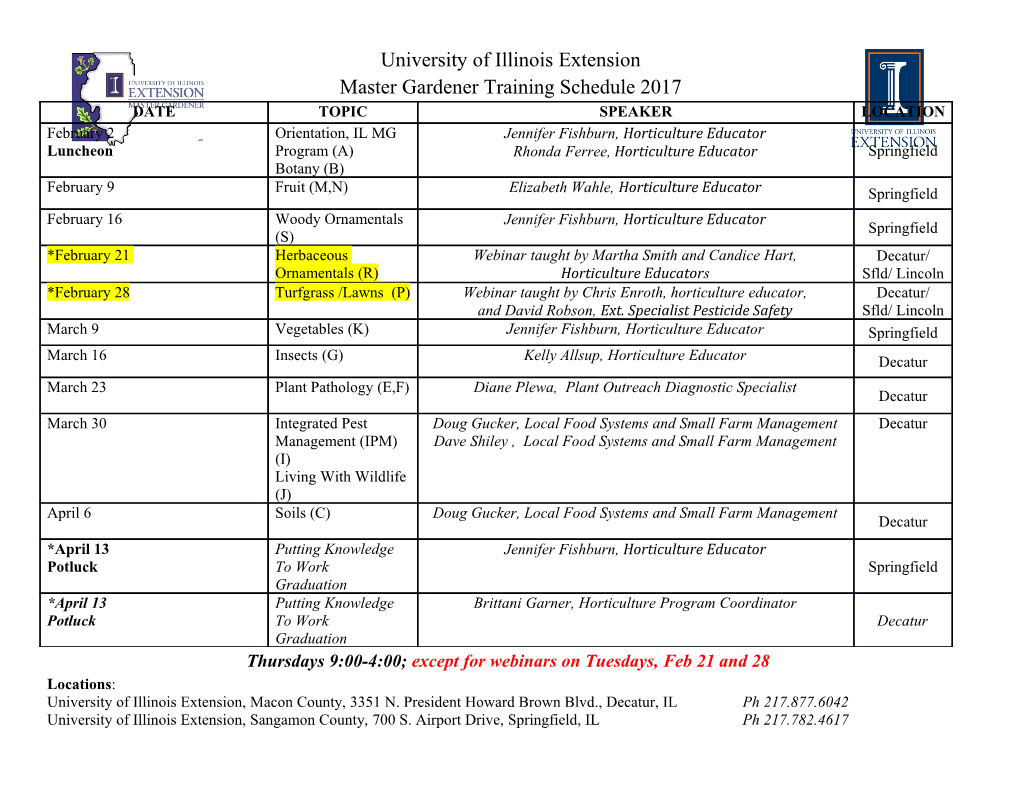
Europaisches Patentamt (19) European Patent Office Office europeenpeen des brevets EP 0 663 379 B1 (12) EUROPEAN PATENT SPECIFICATION (45) Date of publication and mention (51) intci.6: C07C 17/35, C07C 25/13 of the grant of the patent: 23.12.1998 Bulletin 1998/52 (21) Application number: 95300226.8 (22) Date of filing: 13.01.1995 (54) Process for the production of substituted aromatic hydrocarbons from corresponding anilines by dediazoniation Verfahren zur Herstellung von substituierten aromatischen Kohlenwasserstoffen durch Dediazonierung der ubereinstimmenden Anilinen Procede pour la production d'hydrocarbures aromatiques substitues par dediazonisation des anilines correspondantes (84) Designated Contracting States: (74) Representative: AT BE CH DE DK ES FR GB GR IE IT LI LU MC NL Ellis-Jones, Patrick George Armine et al PT SE J.A. KEMP & CO. 14 South Square (30) Priority: 13.01.1994 GB 9400569 Gray's Inn London WC1R 5LX (GB) (43) Date of publication of application: 19.07.1995 Bulletin 1995/29 (56) References cited: WO-A-93/19026 (73) Proprietor: RHODIA LIMITED Watford, Herts WD1 1QM (GB) • CHEMICAL ABSTRACTS, vol. 115, no. 15, 14 October 1991, Columbus, Ohio, US; abstract no. (72) Inventors: 158599, K AKIN AMI T ET AL 'Indirect synthesis • Mercier, Claude of bromo-substituted aromatic compounds' & Sneyd Park, Bristol BS9 1 RU (GB) UBE KOGYO KOTO SENMON GAKKO KENKYU • Scott, Graham Vaughan HOKOKU (UKKHDQ,03864359);91; VOL.37,; Chew-Magna, Avon BS18 8SX (GB) PP.43-7, UBE TECH. COLL.;UBE; JAPAN (JP) • PATENT ABSTRACTS OF JAPAN vol. 015, no. 163 (C-0826) 24 April 1991 & JP-A-03 034 944 (TOOKEMU PROD:KK) 14 February 1991 DO O) Is- CO CO CO CO Note: Within nine months from the publication of the mention of the grant of the European patent, any person may give notice the Patent Office of the Notice of shall be filed in o to European opposition to European patent granted. opposition a written reasoned statement. It shall not be deemed to have been filed until the opposition fee has been paid. (Art. a. 99(1) European Patent Convention). LU Printed by Jouve, 75001 PARIS (FR) EP 0 663 379 B1 Description This invention relates to the production of aromatic hydrocarbons. It is well known to replace aromatic primary amino groups by hydrogen by converting the amino group into a 5 corresponding diazonium salt group and then reducing the latter. For this purpose a number of reducing agents have been used, including hypophosphorous acid (H3P02) and primary alcohols. A metallic catalyst, e.g. copper or one of its salts, is usually included in the reaction mixture to promote the reduction. 1 ,3-Difluorobenzene is an important intermediate in the preparation of antifungal agents, and it has often been prepared from 2,4-difluoroaniline by diazotisation followed by reducing dediazoniation. Japanese Patent Application 10 91/34944 (Tokemu Product K.K., Chemical Abstracts 115: 28858c) describes the production of 1 ,3-difluorobenzene by diazotization of 2,4-difluoroaniline and reductive dediazoniation with hypophosphorous acid in the presence of more than 2 moles of acid (3 moles in the Examples). In another process, the reduction has