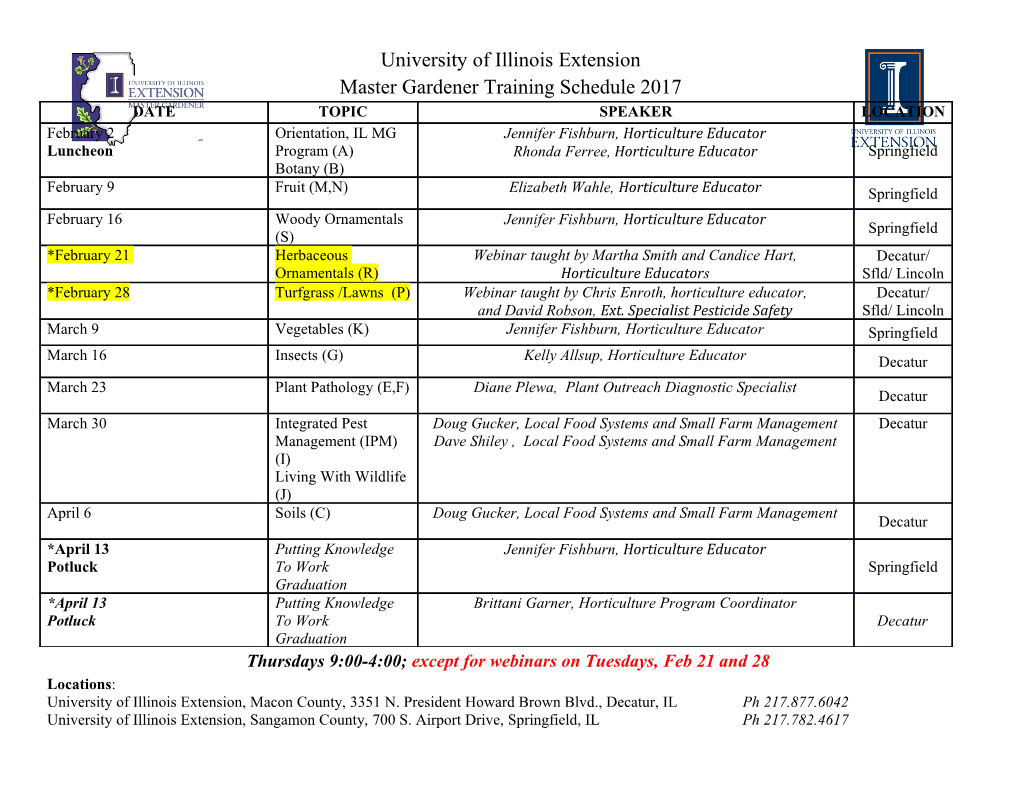
Interface Design of Copper/Alumina Composites with Interpenetrating Phase Structure (Preform-MMCs) by Oliver Patrick Lott Thesis submitted to fulfil the requirements of Doctor of Philosophy School of Materials Science and Engineering, University of New South Wales, Sydney, Australia 2012 Certificate of Originality I hereby declare that this submission is my own work and to the best of my knowledge it contains no materials previously published or written by another person, or substantial proportions of material which have been accepted for the award of any other degree or diploma at UNSW or any other educational institution, except where due acknowledgement is made in the thesis. Any contribution made to the research by others, with whom I have worked at UNSW or elsewhere, is explicitly acknowledged in the thesis. I also declare that the intellectual content of this thesis is the product of my own work, except to the extent that assistance from others in the project's design and conception or in style, presentation and linguistic expression is acknowledged. ______________________________ Oliver Lott, January 2012 i Acknowledgements This thesis was accomplished in cooperation with UNSW School of Materials Science and Engineering, Sydney, Australia, and Aalen University, Materials Research Institute, Aalen, Germany. I express my deepest gratitude to my supervisors at UNSW, Professor Mark Hoffman and Professor Charles Sorrell, for their excellent supervision, advice and guidance; and thank them for fruitful discussions and being always welcomed by them in Sydney. My work would not have been possible without their help and support. I am grateful to Professor Gerhard Schneider of Aalen University for enabling my work in Aalen and for his constant support. My sincere thanks go to Dr Alwin Nagel for supervision and guidance there, and for his trust in me and my project, and for all our discussions. I owe my sincere thanks to the research teams at UNSW, especially to Professor Paul Munroe and Dr Charlie Kong from the EM Unit, and to the Materials Research Institute at Aalen University. Pars pro toto I thank Dirk Staudenecker and Günter Tilk for their constant help: I would not have been able to carry out all the experimental work without them. For their ‘open ears’ I would like to thank Timo Bernthaler, Wilfried Salzwedel, and Thomas Weidler at Aalen University, and thank especially Andreas Häger for his work during his internship at UNSW. My gratitude goes to the staff at UNSW for their assistance and help during my stay here – to Lana Strizhevsky and Jane Gao in particular. A great debt of thanks is owed to Robert Bosch GmbH for financial support during my work: I want to thank Dr Matthias Leonhardt and Jan Göhler especially for their assistance during mechanical testing there. I would like to express my appreciation to Professor Michael Hoffmann and Thomas Waschkies from Karlsruhe Institute of Technology for providing freeze cast preforms. Most of all I would like to thank my family for their attention, support and encouragement during the past years; and especially my girlfriend Jasmin, with the utmost gratitude for her patience throughout. ii Abstract In composite science, interface characteristics have a significant influence on overall composite properties, especially with regard to co-continuous structures. Interface design, therefore, plays a significant role in the manufacture of reliable composites with enhanced mechanical properties; copper oxide, if added in small amounts to alumina preforms in the preparation process, enhances the overall composite properties considerably. The aim of this study is to understand the underlying phenomena and to explain the enhancement of the mechanical properties for reliable fabrication of copper/alumina composites with an interpenetrating phase structure in a squeeze casting infiltration process. The copper used for infiltration has low oxygen content (OF-quality), melted in a reducing atmosphere and, hence, has poor wetting properties. The addition of copper oxide enhances the infiltration process which is not governed by the infiltration initiation, but results in reactions during sintering leading to the formation of aluminate compounds in the microstructure. The aluminate phase is determined as brittle in nature by nanoindentation. The mechanical properties of the composite, however, are enhanced by a factor of two, exhibiting bending strength of up to 800 MPa for additions of as little as 2 wt% copper oxide with good reliability (Weibull modulus of 25.6). Fracture toughness and Young’s modulus are also enhanced to 9.6 MPa.m-0.5 and 220 GPa, respectively. These observed improvements are determined to be the result of reactions during infiltration, as the copper partly dissolves the aluminate phase leading to enhanced infiltration