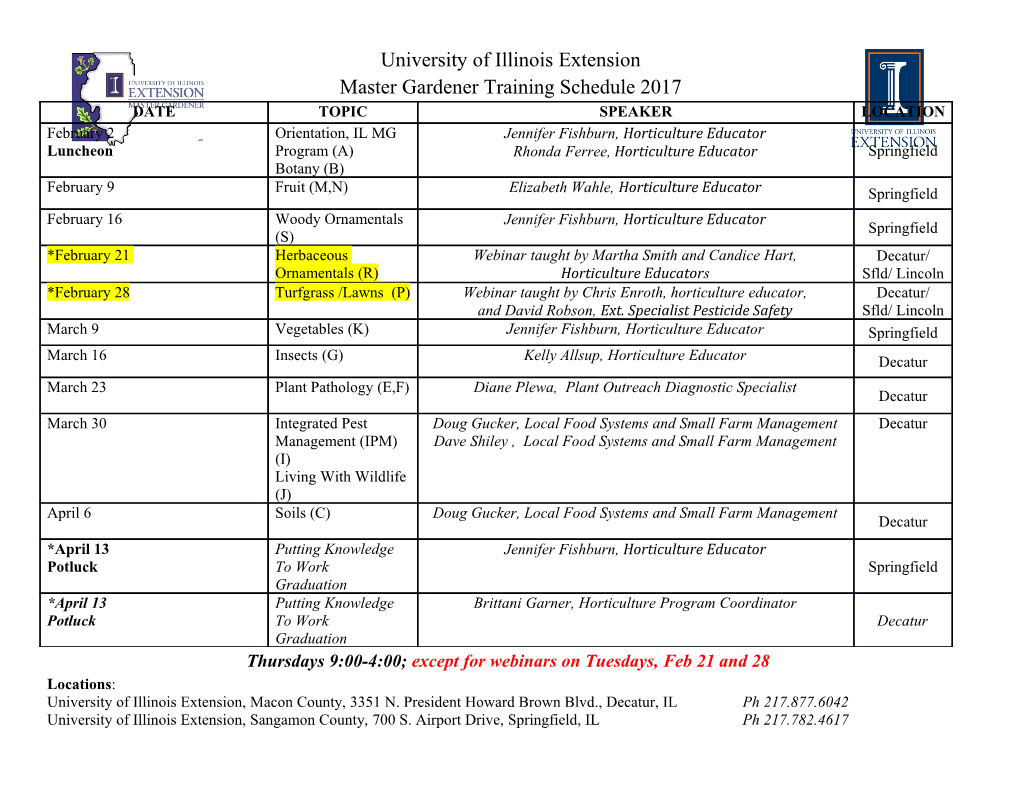
Physics of the Solid State, Vol. 44, No. 6, 2002, pp. 1003–1007. Translated from Fizika Tverdogo Tela, Vol. 44, No. 6, 2002, pp. 961–965. Original Russian Text Copyright © 2002 by Abrosimova, Aronin. METALS AND SUPERCONDUCTORS The Fine Structure of FCC Nanocrystals in Al- and Ni-Based Alloys G. E. Abrosimova and A. S. Aronin Institute of Solid State Physics, Russian Academy of Sciences, Chernogolovka, Moscow oblast, 142432 Russia e-mail: [email protected] Received July 30, 2001 Abstract—The structural perfection of nanocrystals in alloys of different chemical composition is studied by x-ray diffraction and high-resolution electron microscopy. In all the alloys studied, crystallization of the amor- phous phase produces a nanocrystalline structure. The nanocrystal size depends on the chemical composition of the alloy and varies in aluminum-based alloys from 5 nm in Al89Ni5Y6 to 12 nm in Al82Ni11Ce3Si4. Nanoc- rystals in nickel-based alloys vary in size from 15 to 25 nm. Al nanocrystals are predominantly defect-free, with microtwins observed only in some nanocrystals. The halfwidth of the diffraction lines is proportional to sec θ, which implies the small grain size provides the major contribution to the broadening. Nanocrystals in nickel alloys contain numerous twins, stacking faults, and dislocations. © 2002 MAIK “Nauka/Interperiodica”. 1. INTRODUCTION 2. EXPERIMENTAL Al–Ni–Re (Re = Y, Ce, Yb) and Ni–Mo–B amor- A nanocrystalline structure that forms during crys- phous alloys were prepared in the form of ribbons by tallization of an amorphous phase attracts considerable melt quenching on a rapidly rotating wheel. The cool- interest both from the viewpoint of the possibility of ing rate was ~106 K/s, and the ribbons thus obtained developing novel materials with promising physical were 3 mm wide and ~30 µm thick. X-ray measure- chemical properties and as an unusual material in ments were performed on a Siemens D-500 diffracto- which the structural constituents do not exceed a few meter with CuKα radiation. The microstructure was tens of nanometers in size [1, 2]. In most cases, the studied with a high-resolution JEM-4000EX electron nanocrystalline structure is two-phase and consists of microscope at an accelerating voltage 400 kV. A direct nanoparticles of a crystalline phase embedded in an image of the nanocrystal lattice was obtained by amorphous host [3]. In some cases, however, the nanoc- recording a series of images made with different defo- cusing, followed by computer processing. In this paper, rystalline structure may also be made up of nanoparti- we present photomicrographs obtained at an optimum cles of different crystalline phases [4]. The degree of defocusing δ = –46 nm corresponding to the Scherzer structural perfection of nanocrystals is one of the most δ ≅ 1/2 λ1/2 important characteristics of nanocrystalline materials. focus ( –1.2Cs , where Cs is the spherical-aber- λ It is known, for instance, that light nanocrystalline ration constant equal to 1 mm and is the electron alloys have a high strength [5, 6]. Aluminum-based wavelength). The foils for the electron microscopy studies were prepared by ion milling. The alloy compo- alloys containing 