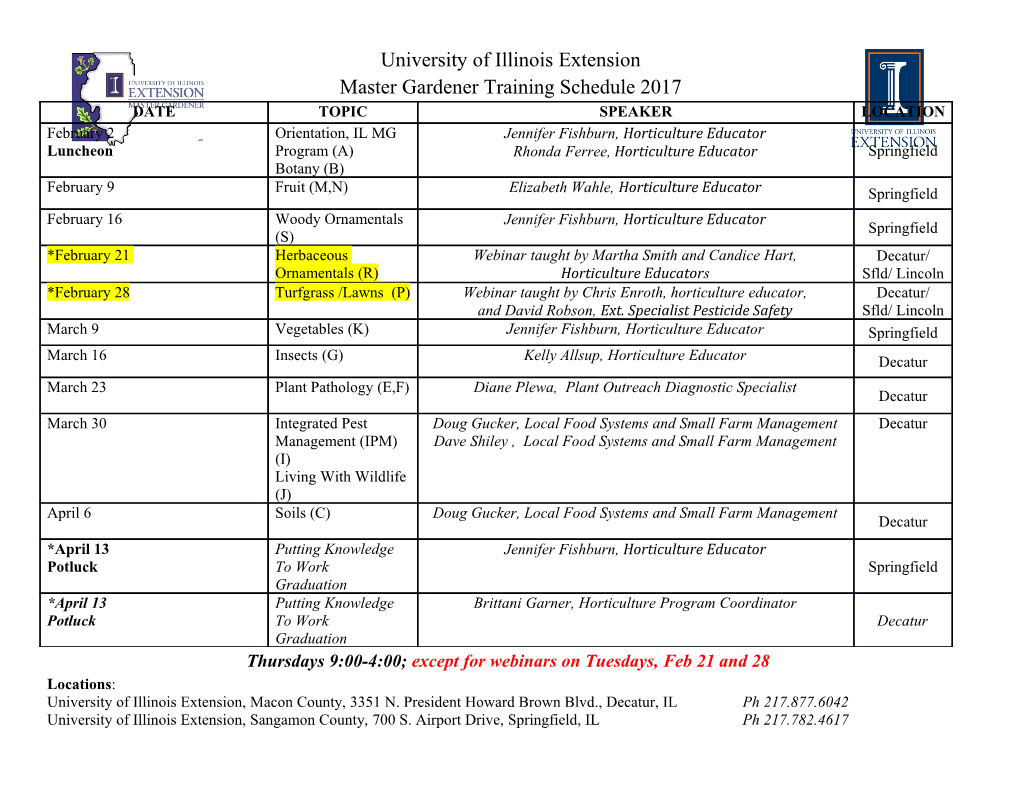
materials Article Microstructure Evolution in High Purity Aluminum Single Crystal Processed by Equal Channel Angular Pressing (ECAP) Jinfang Dong, Qing Dong, Yongbing Dai, Hui Xing *, Yanfeng Han, Jianbo Ma, Jiao Zhang *, Jun Wang and Baode Sun Shanghai Key Laboratory of Advanced High-temperature Materials and Precision Forming, Shanghai Jiao Tong University, Shanghai 200240, China; [email protected] (J.D.); [email protected] (Q.D.); [email protected] (Y.D.); [email protected] (Y.H.); [email protected] (J.M.); [email protected] (J.W.); [email protected] (B.S.) * Correspondence: [email protected] (H.X.); [email protected] (J.Z.); Tel./Fax: +86-21-5474-7387 (H.X.); +86-21-5474-2661 (J.Z.) Academic Editor: Daolun Chen Received: 3 November 2016; Accepted: 16 January 2017; Published: 22 January 2017 Abstract: Aluminum single crystal with 99.999% purity was deformed at room temperature by equal channel angular pressing (ECAP) up to 16 passes. Grain size and misorientation of processed samples were quantitatively characterized by TEM and EBSD. The results show that the refinement efficiency of high purity aluminum single crystal was poor in the initial stage. Extrusion by fewer ECAP passes (n ≤ 8) resulted in only elongated grains containing a large number of subgrains and small misorientations between grains. Stable microstructures of nearly equiaxed grains with high misorientations were obtained by 15 passages, indicating that the initial extremely coarse grains and highly uniform grain orientation are not conducive to the accumulation of strain energy. The initial state of high purity aluminum has a significant effect on the refining efficiency of the ECAP process. Keywords: equal channel angular pressing (ECAP); high purity aluminum; single crystal; deformation; grain boundary 1. Introduction High purity aluminum (Al content ≥ 99.999%), as an important raw material in industry, exhibits a much better performance than general pure aluminum. For instance, it can serve as a sputtering target material to prepare thin films used widely in integrated circuits. Both sputtering rate and thin film performance are strongly correlated with the microstructure of target materials, and fine and homogenous grains are generally required for the applications [1]. Traditional methods (e.g., ball milling, refiner addition) are not suitable for the preparation of high purity aluminum due to the purity limitation, while equal channel angular pressing (ECAP) provides an efficient way to overcome the difficulty [2,3]. ECAP is an attractive method of severe plastic deformation for achieving very significant grain refinement to grain size of submicrometer or even nanometer levels [4–7]. To date, a number of studies have been done to investigate the ECAP processes of pure aluminum and high purity aluminum in both experiments and simulations, amongst which some factors such as extrusion route, extrusion passes, and die angles were studied more frequently [8–15]. For general materials, the initial condition of the material is usually neglected due to less obvious particularity. However, it should be noted that in the process of segregation and purification during directional solidification to get 99.999% purity aluminum, it is easy to form a nearly-consistent orientation relationship (growth along [100] direction) and to form coarse columnar grains with diameter up Materials 2017, 10, 87; doi:10.3390/ma10010087 www.mdpi.com/journal/materials Materials 2017, 10, 87 2 of 8 to several centimeters, as shown in Figure1. These unusual coarse grains can result in substantial decrease ofMaterials original 2017, 10 grain, 87 boundaries in cast ingot, and also lead to smaller misorientations2 of 8 among grains. The influence from the above features cannot be neglected in ECAP processes. diameter up to several centimeters, as shown in Figure 1. These unusual coarse grains can result in In ordersubstantial to study decrease the ECAP of original refinement grain boundaries process (especiallyin cast ingot, under and thealso conditionslead to smaller of low grain boundarymisorientations density and smallamong orientationgrains. The influence relationship from the amongabove features grains), cannot single be neglected crystal in is ECAP considered as an ideal experimentalprocesses. template. Furukawa et al. applied single crystal, making use of its significant advantage of providingIn order to study a unique the ECAP opportunity refinement to process select (especially the orientation under the of theconditions crystal of withlow grain respect to the boundary density and small orientation relationship among grains), single crystal is considered as an pressing directionideal experimental and the template. theoretical Furukawa shear et plane al. applie to studyd single the crystal, fundamental making use