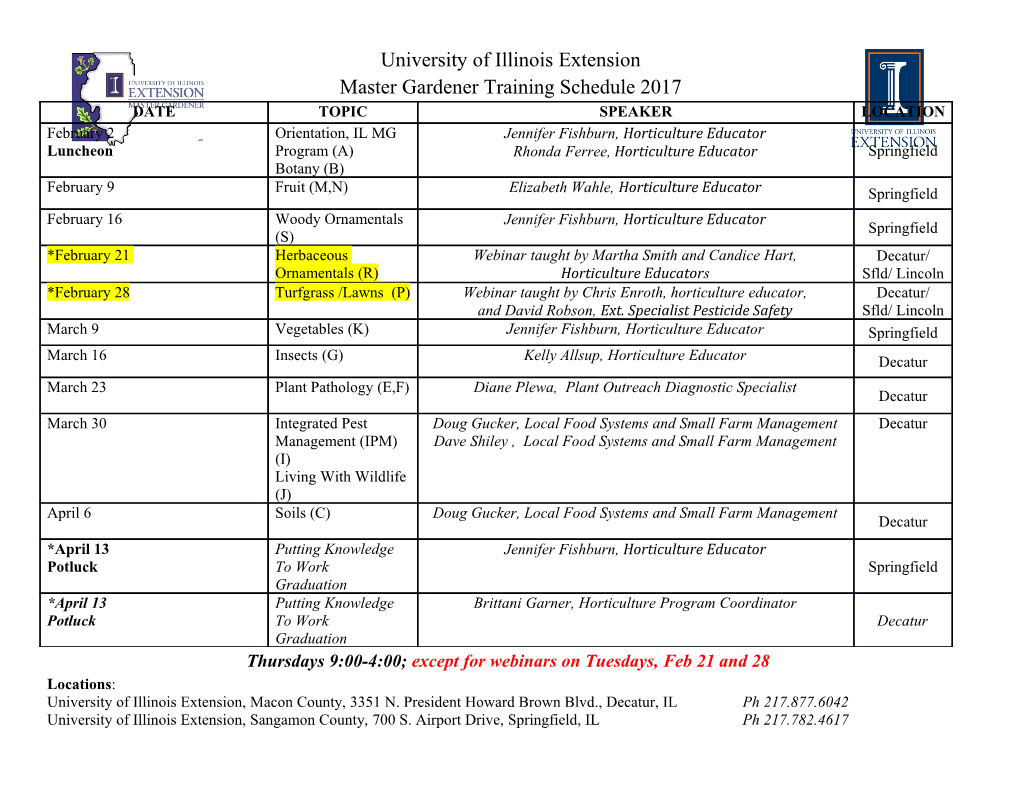
Materials Transactions, Vol. 57, No. 9 (2016) pp. 1560 to 1566 ©2016 The Japan Institute of Metals and Materials Optimal Combination of Calcination and Reduction Conditions as well as Na2SO4 Additive for Carbothermic Reduction of Limonite Ore Guan-Jhou Chen1, Jia-Shyan Shiau2, Shih-Hsien Liu2 and Weng-Sing Hwang1,* 1Department of Materials Science and Engineering, National Cheng Kung University, No.1, University Road, Tainan City 701, Taiwan, R.O.C. 2Iron Making Process Development Section, Iron & Steel Research & Development Dept., China Steel Corporation, 1 Chung Kang Road Hsiao Kang, Kaohsiung 81233, Taiwan, R.O.C. The optimal carbothermic reduction parameters of limonite ore and the inuence of calcining temperature on these were investigated. In addition, the impact of the addition of Na2SO4 on limonite ore which had been calcined before reduction at optimal carbothermic conditions was also investigated. XRD analysis, BET-specic surface area analysis, bromine methyl alcohol solution analysis, and chemical compositional analysis were used in order to obtain the associated parameters. The best nickel grade and recovery rate of the 673 K-calcined limonite ore can reach >30 mass% and 90.2 mass%, respectively, when the reduction temperature is 1373 K, with a reduction time of 30 min, and a carbon-oxygen ratio of 0.6. This is because the 673 K-calcined limonite 2 ores have the highest specic surface area of 46.8 m /g with pores in the size of 29.7 Å. The addition of Na2SO4 by 5 mass% resulted in the best nickel grade of >30 mass% and the best recovery rate of 93.8 mass% at the same reduction temperature, time and carbon-oxygen ratio. [doi:10.2320/matertrans.M2016072] (Received March 4, 2016; Accepted June 27, 2016; Published August 25, 2016) Keywords: limonite, calcination, carbothermic reduction, additive 1. Introduction and high pressure acid leaching (HPAL). Although the recov- ery rate is high, this process is now used less than previous Nickel (Ni) is a ferromagnetic element with a high melting days because of its low economic benets and the large point at 1728 K and thermal endurance, excellent corro- amount of toxic waste it produces, thus causing serious pollu- sion-resistance and antioxidation, good mechanical proper- tion if piled in unsheltered conditions. The smelting technol- ties, superior malleability and chemical stability. Its major ogies include a rotary kiln-electric furnace (RKEF) process, a application is for the smelting of steel and iron, especially for sintering-blast furnace suldation smelting process and a sin- the manufacturing of stainless steel, which accounts for 61% tering-blast furnace smelting process. The industrial applica- of the total consumption of metallic nickel.1–5) The nickel that tion of hybrid hydrometallurgical-re rening technology has been explored in the world are approximately 160 million can be found in the Nippon Yakin Company’s Oheyama tons, of which 30–40% is nickel sulde ore and 60–70% is smelting plant. Laterite nickel ore has many applications, and nickel oxide ore. Since the technology used to extract nickel can be used to produce intermediate products like nickel ox- from the nickel sulde ore is more mature, 60–70% of nickel ide, nickel-sulfur or nickel iron alloy, of which the