goes further by integrating these together into a logically consistent framework that describes the overall failure process at the microstructural level. Keywords: creep fatigue; crack growth; grain boundary 1. Introduction The process of fatigue failure is physically and macroscopically described by crack-growth behaviour. The situation is complicated when creep is also present, because this provides an additional mechanism for plastic deformation and crack growth. In the case of creep-fatigue, an engineering structure fails when the crack length achieves a critical value. The total damage is the accumulated effect of cycle count, temperature, and period (frequency). Some of the ways this has been modelled is to prove a mathematical representation of the various components of facture mechanics [1–3] or to apply curve fitting [4–6]. However, this is not the present topic. Here we are more interested in the progression of crack growth at the microstructural level [7–10], specifically the way the crack navigates through the grains and along grain boundaries under the combined effects of cyclic loading and creep. Existing works do not provide an integrative treatment of this process. This paper develops a microstructural theory for crack growth. It does so by adapting existing mechanisms of plastic blunting and diffusion creep into an integrative conceptual framework. Metals 2018, 8, 623; doi:10.3390/met8080623 www.mdpi.com/journal/metals Metals 2018, 8, x FOR PEER REVIEW 2 of 34 MetalsThis2018, paper8, 623 develops a microstructural theory for crack growth. It does so by adapting existing2 of 32 mechanisms of plastic blunting and diffusion creep into an integrative conceptual framework. This provides a logically consistent framework that describes the creep-fatigue failure in terms of This provides a logically consistent framework that describes the creep-fatigue failure in terms of microstructural damage. microstructural damage. 2. Background Literature 2.1. Phases of Crack Growth ItIt isis generallygenerally accepted accepted that that the the process process of crackof crack growth growth under under cyclic cyclic loading loading is divided is divided into three into phasesthree phases (Figure (Figure1)[ 8]: crack1) [8]: initiation,crack initiation, crack propagation, crack propagation, and structural and structural fracture. fracture. Specifically, Specifically, the first stagethe first presents stage presents a threshold, a threshold, below which below there which is no th crackere is growth.no crack The growth. second The stage second shows stage a relatively shows a steadyrelatively state, steady in which state, thein which crack growththe crack rate growth increases rate steadilyincreases with steadily the increasingwith the increasing number of number cycles (thisof cycles is always (this is described always described by Paris’ Lawby Paris’ [11]). Law The [11] final). stageThe final represents stage represents an unstable an situation, unstable wheresituation, the engineeringwhere the engineering structure fails structure within fails a small within number a small of number cycles. of cycles. Figure 1. Three stages of crack growth. 2.2. Established Principles in the Literature Crack growth caused by fatiguefatigue effect isis attributedattributed toto plasticplastic deformationdeformation at aa crack-tipcrack-tip plasticplastic zone, whereinwherein the the plastic plastic deformation deformation occurs occurs via via dislocations dislocations [7]. Ordinarily[7]. Ordinarily there there is a preferred is a preferred plane, andplane, in and that in plane that thereplane are there specific are specific directions directions along whichalong dislocationwhich dislocation motion motion occurs; occurs; the slip the plane. slip Theplane. axial The (tension axial (tension or compression) or compression) loading is decomposedloading is decomposed into a normal into stress, a normal which isstress, perpendicular which is toperpendicular the slip plane, to andthe slip a shear plane, stress, and whicha shear is stress, parallel which to the is slipparallel plane. to Thisthe slip shear plane. stress This then shear results stress in thethen movements results in the along movements the slip plane.along the This slip implies plane. thatThis shear implies stress that contributes shear stress tocontributes plastic dislocation, to plastic anddislocation, then results and inthen crack results growth. in crack In this growth. case, the In axialthis case, loading the isaxial transformed loading is into transformed the shear stressinto the to produceshear stress fatigue to produce propagation. fatigue propagation. The simplest form of dislocationdislocation is edge dislocation,dislocation, see Figure2 2,, whichwhich representsrepresents aa simplisticsimplistic grain unit. Specifically, Specifically, the dislocation starts from the extra half-plane of atoms (plane I), which is identifiedidentified asas aa defect.defect. When a shear stress is applied, and its magnitude magnitude is sufficient, sufficient, the bond between atom A and atomatom BB isis cut.cut. Then, the bottom of all planes move to the right, and atom B isis bondedbonded withwith itsits neighbouringneighbouring atom (atom C). In this case, a new half-plane of atoms (plane II) is generated. Under thethe shearshear stress, stress, this this irreversible irreversible process process is successivelyis successively and and repeatedly repeatedly presented, presented, with with the final the resultfinal result being being the creation the creation of a step of a at step the at edge the ofedge this of unit. this Theunit. process The process is irreversible is irreversible because because the other the atomsother atoms in the grainin the also grain move also into move new into positions new (notpositions shown (not in theshown figure) in duethe tofigure) other disturbances,due to other hencedisturbances, the atoms hence do not the spontaneously atoms do not revert spontaneously to their original revert positions to their (plastic original deformation). positions (plastic Hence, deformation). Hence, the dislocation is an enduring feature of the grain. It can, however, be sent in a the dislocation is an enduring feature of the grain. It can, however, be sent in a new direction should new direction should the orientation of the shear stress change, as occurs in reversed loading. By this the orientation of the shear stress change, as occurs in reversed loading. By this means, the plastic means, the plastic deformation is produced due to the motion of numbers of dislocations. In addition, deformation is produced due to the motion of numbers of dislocations. In addition, there may be there may be atomic displacement perpendicular to the plane, hence causing a screw dislocation. In atomic displacement perpendicular to the plane, hence causing a screw dislocation. In practical Metals 2018, 8, 623 3 of 32 Metals 2018, 8, x FOR PEER REVIEW 3 of 34 practicalsituations, situations, the behaviours the behaviours of edge and of screwedge and dislocations screw dislocations are mixed, are and mixed, both contribute and both tocontribute the overall to plasticthe overall deformation plastic deformation of the grain of and the ultimatelygrain and ultimately of the macroscopic of the macroscopic deformation deformation of the part. of the part. Figure 2. Edge dislocation process. Figure 2. Edge dislocation process. As mentioned above, the half-plane of atoms is regarded as the source of dislocation. The edge of thisAs half mentioned plane is terminated
Details
-
File Typepdf
-
Upload Time-
-
Content LanguagesEnglish
-
Upload UserAnonymous/Not logged-in
-
File Pages32 Page
-
File Size-