been effected with isopropanol in the presence of a copper catalyst. Chemical Abstracts 1991 , 115 (15), 158599e describes reacting bromobenzamine derivatives with NaN02/H2S04 is in water and 30% phosphinic acid. These processes have significant disadvantages in practical use. Diazonium salts are unstable and can decompose violently in the solid or concentrated form. The handling of diazonium salts in sub- stantial quantities on an industrial scale requires special precautions to prevent accident. Moreover, the known proc- esses produce significant quantities of effluent which requires treatment (e.g. to reduce its copper content) before it can be discharged. There is therefore a need for a process which can be operated easily on an industrial scale with 20 reduced risk and reduced quantities of effluent. We have now devised a process in which the diazotization of substituted aromatic primary amines is carried out in the presence of hypophosphorous acid and a suitable metal catalyst so that the diazonium salt group formed is immediately replaced by hydrogen. The reaction mixture thus never contains any substantial quantity of diazonium salt. Moreover, reduced quantities of reagents, especially catalyst and mineral acid, are used, and this very considerably 25 simplifies the handling of the effluents produced by the process, and its volumic productivity is increased. An improved method for the isolation of the substituted aromatic hydrocarbon has also been devised which makes it possible to obtain a product of high purity in a very simple way. The process of the present invention for the production of a substituted aromatic hydrocarbon from a corresponding substituted aromatic primary amine comprises converting the said amine into a corresponding diazonium salt in the 30 presence of hypophosphorous acid or a hypophosphite salt and, optionally, a strong acid (i.e. an acid having a pKa less than or equal to O) in an amount not greater than that required to convert the amine into an acid addition salt thereof and to convert a said hypophosphite salt (if used) into hypophosphorous acid, and a metal catalyst that promotes reduction of the diazonium salt, e.g. a copper or iron catalyst (so that the diazonium group is replaced by hydrogen as it is formed). 35 The new process is especially useful for the production of substituted aromatic hydrocarbons such as the 1 ,3-di- fluorobenzene already mentioned. Thus, in its preferred operation, the new process involves the conversion of a starting material of formula: 40 NH2 (Hal). 45 where R is alkyl, alkoxy or alkylthio each of which has up to 4 carbon atoms and is unsubstituted or substituted by halogen, e.g. methyl, trifluoromethyl, trifluoromethoxy, or trifluoromethylthio, Hal is fluorine, chlorine or bromine, m is so 0 to 4, and n is 1 to 5, the Hal radicals being the same or different when n is 2 to 5, and the sum of m and n being 1 to 5, into a product of the formula: (Hal)n 2 EP 0 663 379 B1 where Hal, m and n are as hereinbefore defined. The diazotisation of the aromatic amine is carried out with reagents of known kind. Thus the amine, in the presence of a suitable strong mineral acid, preferably an