6–15% of a transition metal (Fe or Ni) sition was determined by x-ray spectral analysis. and a few percent of a rare-earth metal may feature a yield strength as high as 1.6 GPa [7] while having, at the same time, a good plasticity. To properly understand 3. RESULTS AND DISCUSSION the processes involved in the plastic deformation of The as-prepared samples were amorphous. The cor- such materials, one has to know the specific features of responding x-ray and electron diffraction patterns their structure (the fraction of nanocrystals, their exhibit only broad maxima, with no peaks due to crys- mutual arrangement) and the possibility of deforma- talline phases present. The high-resolution images of the structure of the as-prepared alloy feature only the tion, i.e., the degree of perfection of the nanocrystals. It mazy contrast typical of an amorphous structure. Fol- is important to compare this characteristic of perfection lowing controlled crystallization, a nanocrystalline in alloys of different mechanical properties and estab- structure formed in all the alloys. lish the relation connecting the structure with the prop- When heated, all the samples crystallized by the pri- erties of the material. This paper reports on a study of mary mechanism. In aluminum-based alloys, fcc Al the perfection of nanocrystals in aluminum- and nickel- crystals precipitate. At the end of the first crystalliza- based alloys. tion stage, the structure of the Al–Ni–Re alloys consists 1063-7834/02/4406-1003 $22.00 © 2002 MAIK “Nauka/Interperiodica” 1004 ABROSIMOVA, ARONIN where L is the grain size, λ is the wavelength of the radiation used, θ is the reflection angle, and ∆(2θ) is the (111) halfwidth of the corresponding reflection. The half- width of the diffraction lines is usually denoted by B; this notation will be employed in the graphs below. As the halfwidth of diffraction reflections in nanocrystal- (200) Intensity line materials is large, one can neglect the instrumental (220) (311) broadening. (222) (331) (420) (422) θ θ (400) The broadening proportional to 1/cos (i.e., to sec ) can also be caused by stacking faults in the material. 40 60 80 100 120 140 For instance, a stacking fault in an fcc structure changes 2θ, deg the ...ABCABC... sequence of the {111} planes to ...ABCACABC... The broadening caused by stacking Fig. 1. Diffraction pattern of the Al88Ni6Y6 nanocrystalline faults is similar to that originating from small particle alloy. size, but its magnitude depends on the defect concentra- tion and interference indices; i.e., stacking faults can produce crystallographic anisotropy in the calculated B grain size, even if the true particle dimensions are inde- 2.6 pendent of crystallographic direction. 2 If crystals contain randomly distributed disloca- 2.2 tions, the displacement of atoms from lattice sites is determined by the superposition of displacements due 1 to each dislocation and, therefore, the action of dislo- 1.8 cation fields can be treated phenomenologically as a local change in the interplanar distance [9]. The dif- 3 ∆ θ 1.4 fraction line broadening 2 (2 ) (or B) can be written in this case as ∆()θ ()θ∆ 1.0 2 2 = 4 dm/d0 tan , ∆ where dm is the average maximum change in the dis- 0.6 tance between the