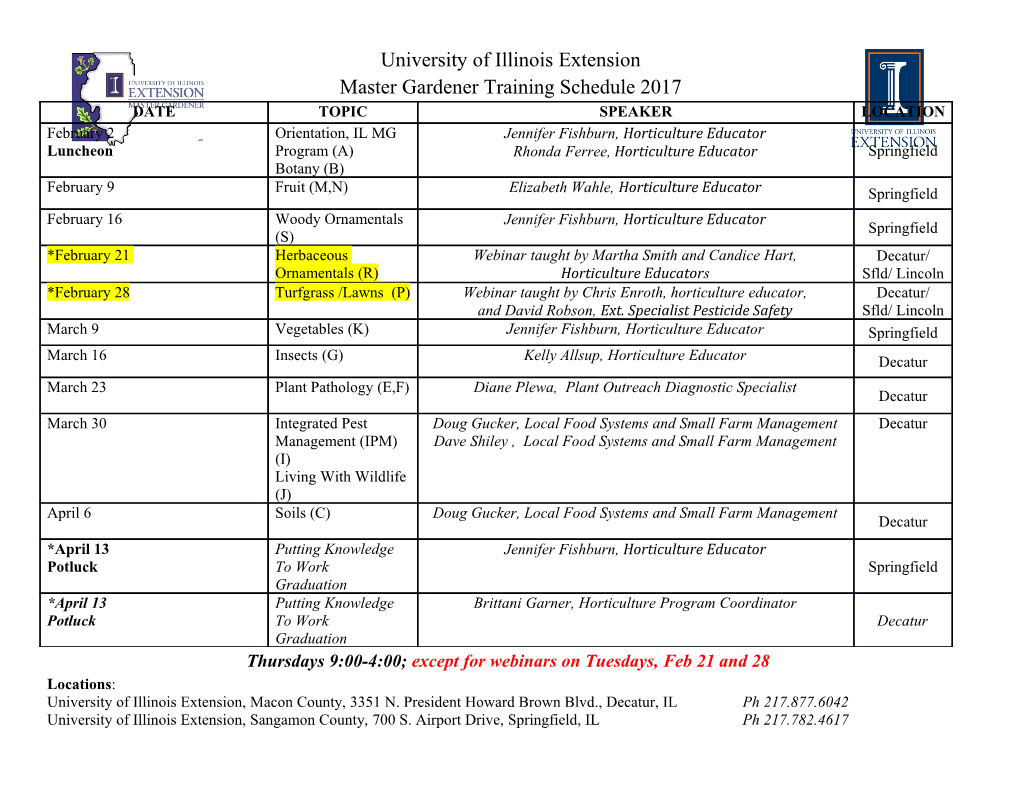
A MULTICHANNEL OIL DEBRIS SENSOR FOR ONLINE HEALTH MONITORING OF ROTATING MACHINERY A Dissertation Presented to The Graduate Faculty of The University of Akron In Partial Fulfillment of the Requirements for the Degree Doctor of Philosophy Li Du December, 2012 i A MULTICHANNEL OIL DEBRIS SENSOR FOR ONLINE HEALTH MONITORING OF ROTATING MACHINERY Li Du Dissertation Approved: Accepted: _____________________________ _____________________________ Advisor Department Chair Dr. Jiang Zhe Dr. Celal Batur _____________________________ _____________________________ Committee Member Dean of the College Dr. Eric Engeberg Dr. George K. Haritos _____________________________ _____________________________ Committee Member Dean of the Graduate School Dr. Jae-Won Choi Dr. George R. Newkome _____________________________ _____________________________ Committee Member Date Dr. Joan Carletta _____________________________ Committee Member Dr. Chien-Chung Chan ii ABSTRACT Condition based monitoring has become essential in maintaining and extending the health of high-speed rotating and reciprocating machinery. One effective approach to detect signs of potential failure of a rotating or reciprocating machine is to examine the wear debris in its lubricating oil. Magnetic inductive sensors have gained certain success due to the capability of differentiation of ferrous and non-ferrous wear debris, which is important for condition monitoring of rotating and reciprocating machinery. However, they are limited to debris larger than 100 µm in size because of the low sensitivity of 3-D solenoids. To overcome this problem, the design concept and preliminary testing results of an inductive coulter Counter that uses a planar coil as sensing element are presented. We first demonstrate the feasibility of the inductive Coulter counting principle to detect metal particles in lubrication oil using a microfluidic device. The device detects the passage of ferrous and nonferrous metal particles by monitoring the inductance change of an embedded planar coil. The device was tested using iron and copper particles ranging in size from 50 µm to 125 µm. The testing results have demonstrated that the device is capable of detecting and distinguishing ferrous and nonferrous metal debris particles in lubrication oil. Next, to overcome the limitations of the microfluidic device, a meso-scale oil debris sensor was studied. The sensor used a two-layer planar coil with a iii meso-scale fluidic pipe crossing the planar coil’s center as the sensing element. The testing results indicated that the throughput is significantly higher than that of the microfluidic channel without sacrificing the sensitivity. However, the throughput still needs to be improved to meet the online monitoring requirements. To further improve the throughput, we designed and tested an inductive Coulter counter with seven detection channels to detect and count metal particles in lubrication oil. The testing results indicated that using multichannel sensor we are able to improve the detection throughput of the sensor seven times in contrast to a single channel sensor. Negligible crosstalk among channels was observed. Finally, a proof-of-principle resonant frequency division multiplexed four-channel inductive sensor for detecting microscale metallic debris in lubrication oil using only one set of detection electronics is presented. Using the resonance frequency division multiplexing method, debris particles in four parallel sensing channels were successfully detected and counted simultaneously. Testing results indicate the sensor is capable of differentiating and detecting ferrous and non-ferrous metallic debris. Crosstalk among four sensing channels is negligible. iv DEDICATION This dissertation is dedicated to my parents Hanjie Du and Runxin Shang, who made all this possible, for their endless love, support, encouragement and patience. v ACKNOWLEDGEMENTS It would not have been possible to write this doctoral dissertation without the help and support of the kind people around me, to only some of whom it is possible to give particular mention here. First, I would like thank my advisor and mentor Prof. Jiang Zhe. His good advice and support has been invaluable on both an academic and a personal level, for which I am extremely grateful. The research journey at The University of Akron would not be possible without the support of all my colleagues and friends in the lab: Dr. Ashish V. Jagtiani, Mr. Abhay Vasudev, Mrs. Hui Ouyang, Mr. Zhuochen Wang and Mr. Yu Han. I would also like to extend my gratitude to the staff in the Mechanical Engineering, Mrs. Stacy Meier, Mrs. Christina Christian and Mr. Cliff Bailey for their assistance and technical support since the start of my graduate work in The University of Akron. I would also like thank my friends that I made over the