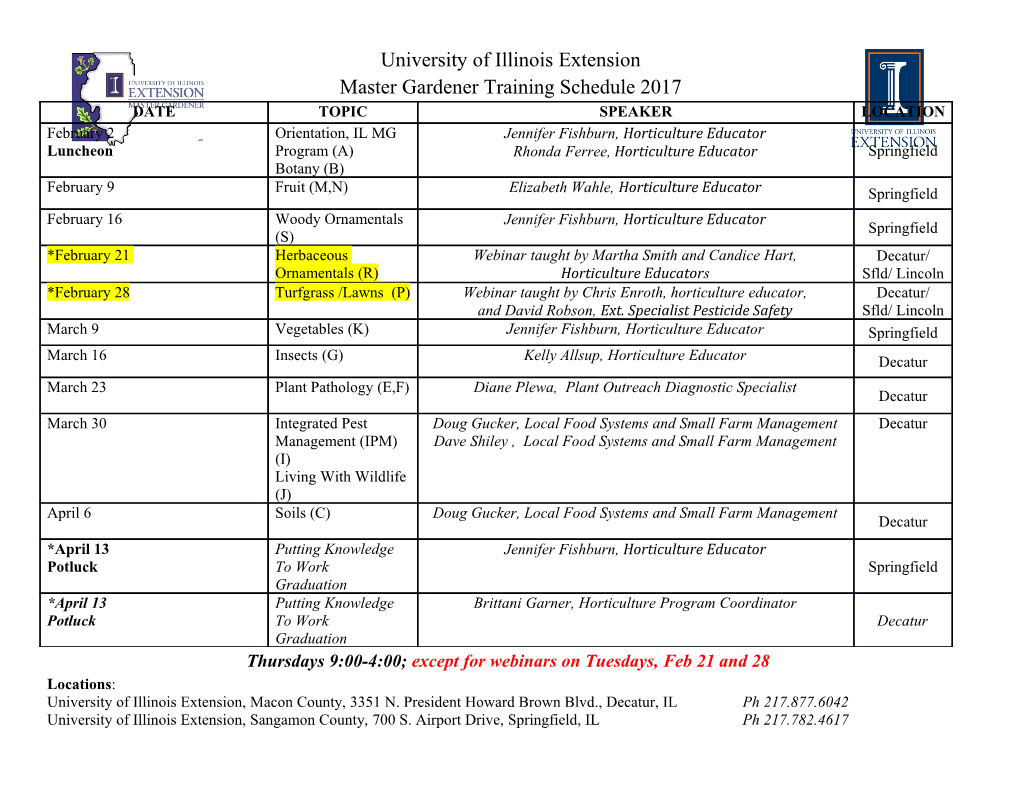
Paper ID #21403 A Portable Engine Dynamometer Test Cell for Studying Spark-ignition En- gine Performance and Mechanical-Electrical-Thermodynamic Energy Con- version Prof. Gene L. Harding, Purdue Polytechnic Institute GENE L. HARDING is an associate professor of Electrical and Computer Engineering Technology at Purdue University, where he has taught since 2003. He has three years of industrial experience with Agilent Technologies, 28 years of combined active and reserve service in the United States Air Force, holds an MSEE from Rose-Hulman Institute of Technology, and is a licensed professional engineer. Dr. Megan Prygoski, Purdue University, West Lafayette Dr. Prygoski teaches Mechanical Engineering Technology at Purdue University’s South Bend campus. She has her B.S. in Mechanical Engineering from the University of Arizona and a M.S. and Ph.D. in Mechanical Engineering from the University of Notre Dame. Her teaching focuses on energy transfer and thermodynamics and well as introductory mechanics classes such as Statics and Dynamics. Her personal interests are in Orthopedics which she uses as teaching examples in the mechanics classes. Dr. James Burns, Purdue Polytechnic Institute Jim Burns, Ph.D. Assistant Professor, Department of Technology Leadership & Innovation Bio: Jim joined the faculty at Purdue Polytechnic in 2015 after completing a Ph.D. in Industrial Engineering from Western Michigan University, and has more than 10 years industry experience in the manufacturing sector in a variety of roles including process engineering, operations management, and technical sales. His area of expertise centers on applying OR/MS and Simulation techniques to Supply Chain & Operations Management problems, and has also conducted research in the areas of Human Factors and Work Design for evaluating time and motion efficiencies of operations. Jim also holds an undergraduate IE degree and a Six Sigma Greenbelt. Mr. Brian Jeffrey Carmichael, Security Automation Systems Brian is a recent graduate of Purdue University’s Electrical Engineering Technology program. He lives and works in Indianapolis, Indiana. Matthew S. Engstrom, Purdue University Matthew Engstrom is an undergraduate student at Purdue Polytechnic Institute working towards a Bach- elors degree in Electrical Engineering Technology. c American Society for Engineering Education, 2018 A Portable Engine-Dynamometer Test Cell for Studying Spark- Ignition Engine Performance and Mechanical-Electrical- Thermodynamic Energy Conversion Abstract Automotive spark-ignition engines are great platforms for studying a variety of sensors, actuators, and control algorithms, but the size, expense, and maintenance required for an automotive engine coupled with a dynamometer test cell are impractical for many engineering and engineering technology programs. This paper proposes a portable engine-dynamometer test cell using a one-cylinder all-terrain vehicle (ATV) engine driving a set of high-current alternators. Engine loading is to be accomplished with a set of electric resistance heaters and a power switching array. Although associated with a large university, this project is being undertaken by a satellite campus with limited space and financial resources. The plan is to implement the Engine-Dyno Project in phases over a period of years using primarily undergraduate students working on directed projects. The planned phases at this time are as follows: 1. Build a sturdy but portable cart to hold the engine, load cell, accessories, and controls. (This phase is complete.) 2. Install the engine and get it running with no load (complete). 3. Construct a thermoelectric loading system and test the engine using manual switching of the electrical load. 4. Implement and test an electronic control system to dynamically adjust loading. 5. Implement and test a dynamometer control and data acquisition system to perform automated test runs while recording data. 6. Convert the engine to electronic ignition and fuel injection and run baseline tests. 7. Design and implement an engine control system with user-programmable ignition and fuel system parameters, and appropriate test points for monitoring sensor data and controlling actuators. 