hkl planes and d0 is the interplanar 0.4 distance in a perfect crystal. Thus, the broadening orig- 1.0 1.2 1.6 2.0 2.4 2.8 inating from a random dislocation distribution is pro- secθ portional to tanθ. By analyzing the angular dependence of the broad- Fig. 2. Halfwidth of the reflections of (1) the Al Ni Y , (2) ening, one can reveal the factor responsible for the 88 6 6 major contribution to it; indeed, if the broadening is Al88Ni10Y2, and (3) Al82Ni11Ce3Si4 nanocrystalline alloys θ plotted vs. secθ. proportional to sec , it is caused by the small crystallite size, but if it is proportional to tanθ, the broadening originates from dislocations and their clusters, which of fcc Al nanocrystals dispersed randomly throughout generate long-range distortion fields. the amorphous host, whose size depends on the chemi- Part of the reflections presented in Fig. 1 is due to cal alloy composition and varies from 5 nm in the superposition of reflections from the crystalline Al89Ni5Y6 to 12 nm in Al82Ni11Ce3Si4. phase and from nanocrystals; therefore, one should first Figure 1 presents a typical x-ray diffraction pattern separate them. For this purpose, special computer codes of an aluminum-based nanocrystalline alloy. The pat- were used which permit background correction, tern is seen to contain both broad lines due to fcc Al smoothening, and deconvolution of overlapping max- nanocrystals and a diffuse halo originating from the ima, as well as determination of the halfwidth of the amorphous phase. maxima. The shape of a diffuse maximum was fitted by 2 The width of the diffraction line may depend on a a Gaussian hexp(–ax ), the fitting of the calculations to number of factors. Among them are the small size of the experimental data being preformed in both parameters crystals, the presence of various defects, and inhomo- h and a. geneities in the chemical composition. Figure 2 plots the dependence of the halfwidth B of θ The broadening due to the small grain size is diffraction reflections on sec for a sample of the described by the Selyakov–Scherrer expression [8] Al88Ni6Y6 alloy (curve 1) whose diffraction pattern is shown in Fig. 1. Similar curves for other aluminum- L = λ()1/cosθ /∆()2θ , based alloys are also presented in Fig. 2. PHYSICS OF THE SOLID STATE Vol. 44 No. 6 2002 THE FINE STRUCTURE OF FCC NANOCRYSTALS 1005 All three dependences can be fitted with good accu- B Σ 2 racy by straight lines, with the variance (y – yi) ( yi are 2.2 the experimental values, and y are obtained in calcula- tions) not exceeding 0.005; the variance is 0.0008 for 1.8 Al88Ni6Y6, 0.0035 for Al88Ni10Y2, and 0.001 for Al82Ni11Ce3Si4. At the same time, the similar depen- dence of the halfwidth of diffraction peaks on tanθ is 1.4 obviously not linear (Fig. 3). An attempt to fit it with a linear function yields a substantially larger variance 1.0 (0.045). Thus, analysis of the angular dependences of dif- 0.6 fraction reflections allows one to conclude that the 0.2 0.6 1.0 1.4 1.8 2.2 2.6 broadening of diffraction lines in aluminum-based tanθ nanocrystalline alloys is dominated by the small grain size.
Details
-
File Typepdf
-
Upload Time-
-
Content LanguagesEnglish
-
Upload UserAnonymous/Not logged-in
-
File Pages200 Page
-
File Size-