oxygen-containing acid such as sulphuric acid, may be treated with an alkali metal nitrite, e.g. sodium nitrite. Since, in the process of the invention, the diazotisation is carried out in the 5 presence of hypophosphorous acid (H3P02), the latter may be used to convert the alkali metal nitrite into nitrous acid. The reduction of the diazonium salt to replace the diazonium group by hydrogen requires 1 mole of hypophosphorous acid per mole of starting amine (i.e. per amino group to be replaced by hydrogen). In principle, therefore, 1 mole of hypophosphorous acid per mole of starting amine can be used both to convert the required amount of alkali metal nitrite into nitrous acid, and to reduce the diazonium group. However, in practice, a moderate excess of acid (preferably 10 not more than 1 .33 mole per amino group to be replaced) should be used. If hypophosphorous acid is used as the sole mineral acid, 1 to 2 moles per mole of starting amine are used, while if a strong mineral acid is also included in the reaction mixture, then the proportion of hypophosphorous acid may be reduced, but not below 1 molar proportion per amino group to be replaced, and the amount of the strong acid may be 0 to 1 equivalent per mole of starting amine. It is to be noted in this connection that sulphuric acid behaves in the context of the present invention as a monobasic is acid as its second dissociation constant is not that of a strong acid as defined above. If the hypophosphorous acid is introduced in the form of a salt, e.g. NaH2P02, 1 equivalent of strong mineral acid is required to convert this salt into hypophosphorous acid, and one equivalent of the strong acid is also required to convert the alkali metal nitrite into nitrous acid. In no case are more than 2 equivalents of total acids used per mole of amine. 20 The reaction may be operated at a temperature in the range of 10 to 80°C. At temperatures below about 10°C, the reaction proceeds only slowly even in the presence of the catalyst. At above 80°C, the reaction may be difficult to control. A preferred temperature range is 20 to 50°C. A metal catalyst based on, for example, iron or preferably copper is included in the reaction mixture. The proportion of copper catalyst required is only 0.001 to 0.1 moles of copper, preferably about 0.005 moles, per mole of the aromatic amine starting material. The copper catalyst is conveniently 25 added in the form of a cupric salt, e.g. cupric sulphate, but can, if desired, be added in other forms, e.g. as cuprous oxide (Cu20) or even finely divided metallic copper. The reaction is preferably operated by forming a reaction mixture comprising aqueous hypophosphorous acid (as such or as a salt), e.g. in a proportion of 1 .00 to 1 .3 moles per mole of the amine to be used, and sulphuric acid in a proportion of 0.25 to 0.5 moles per mole of amine (plus any amount required to convert a salt of hypophosphorous 30 acid into the free acid). To this mixture, the copper catalyst, e.g. cupric sulphate, is added in a proportion of 0.002 to 0.01 moles per mole of amine.
Details
-
File Typepdf
-
Upload Time-
-
Content LanguagesEnglish
-
Upload UserAnonymous/Not logged-in
-
File Pages9 Page
-
File Size-