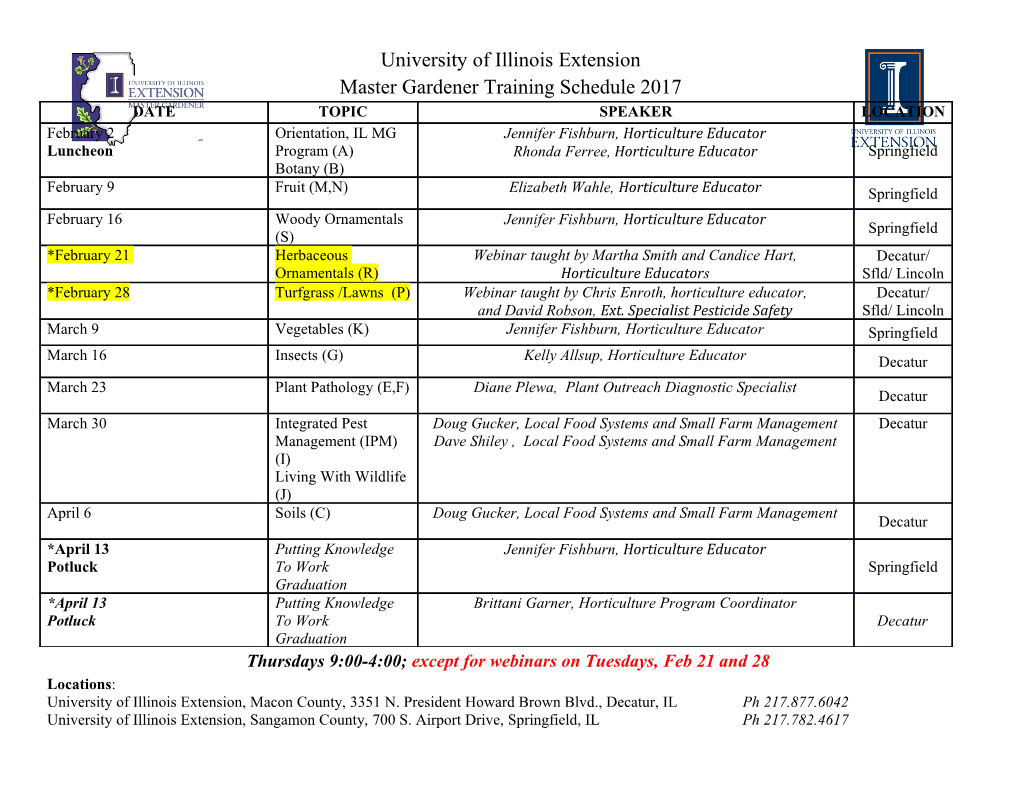
CARBON DIOXIDE CLEANING GOING THROUGH PHASES A Panel discussion of CO 2Cleaning Technology 26 PC July/August 1999 A panel recently convened at CleanTech ‘99 to examine the current state of carbon dioxide (CO 2)-based cleaning technology. Panel members discussed the typical applications appropriate to each system, the benefits of C02-based sys- tems over other cleaning techniques, and the complexities of system operation and maintenance. Panelists also reviewed performance levels, relative costs, and specific application strategies. iquid Carbon Dioxide Systems to 25 minutes, depending on the size of the Panelist: Liz Hill cleaning vessel, the size of the pumps, the Research Triangle Institute nature of the contaminants, and the number of Liquid carbon dioxide (LCO2 ) technol- required cycles (ie, washes and rinses). ogy is one that can be classified as a Efficacy is specific to the contaminants being "maturing" technology. At high pres- addressed: however, pretreatment or additives sures, CO 2 takes on a liquid form that (eg, solvents or surfactants) improve the range is sustainable at, above, and below of cleaning. Some contaminants that respond room temperatures (see Figure 1, well to LCO 2removal include: light oils, hydro- page 28). carbons, machining fluids, and chips (due The equipment used in LCO2 appli- to agitation). cations includes a vessel by which a To date. reliable submicron particle removal L constant pressure is maintained. (to this speaker’s knowledge) has not yet been Some form of agitation (eg, spinning, achieved by LCO 2 processes, but this limitation spraying, ultrasonics, etc) is generally required is likely a temporary one. Heavy hydrocarbon as well. To recycle and clean LCO2 it must be greases do not respond well; however, additives transferred to another chamber, where pressure can remedy this shortcoming. Salts and many is released, allowing the CO2 to expand back to other inorganic soils continue to present a chal- a gas. This leaves behind only the contaminants lenge to LCO 2systems. Paint. rust, and carbon that were removed from the parts, which are residues will likely never be ideal soils for this collected for disposal or re-use. The CO2 is then type of technology. returned and repressurized in the cleaning Liquid CO 2systems have demonstrated suc- chamber. In many systems, such additives as cess over a range of cleaning applications, organic solvents and surfactants are mixed with including: the LCO improve performance. s Fiber optics 2 Pure LCO2 systems do not require any per- s Machined metal parts mits, but users must be aware that some addi- s Hydrocarbon residues from electrical tives, like certain organic solvents, may have components permit issues. No water or sewer connections s Rag cleaning (even paper) are required for these systems, and waste is s Dry cleaning collected at the recycling point. Carbon dioxide In LCO 2systems, the dimensions of the clean- is a greenhouse gas, but it is not a net addi- ing vessel will dictate the type of parts that can tion because it is gathered from other be cleaned efficiently. Parts must also be com- processes. Carbon dioxide is not an ozone- patible with the high pressures of the cleaning depleting compound (ODC) nor is it considered chamber. Condensation is a possibility, and a volatile organic compound (VOC); it is non- parts must be warmed properly before removal flammable and is not considered a hazardous from the chamber to prevent this. Obviously, air pollutant (HAP). this step can increase cycle time. CO2 has been Unlike many traditional systems that perform known to strip certain plasticizers and pene- to limitations set by bath life and the effective- trate some elastomers. When the pressure is ness of the cleaning agent, LCO 2 systems fea- dropped for removal. bubbles can form inside ture cleaning cycles that employ fresh, clean the elastomer and cause deformities. CO introduced from a recycling loop. It is a Operation of LCO equipment is fairly simple 2 2 batch process, and cycle times can be long-10 due to its high level of automation. Health and BASED ON A PANEL PRESENTATION AT July/August 1999 PC 27 phases become one (this is unlike the commonly held theory that a vapor phase becomes so dense that it acts like a liquid). As such, the fluid has the penetrating power of a gas, but the cleaning ability of a liquid. As Figure 1 shows, supercritical fluid begins at 73 atm and 31°C. Supercritical CO 2(SCCO 2 ) possesses physical characteristics that allow it to relate with other more familiar substances. One of the attractive fea- tures of SCCO 2is its reputation as a ‘tunable” solvent-this is, as you change the pressure of the system (and thus the density of the SCCO 2 you change its solvating characteris- tics. In principle, SCCO 2systems Figure 1. A phase diagram of carbon work in much the same manner as dioxide. those for LCO. 2 All of the environmental and safety safety