years at The University of Akron, Dr. Jie Wen, Mr. Pei Chen, Dr. Ruifeng Wang, whose friendship over the years have made this possible. I must also thank Mr. Yu Han, Mr. Xiaoliang Zhu and Mr. Abdullah Al Amin who took time to help me proof read this dissertation. I would also like to thank Dr. Joan Carletta for her continuing advice with my research. In addition, I must extend my gratitude towards my committee members Dr. Eric Engeberg, Dr. Jae-Won Choi, Dr. Joan Carletta and Dr. Chien-Chung Chan. A special thank goes to Dr. Chien-Chung Chan who agreed to join my dissertation vi committee after my research proposal and towards the end of this project. Finally, I would like to thank my parents, my wife Lixuan Yan, my son Yi Du and my daughter Coco Du for their endless love and personal support at all times. vii TABLE OF CONTENTS Page LIST OF TABLES .............................................................................................................. x LIST OF FIGURES ........................................................................................................... xi CHAPTER I. INTRODUCTION .......................................................................................................... 1 1.1 Introduction ........................................................................................................... 1 1.2 Motivation ............................................................................................................. 3 1.3 Research objectives ............................................................................................... 4 1.4 Summary ............................................................................................................... 6 II. BACKGROUND AND LITERATURE REVIEW ........................................................ 8 2.1 Electrical impedance detection ............................................................................. 9 2.1.1 Resistive detection ..................................................................................... 9 2.1.2 Capacitive detection ................................................................................. 11 2.1.3 Inductive detection ................................................................................... 14 2.2 Ultrasonic detection ............................................................................................ 18 2.3 Optical and imaging detection ............................................................................ 22 2.4 X-ray spectrometer .............................................................................................. 25 2.5 Summary ............................................................................................................. 27 III. PRELIMINARY RESULTS: DEMONSTRATION OF INDUCTIVE COULTER COUNTING PRINCIPLE USING MICROFLUIDIC CHANNEL DEVICE .................. 29 3.1 Inductive Coulter counting principle .................................................................. 29 3.2 Demonstration of inductive Coulter counting principle by using planar coil ..... 35 viii 3.3 Micro fluid channel debris sensor ....................................................................... 42 3.3.1 Device description and fabrication ...................................................... 42 3.3.2 Experimental results and discussion .................................................... 45 3.4 Summary ............................................................................................................. 50 IV. DESIGN AND IMPLEMENTATION OF A MESO-SCALE WEAR DEBRIS SENSOR ........................................................................................................................... 52 4.1 Device design and measurement scheme ............................................................ 53 4.2 Static test and analysis ........................................................................................ 55 4.3 Experimental results and discussions.................................................................. 59 V. DESIGN AND IMPLEMENTATION OF A SEVEN CHANNEL MULTIPLEXED WEAR DEBRIS SENSOR BASED ON UNDERSAMPLING TECHINIQUE .............. 66 5.1 Device design and measurement setup ............................................................... 67 5.2 Undersampling measurement .............................................................................. 71 5.3 Signal processing ................................................................................................ 79 5.4 Crosstalk analysis................................................................................................ 80 5.5 Experimental results and discussion ..................................................................
Details
-
File Typepdf
-
Upload Time-
-
Content LanguagesEnglish
-
Upload UserAnonymous/Not logged-in
-
File Pages148 Page
-
File Size-