and interface bonding behaviour due to small levels of oxygen enrichment. Residual porosity is reduced and, consequently, mechanical properties enhanced. The dissolution of aluminate leads to fine-structured alumina phases remaining in the microstructure. iii Table of Contents Certificate of Originality .................................................................................... i Acknowledgements .......................................................................................... ii Abstract ............................................................................................................ iii Table of Contents ............................................................................................. iv Symbols ............................................................................................................ vi 1 Introduction ................................................................................................ 1 2 Literature Review ....................................................................................... 4 2.1 Static Wetting ................................................................................................. 4 2.1.1 Wetting in Metal/Ceramic Systems ....................................................................... 7 2.1.2 Manipulating the Wetting System .......................................................................... 9 2.1.3 Reactive Wetting ................................................................................................. 11 2.2 Dynamic Wetting and Infiltration of Porous Media ......................................... 17 2.3 Preform Fabrication ...................................................................................... 28 2.3.1 Freeze Cast Preforms ......................................................................................... 29 2.3.2 Particle Preforms ................................................................................................. 30 2.4 Pressure-assisted Infiltration Techniques ..................................................... 32 2.4.1 Squeeze Cast Infiltration ..................................................................................... 33 2.4.2 Gas Pressure Infiltration ...................................................................................... 38 2.5 Interfaces in the Copper/Alumina system ...................................................... 40 2.5.1 Different Phases and their Formation ................................................................. 41 2.5.2 Characteristics of Phases ................................................................................... 49 2.6 Influence of Interfacial Chemistry on Mechanical Properties ......................... 49 2.7 Mechanical Properties of Interpenetrating Phase Networks .......................... 54 2.8 Summary ...................................................................................................... 56 3 Prelimary work, Hypotheses and Approach .......................................... 59 4 Experimental Procedure.......................................................................... 63 4.1 Characterisation of Raw Materials ................................................................ 63 4.2 Preform Processing ...................................................................................... 68 4.2.1 Fabrication of Sintered Porous Particle Compacts ............................................. 68 4.2.2 Processing of Preforms for Model Investigation ................................................. 72 4.3 Composite Fabrication .................................................................................. 74 4.3.1 Direct Squeeze Cast Infiltration ........................................................................... 74 4.3.2 Gas Pressure Infiltration ...................................................................................... 76 4.4 Characterisation Methods ............................................................................. 77 4.4.1 Permeability of Preforms ..................................................................................... 78 4.4.2 Surface Preparation, Microscopy and Image Analysis ....................................... 79 4.4.3 Mechanical Properties ......................................................................................... 82 4.4.4 Nanoindentation testing ...................................................................................... 84 4.4.5 Thermal Conductivity .......................................................................................... 85 5 Results and Analysis ..............................................................................
Details
-
File Typepdf
-
Upload Time-
-
Content LanguagesEnglish
-
Upload UserAnonymous/Not logged-in
-
File Pages228 Page
-
File Size-