concerns include proper issues that go along with LCO 2apply instruction in operating pressurized to SCCO 2The performance benefits of replacing traditional cleaning sys- systems, close monitoring of CO2 lev- els in the air, attention to possible tems with SCCO2 are also similar to overexposure to cold gas and liquid those of LCO2 Some of the more sig- (resulting in possible skin bums), and nificant beneilts include the absence temperature of parts being removed of cleaning agent residue, no required from the system. drying step, and high-temperature Prices range from $100,000 and operation, which expedites solvency higher, with the CO 2running $0.15 to action. Applications for the technol- $0.20 per gallon for bulk and about ogy are concentrated mostly in $0.85 per gallon in bottles. smaller, niche markets. LCO2 systems have proven very suc- SCCO2 is actually quite effective at cessful in cleaning a variety of sub- removing particulate matter. Research strates. Even an intricate material like has been carried out on integrated cir- aluminum honeycomb has been cuit wafers, where a concept dubbed cleaned down to practical standards “turbulent flow” has proved effective in without evidence of substrate damage. removing micron to sub-micron parti- Results also were favorable when cles. This is a significant benefit given the technology was employed on that SCCO 2will remove any organic brass hydraulic filters from a heli- residue helping the particles to adhere copter; the filters were covered with a to the surface of the substrate being gritty/oily substance (Figure 2). Prior cleaned. Lower temperatures facilitate to investigating CO 2 technologies, the removal of smaller particles due to manufacturer originally cleaned these the greater density of the fluid at parts by soaking them for 24 hours in these temperatures. a hydrocarbon mixture, scrubbing by For one manufacturer, an SCCO2 hand, soaking them for another 24 system solved the challenging task of hours, and scrubbing again. With the cleaning silicon wafers. The challenge new LCO 2 process, the parts were came in cleaning the wafers after they first soaked in a warm hydrocarbon were cut from the parent ingot with a oil/surfactant mixture for about 10 wire saw. Contamination resulted minutes, hand scrubbed, and then from a machine containing silicon cleaned in LCO for 20 minutes. This carbide, which was used as the abra- 2 turned a P-day process into a 45- sive to cut the individual wafers. The minute task. cut wafers had a tendency to lean The technique offers manufacturers against one another, and the oil at a way to minimize waste streams, that contact point was difficult to clean parts that are incompatible with remove again, at least with traditional water, and eliminate hazardous cleaning agents. Correction of the cleaning agents. wafer positions was not possible because they had to remain glued to Cleaning With Supercritical CO2 a glass substrate from the point of Panelist: Yale West, cutting through cleaning. Applied Separations Primary testing demonstrated Supercritical fluid is a very unique immediate success and was accom- state of matter, almost a fourth state plished by sandwiching two wafers per se. It essentially refers to the with oil between them and then point where the liquid and vapor attempting to clean them with July/August 1999 Figure 2. Helicopter hydraulic filters before and after cleaning with liquid carbon dioxide. SCCO2 Full implementation of an SCCO2 system followed, and the wafer cleaning process showed considerably improved results. SCCO2 systems can be either fully manual or automatic. Another use for SCCO2 is as a solvent/carrier for sur- face treatments. Snow CO, Cleaning Panelist: Dr. Robert Sherman, Applied Surface Technologies Snow CO2 (SCO2 ) is generated by expanding liquid or gaseous CO, through an orifice. It removes both organic soils and particles as small as several hundred angstroms (1.0 X 10-10 meters). It will not, however, remove substances that are chemically bonded to a surface (eg, paint, epoxies, evapo- rated metals, rust. etc). SCO2 is non- toxic and nonflammable: it is not listed as an ODC or a VOC. To safely apply the technology, users should avoid skin contact, consider room oxygen displacement, and be aware of exces- sive CO, buildup in the room. According to the phase diagram (Figure 1). SCO 2 formation takes place along the phase boundary lines separating gas, liquid, and solid. The thermodynamics of snow formation should be a constant enthalpy process. The expansion within and after the orifice leads to lower pres- sures and temperatures, creating a gaseous and solid-phase mix that can travel at high velocities. Exposing a CO, gas source to the dropping pressure inside an orifice causes fluid droplets to nucleate: as a result, the percentage of liquid increases.
Details
-
File Typepdf
-
Upload Time-
-
Content LanguagesEnglish
-
Upload UserAnonymous/Not logged-in
-
File Pages8 Page
-
File Size-