8. Develop labs for the following courses: Introduction to Automotive Electronics, ECET 38501 (lecture) and ECET 38502 (lab), Heat and Power, MET 22000, and Applied Thermodynamics, MET 32000. The paper begins with background information about how the Engine-Dyno project came about along with a high-level description of the concept, requirements, and estimated timeline. It then lays out details for each project phase and the current project status, including photographs of the construction thus far. Background One of the authors teaches an introductory Electrical and Computer Engineering Technology (ECET) course in automotive electronics, ECET 38501 [1] and ECET 38502 [2], that focuses on sensors and actuators in the context of operating a spark ignition internal combustion engine. The course covers sensor characterization, actuator control, and circuit design to condition sensor output signals and drive actuators. It also describes control systems at a rudimentary level. During the course, students work with a variety of sensors and actuators: thermistor engine coolant and intake air temperature sensors, resistive gas pedal position and fuel level sensors, piezoelectric knock sensors, Wheatstone bridge intake air and oil pressure sensors, mass airflow sensors, inductive rotational sensors, fuel injectors, and distributorless ignition systems. Although these devices provide a great learning experience for interpreting sensor signals and driving fuel injectors and ignition systems, there is currently no opportunity to combine all of these devices with some control theory to operate a real engine. Several years ago someone donated two single-cylinder gasoline engines to us. The lead author wanted to take advantage of the donations to create an engine-dynamometer test cell that would allow operation of one of these engines to do labs in his Automotive Electronics course, and possibly other courses. A traditional turnkey dynamometer is prohibitively expensive, so he decided to embark on a multi-year series of directed student projects (explained below) to create a dynamometer test cell that uses thermoelectric loading. The engine will drive a pair of heavy duty alternators that power an array of electric resistance heaters immersed in a tank of water. Power to the heaters, and thus load on the engine, will be regulated with power switching electronics using pulse width modulation (PWM) control. The long-term undertaking is called the Engine-Dyno project, and a system block diagram of the concept is shown in Figure 1. Figure 1: Engine-Dyno system block diagram A directed project, designated ECET 29900, is a variable-credit course that can be modified as needed to fit a wide variety of circumstances. For each project, the professor and student(s) craft a proposal that is essentially a contract for the project. It includes the stated purpose, general steps involved, deliverables, and the grading standard to be applied. A directed project template is shown at Appendix 1. Once the Engine-Dyno is complete, the current plan is to continue a compressed version of the existing sensor/actuator labs for the Automotive Electronics course, but augment them with two or three labs that add engine control and data collection activities. Moreover, faculty in other departments plan to use the Engine-Dyno setup in two Mechanical Engineering Technology (MET) courses, two Industrial Engineering Technology (IET) courses, and a Statistics course. The requirements driving the development of the Engine-Dyno test cell are listed below. Requirements followed by [old] are existing requirements that will be continued, while those followed by [new] are new requirements that cannot be met with existing equipment. 1. Condition and convert sensor signals into a usable form. One example would be implementing circuitry to convert the variable-frequency variable-magnitude sinusoidal signal from a magnetic wheel speed sensor and display revolutions per minute (RPM). [old] 2. Effect circuitry to drive automotive actuators, such as a fuel injector. [old] 3. Read sensor data from a running spark-ignition engine. Examples include crankshaft speed and position, exhaust gas oxygen levels, intake manifold pressure, and intake air temperature. [new] 4. Drive actuators, such as fuel injectors and spark plugs, on a running engine. [new] 5. Observe the effect on engine performance of changing fuel mixture and ignition timing. [new] 6. Experiment with different engine control algorithms and techniques. [new] 7. Calculate and experimentally measure energy conversion based on heat transfer and fuel consumption measurements. [new] 8. Any lab equipment emitting noxious fumes must be portable so it can operate outside due to a lack of proper ventilation inside the building. [old] We are currently in Phase 3 of an 8-phase design process. The estimated timeline for the project is depicted in Table 1. This paper discusses the details regarding each project phase, some of which are completed, in progress, and not yet started. For the latter we list the learning objectives that will drive the student directed projects. Table 1: Estimated project timeline by phase Phase # Description Status Planned Completion 1 Build cart Complete August 2016 2 Running engine Complete 05 December 2017 3 Thermoelectric loading via manual In progress Spring
Details
-
File Typepdf
-
Upload Time-
-
Content LanguagesEnglish
-
Upload UserAnonymous/Not logged-in
-
File Pages19 Page
-
File Size-