refinementof its significant mechanism of ECAP [16advantage–18]. Therefore, of providing they a unique only opportunity performed to select an experiment the orientation of of one-pass the crystal extrusion, with respect andto did not observe thethe whole pressing microstructure direction and the evolution. theoretical In shear this study,plane to a 99.999%study thepurity fundamental aluminum refinement single crystal was appliedmechanism to deformation of ECAP by[16–18]. ECAP Theref to highore, they strain only (16 performed passes, an equivalent experiment stain of one-pass of 13.52). extrusion, Key structural and did not observe the whole microstructure evolution. In this study, a 99.999% purity aluminum parameterssingle ((sub)grain crystal was size applied and to misorientation) deformation by ECAP during to high microstructure strain (16 passes, equivalent evolution stain were of 13.52). quantitatively measured.Key Based structural on the parameters evolution ((sub)grain features size of and both miso parameters,rientation) during grain microstructure refinement andevolution formation were process of subgrainquantitatively boundaries measured. and high Based angle on grainthe evolution boundaries features were of both analyzed paramete andrs, grain further refinement discussed and without consideringformation the influence process fromof subgrain original boundaries grain boundaries.and high angle grain boundaries were analyzed and further discussed without considering the influence from original grain boundaries. Figure 1. Photo of a cast ingot of high purity (99.999%) aluminum. Figure 1. Photo of a cast ingot of high purity (99.999%) aluminum. 2. Experiment 2. ExperimentA single crystal rod of high purity (99.999%) aluminum was used in this study. ECAP specimens had square cross-section with dimensions of 10 × 10 mm2 and length of 50 mm were cut from the rod A singleusing crystal a wire rodcutting of highfacility. purity Figure (99.999%) 2 gives a schematic aluminum diagram was of used the ECAP in this die study. and specimen. ECAP specimens had squareEquivalent cross-section strain εwith of ECAP dimensions is determined of 10by internal× 10 mm angle2 andand external length angle of 50 of mm the die were per cutthe from the rod usingfollowing a wire cutting relationship facility. [19]: Figure2 gives a schematic diagram of the ECAP die and specimen. Equivalent strain " of ECAP isε=N/ determined√32cotφ by/2 internal+ Ψ/2 + Ψ anglecosec( andφ/2 + externalΨ/2), angle of the die per the following relationshipwhere N is the number [19]: of ECAP passes. It can be seen that smaller inner angle leads to larger equivalent strain applied. Furuno used a p die with inner angle" = N/ of 60° 3for(2 the cot extrusion(φ/2 + ofY pu/2re) +aluminum,Y cos ec but(φ /2dies+ withY/2 acute)), angle generally need more extruding force, so cracks easily emerge in the sample [20]. It is also difficult to steadily where N isextrude the number sample to of higher ECAP stains passes. without any heat treatments during the process, which brings about more difficulty and complexity. Therefore, dies with inner angles above 90° were generally used. It canWhile be seen the thatlarger smaller inner angle inner corresponds angle leads to an toeasier larger sample equivalent extrusion, strain the larger applied. angle also Furuno results used a die ◦ with innerin angle smaller of equivalent 60 for the strain. extrusion Moreover, of die pure configur aluminum,ation is correlated but dies with with deformation acute angle effect. generally For need more extrudingexample, force, the experimental so cracks easilystudy for emerge pure Al inusing the a sample90° die revealed [20]. Itthat is route also difficultBC was more to effective steadily extrude sample to higher stains without any heat treatments during the process, which brings about more difficulty and complexity. Therefore, dies with inner angles above 90◦ were generally used. While the larger inner angle corresponds to an easier sample extrusion, the larger angle also results in smaller equivalent strain. Moreover, die configuration is correlated with deformation effect. For example, ◦ the experimental study for pure Al using a 90 die revealed that route BC was more effective than route C and route A [21]. By contrast, experiments using a 120◦ die showed that route A was most Materials 2017, 10, 87 3 of 8 effective because of negligible stress waste [22]. In order to better observe the microstructure evolution under high strain, route A (no sample rotation between neighboring passes) was selected for sample extrusion.Materials Given 2017 the, 10, 87 industrial application of high purity aluminum as sputtering target3 of 8 material, ◦ ◦ a home-designedthan
Details
-
File Typepdf
-
Upload Time-
-
Content LanguagesEnglish
-
Upload UserAnonymous/Not logged-in
-
File Pages8 Page
-
File Size-