nickel-sul- production comes from this. However, the amount of nickel fur and nickel oxide can be used by nickel reneries to solve sulde ore which can be exploited is limited, and the reserves the problem of insufcient nickel sulde. A nickel-iron alloy of nickel oxide ore are still rather high and the mining cost is can also be used as a substitute for pure nickel addition in the relatively low. As such, the use of nickel oxide ore has be- manufacturing of stainless steel and low-nickel alloy come an important issue. steel.11–15) An oxidized-type of laterite nickel ore is formed from the According to the Gibbs free energy of the Ellingham dia- mass nickel-containing serpentine in tropical or subtropical gram, the lower the coordinate in the diagram, the lower and zones through long-term weathering and erosion effects. It is more stable the free energy, which indicates that the oxides in an oxidized-type of silicate mineral with a loose clay soil ap- the lower part of the diagram will stably exist, and thus be pearance containing hydrous oxides of iron, aluminum and difcult to reduce. In contrast, in the upper range of the Ell- silicon. The mineral vein of laterite nickel ore can generally ingham diagram the existence of oxides causes higher free be divided into two layers: the upper layer is limonite-type energy in the reaction, which then destabilizes the oxides, laterite nickel ore, which contains more iron and less nickel making them more readily reduced. This concept can be ap- (about 0.8–1.5%); the lower layer is saprolite-type magne- plied to the selected reduction of oxides, where manufactur- sium silicate nickel ore, which contains less iron and more ers can allow certain oxides to be reduced by controlling the nickel, and the nickel content is about 1.5–2.5%.6–10) temperature and reducing atmosphere, based on the associat- At present, there are three categories of rening technolo- ed Ellingham diagram. By applying this mechanism to later- gies for nickel: the hydrometallurgical process, re-rening ite nickel ore in a carbothermic reduction experiment, the re- process and hybrid hydrometallurgical-re rening process. duction of the nickel oxide will take place before the iron Two types of hydrometallurgical processes are used in indus- oxide starts to be reduced. In addition, by adjusting the trial production, reduction roasting-ammonia leaching (AL) amount of reductant that is added, as well as the reduction temperature and reduction time, one can control the reduction * Corresponding author, E-mail: [email protected] level of selected oxides. Optimal Combination of Calcination and Reduction Conditions as well as Na2SO4 Additive for Carbothermic Reduction of Limonite Ore 1561 With the addition of reductants, and with the appropriate to meet industrial standards: 15–16 mass% for nickel grade control of temperature and time, the carbothermic reduction and 85 mass% for the recovery rate. process of laterite nickel ore can be conducted in order to extract the metal phases of nickel and iron from the mineral 2. Experimental Procedure phase.16–20) Many studies on the thermal analysis of laterite nickel ore report that the free water is removed at tempera- The experimental ow chart of this research is shown in tures between 333 K and 383 K, dehydration occurs at 553 K, Fig. 1. The rst step was to prepare the samples for the exper- the serpentine phase transforms into enstatite and olivine at iment. In order to conduct the calcination experiment, Indo- 898 K, and the recrystallization reaction happens at 1093 K.21) nesian limonite-type laterite nickel ores undergone heat treat- Zevgolis et al.22) pointed out that a higher specic surface ment at 673, 873 and 1173 K, each for 2 h, in advance. The area is helpful to the carbothermic reduction of laterite nickel ores and reductants (graphite powder) were then separately ore, and the limonite-type laterite nickel ore has a lower re- ground into ne powders, which could pass through a 200- duction rate. As indicated by previous study,23) the mineral mesh sieve, and these were dried at 378 K until they had no phase of limonite-type laterite nickel ore could be simplied free water. Next, the powders were mixed based on the calcu- by calcining at 1173 K. Therefore, after being calcined in ad- lated carbon-oxygen ratio (C/O), and the additive (Na2SO4) vance, the following carbothermic reduction process (at a re- and binding agent (Bentonite) were then added. Finally, the action temperature of 1373 K) could enhance the nickel grade powders were manually rolled into small pellets with a diam- of the laterite nickel ore, accompanied by a lower recovery eter of about 12 mm. rate. Yang et al.24) proposed that garnieritic-type laterite nick- The procedures of the high temperature carbothermic re- el ore has a phase transformation at the calcining temperature duction experiment are as follows: Let the inert gas (N2, of 873–973 K, and the accompanying increase in surface area 500 cc/min) ow into the mufe furnace; start the furnace and the generation of ne pores are also helpful to the carbo- and let the temperature rise to 1373 K. Put the sample pellets thermic reduction. At a calcining temperature of 973–1123 K, into the furnace; conduct the carbothermic reduction process laterite nickel ore will start its recrystallization, reducing its and then, take the sample out of the furnace after the preset specic surface area and generating bigger pores, which are reaction time is completed. Place the hot sample into a nitro- detrimental to the following carbothermic reduction. There- gen-owing cooling box until it is chilled to room tempera- fore, for garnieritic-type laterite nickel ore, the calcining tem- ture. A schematic diagram of the furnace is shown as Fig. 2. perature benecial to the carbothermic reduction is 873– The optimal carbothermic reaction parameters with the 973 K. best nickel grade and recovery rate were investigated through Sodium salts or other alkaline additives can react with min- the carbothermic reduction process of 1173 K-calcined limo- erals containing aluminum oxide and silicates, thus forming sodium aluminate or sodium aluminum silicates. Moreover, the sodium salts can intensify the reduction of iron oxides, resulting in the separation of iron from aluminum and sili- 25) 26,27) con. As indicated by Li et al., the addition of Na2SO4 to the carbon-bearing pellets of laterite nickel ore is benecial to the reduction of nickel, resulting in a better nickel grade and recovery rate.
Details
-
File Typepdf
-
Upload Time-
-
Content LanguagesEnglish
-
Upload UserAnonymous/Not logged-in
-
File Pages7 Page
-
File Size-